Over the Wire
TAPPI
Weekly Spotlight
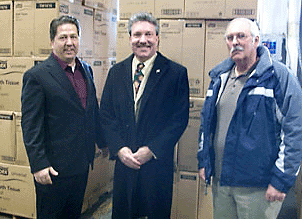 SCA, Sweden and North America, this past week carried out two major donation projects—one in New York, USA, and the other in Queensland, Australia. The New York project involved $2,000 worth of towel and bath tissue products donated to Double H Ranch, a camp for seriously ill children located in Lake Luzerne, N.Y. The Australian project involved donations of essential tissue products to devastated flood victims in that country.
In New York, 100 cases of towel and bath tissue products made and converted locally by SCA in South Glens Falls and Greenwich, were picked up from the company's Saratoga distribution center. The products will be used to serve the more than 1,500 children with life-threatening illnesses and their family members who visit the ranch every year...
"SCA is committed to taking an active role in the communities where we do business," said Mike Mound, regional director of SCA's Northeast Operations. "The Double H Ranch works hard to improve the quality of life for children with serious illnesses, by giving them the opportunity to experience the beauty of the Adirondacks in a camp setting. We are proud to support their mission with our Tork products."
Max Yurenda, CEO and executive director at the ranch, noted that "over the past several years SCA has provided ongoing support for the Double H Ranch. We're grateful for SCA's donation. Essentials like bath tissue and towels help us accommodate the campers, their families, and the more than 1,000 volunteers who aid us in creating memorable experiences for the children we serve throughout the year."
Keith Baker, president of the United Steelworkers Local 1478 for SCA Tissue North America, said this is one of the many ways SCA supports the local community. "We're very proud to give back to the communities where we, as employees, live and work and it's especially meaningful to see the products we make support a charitable organization like Double H Ranch."
In Australia, SCA is working with Foodback Australia, a not-for-profit organization that collects and distributes food and grocery items to welfare agencies, to coordinate the delivery of more than AUD 50,000 (cost to SCA) worth of donated stock. The donated stock includes drastically needed toilet paper, nappies, and feminine hygiene products.
SCA notes that one of the greatest difficulties at the moment in flooded regions of Australia is that many roads are blocked and impassable. It is believed, SCA says, that it may be at least a week before trucks are able to get through.
SCA adds that all of its employees in the region are safe and accounted for and that its facility at Larapinta remains unaffected by the floods. All employees have, however, been offered access to an Employee Assistance Program, a free, confidential counseling service, SCA points out.
In the photo below, preparing to load up donated New York supplies are, from the left, Mike Mound, regional director of SCA's Northeast Operations, Max Yurdenda, executive director of the Double H Ranch, and Keith Baker, president of the United Steelworkers Local 1478 for SCA Tissue North America.
##SHARELINKS##
|
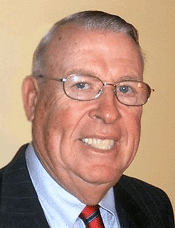 Richard A. Reese will receive the 2011 TAPPI Gunnar Nicholson Gold Medal Award, TAPPI's most prestigious annual award. Carrying a cash prize funded by an endowment by Dr. Gunnar W. E. Nicholson and TAPPI Foundation, the award will be presented to Reese at the Tuesday evening, May 3, 2011, awards dinner during the 2011 PaperCon Conference at the Northern Kentucky Convention Center in Covington, Ky., USA.
The Gunnar Nicholson Gold Medal Award was established in 1985 to replace the TAPPI Gold Medal, which had been awarded from 1928 to 1984. It recognizes an individual who has created a preeminent scientific and engineering achievement that has proven commercial benefit to the world's pulp, paper, board, and forest products industries and other industries that TAPPI serves.
"Dick has made enormous contributions throughout his career to the successes of the world-wide pulp and paper industry," said Larry N. Montague, president and CEO of TAPPI. "He has become one of the outstanding teachers of technology and has put into practice many of the concepts and ideas he previously developed."
A graduate of Miami University in Oxford, Ohio, with a bachelor of science degree in applied science with a major in paper technology, Reese joined Hammermill Paper Co. after graduation and worked in several technical, engineering, and production positions. During his career, he has worked at Huytech Systems Division of Huyck Corp., Poyry-BEK, OPTEC Division of Rust International, CRS Sirrine Engineers Inc., and Georgia-Pacific Engineering Technology and Manufacturing Services. He founded Dick Reese and Associates Inc. in 2004 and currently works with paper companies around the world to reduce energy consumption. Reese has conducted performance and energy evaluations on more than 300 paper machines in his career.
Reese has developed a number of paper machine performance guidelines that have been used for TAPPI TIPs, technical papers and paper industry conference presentations. He has made more than 50 presentations at paper industry conferences and published more than 60 technical articles. He conducted a world-wide paper machine energy survey for TAPPI in 2005 and used the results to develop paper machine energy targets and paper machine energy scorecards to benchmark energy performance. The energy scorecards have been translated into Spanish and French and are used worldwide. Reese has contributed to development of instrumentation for assisting in evaluating paper machine performance, including on-line and portable total mass and moisture meters, opacity sensors, dryer pocket humidity testers, and dryer surface temperature measurement equipment.
At Georgia-Pacific, Reese was involved in paper machine capital improvements, including installation of a new recycled linerboard machine at the Big Island, Va., mill. He developed a comprehensive interactive papermaking training program for G-P papermakers and papermaking support personnel, resulting in improved paper machine performance and significant cost reductions. His paper machine performance analysis and reporting techniques evolved over 20 years of work and are used as industry standards.
