 |
|
Weekly Spotlight
Pratt Industries, Conyers, Ga., USA has announced plans to build its fourth, 100% recycled containerboard mill, eventually bringing the company's overall containerboard capacity to 1.5 million tons
Learn More...
|
Shortly before Pratt Industries, Conyers, Ga., USA, announced plans to build a fourth paper mill (see article above), New York City Mayor Michael Bloomberg issued an official proclamation declaring this past September 17 "Pratt Industries Day" in the Big Apple to commemorate the recent production at Pratt's Staten Island mill of 5 million tons of recycled paper
Learn More...
|
This week the Sustainable Forestry Initiative (SFI) recognized Hans Wegner, chief sustainability officer of the National Geographic Society, with the SFI President's Award during its annual conference in San Antonio, Texas, USA.
Learn More...
|
The Canadian Institute of Forestry (CIF), Ottawa, Ont., Canada, this week announced a new partnership with the Forest Products Association of Canada (FPAC), Canadian Forestry Association (CFA), TreeCanada, and TDBank who are joining forces to celebrate National Forest Week 2013 under the theme, "the GreenestWorkforce"
Learn More...
|
Below is the latest listing of job openings in the TAPPI Career Center.
Learn More...
|
Market Roundup
Total U.S. printing and writing (P&W) paper shipments in August 2013 decreased 4% compared with August 2012, according to the AF&PA (Washington, D.C., USA) August 2013 Printing-Writing Paper Report released this week
Learn More...
|
August 2013 containerboard production in the U.S. increased 1.1% over July 2013, and 4.4% over the same month last year
Learn More...
|
Kraft paper shipments in the U.S. totaled 135, 400 tons in August, essentially flat compared with the prior month
Learn More...
|
Total August 2013 boxboard production in the U.S. increased by 2.8% compared with August 2012, and increased 3.2% from last month
Learn More...
|
Pulp & Paper
Andritz, Graz, Austria, reports that it has successfully completed startup of the PrimeLine tissue machine with a shoe press supplied to Ganzhou Hwagain Paper in China
Learn More...
|
Cascades Inc., Kingsey Falls, Qué., Canada, this week announced plans to install a second tissue machine at its mill in St. Helens, Ore., USA
Learn More...
|
Chinese tissue and board producers Wuhu Hengan Paper Co. and Shandong Sun Paper Industry Joint Stock Co. have placed several orders for Metso's automation solutions to boost their processes and improve product quality
Learn More...
|
Kemira Oyj, Finland, this past week signed an agreement to acquire Soto Industries Inc, a privately owned company headquartered in Vancouver, B.C., Canada
Learn More...
|
Metso, Finland, reports that its Pulp, Paper, and Power segment has completed statutory negotiations in most of its units serving the paper industry
Learn More...
|
Slave Lake Pulp, a division of West Fraser Mills Ltd., has contracted ADI Systems Inc., Fredericton, N.B., Canada, to install a wastewater treatment system at its pulp mill in Alberta, Canada
Learn More...
|
Tauriga Sciences Inc., New York, N.Y., USA, this week announced that it received the first product samples of 100% bamboo-based printing and photo copy paper from Green Hygienics Inc. (GHI), Cape Coral, Fla.
Learn More...
|
Tembec, Montreal, Qué., Canada, this week announced that it has secured additional financing in the amount of $27.8 million to fund a portion of the Temiscaming, Qué., specialty cellulose cogeneration project
Learn More...
|
UPM, Finland, this week said that it has decided to renew apprenticeship programs at its Kymi and Kaukas mills in Finland
Learn More...
|
Wangpaper Co., (a member of the Wangkanai Group), Thailand, has ordered from PMP Group, Poland, an Intelli-Tissue® 900 machine for the production of premium quality tissue with low media consumption
Learn More...
|
Containerboard/Packaging
In response to demands for new solutions addressing folding carton, corrugated, and flexible packaging applications, Kodak, Rochester, N.Y., USA, and Bobst, Switzerland, report that they have formed a strategic development agreement to integrate Kodak technology into the Bobst portfolio of packaging production equipment
Learn More...
|
Metsä Board, Finland, a producer of coated white-top kraftliners, has introduced a new fully bleached liner that complements its Kemiart range
Learn More...
|
Rengo Co., Kita-ku, Osaka, Japan, this past week announced that Thai Containers Group Co. (TCG), Thailand, a joint venture between Rengo and SCG Paper Public Co., a subsidiary of The Siam Cement Public Co., has completed the acquisition of a 90% stake in PT Primacorr Mandiri, which operates a plant in the suburbs of Jakarta, Indonesia
Learn More...
|
|
New Products
H.B. Fuller, St. Paul, Minn., USA, showcased its Sesame® High Modulus Tape at Pack Expo in Las Vegas, Nev., this week, noting that with the new tape, produce trays see improved stacking longevity and up to 40% enhanced bulge resistance versus the same packaging with no reinforcement
Learn More...
|
HIS, Englewood, Colo., USA, has released IHS StruxureTM 6.1 software for maintenance, repair, and operations (MRO) supply chain management
Learn More...
|
EAM-Mosca Corp., Hazle Township, Pa., USA, has introduced its new, fully automated inline strapping machines UATRI-2 XT (right ) and MCB-2 XT (left) , which meet the specific needs of the corrugated cardboard industry
Learn More...
|
PMP Group, Poland, has launched a new promotional campaign focused on the "three forces of nature"—earth, wind, and fire
Learn More...
|
Published Pricing
DuPont, Wilmington, Del., USA, announced this week that it will increase prices on all of its titanium dioxide (TiO2) products sold in North America, Europe, Middle East, Africa, Latin America, and the Asia Pacific regions
Learn More...
|
Thermax Inc., Northville, Mich., USA, will increase prices for its Tulsion® ion exchange resins sold in North America by 5% to 10%, effective immediately or as contracts allow
Learn More...
|
Energy
Andritz Energy & Environment (AE&E), Graz, Austria, reports that it has received an order from energy utility Mjölby-Svartadalen Energi (MSE) of Sweden to supply a biomass-fired combined heat and power (CHP) plant for the town of Mjölby
Learn More...
|
People
Finch Paper, Glens Falls, N.Y., USA, has appointed Gregory Maio VP, sales and marketing and the company's newest member of the Senior Leadership Team
Learn More...
|
NewPage Holdings Inc., Miamisburg, Ohio, USA, has appointed Linda Sheffield controller and chief accounting officer for NewPage and its subsidiaries, effective October 1
Learn More...
|
PaperlinX, Australia, this week announced that, effective immediately, Andrew Price has been appointed managing director and CEO
Learn More...
|
Hubert Lienhard, CEO of the German machinery company Voith, will take over the chair of the Asia-Pacific Committee of German Business (APA) in early 2014
Learn More...
|
TAPPI News
There is still time to register for TAPPI 2013 CorrExpo, October 7-9, at the JW Marriott in Indianapolis, Ind., USA.
Learn More...
|
Join us on Today, Thursday, September 26, at 1:00 p.m. EDT as Thanh Trung, VP Technology for FITNIR Analyzers Inc. presents a Webinar on Advanced Online Process Analyzers for Pulp Mill Control.
Learn More...
|
With a new TAPPI student chapter recently formed this June, attendance at their chapter meeting was larger than expected..
Learn More...
|
TAPPI's 2013 Nominating Committee presents a slate of candidates for three director positions on the TAPPI Board.
Learn More...
|
Doug Sweet, of Doug Sweet and Associates, will present "Paper Machine Vacuum Systems 101" on October 7 at 2:00 p.m. EST.
Learn More...
|
Abstracts addressing the latest advances in characterization, functionalization, modeling, new products, applications, and health and safety issues of renewable and sustainable nanomaterials are sought.
Learn More...
|
The TAPPI Microbiology and Microbial Technology committee has announced the next webinar in its series on Microbes in Papermaking, to be held October 16 at noon EST.
Learn More...
|
New web community for TAPPI members allows gathering and sharing of information on a wide range of business and industry topics that are important to them.
Learn More...
|
Tighten-up plans to attend the Piping System Training courses planned for two locations coming this fall, October 2-3, in Chicago, Ill., and October 23-24 in Houston, Texas.
Learn More...
|
Don't miss out on your chance to present at the largest program for the pulp and paper industry.
Learn More...
|
TAPPI will organize another tissue program to be held at the PaperCon 2014 Conference, scheduled for April 27-30 in Nashville, Tenn., USA.
Learn More...
|
Maintenance course returns October 8-10 in Raleigh, N.C., USA.
Learn More...
|
TAPPI members save $70 dollars off the list price. A percentage of proceeds from the sale of this book go to the TAPPI Foundation.
Learn More...
|
Member uses benefits of membership to expand global knowledge base.
Learn More...
|
"Kraft Recovery Boilers" is a comprehensive textbook that covers recovery boilers in great depth and pulls together information on combustion, safety, emissions, plugging, and corrosion. TAPPI members save $47 dollars on their order.
Learn More...
|
Foundations of Leadership Excellence, Oct. 22-24, 2013, is focused on the fundamentals of leadership and management skills for emerging leaders, high-potentials, and area operating managers and other technical professionals.
Learn More...
|
Members save $77 off the list price on the new 5th edition.
Learn More...
|
Join more than 7,000 TAPPI members across the world with 650-plus years of industry experience.
