 |
|
Weekly Spotlight
Sappi Fine Paper Europe (SFPE), Brussels, Belgium, this week reported that, due to the continued market decline and resulting overcapacity in the European coated paper markets, combined with high raw material costs not compensated for by higher selling prices, it will concentrate its production at fewer sites
Learn More...
|
Italy-based tissue producer Sofidel will acquire NTG Papermill Limited (tissue) in the U.K. Lancaster area
Learn More...
|
UPM, Helsinki, Finland, reports that, with respect to its goal of simplifying its operating models and structures to address the competitive challenge in mature European business, UPM Paper ENA, which becomes effective on November 1, plans to reorganize its head office activities
Learn More...
|
In a joint effort promoting stewardship, environmental responsibility, and community engagement, Catalyst Paper, Richmond, B.C., Canada, this past week partnered with Halalt First Nation, with support from the Young Professionals of Cowichan, Crofton Fire Hall, and Island Corridor Foundation, to participate in the Great Canadian Shoreline Cleanup, a conservation initiative of the Vancouver Aquarium and World Wildlife Fund of Canada
Learn More...
|
Changing markets, mill cutbacks and closures, changing rules for employment law, and new health care regulations—this is the stuff of nightmares for today's industry HR managers
Learn More...
|
Market Roundup
Wood chip and pulp log prices fell in many regions of the world during the 2Q/13, with the biggest declines occurring in Japan, Brazil, and Spain
Learn More...
|
The return of the U.S. housing market is driving up demand for lumber and wood panel products
Learn More...
|
The global paper and paperboard market had total revenues of $389.9 billion in 2012, representing a compound annual growth rate (CAGR) of 2.3% between 2008 and 2012
Learn More...
|
Pulp & Paper
The City of Port Alberni, B.C., Canada, completed its purchase of the Catalyst Paper (Richmond, B.C.) wastewater treatment facility and additional lands as scheduled on September 30, in accordance with formal agreements endorsed by both parties
Learn More...
|
Celulosa Argentina, Argentina, has ordered from Voith Paper, Germany, a complete tissue production line
Learn More...
|
Fortress Paper Ltd., Vancouver, B.C., Canada, this week announced that its Fortress Specialty Cellulose (FSC) Mill successfully installed a new high pressure water pump for its cogeneration facility and synchronized the cogeneration facility with the Hydro Québec grid without issue
Learn More...
|
In line with the theme of this year's 52nd Man-made Fiber Congress meeting September 11 -13 in Dornbirn, Vorarlberg, Austria, Kelheim Fibres, Bavaria, Germany, reported on several "new challenges and new solutions" for its specialty fiber products and markets
Learn More...
|
Kawanoe Zoki, Japan, and Metso, Finland, have extended their cooperation in tissue making technology to include the marketing and supply of Advantage DCT 40 and 60 technologies to the Chinese market
Learn More...
|
Mercer International Inc., New York, N.Y., USA, this week announced that its Stendal facility in Germany has successfully amended its senior project finance credit facility (approximately EUR 413 million outstanding) and its EUR 17.0 million amortizing term facility in respect of Project Blue Mill (approximately EUR 15 million outstanding)
Learn More...
|
Metsä Tissue, Finland, part of Metsä Group, will invest in a tissue machine upgrade at its Raubach mill in Germany
Learn More...
|
AstenJohnson, Charleston, S.C., USA, reports that its new AccuFlow™ II press fabric is getting an outstanding reception from printing and writing paper producers
Learn More...
|
Tembec, Montreal, Que., Canada, this week announced that it will sell approximately 1,875 hectares of land within the Regional District of East Kootenay, B.C., to Jemi Holdings Ltd. for $4.2 million
Learn More...
|
Containerboard/Packaging
Folding carton producer Mod-Pac Corp., Buffalo, N.Y., USA, reports that its shareholders approved, at a special shareholder meeting this past week, the going-private merger agreement under which Kevin T. Keane, chairman, and Daniel G. Keane, president and CEO
Learn More...
|
Rengo Co., Kita-ku, Osaka, Japan, has announced that Thai Containers Group Co. (TCG), Thailand, a joint venture between Rengo and SCG Paper Public Co., a subsidiary of The Siam Cement Public Co., has completed the acquisition of a 90% stake in PT Primacorr Mandiri, which operates a plant in the suburbs of Jakarta, Indonesia
Learn More...
|
|
New Products
Archroma, Reinach, Switzerland, this week announced its official launch as a newly formed global color and specialty chemicals company that comprises the former Paper Solutions, Textile Specialties, and Emulsion Products businesses of Clariant
Learn More...
|
Menges Roller Co, Wauconda, Ill., USA, a designer and manufacturing of precision rollers for the paper converting industries, has announced the enhancement of its engineering department capabilities
Learn More...
|
Metso has launched polyurethane roll covers for tissue machine press and suction press rolls
Learn More...
|
UPM Raflatac, has introduced a range of next-generation labelstock products that offer fit-for-purpose performance for the main end-use segments
Learn More...
|
Published Pricing
Metsä Fibre, Finland, has increased the price of its Botnia Nordic Pine NBSK (northern bleached softwood kraft) pulp in Europe, effective October 1
Learn More...
|
Södra, Sweden, this past week also raised the price of its NBSK (northern bleached softwood) pulp to $900 per metric ton
Learn More...
|
People
Motion Industries, Birmingham, Ala., USA, a distributor of industrial maintenance, repair, and operation (MRO) replacement parts, is pleased to announce that Tim Breen has been named president and COO
Learn More...
|
Mikko Forsell, M. Sc. (Econ.), M. Sc. (Tech.), has been appointed Metsä Tissue's CFO and a member of Metsä Tissue's management team, effective Jan. 1, 2014
Learn More...
|
Motion Industries, Birmingham, Ala., USA, a distributor of industrial maintenance, repair, and operation (MRO) replacement parts, has named Joe Limbaugh VP-Operations
Learn More...
|
TAPPI News
This TAPPI member's career passion began on her first day of college studies.
Learn More...
|
This powerful new industry-specific search engine will help TAPPI members learn about vendors, but we will need your initial input to make this a success.
Learn More...
|
There is still time to register for TAPPI 2013 CorrExpo, October 7-9, at the JW Marriott in Indianapolis, Ind., USA.
Learn More...
|
Doug Sweet, of Doug Sweet and Associates, will present "Paper Machine Vacuum Systems 101" on October 7 at 2:00 p.m. EST.
Learn More...
|
Maintenance course returns October 8-10 in Raleigh, N.C., USA.
Learn More...
|
TAPPI members save $40 off the list price of this unique text that illustrates many different problem solving technologies by example, as well as introducing plant-proven tools that will help you quickly find solutions to your toughest problems.
Learn More...
|
The TAPPI Microbiology and Microbial Technology committee has announced the next webinar in its series on Microbes in Papermaking, to be held October 16 at noon EST.
Learn More...
|
Tighten-up plans to attend the Piping System Training courses planned for two locations coming this fall, October 2-3, in Chicago, Ill., and October 23-24 in Houston, Texas.
Learn More...
|
Annual meeting on November 6 will feature an informative one-day conference titled "Safety: Best Practices" with speakers presenting various safety topics that could impact our work and personal lives.
Learn More...
|
Lake States TAPPI/North Central PIMA will hold its annual Energy Technical Program on November 6 in Neenah, Wis., USA.
Learn More...
|
TAPPI's 2013 Nominating Committee presents a slate of candidates for three director positions on the TAPPI Board.
Learn More...
|
Abstracts addressing the latest advances in characterization, functionalization, modeling, new products, applications, and health and safety issues of renewable and sustainable nanomaterials are sought.
Learn More...
|
Don't miss out on your chance to present at the largest program for the pulp and paper industry.
Learn More...
|
TAPPI members save $70 dollars off the list price. A percentage of proceeds from the sale of this book go to the TAPPI Foundation.
Learn More...
|
Foundations of Leadership Excellence, Oct. 22-24, 2013, is focused on the fundamentals of leadership and management skills for emerging leaders, high-potentials, and area operating managers and other technical professionals.