Reese has been a member of TAPPI since 1973 and is an active member of the Papermakers and Water Removal committees. He founded the Papermaking Specialist subcommittee. He was named a TAPPI Fellow in 1992 and was awarded the Harris O. Ware Prize from the TAPPI Paper and Board Manufacture Division in 1997 and the TAPPI Engineering Division Beloit Technical Award in 1999.
##SHARELINKS##
|
Market Roundup
For the fourteenth straight month, U.S. containerboard production rose over the same month a year ago, the American Forest & Paper Association (AF&PA), Washington, D.C., USA, reports in its December 2010 U.S. Containerboard Statistics Report released this week. Total production increased 40,300 tons or 1.5% compared with December 2009. Production was also up compared with November 2009; however, the month-over-month average daily production was down by 2.4%. Year-end 2010 production increased 7.1% over 2009. The containerboard operating rate for December 2010 was up 3.7 points over December 2009, to 92.6%.
Additional key findings from the report include:
- Linerboard production continued to increase over the same month last year
- Corrugating medium production also increased over last year
- Containerboard operating rates were up.
##SHARELINKS##
|
The value of softwood logs and lumber exported from North America to China reached more than $1.6 billion in 2010, which was 150% higher than the previous year and more than 10 times as much as in 2006, reports the Wood Resource Quarterly (WRQ), Seattle, Wash., USA.
The increased demand for both wood raw-material and processed forest products in China has, to a large degree, benefited the forest industry in British Columbia and the states of Washington and Oregon in the U.S., WRQ says, adding that "it is interesting to note that the two countries have chosen different paths over the past few years." In Canada, it explains, sawmills historically shipped more than 90% of their exports to U.S. markets, but this changed as demand for lumber fell when the housing bubble burst in 2008.
In the 3Q/10, less than 70% of exported lumber was destined for the U.S. market, according to WRQ. On the other hand, lumber shipments to China have gone up seven-fold the past three years and are expected to reach almost four million m3 in 2010. This makes Canada the largest softwood lumber supplier to China, having surpassed Russia in the 4Q/10.
Another factor that has had an impact on the higher Canadian lumber exports to China is the abundant supply of low-cost beetle-killed timber in British Columbia, WRQ says. Sawmills in the interior of the province have increased their production levels lately, ending up almost 20% higher in the 3Q/10 than in the same quarter of 2009. Much of the additional volume has been low-grade lumber targeted for the construction market in China. An estimated 16% of the B.C. lumber production in 2010 was exported to China.
While Canada has drastically raised lumber shipments to China in recent years, the U.S. has instead expanded exportation of logs to Chinese sawmills and plywood manufacturers, WRQ points out. In 2007, the U.S. exported less than 100,000 m3; in 2010 an estimated 2.4 million m3 was exported. The U.S. is now the third largest softwood log supplier to China, after Russia and New Zealand. The strong export market has caused sawlog prices in the U.S. Northwest to go up more than in any other region of North America the past year, according to WRQ.
More information is available online.
##SHARELINKS##
|
Total U.S. kraft paper shipments in December were 126,900 tons, an increase of 1.3% compared with December 2009, and flat when compared with November 2010, according to the AF&PA's December 2010 Kraft Paper Sector Report released this week. Total year-end shipments rose 10.2% over last year. Total inventory was 79,700 tons.
Additional key findings from the report include:
- Total unbleached kraft shipments increased over December 2009
- Total bleached kraft shipments were down compared with the same month last year.
##SHARELINKS##
|
Total U.S. boxboard production increased by 7.3% compared with December 2009, and was flat compared with last month, according to the AF&PA's December 2010 U.S. Paperboard Report released this week. Year-end production was up 3.7% over 2009.
Additional key findings of the report include:
- Unbleached kraft folding production increased
- Solid bleached folding was up over the same month last year
- Recycled folding saw a decrease in production
- Inventory of solid bleached kraft paperboard increased.
##SHARELINKS##
|
As expected, U.S. pulp prices remained flat in January on a m/m basis, Mark Wilde, senior analyst with Deutsche Bank, reports. In China, he says, prices continue to rise. NBSK rose $10/metric ton in January and is expected to rise another $10 - $20/metric ton in February. Domestic hardwood prices remain flat, but fundamentals appear weaker than softwood. "We are hearing reports of Brazilian producers offering $10- $20/metric ton discounts on BEK in the U.S," Wilde noted.
##SHARELINKS##
|
Pulp & Paper
Finland-based Stora Enso and Chile-based Arauco announced this week that their joint-venture company, Montes del Plata, will build a new state-of-the-art 1.3 million metric tpy pulp mill at Punta Pereira, in the department of Colonia, Uruguay. The total investment is estimated to be approximately $1.9 billion (EUR 1.4 billion). Each of the joint-venture shareholders has a 50% stake in the mill's equity and will be entitled to half of its output. The project will be financed about 40% through equity and about 60% through loans raised by Montes del Plata. Stora Enso is consolidating its 50% share with the equity method.
The project includes a state-of-the-art with Best Available Techniques pulp mill, a deepwater port, and a power generating unit based on renewable resources. The new mill is expected to be operational by the end of the first quarter of 2013.
The eucalyptus pulpwood will be sourced essentially from Montes del Plata's own plantations. The company currently owns 254,000 hectares of forestland in Uruguay, of which 138,000 hectares are planted, about 100,000 hectares are protected, and 16,000 hectares are suitable for planting. The project will also be of value for the economic and social development of Colonia and Conchillas, where the company is committed to an environmental performance of excellence and to working with the local authorities and the community.