Learn More...
|
This once-in-a-lifetime event will expand public awareness, foster further connection, and provide outstanding opportunities for collaboration, growth, and investment in our future for all of those involved.
Learn More...
|
As TAPPI's 100th year approaches, we are looking for donations to the TAPPI Library.
Learn More...
|
|
Find us on Facebook
Network with us on LinkedIn
Follow us on Twitter
|
Weekly Spotlight
Pratt Industries, Conyers, Ga., USA has announced plans to build its fourth, 100% recycled containerboard mill, eventually bringing the company's overall containerboard capacity to 1.5 million tons. The new, $260 million mill will be located in Valpariaso, Ind., adjacent to the company's existing box-making plant, which is the world's largest.
Chairman and owner Anthony Pratt said construction would begin in March of next year and be completed by July 2015.
"This new facility will allow us to better service the needs of our expanding customer base not only in the Midwest, but throughout the U.S.," Anthony said. "And Indiana is a perfect fit for us. We've been a part of the business community here for many years now and we know there is a skilled, reliable workforce available to us."
The mill will occupy a new 250,000 sq. ft. building on a 50-acre site. It will include a wastewater pre-treatment facility and road improvements. When it reaches full capacity, the new facility will produce 360,000 tons of recycled paper each year.
Pratt expects the new mill will eventually employ more than 100 people. The company currently employs more than 300 at the box plant. It expects to begin hiring paper machine operators, equipment operators, electrical and instrumentation technicians, shipping representatives, waste yard personnel, shift supervisors, and maintenance associates late next year.
Valparaiso mayor Jonathon Costas believes the project represents "the single largest private taxpaying investment in the history of the city. And Pratt's state of the art green recycling technology will help conserve America's forests and landfills," he said. "It has been a real pleasure working alongside Pratt executives to pave the way for this expansion and it is clear to us why they have become the world's largest privately-held, 100% recycled paper and packaging company."
In the photo announcing the project (l-r) are: Gary Byrd, president, Pratt Holdings; Brian McPheely, Pratt CEO; Anthony Pratt; Mayor Costas; and Eric Doden, president of the Indiana Economic Development Corp
Back To Top
|
Shortly before Pratt Industries, Conyers, Ga., USA, announced plans to build a fourth paper mill (see article above), New York City Mayor Michael Bloomberg issued an official proclamation declaring this past September 17 "Pratt Industries Day" in the Big Apple to commemorate the recent production at Pratt's Staten Island mill of 5 million tons of recycled paper.
"About half of all the paper New Yorkers recycle is shipped here and recycled through the Pratt mill," the Mayor told an audience of Pratt customers, political and business leaders, and mill employees.
"If New Yorkers aren't impressed by that, they will appreciate the importance of what this paper gets turned into — pizza boxes, thousands of them every day! But pizza aside, Pratt Industries is really a key player in Plan NYC, our longer-term plan for creating a greater, greener, more sustainable city."
Bloomberg added that Pratt's barge system, which brings discarded paper from Manhattan down the Hudson River to the mill and eliminates the need for more than 350 trucks a week, "helps meet our ambitious recycling goal that we set in 2011, and that was to increase the city's recycling rate by 30% by the year 2017."
Pratt chairman Anthony Pratt noted that the company "has invested more than $350 million in New York, generating hundreds of jobs. And we would like to do even more by turning even more locally-generated paper into even more jobs and creating even more economic security for this great city."
Anthony also made special mention of employees at the mill, who have produced enough paper to fill the Empire State Building more than four times. "Thank you to manager Jay Hennessey and his dedicated team on reaching this milestone...well done to all," he said. "It's a wonderful achievement."
Not to be outdone, Pratt's sister mill in Conyers recently passed the 6 million ton mark, and the company's third mill, in Shreveport, La., has produced more than 1.5 million tons since start up in 2009.
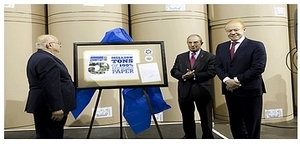
In the photo, company chairman Anthony Pratt is joined by New York City Mayor Michael Bloomberg (center) and Staten Island Borough President James Molinaro (left) at the unveiling of the plaque celebrating the mill's papermaking milestone.
Back To Top
|
This week the Sustainable Forestry Initiative (SFI) recognized Hans Wegner, chief sustainability officer of the National Geographic Society, with the SFI President's Award during its annual conference in San Antonio, Texas, USA. Wegner's many contributions—both personally and on behalf of National Geographic Society—have been instrumental in raising awareness of the benefits associated with utilizing forest certification as a proof point for sourcing forest products responsibly and for modeling sustainability principles into daily decisions, SFI noted.
"Hans' commitment to sustainability is matched only by the depth of his knowledge and his passion for raising awareness among others," said SFI President and CEO Kathy Abusow. "Hans believes that as a publisher, National Geographic Society has a crucial role to play in encouraging responsible forestry practices and helping to build the foundation of a sustainability model for all users of forest products. He is a true leader in the cause of sustainable forestry."
Hans Wegner, chief sustainability officer of the National Geographic Society, said that "we, as publishers, are constantly looking for ways to demonstrate that we are sourcing our paper responsibly, Our commitment to the SFI Forest Partners Program is a tangible way to increase the supply of certified fiber that helps us meet our responsible procurement objectives."
Wegner recommended that National Geographic take part in a SFI certification pilot project in Maine that became the foundation for the SFI Forest Partners program. Joining the National Geographic Society, Time Inc., Macmillan Publishers, and Pearson added their support to the SFI Forest Partners program to develop innovative approaches to certification with the goals of increasing the amount of fiber available from certified forestlands through chain-of-custody and fiber sourcing certification by establishing a goal of expanding certified U.S. forestland by 10 million acres by the end of 2017. Under Wegner's leadership, the National Geographic Society undertook a complete carbon footprint analysis of the operations of its headquarters and implemented a variety of measures to achieve carbon neutral status for its complex.
Back To Top
|
The Canadian Institute of Forestry (CIF), Ottawa, Ont., Canada, this week announced a new partnership with the Forest Products Association of Canada (FPAC), Canadian Forestry Association (CFA), TreeCanada, and TDBank who are joining forces to celebrate National Forest Week 2013 under the theme, "the GreenestWorkforce," which helps promote the new direction of Canada's forest products industry while recognizing the "green" credentials of those who work in the sector. It is also an online tool that highlights the work-life balance on offer to the next generation of employees and outlines a broad variety of solid careers now available in the industry.
"National Forest Week recognizes the importance of the forests in Canada. This year we are thrilled to see an inclusive partnership among some of the largest national organizations representing the forest sector united under a single banner: The GreenestWorkforce," says Dr. Tat Smith, president of CIF. "The GreenestWorkforce recognizes the stewardship and responsibility that our workforce embraces, and highlights the amazing opportunities available in the sector while promoting the work-life balance that the industry's workforce has come to enjoy. There really is something for everyone."
David Lindsay, president and CEO of FPAC, added that "this national partnership proves how motivated and focused the industry has become in telling its story of transformation, opportunity, and growth. We have adopted the brand of the GreenestWorkforce to help the industry attract workers who care about the environment and their future."
Under FPAC's Vision2020 plan, the forest products industry is looking to renew its workforce with an additional 60,000 workers, including more women, Aboriginals, and new Canadians. Vision2020 also seeks to further environmental credentials of the forest sector by 35% and to generate an additional $20 billion in economic activity from new products and markets by the end of the decade.
"Canadians can actively engage in this year's National Forest Week theme by inviting foresters into the classroom to teach students about Canada's world leading progressive forest management practices. Students can also learn about the innovative green products that can be made from forest fiber such as cosmetics, car parts, and clothing," says Dave Lemkay, GM of CFA. "We encourage everyone to find out what is happening in their region, or start their own event to raise awareness of the importance of the industry to our past, our present, and our future."
National Forest Week is a challenge to individual Canadians to learn more about their forest heritage and support greater recognition of this valuable resource. It runs this week, from September 23 to 28. National Tree Day was observed on Wednesday September 25.
More information is available online.
Back To Top
|
Below is the latest listing of job openings in the TAPPI Career Center. The current listing includes job openings for a variety of positions including sales representative, quality team leader, operations manager, power-utilities process engineer, technical service manager, and two process engineers. Current, specific job openings at companies and locations in the TAPPI Career Center include:
Employer |
Title |
Location |
DuBois Chemicals |
Sales Representative |
NE La./SE Ark |
Homasote Co. |
Laboratory and Technical Mgr. |
W. Trenton, N.J. |
KapStone Paper & Packaging |
Quality Team Leader |
Longview, Wash. |
Layfield Group |
Process Engineer |
Richmond, B.C. |
Orchids Paper Products |
Paper Machine Supervisor |
Tulsa, Okla. |
Pratt Industries |
Operations Manager |
Conyers, Ga. |
RockTenn |
Merch. Displays Design Assistant |
Bentonville, Ark. |
Sappi |
Power-Utilities Process Eng. |
Cloquet, Minn. |
Tru Vue Inc. |
Technical Service Manager |
McCook, Ill. |
Zilkha Biomass |
Process Engineer |
Houston, Texas |
More information about these jobs is available online.