Learn More...
|
Members save $77 off the list price on the new 5th edition.
Learn More...
|
Join more than 7,000 TAPPI members across the world with 650-plus years of industry experience.
Learn More...
|
This once-in-a-lifetime event will expand public awareness, foster further connection, and provide outstanding opportunities for collaboration, growth, and investment in our future for all of those involved.
Learn More...
|
As TAPPI's 100th year approaches, we are looking for donations to the TAPPI Library.
Learn More...
|
|
Find us on Facebook
Network with us on LinkedIn
Follow us on Twitter
|
Weekly Spotlight
Sappi Fine Paper Europe (SFPE), Brussels, Belgium, this week reported that, due to the continued market decline and resulting overcapacity in the European coated paper markets, combined with high raw material costs not compensated for by higher selling prices, it will concentrate its production at fewer sites. To help return the company's operations to profitability, it will close the Nijmegen Mill in the Netherlands and shift its entire production to other Sappi mills in Europe.
The decision comes after an exhaustive review of Sappi's European production assets indicated that shutting down the Nijmegen Mill would be the preferred option. The aim of this action would be to optimize Sappi's entire heat set web offset (HSWO) business.
To identify possible alternatives for the future of the Nijmegen Mill, SFPE says it has initiated a process of consultations with its Nijmegen Mill employee representatives and social partners as well as the works council. The mill currently employs 192 people.
Should the relocation go ahead, SFPE capacity for WFC reels would reduce by 240,000 tons.
Back To Top
|
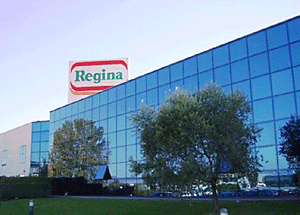 Italy-based tissue producer Sofidel will acquire NTG Papermill Limited (tissue) in the U.K. Lancaster area. The acquisition enables Sofidel to optimize the operations of its converting plants in the U.K. Sofidel, one of the leading European manufacturers of paper for hygiene and domestic use, reached agreement for acquisition of the shares of NTG Papermill earlier this week, on Monday, September 30, and it became effective October 1.
The tissue mill, that is located in the North West of England, Lancaster area, is equipped with a paper machine with a capacity of approximately 32,000 metric tpy.
"Through this acquisition, we further strengthen our production capacity in a major market place such as Britain. It is a move that enables Sofidel to optimize the operations of its converting plants in the U.K." said Luigi Lazzareschi, CEO of Sofidel.
Sofidel, a privately held company owned by the Stefani and Lazzareschi families was established in 1966. The Group has 27 subsidiary companies in 13 countries (Italy, Spain, Sweden, the U.K., Belgium, France, Croatia, Germany, Poland, Romania, Greece, Turkey, and the U.S.) and more than 5,000 employees. With an aggregate turnover of EUR 1,511 million, Sofidel is the second largest producer of tissue paper in Europe and the sixth in the world.
Back To Top
|
UPM, Helsinki, Finland, reports that, with respect to its goal of simplifying its operating models and structures to address the competitive challenge in mature European business, UPM Paper ENA, which becomes effective on November 1, plans to reorganize its head office activities. The aim is to improve profitability by creating a leaner management structure. In this regard, UPM Paper ENA's head office will be relocated from Helsinki to Augsburg to be near the main markets and close to customers.
The planned changes will have an impact to the whole UPM Paper ENA's way of working. According to the plan, the new organization would be smaller than the current one and have less organizational layers. The new leaner management structure will improve agility and speed up the decision making process. The management will also have a strong operational focus, the company notes.
The employee consultation process in Finland will be started immediately, covering the current head office staff of UPM Paper Business Group. This employee consultation process does not cover Tampere Supply Center nor the mill organizations. The number of positions affected by the planned changes is 75. If this plan is realized, the above mentioned changes would have an impact on a maximum of 45 positions in Finland.
"These planned measures are regrettable to our personnel, however, necessary due to the weak profitability development during the first half of the year. With these changes, we hope to bring the UPM Paper ENA's profitability on the right track," says Bernd Eikens, EVP, UPM Paper ENA.
The company plans to begin the employee consultation process today, October 3, which will last approximately six weeks. Decisions on organizational changes will be implemented as soon as possible, latest at the end of the consultation process. Decisions on job reductions and support for impacted employees will be made when the consultation process has been completed.
UPM consists of three Business Groups: Energy and Pulp, Paper, and Engineered Materials (until October 31). The Group employs around 22,000 people. UPM's annual sales exceed EUR 10 billion.
Back To Top
|
In a joint effort promoting stewardship, environmental responsibility, and community engagement, Catalyst Paper, Richmond, B.C., Canada, this past week partnered with Halalt First Nation, with support from the Young Professionals of Cowichan, Crofton Fire Hall, and Island Corridor Foundation, to participate in the Great Canadian Shoreline Cleanup, a conservation initiative of the Vancouver Aquarium and World Wildlife Fund of Canada. Catalyst and Halalt First Nation cleaned up an area along the Chemainus River near the intersection of Halalt Road and Westholme Road to conserve as natural habitat for wildlife and recreation area for the community.
In its 20-year history, the Great Canadian Shoreline Cleanup has come to attract more than 50,000 volunteers across Canada annually and has benefitted some 22,000 km of shorelines, making it one of the largest volunteer cleanup efforts in the world. Catalyst Paper and Halalt First Nation extended the invitation to residents of the North Cowichan community.
Halalt First Nation is one of six bands that make up the Hul'qumi'num Treaty Group. It is located 13 km north of Duncan in the district of Westholme and has approximately 200 members. It is well known for shellfish harvesting and Robert James Thomas is the chief.
The Young Professionals of Cowichan (YPC) is a not-for-profit organization that unifies Cowichan's under~45 business professionals and entrepreneurs for the purpose of networking, community involvement, and professional development. The YPC hopes to build partnerships with Cowichan's leading businesses, educational institutions, and community groups to assist its members in developing the skills they will need to become the next generation of leaders in the Cowichan Valley.
Back To Top
|
Changing markets, mill cutbacks and closures, changing rules for employment law, and new health care regulations—this is the stuff of nightmares for today's industry HR managers. To focus on these important topics, the Pulp and Paper Management Association (PPMA) will bring together a host of industry experts at its annual Human Resources conference, October 23-25 in Milwaukee, Wis., USA.
With the theme "212° The Importance of the Extra Degree," the Annual Meeting will provide attendees with "information that can be used to improve business performance, both personally and within their companies," notes PPMA Executive Director Dick Kendall. "In addition, we have a strong speaker line-up featuring a panel discussion about the latest in human resources issues and solutions."
Topping the list of presenters is John D. Williams, president of Domtar, who will provide this year's CEO's perspective on our industry as he focuses his address on Domtar's business approach. Industry experts scheduled to speak include:
- Thomas Evans, Training Logic, Taking Organizational Culture to the Next Degree.
- Guy Morrison, Marsh and McLennon Agency, and Peter Marathas, ERISA Litigation Practice Center, Complying with PPACA and Managing Company Costs
- Dan Murphy and Mark Tilkens, Constangy, Brooks and Smith, Taking Labor's Pulse: What we can learn from Watching the Indicators
- Eric Hobbs, Michael Best & Friedrich Law Firm, An Employment Law Update
- Mark Kinnich, Right Management, Workforce Management in Changing Times
- Ron Bridges, Genesis Performance Partners, Becoming a Person of Influence
- Tom Mackenzie, Linder and Marsack Law Firm, Strategic Positioning approaching negotiations.
A panel discussion will focus on PPACA compliance and what you can do to best position your company. Panelists include:
- Scott Koenigs, VP and chief HR officer, Carustar
- Kerry Arent, Sr. VP of HR, Appvion
- Alexandra Bourke, HR generalist, Gusmer Enterprises
- Guy Morrison, Marsh and McLennon Agency
- Peter Marathas, ERISA Litigation Practice Center.
While at the PPMA conference, attendees will be able to network with top HR professionals from Fortune 500 companies. On Wednesday evening, attendees will have the chance to network and relax with fellow attendees at The Safe House, one of Milwaukee's most unique hot spots.