"Low cost plantation-based pulp is one of the cornerstones of our strategy. Our investment is a concrete step in implementing this strategy to build the future of our Group. The Uruguayan government authorities both nationally and locally have been a welcoming supporter to Montes del Plata. We look forward to implementing the project in close co-operation with them. We are also proud to invest together with a great partner like Arauco and have a joint vision of building something in Uruguay that will be a role model for the world," says Jouko Karvinen, CEO of Stora Enso.
"We are extremely happy to see this investment becoming a reality. It is the result of hard work by the team of Montes del Plata, strong support from the shareholders Stora Enso and Arauco, and seamless co-operation between the company and the Uruguayan and Colonia authorities. A new stage is beginning in which we will strive to build a project of excellence," says Erwin Kaufmann, CEO of Montes del Plata.
The new pulp mill will be the largest-ever privately executed investment in Uruguay. The construction and operation of the pulp mill will have significant economic and social impacts in the country. An average of 3,200 and a peak of 6,000 workers will be employed during construction and about 500 people are expected to work at the mill once it is operational. The mill is forecast to have a positive impact on Uruguay's GDP of 0.8% during construction and 2% when it is operating.
##SHARELINKS##
|
AbitibiBowater, Montreal, Que., Canada, this week announced the selection of a new Executive Team, reporting directly to Richard Garneau, president and CEO. The leadership transition includes a number of senior management changes, supporting the company's execution of its business strategy. In addition to Garneau, the new Executive Team includes:
- Alain Boivin, SVP, Pulp and Paper Operations. Boivin most recently was VP of Mill Operations, Central Region at Smurfit-Stone Container and will assume his new responsibilities at AbitibiBowater on March 7. This role will be managed on an interim basis by David J. Spraley, SVP, Pulp and Paper Manufacturing, Engineering and Quality. Boivin served as a VP at Smurfit-Stone since 2000. He previously was SVP, Containerboard Operations for St. Laurent Paperboard from 1999 to 2000. Prior to that, he was mill manager at several operations for Donohue and Avenor.
- Alain Grandmont, SVP, Human Resources and Public Affairs. Grandmont most recently served as EVP, Human Resources and Supply Chain for AbitibiBowater. He was previously SVP, Commercial Printing Papers from October 2007 to July 2009, and served as SVP, Commercial Printing Papers of Abitibi-Consolidated from 2005 to October 2007 and as SVP, Value-Added Operations and Sales of Abitibi-Consolidated in 2004.
- William G. Harvey, SVP and CFO. Harvey served most recently as EVP and CFO for AbitibiBowater. He previously was SVP and CFO of the company from October 2007 to July 2009, and served as EVP and CFO of Bowater from August 2006 to October 2007, and as SVP and CFO and Treasurer of Bowater from 2005 to 2006.
- John Lafave, SVP, Pulp and Paper Sales and Marketing. Lafave most recently served as VP Sales, National Accounts - Paper Sales for AbitibiBowater. Prior to that, he was VP Sales, National Accounts - Newsprint for the company and VP Sales, Commercial Printers for Abitibi-Consolidated from 2004 to 2009. Lafave previously held positions in sales with UPM-Kymmene and Repap Enterprises.
- Yves Laflamme, SVP, Wood Products, Global Supply Chain and Information Technology. Laflamme served most recently as SVP, Wood Products for AbitibiBowater. He was previously SVP, Woodlands and Sawmills of Abitibi-Consolidated from 2006 to October 2007 and VP, Sales, Marketing and Value-Added Wood Products of Abitibi-Consolidated from 2004 to 2005.
- Jacques P. Vachon, SVP and chief legal officer. Vachon most recently served as SVP, Corporate Affairs and chief legal officer for AbitibiBowater. He previously was SVP, Corporate Affairs and Secretary of Abitibi-Consolidated from 1997 to October 2007.
All appointments are effective immediately, with the exception of Boivin who will join the company in March. Also reporting directly to Garneau is William Kerr who will serve as VP, Internal Audit. Kerr also reports functionally to the company's Audit Committee of the board.
AbitibiBowater owns or operates 18 pulp and paper mills and 24 wood products facilities in the U.S., Canada, and South Korea.
##SHARELINKS##
|
Fuel and forestry conglomerate Empresas Copec SA, Santiago, Chile, said this week that it will pursue a capital expenditure plan of between $900 million and $1.1 billion this year. During the past 20 years, Copec has made capital expenditures of some $11 billion, with around $800 million invested in 2010.
Copec's Celulosa Arauco y Constitucion SA forestry and pulp subsidiary is one of the world's top pulp producers. A massive 8.8-magnitude quake that rocked Chile's central-southern regions last February damaged and temporarily shutdown some of Copec's pulp plants.
##SHARELINKS##
|
Eldorado Celulose e Papel Ltda, Brazil, has awarded a basic and detailed engineering contract to Pöyry's Industry Business Group, Finland, for the Balance of Plant (BOP) of the 1.5 million metric tpy bleached eucalyptus market pulp mill to be built in Mato Grosso do Sul state, Brazil. The assignment also includes the suppliers' document management. The value of Pöyry's contract is about EUR 8.4 million. The duration of Pöyry's engineering services is about 14 months.
The contract is a continuation of the pre-engineering and preparatory work for the mill infrastructure that Pöyry was awarded in early 2010.