Back To Top
|
Market Roundup
Total U.S. printing and writing (P&W) paper shipments in August 2013 decreased 4% compared with August 2012, according to the AF&PA (Washington, D.C., USA) August 2013 Printing-Writing Paper Report released this week. Additional key findings of the report include:
- August coated free sheet (CFS) paper shipments decreased 5% compared with August 2012, with year-to-date shipments through August essentially flat compared with 2012. U.S. imports of CFS papers decreased 6% year-over-year in July.
- Uncoated free sheet (UFS) paper shipments decreased 3% in August. For the year, shipments are down 3% in 2013. U.S. exports of UFS papers in July increased year-over-year for the fourth consecutive month.
- August uncoated mechanical (UM) paper shipments decreased 7% compared with August 2012, with year-over-year imports through June up 6%. UM exports are up 12% in 2013 compared with the first seven months of 2012.
- Coated mechanical (CM) shipments in August decreased 6% compared with August 2012. Shipments of CM are down 11% for the year, with imports up 4% year-over-year through July.
Back To Top
|
August 2013 containerboard production in the U.S. increased 1.1% over July 2013, and 4.4% over the same month last year, according to the AF&PA (Washington, D.C., USA) August 2013 U.S. Containerboard Statistics Report issue this week. The month-over-month average daily production increased 1.1%. The containerboard operating rate for August increased 1 point from July, from 98.6% to 99.6%.
Back To Top
|
Kraft paper shipments in the U.S. totaled 135, 400 tons in August, essentially flat compared with the prior month. Bleached kraft paper shipments, AF&PA (Washington, D.C., USA) notes in its August 2013 Kraft Paper Report, increased year-over-year 13.2%, but the 4.4% year-over-year decline in unbleached kraft paper shipments was enough to bring overall kraft paper shipments down 2.1% year-over-year.
Total month-end inventory also remained essentially flat compared with July 2013, according to the AF&PA report.
Back To Top
|
Total August 2013 boxboard production in the U.S. increased by 2.8% compared with August 2012, and increased 3.2% from last month, AF&PA (Washington, D.C., USA) stated in its recently published August 2013 U.S. Paperboard Report. Unbleached kraft boxboard production increased over the same month last year, and increased compared with last month.
Total solid bleached boxboard and liner production increased compared with August 2012, and increased compared with last month. The production of recycled boxboard increased compared with August 2012, and increased compared with last month.
Back To Top
|
Pulp & Paper
Andritz, Graz, Austria, reports that it has successfully completed startup of the PrimeLine tissue machine with a shoe press supplied to Ganzhou Hwagain Paper in China. "We were impressed by the startup. It took only 15 min. from starting up the stock pump to the first paper on the reel,"said Liang Hongwei, chief engineer at Ganzhou Hwagain Paper.
According to Hongwei, "the proven Andritz shoe press technology and its energy and drying efficiency, as well as the decades of experience that Andritz has in the pulp and paper industry, were decisive in the award of this order,"
The scope of supply included the stock preparation plant for softwood, hardwood, and bamboo pulp, the two-layer headbox with dilution control system, a shoe press, the wet dust removal system, a reel system, and the machine automation control system.
The company additionally reports that preparations are currently underway for startup of a second Andritz tissue machine supplied to Ganzhou Hwagain Paper, which is scheduled for the coming months.
Back To Top
|
Cascades Inc., Kingsey Falls, Qué., Canada, this week announced plans to install a second tissue machine at its mill in St. Helens, Ore., USA. The project will be realized through the acquisition of the specialty paper machine previously operated by Boise Inc., which is located adjacent to Cascades existing tissue machine. This machine will be reconfigured to produce 55,000 tons of tissue paper annually, bringing the total tissue paper capacity of the St. Helens' site to 120,000 tons annually. The total cost of the project is estimated to be $35 million, and startup is planned for the fourth quarter of 2014.
Suzanne Blanchet, president and CEO of Cascades Tissue Group, said that "we have targeted the West Coast as an area of growth for us. This machine will manufacture hand towels and napkins for the away-from-home market. The retrofitting of an existing machine will allow us to bring the additional capacity to this market at a reduced capital cost and on a faster timeline than if we were to build a new machine. Moreover, the addition of a second machine will allow us to improve the overall operating efficiency of the St. Helen's operation as a whole. "
Mario Plourde, president and CEO of Cascades, added that "this investment fits perfectly with our stated strategic objective of prioritizing investments in the tissue and packaging sectors. The addition of this machine combined with other ongoing projects will further strengthen Cascades growing position in the North American tissue market."
The existing labor force being able to operate and maintain the new machinery was a key reason for the decision to locate in St. Helens. This new line is expected to add 29 new jobs over the coming year and help preserve 59 existing jobs at the mill.
Senator Betsy Johnson noted that "since the announcement of the loss of jobs at the paper mill, State Representative Brad Witt and I have been using all of the tools at our disposal to save these jobs. We are very happy that Cascades is expanding its operations in St. Helens."
Robert Blumberg, board president, Columbia County Economic Team (CCET), added that "we are proud of our joint efforts to expand Cascades operations in St. Helens. Business retention and expansion is one of the main goals of the CCET."
Cascades Tissue Group, a division of Cascades Canada ULC, is the fourth largest producer of tissue paper in North America. Founded in 1964, Cascades produces, converts, and markets packaging and tissue products that are composed mainly of recycled fiber. The company has more than 12,000 employees who work in more than 100 units located in North America and Europe.
Back To Top
|
Chinese tissue and board producers Wuhu Hengan Paper Co. and Shandong Sun Paper Industry Joint Stock Co. have placed several orders for Metso's automation solutions to boost their processes and improve product quality. Wuhu Hengan has chosen the Metso DNA automation system, the Metso IQ quality control system, and non-radiation IQ Fiber Weight Measurement technology for new tissue lines at its greenfield tissue mill.
Metso IQ is a quality control systems (QCS) approach that integrates process quality management, measurements, and profile controls with profilers to provide operating personnel with what they need to understand and manage the process.
Shandong Sun Paper has placed an order for two Metso Wet End Analyzers (Metso WEM) for its new production lines. These analyzers combine all of the relevant wet end variables as a total solution for wet end management. To meet the objectives set for quality, runnability, and overall efficiency, it is vital to stabilize consistency, ash content, charge. and chemistry at startups, during normal operation, and after grade changes. It is best done by measuring, analyzing, controlling, and managing the wet end as comprehensively as possible with cutting-edge analyzer technology, Metso explains.
"Today, more and more chemicals are used in the tissue production process. It is necessary to measure online the most suitable chemical environment for the process," ZhongDe Ye, VP, Sales & Service, Great China, Automation, Metso, points out. "The customer already has several Metso charge analyzers on another paper machine, so they know the analyzers' real performance and how this benefits the process."
Additionally, Metso has received an order for Metso IQ quality control technology to be supplied to a Chinese coated board production line. The line will be rebuilt to produce high-quality folding boxboard. Metso's delivery will include a Metso IQ Scanner with MD and CD controls to provide fast, high-resolution sheet quality profiles from edge to edge. A Metso IQ Dilution Profiler (IQ Dilution Profiler), a profile control system for advanced positioning of the headbox valves, also will be supplied to achieve the best possible weight profiles.
Back To Top
|
Kemira Oyj, Finland, this past week signed an agreement to acquire Soto Industries Inc, a privately owned company headquartered in Vancouver, B.C., Canada. Soto is a specialty chemicals and services supplier to the pulp and paper industry. The parties agreed not to disclose the transaction price.
Soto supplies a broad range of specialty chemicals including digester scale control, silicone and oil-based defoamers, and polymers used in green liquor clarification and effluent treatment for pulp and papermaking.
"This acquisition helps us accelerate our strategic plan and secures our position as a leading supplier to the pulp and paper industry in North America. It also supports Kemira's objective of achieving above-the-market growth in the mature markets. In addition to the strong strategic fit, the transaction is expected to result in synergies through raw material, logistics, and fixed cost savings," said Billy Ford, SVP, Paper segment, North America.
Back To Top
|
Metso, Finland, reports that its Pulp, Paper, and Power segment has completed statutory negotiations in most of its units serving the paper industry. As a result of these, the workforce in Finland will be reduced by a total of 660 positions.
The negotiations were part of Metso's global cost competitiveness program launched this past April to adapt to changes in the marketplace. The program targets an annual cost reduction in the Pulp, Paper, and Power segment of approximately EUR 100 million by 2016. The aim of the personnel reductions at this stage is to achieve savings of approximately EUR 50 million in annual costs. The cost savings for 2013 are estimated to be EUR 5 million.
The original workforce estimate was for a reduction of 750 positions, some 90 fewer than the current estimate. The reduction will take place through redundancies, retirement options, and terminations of temporary contracts. Internal transfers also will take place. The impact of the reductions on the different Metso locations will be determined soon, after details of how many employees will transfer to other locations within the company are known.
Statutory negotiations covering Finnish operations in the company's EMEA (Europe, Middle East, Africa) area organization are continuing.
In addition to personnel reductions, temporary layoffs might also be possible if required by the business' workload or financial situation. This possibility will remain in force until the end of 2014, by which time the situation will have been reviewed. The possibility of temporary layoffs affects all units serving the paper industry.
Metso will provide a range of support measures for those affected by the restructuring through its "Polku" employment support program, which includes support for entrepreneurship, studying, and re-employment, such as job-to-job training, and relocation support.