Registration for the conference is $490 for PPMA members and $590 for nonmembers. For more information, contact Elise Hitchcock ehitchcock@ppmausa.com, 770-209-7214. More information is also available online.
Time is running out and space is filling up, so register online today.
Back To Top
|
Market Roundup
Wood chip and pulp log prices fell in many regions of the world during the 2Q/13, with the biggest declines occurring in Japan, Brazil, and Spain, reports the Wood Resource Quarterly ( WRQ), Seattle, Wash., USA. Lower fiber costs and higher pulp prices have increased profitability for many pulp mills during the first half of 2013.
Lower prices for pulp logs and wood chips in some major markets, and a strengthening U.S. dollar, resulted in lower wood fiber price indices in the 2Q/13, according to the WRQ.
During the past two years, hardwood fiber costs for the pulp industry have declined more than softwood fiber prices. The Hardwood Wood Fiber Price Index (HFPI) has fallen every quarter except one during this period. In the 2Q/13, the HFPI was $100.46, which was 3.1% lower than the previous quarter and 14.8% below the all-time high in the 3Q/11. The biggest price declines since the first quarter of 2013 have occurred in France, Japan, Australia, Russia, and Germany.
Comparing wood fiber costs for the global pulp industry, which typically ranges between 50% and 70% of the production costs, reveals that since 2011, pulp mills in Japan, Brazil, and Spain have seen their fiber costs come down the most of the major hardwood pulp-producing countries in the world.
The Softwood Wood Fiber Price Index (SFPI) was also down in the 2Q/13, but the decline the past two years has been less dramatic than that of HFPI. In the 2Q/13, the SFPI was $97.75, down 2.2% from 1Q/13, with the biggest price reductions seen in Norway, Japan, France, and Australia.
The trend in many regional pulp markets during the second quarter of 2013 was for higher market pulp prices and lower wood fiber costs, indicating improved profitability compared with the previous two quarters since other costs for the manufacturing of wood pulp have not changed substantially the past year. WRQ notes that the wood fiber costs are the highest cost component when manufacturing pulp.
The wood costs as a percentage of market pulp prices fell for the third consecutive quarter for all three major pulp grades in the 2Q/13. The most dramatic decline has been for eucalyptus pulp (EucBK), with the percentage having plunged from 36% in the 4Q/11 to 24.4% in the 2Q/13, according to the WRQ.
The decline in the relative wood fiber cost for northern bleached softwood kraft (NBSK) pulp and southern bleached softwood kraft (SBSK) pulp has been relatively less than that for EucBK the past year.
Back To Top
|
The return of the U.S. housing market is driving up demand for lumber and wood panel products. In response, oriented strand board (OSB) capacity is expected to expand, according to a new study published this week by RISI, Boston, Mass., USA, putting increased pressures on wood fiber pricing in the U.S. South.
Additional capacity will come from idle mills being reopened, expansions at currently operating locations, and potentially from newly opened mills. Some 4.5 billion sq. ft. in increases to OSB capacity have already been announced as coming online through 2014.
"Since the collapse in the U.S. housing market, a significant amount of OSB capacity has been idled. The recent recovery in the U.S. housing market is now driving up demand for OSB both cyclically and seasonally. This increased demand is juxtaposed by a curtailed capacity base. As capacity is added to meet cyclically improving demand, additional wood fiber will be needed. The U.S. pellet export market is developing at the same time that OSB production is ratcheting up and will have implications for wood fiber demand and ultimately prices," said David Fortin, senior economist, Wood Products at RISI.
OSB Capacity Expansion and the Development of US Pellet Exports - Impacts on Woodfiber Supply examines the impact of a sustained housing recovery on the demand for OSB in North America. The study clearly shows how much additional OSB will be needed to meet the expanding demand. It also indicates where this OSB will come from imports, mill restarts, mill enhancements, and potential greenfield mills. The study then looks at whether wood fiber availability will become an issue as mills compete for resources with the developing U.S. pellet market.
Back To Top
|
The global paper and paperboard market had total revenues of $389.9 billion in 2012, representing a compound annual growth rate (CAGR) of 2.3% between 2008 and 2012, according to a new report in Reportlinker's (New York, N.Y., USA) catalogue, titled Paper & Paperboard: Global Industry Guide.
Market consumption volume increased with a CAGR of 1.8% between 2008-2012, to reach a total of 391.7 million units in 2012, the report adds.
Performance of the market is forecast to accelerate, with an anticipated CAGR of 5.2% for the five-year period 2012 - 2017, which is expected to drive the market to a value of $502.2 billion by the end of 2017, the report concludes.
Back To Top
|
Pulp & Paper
The City of Port Alberni, B.C., Canada, completed its purchase of the Catalyst Paper (Richmond, B.C.) wastewater treatment facility and additional lands as scheduled on September 30, in accordance with formal agreements endorsed by both parties. To mark the successful close of the transaction, the presentation of a check representing the initial payment of $5 million was presented by Port Alberni Mayor John Douglas to Catalyst CEO Joe Nemeth at the Catalyst mill site yesterday, October 2 .The remaining $750,000 will be payable on the first anniversary of the closing date.
With the agreements in place, the city will now finalize and be eligible to draw on the $11.2 million grant provided by the federal government in 2012 to integrate Catalyst's lagoon with the city's wastewater treatment infrastructure and improve the city's compliance with the British Columbia Municipal Sewage Regulations and new federal regulations.
As part of the agreement, Catalyst has committed to accept sludge from the lagoon at no additional cost to the city prior to renovations beginning. As well, the city will provide tax certainty to Catalyst at 2012 levels for five years.
Also included with the agreement are land and a road dedication to enable the city to pursue the development of an industrial road along the waterfront. The acquired land runs from the Redford Street entrance to the Catalyst Paper mill to the existing Harbour Road intersection with Argyle Street.
Mayor John Douglas acknowledged the cooperative efforts between the city and Catalyst in reaching this agreement and said "this is a major step forward for the city in reaching key strategic priorities identified by Council. Our wastewater treatment system will receive significant upgrades, increasing capacity and improving water quality in the Alberni Harbour and Somass Estuary." He further added that "a new industrial road has been a priority for the community for many years, and I am excited by the opportunities this brings to increase the livability of our city."
"We are pleased to arrive at the final stages of this jointly beneficial agreement," said Nemeth. "This transaction represents a mutual investment in community prosperity and continued cooperation between community and our industry. It addresses the city's need for infrastructure while enabling Catalyst to focus on core operations."
Catalyst Paper produces specialty mechanical printing papers, newsprint, and pulp. With three mills in British Columbia, Catalyst has a combined annual product capacity of 1.5 million metric tons.
Back To Top
|
Celulosa Argentina, Argentina, has ordered from Voith Paper, Germany, a complete tissue production line. The system, to be supplied as a Process Line Package (PLP), will go on stream in Capitán Bermúdez (about 300 km to the north-west of Buenos Aires) in early 2015.
The new VTM 1 production line, which has a wire width of 2,760 mm and runs at 1,800 m/min, will produce around 30,000 metric tons of 15–21 gsm basis weight toilet tissue and kitchen roll from virgin fiber.
The new production line will enable Celulosa Argentina to break into the production of high-quality tissue papers and continue to pursue its long-term growth strategy. A special feature of this contract is the long-term supplier financing concept configured and arranged by Voith that was a major factor in the realization of the project.
The scope of supply includes a VTM 1 tissue machine consisting of a MasterJet T one-layer headbox, a Voith steel cylinder with high performance hood, the shoe press technology NipcoFlex T, and a MasterReel. Voith's OnQ quality control system equipped with non- radioactive sensors for the measurement of moisture content and fiber weight, the OnC process control system, as well as the entire stock preparation, engineering, and additional services complete the PLP package.
In its three mills in the towns of Capitán Bermúdez (Santa Fe province) and Zárate (Buenos Aires province) in Argentina and in Juan Lacaze in Uruguay, Celulosa Argentina can produce up to 210,000 metric tons of pulp and 194,000 metric tons of paper annually.