The mill design is based on best available technologies and best environmental practices. Technical and environmental criteria for the project are based on international norms and standards and, mainly, on the Brazilian experience, which will make it possible for the mill to produce more with less use of natural resources, low production costs, progressive environmental impact reduction, and minimum work accident risks, Pöyry notes.
##SHARELINKS##
|
Fortress Paper Ltd., Vancouver, B.C., USA, reports that it has successfully completed the acquisition of Bank of Canada's Optical Security Material (OSM) division that produces optically variable material for security threads contained in various banknotes, including Canadian banknotes. The company also reports that it has completed the rebuild of Paper Machine No. 1 at its Landqart Mill in Switzerland, previously announced in January 2010, materially on budget. Rebuilt PM 1 is currently in the paper production testing phase.
The OSM Assets acquired by Fortress include certain patent applications and intellectual property rights to optical security features, unique security applications, and substantially all of the production equipment and machinery currently used at the OSM division.
PM1 was rebuilt into a banknote and security papers machine. Prior to the rebuild, it produced specialty papers and low to medium security papers. The rebuild is expected to increase the company's aggregate banknote and high security papers production capacity from the current 2,500 metric tpy to approximately 10,000 metric tpy.
Fortress Paper operates three mills, the Landqart mill, the Dresden mill in Germany, and the Fortress Specialty Cellulose mill in Quebec, Canada.
##SHARELINKS##
|
M-real Corp., Espoo, Finland, part of Metsäliitto Group, reports that it has started a new profit improvement program for this year. The program focuses on improving the paper business profitability as well as decreasing variable costs of all businesses. The earlier announced profit improvement impact of Simpele and Kemi cartonboard investments and the closure of the specialty paper production at Simpele are included in the new profit improvement program.
The planned measures are expected to improve M-real's annual operating result by EUR 70 million, with full effect from 2012 onwards. The planned measures would improve 2011 results by approximately EUR 30 million. Total 2011 results are thus expected to improve by approximately EUR 90 million, including the impact of the new program and the previous years' profit improvement programs.
"M-real has a good possibility to mostly cover the accelerated cost inflation by its own profit improvement measures. In addition to the earlier implemented measures and this new program, further profit improvement actions will be searched. The focus of the earlier profit improvement programs has been on decreasing fixed costs. M-real has, in upcoming years, significant profit improvement potential especially in variable costs, concerning primarily chemical, energy, and logistic costs", said Mikko Helander, CEO of M-real.
##SHARELINKS##
|
PaperWorks Industries Inc., Philadelphia, Pa., USA, reported this week that Manchester Industries, a major North American converting company, has been acquired by Sun Capital Partners. Manchester will ultimately be merged into PaperWorks, itself an affiliate of Sun Capital Partners.
With five facilities in Michigan, Indiana, Pennsylvania, Virginia, and Texas, Manchester Industries provides large-scale sheeting, rewinding, and cutting operations to commercial printers and packaging companies across the continent. The company's 180 employees will become part of the PaperWorks Paperboard Group.
"Manchester Industries has carved out its place as a world-class converter," said PaperWorks Industries CEO Thomas J. Garland. "These five plants will be a significant asset for PaperWorks as we move forward, and we intend to spare no effort to ensure that Manchester's reputation for service and reliability is honored as they become part of the PaperWorks family. Its FSC, SFI, and PEFC certifications show a commitment to quality that we will be proud to uphold.
"This converting capacity will be a great asset to our existing core service of paperboard manufacturing, With Manchester offering over a dozen paperboard grades and a range of services that start at custom sheeting and cutting and extend to almost every dimension of conversion, this adds an entire range of expertise to our Paperboard Group," Garland said.
Founded in 2008, PaperWorks Industries is an integrated full-service packaging provider. The company's Packaging Division produces specialized folding cartons, with facilities in the U.S. and Canada. Its Paperboard Division manufactures approximately 300,000 tons of 100% recycled paperboard every year for a variety of end uses largely concentrated in consumer products.
##SHARELINKS##
|
SCA, Sweden, reported this week that it is implementing three internal changes to its Corporate Senior Management Team, effective March 31. Christoph Michalski has been appointed the new president of SCA Global Hygiene Category. Michalski is currently president of SCA Asia Pacific.
Ulf Söderström has been named the new president of SCA Asia Pacific. Söderström currently holds the position of SVP, Business Development and Strategy, and in that role is also responsible for mergers and acquisitions, business intelligence, and IT.
Robert Sjöström has been appointed the company's new SVP, Business Development and Strategy, and in that role will also be responsible for mergers and acquisitions, business intelligence, and IT. Sjöström is currently president of SCA Global Hygiene Category.
Michalski, Söderström, and Sjöström will continue to serve as members of the Corporate Senior Management Team and report to the company CEO.
"These changes will allow us to capitalize on the collective know-how of our leaders. We are working continuously to develop the organization and our managers with the aim of advancing our business. These changes are part of this effort," Jan Johansson, president and CEO of SCA, noted.
##SHARELINKS##
|
UPM, Helsinki, Finland, has selected Rauma as the possible location for a biorefinery in Finland. Rauma was chosen ahead of Kuusankoski for two key reasons the company says—more efficient energy utilization, and lower investment costs, e.g, in foundation work. UPM has not yet made an investment decision on building the biorefinery.
UPM considered three different locations — Rauma, Kuusankoski, and Strasbourg, France— for its biorefinery, which will produce second generation biodiesel from energy wood—logging residues, stumps, and bark. UPM has not yet decided whether the biorefinery will be located in Rauma or in Strasbourg where the environmental impact assessment is still ongoing.