"These personnel reductions are necessary to adjust our capacity in the Paper business to meet the fundamental structural changes that have taken place in our operating environment. Working together with personnel representatives, we are actively seeking to soften the impact of the reductions with the help of our wide-ranging employment support program," said Pasi Laine, president of Metso's Pulp, Paper, and Power segment.
Back To Top
|
Slave Lake Pulp, a division of West Fraser Mills Ltd., has contracted ADI Systems Inc., Fredericton, N.B., Canada, to install a wastewater treatment system at its pulp mill in Alberta, Canada. Slave Lake Pulp is a bleached chemi-thermomechanical pulp (BCTMP) mill that produces approximately 240,000 metric tpy of hardwood BCTMP. The new system is expected to be in operation by fall 2014.
The wastewater treatment project will include the installation of an anaerobic ADI-BVF® reactor with a biogas scrubbing system. The anaerobic reactor will reduce demand on the mill's existing aerobic treatment system and will generate biogas. The biogas will be burned in a new co-generation facility to produce up to 6 MW of green electricity for mill use. It is estimated that approximately 30,000 cubic meters per day of methane will be produced from the biogas, roughly enough energy to heat 4,000 Canadian homes.
This new system will ultimately lower Slave Lake Pulp's annual operating costs and allow the mill to continue to meet or exceed environmental requirements for the industry.
ADI Systems, an ADI Group company, has been providing wastewater treatment, anaerobic digestion, and biogas treatment solutions to industry for 30-plus years. It has more than 200 installations worldwide.
Back To Top
|
Tauriga Sciences Inc., New York, N.Y., USA, this week announced that it received the first product samples of 100% bamboo-based printing and photo copy paper from Green Hygienics Inc. (GHI), Cape Coral, Fla. The paper is composed exclusively of bamboo pulp rather than wood pulp and Tauriga says that its quality compares favorably to competitive wood based products. GHI has provided Tauriga with both pricing and delivery schedules for the bamboo-based printing and copy paper, which are packaged in distinct reams of 250 and 500 sheets.
According to Tauriga, several potential and prospective customers will be given product samples in the near future to test the quality of the product and to determine whether the pricing structure is satisfactory for their respective practices or businesses. These potential customers include law practices, physician practices, hospitals, school districts, adult/nursing homes, and a multi-billion dollar Louisiana based corporation. Under terms of the license agreement between Tauriga and GHI, Tauriga will realize 100% of the revenue from purchase orders (pertaining to the license agreement), with net profits being split 50-50 between the licensor and the licensee.
Tauriga notes that it has received a high level of interest from several potential customers, and the company's management is focused on generating profitable revenues during the remainder of calendar year 2013 and beyond.
Back To Top
|
Tembec, Montreal, Qué., Canada, this week announced that it has secured additional financing in the amount of $27.8 million to fund a portion of the Temiscaming, Qué., specialty cellulose cogeneration project. In particular, Tembec has entered into an additional loan in the amount of $17.8 million with Investissement Québec (IQ) and has entered into an amended and restated credit agreement with Integrated Private Debt Fund III LP (IPD), as agent for the project's senior lenders, increasing its credit facility by $10 million (IPD loan).
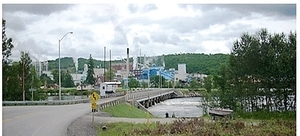
This additional $27.8 million in loans increases the total project financing to $132.8 million, with IQ now committed to $92.8 million of the financing and IPD committed to $40 million. Both the IQ loan and the IPD loan remain subject to the satisfaction of certain customary closing conditions, including the granting of new security for the loans.
To the end of August 2013, Tembec has spent $131 million on the project, which has a total estimated cost of $235 million. The company has used a total of $48 million of the previously noted $133 million of project financing. Of the remaining $104 million to be spent, $85 million will be funded by the remaining project financing and $29 million from the company's internally generated cash flow.
The project involves the replacement of three low-pressure boilers with a single new high-pressure boiler designed to burn waste sulfite liquor generated by the specialty cellulose manufacturing process. The project also includes the installation of a new 50-MW electrical turbine.
Completion of the boiler portion of the project is scheduled for April 2014 and startup of the turbine should occur in September 2014. The company anticipates that the project will improve annual adjusted EBITDA by approximately $48 million. The improvement will include approximately $28 million of incremental electricity revenues, $7 million of operating and maintenance cost reduction, and $13 million of productivity and margin enhancements associated with an annual production increase of 15,000 metric tons of specialty cellulose pulp.
Tembec is a producer of forest products--pulp, paper, specialty cellulose, and wood products. Its principal operations are in Canada and France, and the company has some 3,400 employees and annual sales of approximately $2 billion.
Back To Top
|
UPM, Finland, this week said that it has decided to renew apprenticeship programs at its Kymi and Kaukas mills in Finland. The company has accordingly opened a total of 45 apprentice vacancies in Kuusankoski and Lappeenranta for a two-year trainee program. The renewed apprenticeship program aims at a vocational degree in the paper industry and is carried out in co-operation with the Sampo vocational school of Saimaa.
"The average age of our personnel is high and we want to engage the training of the new working generation in time before the current generations begin to retire," said Juha Kääriäinen, GM of Kymi and Kaukas pulp and paper mills.
The two-year apprenticeship trainee program will enable working in both process and maintenance duties at the pulp and paper mills, leading to the vocational degree. Entry level requirements include 18 years of age and applicable vocational degree in electrical, automation, machine, automotive, or process engineering.
The renewed apprenticeship program will mainly consist of practical training at work that aims at building more versatile professional capabilities in different departments at the mills. "Our versatile trainee program is targeted to increase the mobility of our employees within and between Kymi and Kaukas mills but also between other UPM mills in Finland, especially during maintenance breaks when the needs of the repair and maintenance staff is high," Kääriäinen said.
UPM's Kymi and Kaukas mills have planned to engage trainee programs annually. Applicants that are chosen for the program will get two-year apprenticeship contracts. Applications for the program starting in January 2014 are to be sent through UPM's internet site by October 15.
Back To Top
|
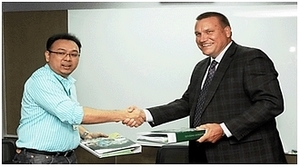 Wangpaper Co., (a member of the Wangkanai Group), Thailand, has ordered from PMP Group, Poland, an Intelli-Tissue® 900 machine for the production of premium quality tissue with low media consumption. The new tissue machine is an expansion of Wangkanai Group's "market horizons" into a new business sector. The group started as a single company, known as Limited, which operates a sugar factory. Over the years, the company extended its operations to include other businesses, some related directly and indirectly to sugar production, and some completely independent of it, such as Wangpaper.
PMP Group says that it is also executing an expansion plan in Asia, with Wangpaper being one of its first projects in Thailand. PMP Group has been active on the Asian market since 2008 and, to date, has completed 38 major projects, in six Asian countries, for 28 customers. The Wangpaper project now expands the company's presence into seven Asian countries.
Back To Top
|
Containerboard/Packaging
In response to demands for new solutions addressing folding carton, corrugated, and flexible packaging applications, Kodak, Rochester, N.Y., USA, and Bobst, Switzerland, report that they have formed a strategic development agreement to integrate Kodak technology into the Bobst portfolio of packaging production equipment. Kodak provides disruptive technologies and solutions for the product goods packaging, graphic communications, and functional printing industries, and Bobst is a supplier of machinery and services to packaging manufacturers in the folding carton, corrugated board, and flexible material industries.
"Bobst's commitment to introducing innovative products, its loyal customer base, and Kodak's portfolio of advanced technologies, including the Kodak Stream Inkjet technology, are a powerful combination that we believe will stimulate growth and transformation for Bobst customers and for our industry," said Antonio M. Perez, Kodak chairman and CEO.
"Flexibility, time to market and improved total cost of ownership are increasingly important to our customers. To extend the capabilities of packaging production equipment, we decided to join forces with Kodak in particular because of their strength in the digital arena," noted Jean-Pascal Bobst, CEO of Bobst Group.
Back To Top
|
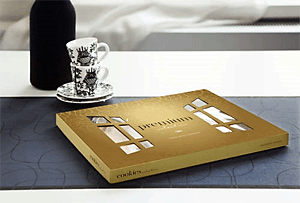 Metsä Board, Finland, a producer of coated white-top kraftliners, has introduced a new fully bleached liner that complements its Kemiart range. Modo Northern Light is a lightweight, uncoated liner with high whiteness, ideal for microflute as well as for traditional corrugated packaging. Made from fresh forest fibers, it is suitable for direct contact with food and other sensitive products.
Modo Northern Light comes in a low substance range from 80-160 gsm and a bright white shade, making it suitable for microflute applications such as perfume, beautycare, and healthcare, as well as packaging for mobile devices. It also performs well in larger applications, such as online and mail-order packaging. In corrugating, it has a low washboarding tendency due to its bulk, and printability of both solids and screens is excellent, with high contrast. It can be used as a top liner, as fluting, and as a reverse side liner. The new fully bleached liner is manufactured at Metsä Board's Husum mill in Sweden.
"This new product complements our Kemiart range of white top kraftliners by providing even more options for our customers," says Risto Auero, VP Linerboard Sales, Metsä Board Paperboard. "Modo Northern Light helps meet demand for lighter-weight packaging and opens up exciting opportunities for combining a lighter liner with fluting in innovative ways."