Back To Top
|
Fortress Paper Ltd., Vancouver, B.C., Canada, this week announced that its Fortress Specialty Cellulose (FSC) Mill successfully installed a new high pressure water pump for its cogeneration facility and synchronized the cogeneration facility with the Hydro Québec grid without issue. Since the successful installation of the new high pressure water pump, the cogeneration facility has generated 4,617 MW hours in cumulative power and averaged daily electrical output of 20.25 MW per hour. In addition, the boiler, turbine, and generator components of the cogeneration facility operated more than 96% of the time during this period.
The company is required to complete a continuous 100 hr. grid test before the cogeneration facility can deliver power to the Hydro Québec grid at the contracted rate. Since the installation of the high pressure water pump, the cogeneration facility has operated continuously on two occasions for 71 and 94 hr., respectively, but has yet to complete the continuous 100 hr. grid test due to minor technical issues that were not directly related to the cogeneration facility and which will be resolved imminently. The company anticipates completing the 100 hr. grid test in the near future.
Fortress says that it continues to respond to inquiries from China's Ministry of Commerce (MOFCOM) relating its investigation into dissolving pulp imports into China, but no date for MOFCOM's final determination on the matter has been set. To mitigate any adverse impacts resulting from the threatened imposition of a dumping tariff by MOFCOM on the import of dissolving pulp into China, and challenges in the dissolving pulp market generally, the company has begun conducting a strategic assessment of alternatives for the FSC Mill.
During the third quarter, the company implemented a plan to reduce logistics, transportation, and distribution costs at the FSC Mill. As a result, there will be an increase in the finished goods inventory levels, due to the company retaining ownership of such inventory for a longer period in the sales cycle. Going forward, the company expects these savings to increase the net realized revenue. Inventories at the FSC Mill may also increase as a result of the uncertainty caused by MOFCOM's investigation resulting in Chinese buyers suspending purchase orders for dissolving pulp.
Fortress Paper operates internationally in two distinct business segments: dissolving pulp and security paper products. The company operates its dissolving pulp business at the FSC Mill in Canada, which is also in the process of expanding into the renewable energy generation sector with the construction of a cogeneration facility. The company also is seeking to expand its dissolving pulp capacity with the recent acquisition of Fortress Global Cellulose Mill at Lebel-sur-Quévillon, Québec, which the company is evaluating to convert into a dissolving pulp mill and re-start the cogeneration facility. The company operates its security paper products business at the Landqart Mill in Switzerland, where it produces banknote, passport, visa, and other brand protection and security papers, and at its high security production and research facility in Canada, where it manufactures optically variable thin film material.
Back To Top
|
In line with the theme of this year's 52nd Man-made Fiber Congress meeting September 11 -13 in Dornbirn, Vorarlberg, Austria, Kelheim Fibres, Bavaria, Germany, reported on several "new challenges and new solutions" for its specialty fiber products and markets. The company noted that the spread of product or trademark piracy is one of these challenges "as it inflicts an enormous loss on our global economy every year and is becoming increasingly explosive. Almost 70% of all businesses are affected," Kelheim Fibres said.
Bernd Probst, a member of Kelheim's R&D team, presented a range of specialty fibers that protect products from illegal counterfeits with a visible or invisible fingerprint.
Another hot topic is the mega-trend "Ageing Society" and the increasing demand for convenient, discrete, and safe incontinence products, the company reported. Kelheim's Dr. Ingo Bernt presented viscose specialty fibers from Kelheim that enable "perfect liquid and moisture management." Their absorption levels, he noted, range from "extra absorbent" to "hydrophobic," hence they allow the production of incontinence solutions that consist completely of renewable materials and at the same time are washable and re-usable.
Dr. Philipp Wimmer gave a lecture on the opportunities that Kelheim's viscose specialties offer in the filtration industry, "a market that is growing in importance in our increasingly ecologically aware and health-conscious society." In contrast with other cellulosic fibers such as cotton, he continued, "viscose fibers stand out not only as a result of their definable and reproducible geometry, which enables a perfect match to be made to the specific processing route or end application. The porosity or surface of a filter, for instance, can be precisely controlled by adding the appropriate viscose fibers with different cross sections. Further, the incorporation of functional additives allows the manufacturing of tailor-made fibers according to the end product's exact demands," Dr. Wimmer pointed out.
Dr. Roland Scholz and Dr. Nina Köhne presented a series of interesting analyses regarding ionically activated viscose fibers and their applications. According to Dr Scholz and Dr. Köhne, by using different technologies, Kelheim's R&D can deliver fibers with cationic or anionic functional groups and thus control the fiber properties. Particularly when it comes to ion exchanging properties, fibers offer a distinct benefit. In comparison with common ion exchange resins, the diameter of the ionically functionalized fibers is considerably smaller and the active surface is significantly larger. Hence they operate up to 10 times faster.
Kelheim Fibres is a global producer of viscose specialty fibers, including viscose fibers for the tampon industry. Approximately 90,000 metric tons of viscose fibers are produced and tested every year at Kelheim's facilities in South Germany. These are used in diverse applications, from fashion, hygiene, and medical products to nonwovens and specialty papers.
Back To Top
|
Kawanoe Zoki, Japan, and Metso, Finland, have extended their cooperation in tissue making technology to include the marketing and supply of Advantage DCT 40 and 60 technologies to the Chinese market. Under the new license agreement, Kawanoe Zoki will market, manufacture, and install Advantage™ DCT® 40 and 60 machines that will be produced at the company's workshop in Zhejiang, China. Metso will supply key components including OptiFlo II TIS headboxes, Metso yankee cylinders, and suction pressure rolls, to form part of Kawanoe Zoki's deliveries.
The first joint delivery to China will be four Advantage DCT 60 tissue machines to Shandong Dongshun Group Co..
Metso and Kawanoe Zoki have a long history of cooperation in supplying tissue machines based on Metso Advantage DCT technology for the Japanese market.
Ever since 1996, several tissue machines based on Metso technology have been successfully installed in Japan. The deliveries include key components from Metso as well as equipment manufactured by Kawanoe Zoki under a technology license from Metso.
"Some 20 years of partnership with successful projects in Japan have nurtured our current deep cooperative relationship with Metso. By combining Metso's world-class technology and our strong sales and after-sales service network in China, this new license agreement should bring success to our business in China," says Takahiro Shinohara, Kawanoe Zoki.
"Kawanoe Zoki has numerous excellent references in China for smaller size tissue machines, and combining this with Metso's unique technology and resources will provide a basis for an attractive offering to the Chinese tissue making industry," says Ingmar Andersson, Metso Tissue Mills business unit.
The first tissue producer to benefit from Metso's Advantage DCT 60 technology and Kawanoe Zoki's vast experience is Shandong Dongshun Group Co., which placed an order for four Advantage DCT 60 tissue machines in July of this year. Two of the machines will be installed at the Dongping mill in Taian City, Shandong Province, in the second half of 2014 and the other two at the same mill in the first half of 2015.
"We have a long-standing relationship with Kawanoe Zoki. Since the first BestFormer Yankee paper machine was contracted in 2005, we have ordered 20 units of Kawanoe tissue machines, which demonstrate our trust and satisfaction with Kawanoe Zoki's high technological skills and committed customer services. Now their cooperation with Metso will help us to become more competitive with higher production and quality products in the Chinese market, thanks to the world-leading Advantage DCT technology," says Chen Shu Ming, chairman of the board, Shandong Dongshun.
Shandong Dongshun Group is the largest tissue paper manufacturer in northern China and one of the leading tissue makers in China in terms of both production amount and business scale. Shandong Dongshun has recently expanded its product range to baby diapers and sanitary napkins in addition to toilet and tissue paper.