UPM will apply for the EU's NER300-grant for biorefinery investment both in Finland and France. Last autumn, EU officials announced that decisions on grants would be made in 2011. According to the most up-to-date information, the decisions are now not expected before the second half of 2012. "Investment decision regarding the biorefinery can be made only after the EU's grant decisions are announced," said Petri Kukkonen, director, UPM Biofuels Business Area.
The planned biorefinery would use gasification and Fischer-Tropsch processes to produce biodiesel from energy wood.
UPM further reports that it is investigating the production of various second generation biofuels. The environmental impact assessment for a possible liquid biorefinery at Lappeenranta, Finland, is now complete. The plant will be built at the Kaukas mill site and the main products of the liquid biorefinery will be transportation biofuels produced with hydrotreatment technology. Raw materials would be biobased liquids such as fats, oils, and forest industry by-products.
The state authority, the Southeast Finland Regional Centre for Economic development, Transport and the Environment, has issued its official statement about the assessment. In the statement, the authority speaks highly of the assessment made by UPM and includes detailed information about the different implementation alternatives and their environmental impacts. The authority concluded that the assessment is sufficient and meets the requirements of the EIA law and statute.
The Kaukas liquid biorefinery is planned to be built in stages. In the first phase, the plan is to build a 20,000 metric tpy test and training facility that could also begin small-scale industrial production. The EIA also includes an assessment of a larger scale commercial size plant that has a total annual production capacity of up to 200,000 metric tons. UPM has not yet made an investment decision to build the Kaukas liquid biorefinery.
"We are making preparations concerning both the technical and permit issues in the light of an investment decision. We aim to make an investment decision on the liquid biorefinery test and training facility this year," says Kukkonen.
##SHARELINKS##
|
Containerboard/Packaging
Demand for green packaging in the U.S., comprised of recycled content, reusable, and degradable packaging, is projected to increase 3.9% yearly to $41.7 billion in 2014, consuming 58 billion lb of material, according to a new report titled Green Packaging, released this past week by the Fredonia Group, Cleveland, Ohio, USA. Growth will outpace overall packaging demand but will remain relatively moderate due to the maturity of many products and the large existing presence of recycled content packaging in paperboard and metal packaging. The fastest gains, the report notes, are anticipated for degradable packaging and plastic recycled content packaging.
Degradable packaging is forecast to expand 13.6 % annually to $685 million in 2014, driven by price competitiveness with conventional resins, capacity expansions, and rising demand for environmentally friendly manufactured goods. Advances will also be based on enhanced performance properties resulting from blending and other modifications, initiatives by brand owners to improve the environmental footprint of their packaging, and legislative bans on polystyrene foam foodservice disposables in some parts of the country. Preventing faster advances will be the maturity of some product types (e.g., ring carriers, loose-fill), the lack of consumer composting networks in most areas of the U.S., and competition from emerging green packaging materials such as non-biodegradable bioplastics.
Recycled content packaging constitutes the vast majority of green packaging and demand is forecast to increase 3.6% annually to $37.3 billion in 2014. Gains will be supported by increased collection activity and processing capacity, coupled with greater use of recycled content packaging by firms seeking to demonstrate environmental responsibility and differentiate their products. Robust growth is anticipated for plastic recycled content packaging based on more concerted collection efforts and expanded processing capacity, especially for food-contact approved resin grades.
Reusable packaging demand is expected to post above-average growth through 2014, improving from the 2004-2009 pace based on a rebound in manufacturing activity from a weak base in 2009. Demand for reusable plastic containers and intermediate bulk containers will benefit from an upswing in manufacturing activity and inroads into lower capacity packaging types such as drums, pails, and shipping sacks.
More information about this report is available online.
##SHARELINKS##
|
Packaging Corporation of America (PCA), Lake Forest, Ill., USA, this past week announced that Charles J. (Jack) Carter has been named VP, Containerboard with responsibility for the company's four containerboard mills and support operations. Carter will report to Mark W. Kowlzan, CEO of the company. Kowlzan was previously responsible for mill operations prior to being named CEO in June 2010.
Carter joined PCA in March 2010 as director, Papermaking Technology. He has almost 30 years of forest products industry experience working in key management positions. Prior to joining PCA, he was VP and GM of Abitibi Bowater's Calhoun, Tenn., mill.
PCA is the fifth largest producer of containerboard and corrugated packaging products in the U.S. with sales of $2.15 billion in 2009. It operates four paper mills and 67 corrugated product plants in 26 states across the country.
##SHARELINKS##
|
Siam Kraft Industry Co., Thailand, has ordered a Petax filtration system from Kadant UK Ltd., Bury, Lancashire, U.K., a subsidiary of Westford, Mass., USA-based Kadant Inc. The Petax filtration system allows for the recycling of white water used in the papermaking process via single-stage filtration of liquids containing a high level of suspended solids. The equipment is similar to that supplied in 2009 for another kraft packaging plant in Thailand operated by the same group. The systems are expected to be delivered to the mill in the second quarter.
"The exceptional filtration offered by the Petax filtration system, removing almost all of the suspended solids over 30 microns in size in the filtrate, is achieved without the addition of chemical flocculants, fiber sweetener stock, or precoats," stated Ron Chambers, managing director of Kadant UK. "The past performance of a Petax system at a sister mill in Thailand provided strong support and rationale for the purchase of these two units by Siam Kraft Industry. We are pleased to see the value our customers place on Kadant's water management solutions to reduce water consumption and effluent in the papermaking process."