Back To Top
|
Rengo Co., Kita-ku, Osaka, Japan, this past week announced that Thai Containers Group Co. (TCG), Thailand, a joint venture between Rengo and SCG Paper Public Co., a subsidiary of The Siam Cement Public Co., has completed the acquisition of a 90% stake in PT Primacorr Mandiri, which operates a plant in the suburbs of Jakarta, Indonesia. Combining the four existing plants operated by PT Surya Rengo Containers (SRC), a joint venture between PT Indofood CBP Sukses Makmur and Rengo, the annual production capacity in Indonesia will increase to 228,000 metric tons, enabling TCG and SRC to capture the ever-growing demands in Indonesia, the company noted.
Further growth of corrugated demand in Indonesia can be expected, Rengo points out, as many Japanese companies choose the country as their manufacturing base in the ASEAN region, and as national income increases. Corrugated packaging in Southeast Asia is an important strategic focus for the overseas business of the Rengo Group—which aims to be a "General Packaging Industry"—and Rengo says it will work to further enhance its corrugated packaging supply system within the region.
Back To Top
|
New Products
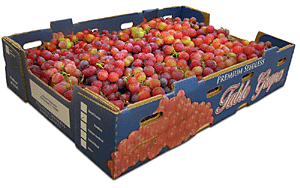 H.B. Fuller, St. Paul, Minn., USA, showcased its Sesame® High Modulus Tape at Pack Expo in Las Vegas, Nev., this week, noting that with the new tape, produce trays see improved stacking longevity and up to 40% enhanced bulge resistance versus the same packaging with no reinforcement. The company pointed out that applied to the bottom of horizontally-corrugated trays, the tape provides a reduction in the rate of bottom sag in a humid environment and a 45% reduction in sag in cold humid conditions versus trays with no reinforcement. This translates to increased time-to-sag failure of more than 10 times, H.B. Fuller emphasized.
Sesame High Modulus Tape also is designed for greater compression strength, which increases stacking strength, keeps stacks straighter longer, and reduces stack failure when compared with the same trays without reinforcement. This tape applied to hand holes of corrugated, Euro-style trays provides a 15% to 23% increase in average compression strength compared with trays without reinforcement and a 4% to 10% increase in average compression strength in regular slotted cartons (RSC), trays, and bins, the company said.
This reinforcement tape technology provides clear advantages in supply chain integrity, cost savings, and sustainability. Stacks of produce and RSC maintain strength and shape longer during transport, endure transit vibration, and reduce damage from fluctuating temperature and humidity conditions. Cost savings also can be achieved through optimizing corrugated linerboard weights and reducing the corrugated footprint while still maintaining necessary box strength. Sustainability goals can be enhanced by reduced dependence on petroleum-derived plastics and polystyrene packaging, according to H.B. Fuller.
More information about Sesame High Modulus Tape is available online.
Back To Top
|
HIS, Englewood, Colo., USA, has released IHS StruxureTM 6.1 software for maintenance, repair, and operations (MRO) supply chain management. The web-based software application is for managing MRO catalogs while providing the foundation for sustained MRO data governance across a customer's enterprise resource planning (ERP), enterprise asset management (EAM), or computerized maintenance management systems investments.
Struxure 6.1 provides excellent global language support, reporting, and analytics, while boosting user performance, product usability, and the breadth of MRO content capabilities. It includes the following keynote system enhancements:
- Enhanced seamless multilingual capabilities with advanced searching and translation
- Connections to multiple ERP/EAM systems by language and/or item criteria
- Redesigned user interface preview with an all-new Login Screen and Menu for streamlining Struxure's ease of use
- Simplified multilingual data maintenance and review with language/system selection drop-down, enabling users to instantaneously change interface and data to the selected language or system
- Improved workflow capabilities.
The new software is the bedrock for enforcing the rules and best practices necessary for creating and maintaining standardized, comprehensive MRO item descriptions.
At the core of the Struxure application is the IHS Standard Modifier DictionaryTM (SMD), a classification schema that delivers industry-aligned templates with consistent, repeatable rules designed specifically for characterizing MRO master data. Together, Struxure and SMD seamlessly integrate into multiple enterprise systems to enable a unified information strategy and dynamically synchronize MRO data. This approach allows for real-time visibility into MRO inventory and greater control over maintenance, operations, supply chain, and procurement effectiveness.
More information about the IHS MRO solutions is available online.
Back To Top
|
EAM-Mosca Corp., Hazle Township, Pa., USA, has introduced its new, fully automated inline strapping machines UATRI-2 XT (right ) and MCB-2 XT (left) , which meet the specific needs of the corrugated cardboard industry. Improvements to the motor systems and a simplified user interface ensure extremely gentle, fast, and reliable strapping of corrugated cardboard with the UATRI-2 XT. The MCB-2 XT is Mosca's high-performance successor of the MCB-2. The auto set-up function ensures that the machine is automatically aligned after the first bundle. To avoid damage to the structure of the corrugated cardboard, both machines apply the strap "inline," that is along the corrugations.
Using the auto set-up function, the MCB-2 XT checks the dimensions of the first infed bundle and then automatically creates the required settings. Once the machine has been set up, an integrated five-sided bundle monitor feeds perfectly aligned, uniform bundles ready for strapping. The advantage of this automatic set-up function is that it enables customers to process batches of different sizes without any major machine set-up time or manual adjustment. The bundles are securely guided through the strapping process by directly driven conveyor systems with frequency control. Non-wearing, direct-drive DC motors power the bundle alignment. A pusher system pushes the bundles into the pre-tensioned strap, which is applied at three points on the bundle. A swing arm then positions and tensions the strap at the fourth point and activates the heat welding system.
If required, the model can be equipped with two sealing units, allowing two parallel straps to be applied simultaneously along the corrugations with a strapping output up to 27 bundles per minute. The parallel strapping ensures optimum product protection over long transport distances without slowing the strapping process. This option is particularly attractive for export, especially to destinations outside of Europe. In addition to saving on material costs (because the corrugated cardboard stacks are generally shorter than they are wide), the "inline" strapping also protects the product from damage to the structure of the corrugated cardboard.
Like the MCB-2 XT strapping machine, the new UATRI-2 XT also straps "inline" and facilitates work for the user with automated processes. The high-performance machine runs on a completely upgraded motor management technology and can be easily integrated in automated high-speed corrugated cardboard production lines. Along with its automatic set-up, the machine also automatically configures torque and other motor parameters to match the need of the products. It calculates the time it will take from detection of the load by the photoelectric barrier to operation of the required strapping functions. The UATRI-2 XT adjusts motor parameters to provide a slower, more powerful feed for large bundles and a lower-power, faster feed for small bundles.
While controls were integrated into the motors of the earlier types, the new UATRI-2 XT relies on centralized motor control. This prevents machine failure and ensures absolute reliability of the strapping system in the automatic production line. The roller drive on the UATRI-2 XT is equipped with a split belt system. Power is transmitted through two drive belts with the main belt guided on an innovative roller bed, simplifying maintenance, increasing the power/performance ratio, and extending service life.
A touch panel with a revised user interface simplifies control of the UATRI-2 XT to prevent work interruptions and damage to the machine by incorrect operation. Different safety levels can be activated according to the operator's skill and experience. There is no need to interrupt production to manually change strap coils. The machine is equipped with two coil dispensers. When one coil runs out of strap, the other strap is automatically joined. With 1,000 coil changes annually, this automatic strap coil change avoids around 50 hours machine downtime. That is equal to 75,000 bundles that could have been strapped in this time at a rate of 25 bundles per minute.
With an optional quality assurance system integrated in the machine, the UATRI-2 XT automatically detects bundles that do not meet specified criteria. Control software in the upstream production stage monitors bundles to ensure they meet the required quality standards. Non-compliant bundles are rejected and moved from the line by the downstream roller chain conveyor.
The special configuration of the machine enables up to 30 bundles per minute to be strapped individually or in parallel in perfectly aligned stacks. The bundles are perfectly aligned on all sides by the plates of an integrated squaring station and held securely in place, which makes sure the machine delivers the stacks neatly strapped.
Back To Top
|
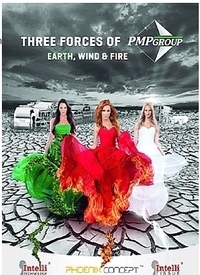 PMP Group, Poland, has launched a new promotional campaign focused on the "three forces of nature"—earth, wind, and fire. The company notes that these three forces of nature have always been associated with power, strength, and vitality. Their metaphorical properties, it adds, have become an inspiration for PMP Group to start a new campaign that symbolizes the benefits of the company's three major technological lines in the pulp and paper business.
PMP's three-forces campaign is described as follows:
Earth–Intelli-Technology®. Platform concept for papermakers, characterized by low media consumption (ECO) and high runnability ("as we always pass the traffic lights when we see a green light")—thus the green color and the connection to Mother Nature. PMP's Intelli-Technology line reflects all benefits that are associated with one of the most powerful forces of nature—earth.
Wind–Intelli-Tissue®. Platform concept for tissue makers. Technology that produces premium tissue (light and bulky) and is characterized by cleanliness of equipment (hygienic, safe, for health)—thus the white color and wind to underline main features of the final product. The PMP Intelli Tissue line is as powerful and delicate as the wind itself, the company says.