Back To Top
|
Mercer International Inc., New York, N.Y., USA, this week announced that its Stendal facility in Germany has successfully amended its senior project finance credit facility (approximately EUR 413 million outstanding) and its EUR 17.0 million amortizing term facility in respect of Project Blue Mill (approximately EUR 15 million outstanding). The amendment agreement modifies the Stendal facilities to provide the Stendal mill greater financial flexibility by, among other things:
- Waiving compliance with the annual debt service cover ratio and the senior debt to EBITDA cover ratio under the Stendal Facilities until and including Dec. 31, 2013
- Amending the same so that the financial covenants now deduct from senior debt cash in the debt service reserve account and cash above a stipulated threshold to include certain cash reserves in the calculation of senior debt
- Providing that a failure to satisfy the covenant to maintain an annual debt service cover ratio under the Stendal Facilities would only be an event of default when amounts in the debt service reserve account plus certain cash reserves are below a specified threshold
- Revising the calculation of amounts required to cure financial covenant defaults under the Stendal Facilities.
In connection with the amendment agreement, the company made a capital investment of $20.0 million in Stendal.
"We are pleased to have successfully amended and improved the covenants in our Stendal mill credit facilities, which will provide our Stendal mill with greater flexibility," said Jimmy Lee, president and chairman. "We are pleased with the continued support of our lenders."
The Stendal mill is a single-line NBSK (northern bleached softwood kraft) pulp mill situated near the town of Stendal, Germany, with an annual pulp production capacity of approximately 650,000 air dried metric tpy.
Back To Top
|
Metsä Tissue, Finland, part of Metsä Group, will invest in a tissue machine upgrade at its Raubach mill in Germany. In addition to higher product quality and increased capacity, the upgrade will improve the energy efficiency of tissue production at the mill.
The investment is part of Metsä Tissue's energy efficiency improvement program. "Between 2007 and 2012, we have reduced our energy use company-wide by 20%. By 2020, our aim is to improve our energy efficiency by a further 10%," said Christoph Zeiler, SVP, Tissue, Western Europe.
Toscotec has been chosen as the main supplier of the paper machine upgrade at Raubach mill. The project will be handled on a turnkey basis, including engineering, full installation, startup, and training. It is due to be completed by the end of this year.
Back To Top
|
AstenJohnson, Charleston, S.C., USA, reports that its new AccuFlow™ II press fabric is getting an outstanding reception from printing and writing paper producers. To date, it says, 95% of the trials have resulted in new orders for the fabric. And, it adds, 65% of these orders have been received while the trial fabric is still on the machine.
Daniel Hédou, AstenJohnson's global innovation leader for press fabrics, points out that "this is virtually unheard of. Usually, papermakers will not reorder a product until the trial fabric has come off of the machine and has been fully evaluated."
AccuFlow II is the newest addition to AstenJohnson's press fabric portfolio. It shares some of the unique features of the original AccuFlow (like a patent-pending base design that gives it superior water handling abilities) and has the added ability to resist wear from abrasive fillers.
"Of all of the seamed structure fabrics in the marketplace, we are the only ones laminating a two-layer with another two-layer product," Hédou explains. "The fabric stays open on the machine, giving it exceptional water handling capacity."
According to Hédou, mills running the AccuFlow II fabric have documented savings of more than $13 millon combined due to longer run times, reduced sheet breaks, and greater dewatering with less vacuum, which saves energy. To date, the fabric has been run on 17 different paper machine positions.
The base for AccuFlow II, which is primarily designed for high-speed printing and writing machines, is manufactured using single monofilament and cabled monofilament yarns. This provides resistance to compaction, low flow resistance, high water handling capacity, and increased resistance to wear.
More information on AccuFlow II fabrics for printing/writing grades is available online.
Back To Top
|
Tembec, Montreal, Que., Canada, this week announced that it will sell approximately 1,875 hectares of land within the Regional District of East Kootenay, B.C., to Jemi Holdings Ltd. for $4.2 million. Closing of the transaction is expected to occur on or about November 1.
Tembec owns approximately 64,500 hectares of land in the East Kootenay region. It is currently pursuing the sale of several parcels of land and has set an objective of realizing up to $75 million in land sales, including the previously noted transaction, by December 2014. The company will provide regular updates on the B.C. Land Sale Initiative as it progresses. There can be no assurance, Tembec notes, that it will attain the stated objective or that it will do so within the specified time period.
Tembec is a producer of pulp, paper, and specialty cellulose, as well as forest products (lumber). Its principal operations are in Canada and France. The company has some 3,400 employees and annual sales of approximately $1.6 billion.
Back To Top
|
Containerboard/Packaging
Folding carton producer Mod-Pac Corp., Buffalo, N.Y., USA, reports that its shareholders approved, at a special shareholder meeting this past week, the going-private merger agreement under which Kevin T. Keane, chairman, and Daniel G. Keane, president and CEO, and their associates and affiliates will acquire approximately 81.3% of the company's outstanding capital stock that they do not already own for $9.25 per share in cash. The merger was approved by more than 66 2/3% of the company's shareholders voting as a single class and by a majority of the issued and outstanding shares of the company's stock, when excluding the shares beneficially owned by the Keanes and any other related shares. The total transaction is valued at some $24.6 million.
Daniel Keane said that "the transition to a private company will be seamless for our customers and employees. We will continue to deliver high quality product on time, on demand." The company's operations and headquarters will remain in Buffalo.
Mod-Pac provides custom folding cartons for branded and private label consumer products in the food and food service, healthcare, medical, and automotive industries. The company also offers a line of stock packaging primarily to the retail confectionary industry. The company also has a personalized print product line.
Back To Top
|
Rengo Co., Kita-ku, Osaka, Japan, has announced that Thai Containers Group Co. (TCG), Thailand, a joint venture between Rengo and SCG Paper Public Co., a subsidiary of The Siam Cement Public Co., has completed the acquisition of a 90% stake in PT Primacorr Mandiri, which operates a plant in the suburbs of Jakarta, Indonesia. Combining the four existing plants operated by PT Surya Rengo Containers (SRC), a joint venture between PT Indofood CBP Sukses Makmur and Rengo, the annual production capacity in Indonesia will increase to 228,000 metric tons, enabling TCG and SRC to capture the ever-growing demands in Indonesia, the company noted.
Further growth of corrugated demand in Indonesia can be expected, Rengo points out, as many Japanese companies choose the country as their manufacturing base in the ASEAN region, and as national income increases. Corrugated packaging in Southeast Asia is an important strategic focus for the overseas business of the Rengo Group—which aims to be a "General Packaging Industry"—and Rengo says it will work to further enhance its corrugated packaging supply system within the region.
Back To Top
|
New Products
Archroma, Reinach, Switzerland, this week announced its official launch as a newly formed global color and specialty chemicals company that comprises the former Paper Solutions, Textile Specialties, and Emulsion Products businesses of Clariant. Archroma, owned by SK Capital Partners, a U.S. based private investment firm, is combining the three businesses into a single entity.
To be led by CEO Alexander Wessels, the newly recruited senior leadership team will seek to generate a renewed sense of purpose and vision, and will work closely with the current heads of the three businesses acquired from Clariant, whose "unique understanding" of their markets and customers has advanced the strategic positioning of Archroma.
"We're open for business with a new name and a financially strong and knowledgeable parent who believes in our technology, brand, and leading market positions," says Wessels. "I'm proud to join a company with a 120-year long history of providing a portfolio of world-class products and driven by a team of highly talented people who bring fresh thinking and ideas to an industry hungry for innovation. The transaction closing comes after a thorough preparation to ensure a seamless transition of the businesses from Clariant to new ownership. In addition, we believe that realigning the three businesses into a single integrated, market-focused, and dynamic company will benefit both our employees and our customers."
Wessels added that "with SK Capital, we strengthen our business and further improve our offering to our customers. We have all the right cards in our hand. We know who we are and what we offer to our customers – innovation, performance, technical expertise, quality, reliability, a global footprint, and a commitment to sustainability."
Archroma will be headquartered in Switzerland along with the management team of Archroma's Paper Solutions Business. The Textile Specialties Business will be managed from Singapore and the Emulsion Products Business from Brazil.