Kadant UK Ltd. is a provider of doctor blades, doctor blade holders, and doctoring systems for papermaking and other industrial processes. The division's water management products are applied to the cleaning of forming and press fabrics and the filtration of process water, while its fluid handling products, including steam systems and related components, are used to optimize heat transfer in rotating cylinders and fluid-handling systems.
##SHARELINKS##
|
Published Pricing
DuPont Titanium Technologies, Wilmington, Del., USA, has announced a price increase of Yen 40 per kg for all DuPont Ti-Pure® titanium dioxide grades sold in Japan. The price increase becomes effective February 1.
In the U.S., DuPont Titanium Technologies operates plants at DeLisle, Miss., New Johnsonville, Tenn., and Edge Moor, Del. The company also operates plants at Altamira, Mexico, and Kuan Yin, Taiwan, all of which use the chloride manufacturing process. The company also operates a mine in Starke, Fla., USA.
##SHARELINKS##
|
Kemira, Finland, will raise paper chemicals prices in all major markets, effective February 1 or as contracts allow. The increases will range from 5% to 15% depending on specific product. The company attributes the increases to escalating energy, raw material, and freight costs.
##SHARELINKS##
|
People
Boise Inc., Boise, Idaho, USA, has elected Bernadette Madarieta VP and controller, effective February 1. Madarieta became Boise Cascade LLC's VP and controller in February 2008. From October 2004 to January 2008, she served as director of financial reporting. From 2002 to October 2004, she served as supervisor of external financial reporting for Boise Cascade Corp.
Prior to joining Boise Cascade Corp., Madarieta was an assurance and business advisory manager at KPMG and Arthur Andersen, where she was responsible for planning and supervising audit engagements for corporations and privately held companies. She received a B.B.A. in accounting from Boise State University, where she was a top 10 scholar, and is a certified public accountant.
"We are very pleased that Bernadette is joining Boise Inc.," said Sam Cotterell, SVP and CFO for Boise Inc. "She knows our company and industry well and is a proven leader in the areas of accounting and control."
##SHARELINKS##
|
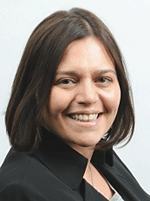 Baisch Engineering, Kaukauna, Wis., USA, has hired Christina FitzGerald as business development and marketing manager. FitzGerald has 13 years of marketing experience in the architectural/engineering/construction industry. Prior to joining Baisch Engineering, she was marketing manager at an engineering firm in Boston, Mass.
FitzGerald is a Certified Professional Services Marketer (CPSM) with a B.A. degree in Journalism/Public Relations from Northeastern University. A member of the Society for Marketing Professional Services (SMPS), she served on SMPS Boston's Board of Directors for five years.
Kurt Kloehn, president of Baisch Engineering, said that "we're thrilled to have Christina onboard. Her experience and background provides an invaluable resource to Baisch and our clients."
Baisch Engineering has 80 employees and was founded in 1958. The company provides services nationally and internationally, including process, mechanical, civil, structural, architectural, electrical, instrumentation and process control, and project administration.
##SHARELINKS##
|
Circonix Technologies, Ringwood, N.J., USA, an engineering company supplying drive and control systems to web coaters and converters, reports to have added three engineers to support its systems integration business in Ringwood and its Fulton Machinery equipment fabrication division, in Phoenix, N.Y.
Larry Ostness is a mechanical engineer with a broad range of experiences involving the design of converting equipment. Mike Brubaker brings his knowledge of converting machinery assembly and installation into his new role of machinery design engineer. Both Ostness and Brubaker have 30-plus years of experience in the converting industry. Jaclyn Grant is a recent mechanical engineering graduate from Binghamton University, and will be involved with not only machinery design, but with onsite installation as well. She will be working at Circonix's Ringwood facility.
##SHARELINKS##
|
Dr. (Chem.Eng.) Heidi Fagerholm has been appointed EVP for Research & Development and Technology, and a member of the Strategic Management Board of Kemira, Finland. Fagerholm will also continue until further notice as head of the Espoo R&D center in Finland, in which position she started last November.
Fagerholm joined Kemira from Ahlstrom Group where she worked as VP, Product Development. Before joining Ahlstrom she has held leading positions in chemical industry companies, one being the head of the Technical Center Europe of Ciba Specialty Chemicals Oy. She succeeds Johan Grön, who will leave Kemira, and reports to Harri Kerminen, Kemira's president and CEO.
##SHARELINKS##
|
Tank cleaning specialist company Gamajet Cleaning Systems, Exton, Pa., USA, has promoted Tadd Wolff from Sanitary Division manager to VP of Distributor Relations. Wolff will be responsible for spearheading Gamajet's efforts to grow distribution within the U.S. as well as internationally. In addition to growing the channels of distribution, he will also be working with current distributors to further develop and streamline their sales and service efforts.
Wolff has 15 years of experience working with both customers and distributors, two of which were at Gamajet. He holds a B.A. degree in Interpersonal Communications from West Virginia University.
##SHARELINKS##
|
TAPPI News
Corrugators are increasingly complex and processes are often changing. It might be time to catch up on the latest information and techniques from some of the sharpest minds in the industry. Here's where you can access that knowledge...
Register for the TAPPI Best Practices on the Corrugator Course February 15-18. You will learn how to:
• Increase productivity and improve quality
• Reduce excess waste
• Adopt the "Centerline Process" to achieve a product that is consistent on every shift
• Maintain quality while reaching maximum corrugator speeds
• Reach the maximum yield of boxes from the paperboard consumed
• Troubleshoot most common operational problems
• Recognize critical properties of paperboard, starch adhesive and how to control warp
The Proposed Course Schedule shows the content offered each day.