Fire – Phoenix Concept™. The line that offers rebuilds on three levels: Basic (classic type, e.g., exchanging the old section for a new one); Advanced (logistically sophisticated, including PM/TM relocation and a profile change); and Premium (including basic/advanced level, plus products exclusively designed for a particular customer). The red color symbolizes energy and power to act. Fire underlines the dynamism. For PMP Group, Fire, it explains, is the link between Earth and Wind. In the technological concept, it refers to both the Intelli-Technology and Intelli-Tissue line.
Back To Top
|
Published Pricing
DuPont, Wilmington, Del., USA, announced this week that it will increase prices on all of its titanium dioxide (TiO2) products sold in North America, Europe, Middle East, Africa, Latin America, and the Asia Pacific regions, effective October 1, or as contracts allow, as follows:
- $100 per metric ton for Ti-Pure® titanium dioxide grades sold in the Asia Pacific and Latin America regions
- $100 per metric ton for Ti-Pure titanium dioxide grades sold in the dollar markets, or EUR 75 per metric ton in Eurozone markets in Europe, Middle East, and Africa region
- $0.05 per pound for Ti-Pure titanium dioxide grades sold in the North America region with the exception of RPS Vantage™ titanium dioxide products sold into paper and paperboard applications, which will be managed separately.
DuPont Titanium Technologies operates plants at DeLisle, Miss.; New Johnsonville, Tenn.; Edge Moor, Del.; Altamira, Mexico; and Kuan Yin, Taiwan, all of which use the chloride manufacturing process. The company also operates a mine in Starke, Fla.
Back To Top
|
Thermax Inc., Northville, Mich., USA, will increase prices for its Tulsion® ion exchange resins sold in North America by 5% to 10%, effective immediately or as contracts allow. Specific price increases will be determined based on resin grade, packaging, and delivery point.
Tulsion strong acid cation (SAC) industrial grade ion exchange resins purchased in full containers and delivered direct to customers are specifically excluded from this increase. "Higher materials, energy, and transportation costs related to the oil industry have exceeded our best efforts to keep overall costs at an acceptable level," said Steve Braley, CEO.
Tulsion ion exchange resins are used in the separation, recovery, and purification of a wide range of materials from water and process streams.
Back To Top
|
Energy
 Andritz Energy & Environment (AE&E), Graz, Austria, reports that it has received an order from energy utility Mjölby-Svartadalen Energi (MSE) of Sweden to supply a biomass-fired combined heat and power (CHP) plant for the town of Mjölby. Startup is scheduled for the third quarter of 2015.
The scope of supply consists of an EcoFluid bubbling fluidized bed boiler with a capacity of 35 MW, the fuel handling and flue gas cleaning systems, and a steam turbine with all auxiliary systems. The high efficiency of the boiler plant, and the technology to enhance environmental protection, were decisive in the award of this order, Andritz notes.
The new plant will supply renewable, clean energy for district heating in the town of Mjölby (26,000 inhabitants) in southern Sweden. AE&E is part of Andritz's Pulp and paper business area. The company designs and constructs turnkey power plants and supplies components such as steam generators and flue gas cleaning systems.
Back To Top
|
People
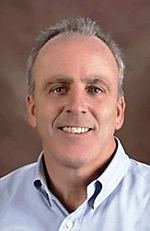 Finch Paper, Glens Falls, N.Y., USA, has appointed Gregory Maio VP, sales and marketing and the company's newest member of the Senior Leadership Team. Maio has earned a succession of sales leadership positions, serving more than a dozen years with National Envelope, of which the last five he was VP of sales. He has broad experience managing sales performance, developing distribution strategies, and driving a customer-focused culture. Maio began his career with envelope manufacturer Williamhouse-Regency (acquired by National Envelope in 1999) and is a business graduate of the University of Wisconsin-La Cross.
According to Finch Paper President and CEO Debabrata Mukherjee, "Greg's career includes more than 25 years of sales leadership and channel strategy in the uncoated freesheet market space. He brings a diverse background in sales, manufacturing and distribution, and performance improvement," Dr. Mukherjee said.
Maio joins Finch at a pivotal time, the company noted. As the industry is being reshaped by mill closures and repurposing, Maio is charged with setting strategy and directing Finch's sales efforts, drawing on the team's diverse and broad industry experience. "I look forward to the opportunities that this dynamic marketplace offers Finch," Greg remarked. "I have complete confidence in our ability to maneuver, invest, and grow in the number of partnerships we hold across North America."
Back To Top
|
NewPage Holdings Inc., Miamisburg, Ohio, USA, has appointed Linda Sheffield controller and chief accounting officer for NewPage and its subsidiaries, effective October 1. Sheffield has been with NewPage Corp. since its inception in 2005 and has served in key positions including treasurer and VP of finance, and most recently as VP of compliance. She was responsible for establishing new systems, internal controls, Sarbanes Oxley compliance, internal audit, and other processes necessary for corporate governance when NewPage was formed in 2005. As the company expanded, she led the finance integration of the businesses following the Stora Enso North America acquisition in 2007.
Sheffield previously held positions with increasing responsibility for predecessors to NewPage Corp. for more than 25 years. During this period, she held various positions including VP of finance with responsibility for the controllers group and shared services, VP of audit, and a division VP of finance and logistics. She also led finance integration activities following several major mergers and acquisitions.
Sheffield is replacing Patrick Buchenroth who resigned from the position of controller and chief accounting officer for NewPage and its subsidiaries, effective September 30. Buchenroth is leaving to take a senior operations role with a company in another industry.
"Linda has tremendous experience and we are excited to have her assume the role of controller and chief accounting officer. We also want to thank Pat who provided strong technical support on complex accounting issues during a transitional time for NewPage and wish him well in his new position," said Jay Epstein, SVP and CFO for NewPage. "Linda and Pat have worked closely together and will continue to do so over the next few weeks to ensure a smooth transition for the financial reporting group."
NewPage is a producer of printing and specialty papers in North America with $3.1 billion in net sales during 2012. The company owns paper mills in Kentucky, Maine, Maryland, Michigan, Minnesota, and Wisconsin, with a total annual production capacity of some 3.5 million tons of paper. The company's portfolio of paper products includes coated, supercalendered, and specialty papers.
Back To Top
|
PaperlinX, Australia, this week announced that, effective immediately, Andrew Price has been appointed managing director and CEO. Dave Allen has stepped down as the Group's CEO but will remain with the company until December 31 to assist with special projects and to work with Price on transition.
Robert Kaye, chairman of PaperlinX, said that "significant progress has been made during the past 12 months as the company restructures its business globally in the face of a declining paper market, while simultaneously focusing on developing its diversified businesses. We would like to thank Dave for his valuable contribution to the turnaround efforts at PaperlinX over the past 12 months.
"We are pleased that Andrew has accepted the role of managing director and CEO. Since his appointment as an executive director in November 2012, he has been working closely with management, particularly in Europe, to accelerate the restructuring initiatives. Accordingly, the board is confident that Andrew will be able to return PaperlinX to profitability in the shortest possible time," Kaye said.
Back To Top
|
Hubert Lienhard, CEO of the German machinery company Voith, will take over the chair of the Asia-Pacific Committee of German Business (APA) in early 2014. Following the CEOs of Siemens and BASF, Lienhard will be the first CEO of a German family-owned company to steer APA. APA was founded in 1993. Previous chairmen include the former Siemens-CEO Heinrich von Pierer and the former BASF-CEO Jürgen Hambrecht. The current APA chairman is Peter Löscher, the former Siemens CEO.
"We aim at strengthening trade and investment between Asia and Europe in both directions. And we need to reduce barriers to trade and investment," Lienhard stated. Value chains connect Asia and Europe in a much higher intensity compared with 10 years ago. This process needs to be accelerated towards further integrating Asian markets into the world economy. Today, research and development in business is international and needs to be close to the market and the customer.
"German industry is well positioned in Asia," Löscher, the current APA chairman, added. "The guiding principles of APA--partnership, innovation, and sustainability—fit well to the global challenges that need to be tackled jointly by the leaders from Europe and the Asia-Pacific region. It was a pleasure having been asked to chair APA in July 2010 and I will remain fully committed until the end of my term," Löscher assured. With the APA, he sees a unique tool for the German business community to ensure a joint position towards Asia.
Back To Top
|
TAPPI News
There is still time to register for TAPPI 2013 CorrExpo, October 7-9, at the JW Marriott in Indianapolis, Ind., USA .
Looking for the latest and greatest the industry has to offer? CorrExpo will include two What's New Sessions revealing 16 new developments to the corrugated industry since 2011. You'll also want to take a lap on the sold out exhibit floor.
The conference features two Keynote presentations. Alexander Toeldte, president and CEO- Boise Inc., will kick off the conference on Tuesday and on Wednesday you can learn about "Truly Human Leadership" from Bob Chapman, CEO andcChairman of Barry-Wehmiller. Come one hour early on both days and take in the technical expertise offered at the Eye Opener Sessions. Want to attend more than one? Set your alarm for both mornings; the sessions will be repeated on Wednesday.
The three concurrent Wednesday workshops will be like a performance-boosting pit stop created to give packaging pros that race-winning edge. The workshops are open to conference registrants, exhibitors, and those registered to visit the exhibit.
These are just a few of the highlights of the jam-packed program. Learn more at the conference website.
Back To Top
|
With increasing competition worldwide, pulp and paper manufacturers, particularly those in North America, require greater emphasis on cost reduction and increased efficiency and product quality.