Back To Top
|
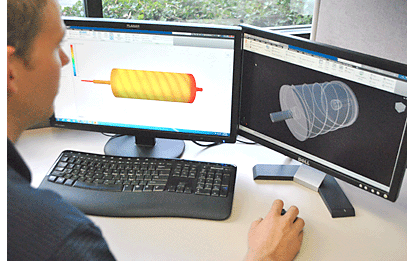 Menges Roller Co, Wauconda, Ill., USA, a designer and manufacturing of precision rollers for the paper converting industries, has announced the enhancement of its engineering department capabilities. Heat transfer rollers are a flagship product at Menges, and these engineering enhancements are primarily aimed at the heat transfer roll marketplace. Using advanced technology, Menges says that it engineers can now see and predict the exact temperature a roller will achieve and how that temperature will affect the web – all before the roller is built. These advancements help Menges Roller design rollers that perform specific tasks at very specific temperatures.
Using the latest computational fluid dynamics (CFD) technology, Menges Engineers compute all of the relevant factors—substrate types and dimensions, line speeds, thermal transfer fluid data, roller dimensions, flow rates, etc.—to see the temperature and thermal profile of a roller before it is built, the company emphasizes.
Matt Menges, president of Menges Roller, explained that "with modern converting applications, heat transfer rolls must perform at a very high level...and we take pride in building some of the best heat transfer rolls on the market. With these engineering enhancements, we're simply continuing on that path. Now, instead of just seeing static roller dimensions, we can demonstrate how changes to those dimensions affect the flowrate, the roller's temperature, the web's temperature, and the entire converting process. It's all about designing custom rollers that perform flawlessly in their application."
As part of these engineering department enhancements, Menges says that it also has invested in technology that allows engineers to model weight and load-bearing characteristics. This allows engineers to compare the strength and stress capacities of various steels in relation to roller design and component dimensions.
Menges Roller Co. serves the, paper, plastics, non-wovens, and steel markets with heat transfer and chill rolls, large process rolls, as well as web spreaders and other rubber-covered rollers. It also provides a full range of maintenance and repair services, from comprehensive roll refurbishing, to journal and core replacement, dynamic balancing, parabolic crowning, chrome finishing, and rubber covering options.
More information is available online.
Back To Top
|
Metso has launched polyurethane roll covers for tissue machine press and suction press rolls. The new PressHusky and VacuHusky roll covers are designed especially for yankee press applications widely used in dry crepe tissue production. As an option, a Metso iRoll online nip profile measuring system can be applied with these new roll covers.
Some tissue grades are sensitive when it comes to bulkiness and thickness, so lower nip pressures are preferred in pressing. Traditionally, this has been a limitation in the use of polyurethane roll covers in yankee press applications, according to Metso. However, the new polyurethane material of PressHusky and VacuHusky covers offers several hardness alternatives and more options for cover topography, which results in maximized dewatering and the desired tissue quality with high bulkiness and thickness.
PressHusky and VacuHusky covers also provide lowered operating costs due to the reduced need for regrinding, the company notes, adding that their low rolling resistance creates energy savings thanks to reduced roll drive power. In addition, solid press rolls with a PressHusky cover can be operated cost-efficiently without internal water cooling.
Nip profile monitoring and control has been quite a challenge in a nip formed between a roll and a yankee dryer, Metso continues. Reliable information on nip profile errors or skewness problems can only be gained when measurements are taken at operating speed with the desired steam pressure inside the yankee dryer. Metso's iRoll measurement technology can be utilized with these new polyurethane roll covers, providing accurate nip pressure profile data for efficient nip control.
Back To Top
|
UPM Raflatac, has introduced a range of next-generation labelstock products that offer fit-for-purpose performance for the main end-use segments. The Fit range combines increased production efficiency and sustainability credentials with no compromises on printing and dispensing performance.
Raflacoat Fit PEFC provides efficiency to high-volume food applications. The new PEFC-certified mid-gloss label face is sustainably sourced, and the thinner 63 µm in caliper yields up to 30% longer rolls, substantially reducing downtime during roll changes, the company notes. The labelstocks are equipped with adhesives for all food labeling temperatures, including the EU 10/2011 compliant next generation hotmelt RH 6 optimized for chilled conditions but equally capable in room temperatures. Raflacoat Fit PEFC is available with three liner options. The HG65 and HG45 glassine liners are PEFC-certified like the label face. The ProLiner PP30 option maximally reduces the labelstock thickness to increase productivity and to provide better performance in high-speed applications and humid conditions.
Retail Eco Fit PEFC provides optimal performance in weigh-price and backroom applications and assures a crisp image for scanning at the cash register. Thermal Eco Fit PEFC is a fit-for-purpose solution for packaging films and most common cardboards in short-life labeling. Laminate structure in these two products is 17% thinner, meaning more labels per roll, 17% fewer roll changes, and possibility to move to longer reel lengths both in printing and in labeling. The HG45 liner is lighter than HG65, which results in 20% less liner waste and a comparable reduction in landfill costs, the company says.
The label faces and glassine liners are PEFC-certified. The liner waste is 100% recyclable through UPM Raflatac's waste management concept RafCycle, leading to reductions in carbon footprint, liner waste, and landfill costs.
UPM Raflatac explained that the environmental impact of the Fit products is based on comprehensive lifecycle assessments (LCA). The LCAs carried out at UPM Raflatac are performed in accordance with ISO 14014/44 and are consistent with the methodology used by many large brand owners to evaluate their own environmental impacts.
Back To Top
|
Published Pricing
Metsä Fibre, Finland, has increased the price of its Botnia Nordic Pine NBSK (northern bleached softwood kraft) pulp in Europe, effective October 1. The new price is $900 per metric ton, CIF Metsä Fibre's frequently used European ports of destination. All other terms and conditions remain unchanged.
Back To Top
|
Södra, Sweden, this past week also raised the price of its NBSK (northern bleached softwood) pulp to $900 per metric ton, effective October 1. The company attributes the increase to improved market fundaments.
Back To Top
|
People
Motion Industries, Birmingham, Ala., USA, a distributor of industrial maintenance, repair, and operation (MRO) replacement parts, is pleased to announce that Tim Breen has been named president and COO. Most recently, Breen has served as EVP and COO of the company's U.S. operations since 2011. In his new role, he will continue to lead the company in the areas of bearings/power transmission/fluid power/hose and corporate accounts, with the addition of purchasing/distribution, inventory management, and sales.
Breen began his career with Berry Bearing Co. in 1982 and has held significant key positions since Berry Bearing was acquired by Motion Industries in 1993. Prior to becoming EVP in 2011, he led Motion Industries as a SVP for the Central U.S.
"This move will help better position Motion Industries for growth in the future," said Bill Stevens, Motion Industries' chairman and CEO. "Tim's leadership in these areas of our business will keep us on track to accomplish our goals in the coming years."
With annual sales of $4.5 billion, Motion Industries is a leading industrial parts distributor of bearings, mechanical power transmission, electrical and industrial automation, hydraulic and industrial hose, hydraulic and pneumatic components, industrial products, safety products, and material handling. The company has more than 550 operations including 14 distribution centers throughout North America and serves more than 150,000 customers from the food and beverage, pulp and paper, iron and steel, chemical, mining and aggregate, petrochemical, automotive, wood and lumber, and pharmaceutical industries.
Back To Top
|
Mikko Forsell, M. Sc. (Econ.), M. Sc. (Tech.), has been appointed Metsä Tissue's CFO and a member of Metsä Tissue's management team, effective Jan. 1, 2014. He will report to Mika Joukio, CEO, and will be located in Espoo, Finland.
Mikko joined Metsä Tissue in 2005 and has since held various positions with the company in finance. He is currently working as VP of Purchasing. Mikko replaces Markus Holm, who has been appointed CFO for Metsä Board Corp. as of Jan. 1, 2014.
Back To Top
|
Motion Industries, Birmingham, Ala., USA, a distributor of industrial maintenance, repair, and operation (MRO) replacement parts, has named Joe Limbaugh VP-Operations. This new position at the company will focus on company-performance improvement and corporate projects.
Most recently, Limbaugh served as VP and GM for Motion Industries' Chicago Division in the Central Group. His career began in 1983 with Berry Bearing Co., and since then he has served in leadership positions at the branch and division levels in both the Central Group and the Southeast Group. With this promotion, Limbaugh will be relocating to the corporate office in Birmingham.