Important Information: Register online or by printing this Registration Form for up to $200 in savings on course registration. Bring your questions and corrugator issues to the instructors and you'll take home knowledge and skills that will make 2011 the most productive year yet!
Meet the Course Faculty
The Best Practices in Corrugator Operations Course is taught by Rick Croker, John Troyke, and John Buzzell. Croker has been in the corrugated industry for more than 30 years. He is the Director of Technical Services for Georgia-Pacific Corporation. Troyke is a Sr. Technical Service Representative for Georgia-Pacific Corporation. He specializes in corrugated trouble shooting and has been an instructor at TAPPI's Corrugated Press Hands-On Workshop. Buzzell is a Sr. Technical Service Representative for Georgia-Pacific.
Guest speakers include Pete Snyder, National Accounts, Harper/Love Adhesives; Steve Schmidt, Vice President, Copar Corporation; James Moody, Manager, Packaging Testing Labs, Georgia-Pacific Corporation; Jon Porter, Senior Trainer/ Process Specialist, Fosber America, and Craig Machamer, Steam Systems Specialist.
We look forward to seeing you here February 15-18 at TAPPI!
##SHARELINKS##
|
TAPPI and the Recycled Paperboard Technical Association (RPTA) announced today that RPTA will locate its annual Production-Technical (P-T) Seminar at TAPPI's PaperCon 2011 on May 2-3, 2011, in Covington, Ky., USA, near Cincinnati.
"Co-locating our event with PaperCon will allow RPTA members more educational and networking opportunities," said Deborah White, executive director of RPTA. "We are very excited to hold our conference at TAPPI's world-class event."
RPTA members will have access to the PaperCon Opening Session and Keynote, Executive Panel, Trade Fair, New Technology Showcase, Poster Sessions and hospitality receptions, in addition to the popular P-T Seminar sessions organized by RPTA expressly for the recycled board industry. Likewise, PaperCon attendees will be permitted to join the P-T sessions.
"We've been fans of RPTA for a long time and are excited to have our RPTA friends join us at PaperCon," said Larry N. Montague, president and CEO of TAPPI. "Recycled paperboard is an important market segment and the information shared by co-locating our two meetings will only benefit the industry."
PaperCon is North America's largest pulp and paper conference, bringing together industry leaders, technical experts, and manufacturing professionals from around the world. In 2011, the theme is "Rethink Paper: Lean and Green," highlighting new ways to improve efficiency, use less water, fiber and air, and achieve operational excellence. The unique program of peer-reviewed papers and invited speakers will attract CEOs, mill managers, superintendents, scientists and engineers from around the world.
PaperCon brings together members with decades of experience in leading, producing and advancing technology for the pulp and paper industry as well as a strong history of more than 90 years in organizing key industry educational programs, conferences and exhibits. PaperCon combines TAPPI's expertise in papermaking, coating, and leadership/management topics with information from producers, government and academic entities, technology suppliers, consumers and associations in multiple industries looking for more cost effective and profitable ways of doing business. New for 2011, special forums are planned on tissue making, sustainability and maintenance.
For program details visit www.papercon.org.
##SHARELINKS##
|
Lake States TAPPI and North Central PIMA have jointly arranged a one-day conference "Maintenance - Maximize Uptime" on February 16 at the Westwood Conference Center in Wausau, Wis. The program focuses on improving the uptime/availability/time efficiency of paper production lines and includes papers by Verso Paper, Packaging Corporation of America, and many others.
For your information, an overview of the conference program as well as directions to the event, visit the Lake States TAPPI website or contact Clark Schabo at 920-734-5073.
##SHARELINKS##
|
Join your colleages for the 13th Annual European PLACE Conference, 30 May to 1 June 2011 at the Festspiel- und Kongresshaus in Bregenz, Austria.
The technical program for this biennial conference will have a special emphasis on the latest trends and technologies relating to extrusion, coating, and lamination of web-based materials.
This is your opportunity to hear presentations focusing on:
• Packaging & Society
• Polymers and Paper
• Solid Conveying
• Laminator Hardware
• Sustainability
• Adhesion Issues
• Resin Tool Box
• Interactive Packaging
• Curtain Coating
• Ultrasonic Sealing
• Adhesives
• Inspection
• Regulatory
• Extrusion Coating Process
• Innovation Counter
• Packaging Performance
In addition to these topics, the program will also include a Poster Session and Table Top Walk.
Register online now or download the faxable registration form.
Sponsorship opportunities are available.
##SHARELINKS##
|
PaperWeek Canada will be held at the Fairmont Queen Elizabeth Hotel, in the heart of downtown Montreal, from February 1-3, 2011. The annual PaperWeek conference will feature technical tracks that help share technological advancements, and also for its new business tracks developed to share strategic visions regarding today's challenges and opportunities. With presentations from experts such as scientists, consultants, equipment and service suppliers, and analysts, PaperWeek Canada attracts many other participants from engineers, mill managers and industry leaders to governmental employees, students and allied sector representatives.
PAPTAC is a Canadian-based non-profit organization, dedicated to improving the technical and professional capabilities of its members worldwide, and to the advancement of the pulp and paper industry.
For more details, visit http://www.paperweekcanada.ca
##SHARELINKS##
Colin South, Ph.D., of Lignol Innovations Corp. and Rick Holley of Plum Creek will deliver keynote addresses at the BioPro Expo & Marketplace™ and the International Bioenergy and Bioproducts Conference (IBBC), which will take place in Atlanta on March 14-16, 2011, at the Atlanta Hilton.