Brought to you by the Process Control Division of TAPPI, the Advanced Online Process Analyzers for Pulp Mill Control webinar will briefly review the technology and give further details on economic impacts achieved through the installation of rugged process online FT-NIR analyzers when coupled with advanced process control strategies.
This free webinar will begin today, Thursday, September 26, at 1:00 p.m. EDT. and will be led by Thanh Trung, VP Technology for FITNIR Analyzers Inc.
Back To Top
|
On a recent visit to Virginia Tech's Center for Packaging and Unit Load Design, students showed their enthusiasm for the packaging industry and the support of industry partners and organizations like TAPPI in their pursuit of packaging careers. With a new TAPPI student chapter recently formed this June, attendance at their chapter meeting was larger than expected.
On this evening in September, about 25 students were present, generating a lot of energy in the room. TAPPI provided renewal notices for sponsored memberships and invited new students to join TAPPI, their memberships recently sponsored by TAPPI's generous corporate partners. Visibly appreciative, even as we only had 20 sponsored memberships to give out and many more wanting to be TAPPI Members. Student Chapter Advisor Dr. Young Teck Kim mentioned there were at least an additional 10 students who were not present needing sponsored TAPPI memberships. The VA Tech Center for Packaging and Unit Load Design boasts nearly 40 active students in their program, and is working to make a four-year degree in Packaging a reality.
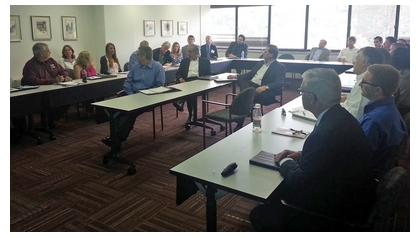
We spoke about TAPPI's enthusiasm around this unique chapter, about TAPPI Community, as well as the benefits of being connected to TAPPI, a lasting professional connection, something only TAPPI members can truly enjoy. Zack Shiner, the chapter president, spoke of the importance of being a part of organizations like TAPPI, and of course Dr. Kim spoke about how getting involved with TAPPI and connecting online can help with internships and jobs, as well as how the industry is global and thriving.
The following day, the Center hosted an Advisory Board meeting with at least 15 industry representatives, plus a few faculty and administrators and several students from the Packaging Center. Industry representatives were openly consulted on the skillsets needed in their respective businesses, as VA Tech wants to consider adding those areas of focus to an imminent Packaging curriculum. Among the topics were business and marketing, as well as preventing loss and damage, as the Center focuses on pallet development and quality and the role that pallets play in this, particularly with shipping internationally.
Students from the Center made presentations on their work, including a group summer project on pallet quality, stretch wrapping, and testing. Two PhD students presented and five undergraduate students presented on their work. It was clear that these students have a passion for what they are doing. Afterward, a reception in the Packaging lab of the Forest Products building provided a perfect venue to acknowledge significant equipment donations from industry representatives present at the meeting.
Back To Top
|
TAPPI's 2013 Nominating Committee presents a slate of candidates for three director positions on the TAPPI Board. The candidates are: Peter R. Augustine, president, Fabio Perini North America; Paul R. Durocher, director Coated Paper Development, Sappi Fine Paper North America; and Christopher A. Krumm, VP of Operations, CorrChoice, a Division of Greif.
Per the TAPPI Bylaws, members of the organization have until November 1, 2013, to review the slate.
Learn more about the slate and election process.
Back To Top
|
TAPPI's Papermaking and Water Removal Committees present an exciting two part webinar on October 7 at 2:00 p.m. EST. Doug Sweet, of Doug Sweet and Associates, will present "Paper Machine Vacuum Systems 101." This free webinar will review some of the typical issues with the vacuum system including instrumentation and vacuum control, seal water systems, and cooling towers, flatboxes and uhle boxes, separators, and extraction pump and vacuum pump reliability. Doug is an engineer with more than 35 years of experience, and his presentations have been one of the highlights of past TAPPI papermaking conferences.
Additional information about the webinar and instructor is available at the course website.
Following Doug's presentation, a round table discussion with leading papermaking experts will be held. The distinguished panel includes: Gary Nyman, International Paper; John Neun, Albany International; and Dave Burton, Asten Johnson, all with more than 30 years of experience in the papermaking industry. This roundtable will be an open forum for any questions you have on papermaking topics. These experts can offer you sound solutions to any challenges you may be facing. You may register and submit a question for the panel by visiting the Papermakers Roundtable website.
The Papermakers and Water Removal committees are very active in planning program content for TAPPI's PaperCon conference being held next year in Nashville Tenn., USA, April 27-30. For more information visit www.papercon.org.
Back To Top
|
The 2014 conference co-chairs invite you to submit an abstract for a presentation at the 2014 TAPPI International Conference on Nanotechnology for Renewable Materials, June 23-26, 2014, at the Fairmont Hotel Vancouver in Vancouver, B.C., Canada.
Abstracts addressing the latest advances in characterization, functionalization, modeling, new products, applications, and health and safety issues of renewable and sustainable nanomaterials are sought. For the 2014 conference, abstracts focused on additive manufacturing, 3D printing, and other industrial manufacturing applications are preferred.
Abstracts are due November 5, 2013.
This year's conference features several opportunities for students to achieve recognition for their work.
View the Call for Abstracts to learn more.
Back To Top
|
The TAPPI Microbiology and Microbial Technology committee has announced the next webinar in its series on Microbes in Papermaking. "Microbial Control: Protecting Mineral Slurries and Papermaking Additives from Spoilage" will be held on October 16 at 12:00 p.m. EST. The webinar will be hosted by Sherrill Gammon, Sr. Research Scientist in the Microbiology Group of Kemira Chemicals, and will focus on the challenges presented when protecting additives in storage against the growth of ever changing microorganisms.
The preservation of mineral slurries and other additives for pulp and paper processes can be a challenge given the dynamic nature of the microorganisms, characteristics of individual biocides, and the chemistry of the products to be preserved. A review of microbial control in the world of white pigments and additives combining the tools of biocides, microbiology, monitoring, and housekeeping will be discussed to make the job of protecting these additives a little easier.
This webinar is offered at no charge. Additional details are available on the course website.
The Microbiology and Microbial Technology committee is an active committee and has produced a successful webinar series on this and other important topics. It also conducts presentations at TAPPI's PaperCon Conference being held next year in Nashville, Tenn., USA. April 27-30. For more information visit www.papercon.org.
Back To Top
|
TAPPI has created a new web based listserv environment for TAPPI staff, TAPPI members, and associated individuals to gather and share information on business topics that are important to them. This online community also allows for groups to be formed that are focused on a wide range of industry topics and depth of conversation.
What can you do in the TAPPI Community?
- Share ideas and collaborate on projects
- Distribute industry findings & news
- Manage TAPPI Committee projects
- Review meeting schedules for committees
- See the latest scheduled coursesand conference events on a community wide calendar
- And so much more...
Back To Top
|
Piping System Training is a course anyone in the piping system industry can use. This course provides real-world practical knowledge for junior engineers, is a good refresher course for senior engineers, and helps operations and maintenance supervisors, design and process engineers, and operators and maintenance personnel better understand how piping systems operate.
Attend Piping System Training courses planned for two locations coming this fall:
- October 2-3 in Chicago, IL
- October 23-24 in Houston, TX
This course provides the foundation of piping terminology, mathematics, and the underlying concepts and principles that determine the performance of individual piping system elements and the system as a whole. Piping System Training places an emphasis on understanding the relationship between components that make up the piping system.
Visit the course website to find more information and register.
Earn 1.6 CEUs and carry back with you two indispensable manuals as well as greater confidence in your work.
Back To Top
|
Calls for Papers have been issued for PaperCon 2014.
After a record attendance in 2013, PaperCon will again bring together CEOs, mill managers, superintendents, scientists, process engineers, and suppliers for the largest pulp and paper technical program in the world. The event will take place April 27-30, 2014, in Nashville, Tenn., USA. Learn more about PaperCon 2014.
For 2014, PaperCon is once again co-located with the Tissue360° Forum, NETInc (Innovative Nonwovens Conference), RPTA (Recycled Paperboard Technical Association) P-T Seminar, and the OpEx Reliability Workshop. Each of these events is open to full PaperCon registrants and papers in these areas are welcome.
Calls for Papers and Posters have been issued. The conference theme is In Tune for Stability, Agility, and Profitability, and authors are encouraged to include this within their papers.
Papermakers Program:
The Papermakers Program encourages topics on paper machine upgrades, product development, stability, agility, and fluid fundamentals, and recycled paperboard. The deadline for submission of abstracts is Nov. 10, 2013. Abstracts for panel discussions and roundtables are welcome. See Papermakers Program Call for Papers.
Coating and Graphic Arts Program:
The Coating and Graphic Arts Program will focus on The Future of Print and its Demands on Paper and Coatings. The deadline for extended abstracts for this program is October 16, 2013. See the Coating and Graphic Arts Program Call for Papers.
All abstracts must be submitted using TAPPI's Speaker Management System for consideration by the TAPPI and RPTA program committees.
Back To Top
|
TAPPI has announced it will be organizing another tissue program to be held at the PaperCon 2014 Conference, scheduled for April 27-30 in Nashville, Tenn., USA. The program will focus on technical advances in tissue making, converting, and on tissue education.