"We congratulate Joe on his new position and thank him for his many contributions to our company," said Tim Breen, Motion Industries' president and COO. "We look forward to Joe's leadership in these key areas that will help us continue to focus on operational improvement throughout the company."
Motion Industries is a wholly owned subsidiary of Genuine Parts Co.
Back To Top
|
TAPPI News
For TAPPI member Margaret Joyce, Ph.D., constantly being on the go is just one satisfying part of a dream career she has been passionate about since her first day of classes at North Carolina State University (NCSU).
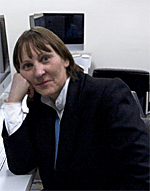
And passionate she is... In addition to her regular teaching schedule at Western Michigan University (WMU) where she serves as a full professor in the Department of Chemical and Paper Engineering, she also teaches continuing education offerings in the summer and is faculty adviser for WMU's Society of Women Engineers student chapter. A member since 1992, she serves on a number of TAPPI committees and divisions, as well as a TAPPI Journal reviewer and short course instructor. Recognized over the years with multiple awards for her contributions to the field, she exudes enthusiasm for the industry, which she describes as one "that produces products from a renewable resource, is diverse in its use, and of great importance to the U.S. economy."
Find out more by reading this month's Member Spotlight. Spotlight participants are recommended by fellow members and staff. If you would like to nominate one or more members, just send their name (or names) to MemberSpotlight@tappi.org. We will forward a Spotlight Questionnaire to fill out and return.
We look forward to seeing you in the Spotlight!
Back To Top
|
We have been working to create a powerful new tool for TAPPI members to learn about industry vendors, but we need your initial input to make this a success. Please take a moment to write a review of a company you've worked with. Search for your favorite company to get started.
Users of the TAPPI Buyers Guide have the ability to avoid the clutter of a general search engine and only search within pulp, paper, packaging, and converting industries, utilizing a basic keyword search or digging deeper with a more specific, advanced search.
Thank you for your time and input, we look forward to hearing from you!
Back To Top
|
There is still time to register for TAPPI 2013 CorrExpo, October 7-9, at the JW Marriott in Indianapolis, Ind., USA .
Looking for the latest and greatest the industry has to offer? CorrExpo will include two What's New Sessions revealing 16 new developments to the corrugated industry since 2011. You'll also want to take a lap on the sold out exhibit floor.
The conference features two Keynote presentations. Alexander Toeldte, president and CEO- Boise Inc., will kick off the conference on Tuesday and on Wednesday you can learn about "Truly Human Leadership" from Bob Chapman, CEO andcChairman of Barry-Wehmiller. Come one hour early on both days and take in the technical expertise offered at the Eye Opener Sessions. Want to attend more than one? Set your alarm for both mornings; the sessions will be repeated on Wednesday.
The three concurrent Wednesday workshops will be like a performance-boosting pit stop created to give packaging pros that race-winning edge. The workshops are open to conference registrants, exhibitors, and those registered to visit the exhibit.
These are just a few of the highlights of the jam-packed program. Learn more at the conference website.
Back To Top
|
TAPPI's Papermaking and Water Removal Committees present an exciting two part webinar on October 7 at 2:00 p.m. EST. Doug Sweet, of Doug Sweet and Associates, will present "Paper Machine Vacuum Systems 101." This free webinar will review some of the typical issues with the vacuum system including instrumentation and vacuum control, seal water systems, and cooling towers, flatboxes and uhle boxes, separators, and extraction pump and vacuum pump reliability. Doug is an engineer with more than 35 years of experience, and his presentations have been one of the highlights of past TAPPI papermaking conferences.
Additional information about the webinar and instructor is available at the course website.
Following Doug's presentation, a round table discussion with leading papermaking experts will be held. The distinguished panel includes: Gary Nyman, International Paper; John Neun, Albany International; and Dave Burton, Asten Johnson, all with more than 30 years of experience in the papermaking industry. This roundtable will be an open forum for any questions you have on papermaking topics. These experts can offer you sound solutions to any challenges you may be facing. You may register and submit a question for the panel by visiting the Papermakers Roundtable website.
The Papermakers and Water Removal committees are very active in planning program content for TAPPI's PaperCon conference being held next year in Nashville Tenn., USA, April 27-30. For more information visit www.papercon.org.
Back To Top
|
TAPPI's problem-solving course designed for those working in industrial settings returns this fall.
Root Cause Problem Elimination Training
October 8-10 in Raleigh, N.C., USA.
This maintenance course is designed to show you how to cut to the core of problems - and eliminate them - by tying cause and effect together with logical thought processes and easy-to-grasp diagrams. You'll learn from case studies and predictive maintenance tools to better analyze root cause and repeat failures.
Back To Top
|
Critical Thinking in Converting
Written by: David R. Roisum, Ph.D.
Critical Thinking in Converting illustrates many different problem-solving techniques by example. The plant-proven tools introduced in this unique book will help you quickly find solutions to your toughest problems. The tools can be adapted to uncover the inner workings of almost any specific problem. Once the problem is truly understood, solution options follow easily. While this is a technical book, no special background is required. The reader only needs a working knowledge of terminology and concepts that are common in web manufacturing and converting.
View the Table of Contents.
Product code: 0101R302
Member Price: $ 81.00
Non-Member Price: $121.00
Back To Top
|
The TAPPI Microbiology and Microbial Technology committee has announced the next webinar in its series on Microbes in Papermaking. "Microbial Control: Protecting Mineral Slurries and Papermaking Additives from Spoilage" will be held on October 16 at 12:00 p.m. EST. The webinar will be hosted by Sherrill Gammon, Sr. Research Scientist in the Microbiology Group of Kemira Chemicals, and will focus on the challenges presented when protecting additives in storage against the growth of ever changing microorganisms.
The preservation of mineral slurries and other additives for pulp and paper processes can be a challenge given the dynamic nature of the microorganisms, characteristics of individual biocides, and the chemistry of the products to be preserved. A review of microbial control in the world of white pigments and additives combining the tools of biocides, microbiology, monitoring, and housekeeping will be discussed to make the job of protecting these additives a little easier.
This webinar is offered at no charge. Additional details are available on the course website.
The Microbiology and Microbial Technology committee is an active committee and has produced a successful webinar series on this and other important topics. It also conducts presentations at TAPPI's PaperCon Conference being held next year in Nashville, Tenn., USA. April 27-30. For more information visit www.papercon.org.
Back To Top
|
Piping System Training is a course anyone in the piping system industry can use. This course provides real-world practical knowledge for junior engineers, is a good refresher course for senior engineers, and helps operations and maintenance supervisors, design and process engineers, and operators and maintenance personnel better understand how piping systems operate.
Attend Piping System Training courses planned for two locations coming this fall:
- October 2-3 in Chicago, IL
- October 23-24 in Houston, TX
This course provides the foundation of piping terminology, mathematics, and the underlying concepts and principles that determine the performance of individual piping system elements and the system as a whole. Piping System Training places an emphasis on understanding the relationship between components that make up the piping system.
Visit the course website to find more information and register.
Earn 1.6 CEUs and carry back with you two indispensable manuals as well as greater confidence in your work.
Back To Top
|
The Northeast Division of PIMA/TAPPI invite you to attend its annual fall meeting and conference to be held at Wells Commons at the University of Maine, Orono, Maine, on November 6.
The annual meeting will feature an informative one-day conference titled "Safety: Best Practices," with speakers presenting various safety topics that could impact our work and personal lives.
Online Registration is now available. More information as well as the mail-in registration form can be found here.
Back To Top
|
Lake States TAPPI/North Central PIMA hosts its annual Energy Technical Program, "Case Studies in Energy Optimization" on November 6 at Miron Corporate Office in Neenah, Wis., USA.
Online Registration is now available. More information and the mail-in registration form can be found here. The Draft Agenda is also available online.