BioPro Expo is the largest conference and exhibition in the Southeastern United States covering the full biomass processing spectrum for multiple industries, from supply through demand and utilization. In-depth educational sessions are backed by a trade show focused on cutting-edge technology, products and services available today. This event examines practical methodologies for quickly transitioning products, residues and waste streams into energy and biofuel.
Dr. South has diverse experience in the area of engineering, management and entrepreneurship. A chemical and bioprocess engineer by training, he has held a range of technical and leadership roles in the engineering, chemical, food and biotech industries. Active in the alternate fuels and chemicals area for much of his career, Dr. South graduated with a degree in Chemical and Process Engineering from the University of Canterbury in New Zealand. He received his Ph.D. in Bioprocess Engineering at Dartmouth College, completing his thesis in the area of cellulosic ethanol production.
Currently he is the Chief Technology Officer of Lignol Innovations Corp., a Burnaby, B.C.-based company developing green fuels and chemicals from lignin, a multifunctional naturally occurring aromatic polymer. Additionally, he is the CEO of Novogy, a renewable fuels company based in Cambridge, Mass., and was the founding President of Mascoma Corporation, an industry-leading company developing and commercializing advanced biotechnology solutions for second-generation cellulosic ethanol.
Holley was elected President and Chief Executive Officer and a member of the Board of Directors of Plum Creek in 1994. Prior to assuming this role, he served as Vice President and Chief Financial Officer since 1985. Holley began his career at General Electric Company in 1974, where he served in a variety of financial management positions. In 1983, he joined Burlington Northern Inc. where he worked as assistant vice president, corporate audit. He held that position until joining Plum Creek in 1985.
He received a bachelor of science degree in accounting and business administration from San Jose State University. He also completed an advanced education program at Northwestern University. In addition to serving on Plum Creek's board, Holley serves on several private and not-for-profit boards including the Sustainable Forestry Initiative Inc., National Alliance of Forest Owners and the Blethen Corporation.
More information about BioPro Expo & Marketplace is available online.
##SHARELINKS##
Congratulations to the newest members of the TAPPI/PIMA Young Professionals Committee.
Fourteen young professionals in the pulp, paper and converting industry have joined the committee, a group shaped by soon-to-be college graduates, recent graduates, young professionals in the industry, and accomplished professionals who want to build connections and provide networks for its members. Its purpose is to encourage younger individuals to get involved and advance the industry by building from fresh, creative and driven minds.
The new members and their affiliations are: Laura Beauchesne – White Birch Paper; Maggie Gerhart – International Paper; Zachary Growe – Weyerhaeuser; Nichole Hartley – Ashland; Natalie Hughey – International Paper; Tim Li – Amec; Jamie Percy – Alpac; Eric Schweighofer – Rio Tinto; Derek Sorensen – Alpac; Michael Subilia – Sappi Fine Paper; Dan Sweeney – Utah University; Emily Tomes – Ashland; Ashley Urbanski – BHS; and Bailey Wandyg – Naval Surface.
Currently the Young Professionals Committee is working on installing a new Young Professionals track at 2011 PaperCon, heading a Young Professional Round Table at the 2011 Student Summit in Kingsport, Tenn., incorporating networking events at all TAPPI Conferences, and reaching out and engaging newly graduated young professionals.
The committee is in need of additional young professionals to be a part of the Young Professional Technical Track at 2011 PaperCon, which will include speakers, session chairs, and co-chairs. For each of the sessions, there will be one professional and one young professional teamed up to work together to produce an excellent session.
The rewards for a young professional to get involved include fine-tuning leadership, speaking, and presentation skills, the ability to work side by side with respected industry experts, and the chance to experience the ins and outs of a professional and technical conference in the paper industry.
Those interested in becoming involved and active on the Young Professionals Committee and 2011 PaperCon should contact Libby Hardison.
##SHARELINKS##
|
With a new name that reflects a growing interest in the nanotechnology sector, the TAPPI 2011 International Conference on Nanotechnology for Renewable Resources takes place June 6-8, 2011, in Arlington, Va. USA. The conference will provide the latest findings in research and applications in nanotechnology from around the world.
In its sixth year, this conference continues to grow and is a gathering place for a unique community of industry experts, scientists, health and safety specialists, legal and government policy makers, and leading researchers to learn about the latest in nanotechnology research and development.
Formerly known as TAPPI's International Conference on Nanotechnology for the Forest Products Industry, the title of this annual conference has been changed to reflect the advances in nanotechnology in renewable materials and their widespread applications in many other industries.
This year's conference theme is "Nanotechnology for a Sustainable Future." Presentations will focus on several key thematic areas such as:
• Nanocellulosics and Nanocomposites
• Applications of Renewable Nanomaterials
• Nanostructured materials by Self Assembly
• Nanotech Coatings and Novel Nano-Enabled Functionalities
• Governmental & Environmental Issues
Abstracts are currently being accepted for this one-of-a-kind event. View the call for papers.
The TAPPI 2011 International Conference on Nanotechnology for Renewable Resources will take place at the Sheraton Crystal City in Arlington, Va. More information is available online.
##SHARELINKS##
"To write that essential book, a great writer does not need to invent it but merely to translate it, since it already exists in each one of us. The duty and task of a writer are those of translator." – Marcel Proust, novelist (1871-1922)
##SHARELINKS##
|
|