"We received fantastic feedback from our first Tissue360° Forum in Atlanta," says Larry Montague, president and CEO of TAPPI, "so we wanted to provide more of what tissue makers need. Several of our outstanding members have stepped up to organize another program this year."
The tissue market is growing globally, with private label growing faster than national brands. This is especially true in North America, where more than half of the new capacity has been structured sheet technology for private label customers. In Europe, dramatic new converting technologies have developed to improve tissue quality and performance. These trends are creating an increasing need for credible technical information and training.
TAPPI responded by organizing the first Tissue 360° Forum in April, 2013. The forum attracted a large crowd to its three-day program of peer-reviewed, non-commercial technical papers. The 2014 Tissue360° Forum will feature more of the same, with an emphasis on converting technologies and TAPPI courses for those who want to grow their knowledge of this dynamic segment. The editorial team from Tissue360° will assist TAPPI tissue experts in the development of the program content.
Tissue360° is TAPPI's semi-annual print and online publication for the tissue and converting industry. PaperCon is TAPPI's annual pulp and papermaking conference that attracts nearly 1,800 executives and technical professionals from around the world. It is the largest technical program in the world and the largest industry trade fair in North America.
Back To Top
|
TAPPI's problem-solving course designed for those working in industrial settings returns this fall.
Root Cause Problem Elimination Training
October 8-10 in Raleigh, N.C., USA.
This maintenance course is designed to show you how to cut to the core of problems - and eliminate them - by tying cause and effect together with logical thought processes and easy-to-grasp diagrams. You'll learn from case studies and predictive maintenance tools to better analyze root cause and repeat failures.
Back To Top
|
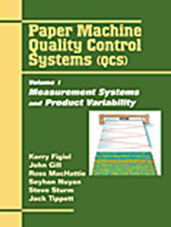 Paper Machine Quality Control Systems - Volume 1: Measurement Systems and Product Variability
By: The Quality Control Systems Education Common Interest Group of the Process Control Division of TAPPI.
Paper Machine Quality Control Systems - Volume 1: Measurement Systems and Product Variability describes in detail the measurement technology used in Quality Controls Systems (QCS). Individual chapters are devoted to the five most prevalent QCS measurements (basis weight, moisture, caliper, ash, and color) in the paper industry. Each of these chapters covers the physical principles involved in each measurement, sensor designs, various methods of implementation and influence factors.
A somewhat lighter coverage is given to10 other QCS measurements that do not have such a abroad installation base. Common issues that impact all sensors are explained, including how sensor performance is measured and reported, the impact of scanning process, filtering, scanner designs and construction, and sensor calibration and correlation. Statistical methods are covered in depth from discrete, one-dimensional variability to multi-dimensional variability. Guidance is provided for using these statistical methods to locate the sources of variability in the paper process.
This book was written by the Quality Control Systems Education Common Interest Group of the Process Control Division.
View the Table of Contents.
Also soon to be available in e-book format.
Product code: 0101R328
Member Price: $135.00
Non-Member Price: $205.00
(A percentage of the proceeds for the sale of this book go to the TAPPI Foundation.)
Back To Top
|
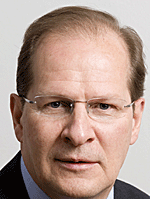 As a long-time executive with Stora Enso, and now the proprietor of Strategy First Ltd Oy, Asko Hyttinen has used nearly 20 years of TAPPI membership to fine tune his understanding of global behaviors specific to the pulp, paper, and packaging industry. He accomplished this over the years by attending numerous conferences and classes, networking with other members across North America and Europe, and through active participation on a number of TAPPI committees.
Having lived extensively on two continents, including four moves back and forth "across the pond," Asko is familiar with the need to educate oneself on new environments. He applies that understanding to the P&P world, noting he has a pertinent desire to develop the paper and forest products industry inside and outside of industrial companies. "Developing a unique global knowledge and understanding of industry behavior and success factors is key to that," he says.
Find out more by reading this month's Member Spotlight. Spotlight participants are recommended by fellow members and staff. If you would like to nominate a member just send their name (or names) to MemberSpotlight@tappi.org. We will forward a Spotlight Questionnaire for you to fill out and return.
We look forward to seeing you in the Spotlight!
Back To Top
|
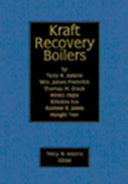 Kraft Recovery Boilers
By: T. N. Adams, W. J. Frederick, T. M. Grace, M. Hupa, K. Lisa, A. K. Jones, H. Tran
Kraft Recovery Boilers is a comprehensive textbook that covers recovery boilers in great depth and pulls together information on combustion, safety, emissions, plugging, and corrosion. The book also covers fundamental chemical and mechanical engineering principles that bear directly on black liquor and recovery boilers. It contains information about typical values and the normal range of important variables, plus many example calculations, data tables, and charts of relevant material properties or constants and conversion factors. Written by a team of industry experts, the text includes a great deal of practical information such as simple tests to pinpoint problems, important observations to help understand issues for particular operations, and "rules-of-thumb" that are generally used in the industry. This text was written as a project of AF&PA and published by TAPPI PRESS.
Preview table of contents.
Product code: 0102B064
Member Price: $93.00
Non-Member Price: $140.00
Back To Top
|
The Foundations of Leadership Excellence Course is the only leadership course specifically focused on the paper and packaging industry.
Foundations of Leadership Excellence explains the fundamentals of leadership and management skills for emerging leaders, high-potentials, area operating managers, and other technical professionals. This three-day session takes place Oct. 22 - 24, 2013, at the TAPPI Training Facility in Metro Atlanta, Ga., USA.
This course will sell out at 25 participants.
The instructors for this course have approximately 100 years of combined experience in leadership, management, and human resource roles within the pulp and paper industry.
Course curriculum covers industry specific, real-world scenarios. Participants will develop personal leadership skills through the use of influence. They will learn to impact organizations from a 360 degree perspective and how to address the challenges of team building, accountability, performance management, and other critical factors of organizational success.
Back To Top
|
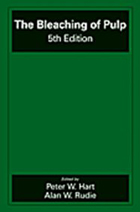 The Bleaching of Pulp
By: Peter W. Hart and Alan W. Rudie
Previous editions of The Bleaching of Pulp have provided comprehensive information on the technology used to bleach wood pulps. The 5th edition will continue this tradition as the premiere industry text on bleaching technologies but will be more focused on the modern industrial processes with less emphasis on fundamental science. New or more comprehensive sections are included on elemental chlorine free bleaching, enzymes, acid treatments for hexeneuronic acids, control of mineral scale, and multi-stage modeling as used to optimize bleaching among multiple stages.
Preview table of contents and sample pages.
Product code: 0101R331
Member Price: $155.00
Non-Member Price: $232.00
Back To Top
|
As TAPPI is getting ready to celebrate its 100th Year Anniversary in 2015, we were wondering how much industry expertise we have in this great group of professionals.
So, we decided to post a discussion question on our TAPPI Social Media outlets. We asked, "How many years of paper and/or packaging experience do you have?"
Who knew such a simple question would have such an impressive response.
With more than 7,000 TAPPI members, all over the world, we have counted 650-plus years of industry experience! And that's just counting the first 30 people who have responded. Now you probably can't find that anywhere else . So why don't you join us?
From those "born" into the industry to third generation professionals. From paper to packaging, to sustainability, environment, tissue, converters, and consulting. This TAPPI network has something for everyone.
Become a part of this unique community of paper and packaging professionals, and add your expertise to our group, and network with others to learn something new.
Visit our website to learn more today!
Back To Top
|
The TAPPI Centennial Celebration will be a multi-year long series of outreach events and educational offerings showcasing the proud history and promising future of the global pulp, paper, packaging, and related industries. This once-in-a-lifetime event will expand public awareness, foster further connection, and provide outstanding opportunities for collaboration, growth, and investment in our future for all of those involved. Goals for the TAPPI Centennial Celebration are:
- To honor TAPPI's 100 years of connection, education, and advancement as a foundation for the sustainable success of our members, our industries, and the world we share
- To recognize the achievements of those who built our industry and to inspire those who seek to build its future
- To celebrate the contributions and innovations of the global pulp, paper, and packaging industries to human culture, commerce, health, and social advancement
- To sustain the industry and support its growth, vitality, and future through the TAPPI Foundation.
We invite you to be a part of this momentous event. The sooner you join us the more opportunities there are for recognition of your company, its products, and key innovations. Keep in mind that an early commitment allows you to spread your investment over multiple years' budgets.
For more information on sponsorship and volunteer opportunities please contact dbell@tappi.org.
The sponsorship prospectus can be downloaded online.
Back To Top
|
Do you have a history book gathering dust on your shelf? TAPPI's 100th year is coming soon and we are looking for donations to the TAPPI Library. Specifically, we are interested in histories of companies and mills in the paper and packaging industry (both producers and suppliers). Each donated book will have a bookplate in the front cover recognizing the donor. For more information please contact David Bell.
Please send books to:
c\o David Bell
TAPPI
15 Technology Parkway, South
Suite 115
Peachtree Corners, Georgia 30092
Back To Top
|
|
|
TAPPI Over the Wire | 15 Technology Pkwy. S. | Norcross, GA 30092 USA | Voice: 770.446.1400 | Fax: 770.446.6947
|
 |