Back To Top
|
TAPPI's 2013 Nominating Committee presents a slate of candidates for three director positions on the TAPPI Board. The candidates are: Peter R. Augustine, president, Fabio Perini North America; Paul R. Durocher, director Coated Paper Development, Sappi Fine Paper North America; and Christopher A. Krumm, VP of Operations, CorrChoice, a Division of Greif.
Per the TAPPI Bylaws, members of the organization have until November 1, 2013, to review the slate.
Learn more about the slate and election process.
Back To Top
|
The 2014 conference co-chairs invite you to submit an abstract for a presentation at the 2014 TAPPI International Conference on Nanotechnology for Renewable Materials, June 23-26, 2014, at the Fairmont Hotel Vancouver in Vancouver, B.C., Canada.
Abstracts addressing the latest advances in characterization, functionalization, modeling, new products, applications, and health and safety issues of renewable and sustainable nanomaterials are sought. For the 2014 conference, abstracts focused on additive manufacturing, 3D printing, and other industrial manufacturing applications are preferred.
Abstracts are due November 5, 2013.
This year's conference features several opportunities for students to achieve recognition for their work.
View the Call for Abstracts to learn more.
Back To Top
|
Calls for Papers have been issued for PaperCon 2014.
After a record attendance in 2013, PaperCon will again bring together CEOs, mill managers, superintendents, scientists, process engineers, and suppliers for the largest pulp and paper technical program in the world. The event will take place April 27-30, 2014, in Nashville, Tenn., USA. Learn more about PaperCon 2014.
For 2014, PaperCon is once again co-located with the Tissue360° Forum, NETInc (Innovative Nonwovens Conference), RPTA (Recycled Paperboard Technical Association) P-T Seminar, and the OpEx Reliability Workshop. Each of these events is open to full PaperCon registrants and papers in these areas are welcome.
Calls for Papers and Posters have been issued. The conference theme is In Tune for Stability, Agility, and Profitability, and authors are encouraged to include this within their papers.
Papermakers Program:
The Papermakers Program encourages topics on paper machine upgrades, product development, stability, agility, and fluid fundamentals, and recycled paperboard. The deadline for submission of abstracts is Nov. 10, 2013. Abstracts for panel discussions and roundtables are welcome. See Papermakers Program Call for Papers.
Coating and Graphic Arts Program:
The Coating and Graphic Arts Program will focus on The Future of Print and its Demands on Paper and Coatings. The deadline for extended abstracts for this program is October 16, 2013. See the Coating and Graphic Arts Program Call for Papers.
All abstracts must be submitted using TAPPI's Speaker Management System for consideration by the TAPPI and RPTA program committees.
Back To Top
|
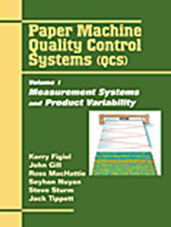 Paper Machine Quality Control Systems - Volume 1: Measurement Systems and Product Variability
By: The Quality Control Systems Education Common Interest Group of the Process Control Division of TAPPI.
Paper Machine Quality Control Systems - Volume 1: Measurement Systems and Product Variability describes in detail the measurement technology used in Quality Controls Systems (QCS). Individual chapters are devoted to the five most prevalent QCS measurements (basis weight, moisture, caliper, ash, and color) in the paper industry. Each of these chapters covers the physical principles involved in each measurement, sensor designs, various methods of implementation and influence factors.
A somewhat lighter coverage is given to10 other QCS measurements that do not have such a abroad installation base. Common issues that impact all sensors are explained, including how sensor performance is measured and reported, the impact of scanning process, filtering, scanner designs and construction, and sensor calibration and correlation. Statistical methods are covered in depth from discrete, one-dimensional variability to multi-dimensional variability. Guidance is provided for using these statistical methods to locate the sources of variability in the paper process.
This book was written by the Quality Control Systems Education Common Interest Group of the Process Control Division.
View the Table of Contents.
Also soon to be available in e-book format.
Product code: 0101R328
Member Price: $135.00
Non-Member Price: $205.00
(A percentage of the proceeds for the sale of this book go to the TAPPI Foundation.)
Back To Top
|
The Foundations of Leadership Excellence Course is the only leadership course specifically focused on the paper and packaging industry.
Foundations of Leadership Excellence explains the fundamentals of leadership and management skills for emerging leaders, high-potentials, area operating managers, and other technical professionals. This three-day session takes place Oct. 22 - 24, 2013, at the TAPPI Training Facility in Metro Atlanta, Ga., USA.
This course will sell out at 25 participants.
The instructors for this course have approximately 100 years of combined experience in leadership, management, and human resource roles within the pulp and paper industry.
Course curriculum covers industry specific, real-world scenarios. Participants will develop personal leadership skills through the use of influence. They will learn to impact organizations from a 360 degree perspective and how to address the challenges of team building, accountability, performance management, and other critical factors of organizational success.
Back To Top
|
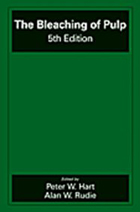 The Bleaching of Pulp
By: Peter W. Hart and Alan W. Rudie
Previous editions of The Bleaching of Pulp have provided comprehensive information on the technology used to bleach wood pulps. The 5th edition will continue this tradition as the premiere industry text on bleaching technologies but will be more focused on the modern industrial processes with less emphasis on fundamental science. New or more comprehensive sections are included on elemental chlorine free bleaching, enzymes, acid treatments for hexeneuronic acids, control of mineral scale, and multi-stage modeling as used to optimize bleaching among multiple stages.
Preview table of contents and sample pages.
Product code: 0101R331
Member Price: $155.00
Non-Member Price: $232.00
Back To Top
|
As TAPPI is getting ready to celebrate its 100th Year Anniversary in 2015, we were wondering how much industry expertise we have in this great group of professionals.
So, we decided to post a discussion question on our TAPPI Social Media outlets. We asked, "How many years of paper and/or packaging experience do you have?"
Who knew such a simple question would have such an impressive response.
With more than 7,000 TAPPI members, all over the world, we have counted 650-plus years of industry experience! And that's just counting the first 30 people who have responded. Now you probably can't find that anywhere else . So why don't you join us?
From those "born" into the industry to third generation professionals. From paper to packaging, to sustainability, environment, tissue, converters, and consulting. This TAPPI network has something for everyone.
Become a part of this unique community of paper and packaging professionals, and add your expertise to our group, and network with others to learn something new.
Visit our website to learn more today!
Back To Top
|
The TAPPI Centennial Celebration will be a multi-year long series of outreach events and educational offerings showcasing the proud history and promising future of the global pulp, paper, packaging, and related industries. This once-in-a-lifetime event will expand public awareness, foster further connection, and provide outstanding opportunities for collaboration, growth, and investment in our future for all of those involved. Goals for the TAPPI Centennial Celebration are:
- To honor TAPPI's 100 years of connection, education, and advancement as a foundation for the sustainable success of our members, our industries, and the world we share
- To recognize the achievements of those who built our industry and to inspire those who seek to build its future
- To celebrate the contributions and innovations of the global pulp, paper, and packaging industries to human culture, commerce, health, and social advancement
- To sustain the industry and support its growth, vitality, and future through the TAPPI Foundation.
We invite you to be a part of this momentous event. The sooner you join us the more opportunities there are for recognition of your company, its products, and key innovations. Keep in mind that an early commitment allows you to spread your investment over multiple years' budgets.
For more information on sponsorship and volunteer opportunities please contact dbell@tappi.org.
The sponsorship prospectus can be downloaded online.
Back To Top
|
Do you have a history book gathering dust on your shelf? TAPPI's 100th year is coming soon and we are looking for donations to the TAPPI Library. Specifically, we are interested in histories of companies and mills in the paper and packaging industry (both producers and suppliers). Each donated book will have a bookplate in the front cover recognizing the donor. For more information please contact David Bell.
Please send books to:
c\o David Bell
TAPPI
15 Technology Parkway, South
Suite 115
Peachtree Corners, Georgia 30092
Back To Top
|
|
|
TAPPI Over the Wire | 15 Technology Pkwy. S. | Norcross, GA 30092 USA | Voice: 770.446.1400 | Fax: 770.446.6947
|
 |