 |
|
Weekly Spotlight
Research and Markets, Dublin, Ireland, this week added the Supplier Relations US, Irvine, Calif., USA, new report Pulp Mills Industry in the U.S. and its International Trade (2013 Q2 Edition) to its offering
Learn More...
|
Domtar Corp., Montreal, Que., Canada, together with U.S. Federal and State of North Carolina officials, are inviting the media to attend a press event to mark the inauguration of a commercial-scale lignin separation plant at its Plymouth, N.C., mill
Learn More...
|
The Catalyst Paper mill in Port Alberni, B.C., Canada, foresees a labor shortage looming on the horizon
Learn More...
|
Ilim Group, St Petersburg, Russia, this week reported that Paul Herbert's contract as CEO of the company, which is jointly owned by International Paper, Memphis, Tenn., USA, will end this June 30
Learn More...
|
TAPPI has reserved exhibit space in the prestigious China International Paper Expo and Conference (CIPTE) to be held Sept. 23-25, 2013, in the National Agriculture Exhibition Center (New Hall), Beijing
Learn More...
|
The U.S. Postal Service Office, Denver, Col., USA, is seeking sources interested in and capable of providing paper and/or envelope products
Learn More...
|
U.S. consumers continue to go green, with 78% saying they buy green products and services, a steady increase from 69% last year
Learn More...
|
Market Roundup
The following are excerpted sections from current issues of Wood Resources Quarterly (WRQ), which is published by Wood Resources International, Seattle, Wash., USA.
Learn More...
|
Total U.S. boxboard production increased by 1.7% compared with April 2012 and increased 2% from last month
Learn More...
|
Pulp & Paper
Asia Pulp and Paper (APP), Jakarta, Indonesia, this week issued a report on progress, which is the third report in relation to its June 2012 Sustainability Roadmap
Learn More...
|
Cosmo Specialty Fibers Inc., Cosmopolis, Wash., USA, an affiliate of The Gores Group, which produces 140,000 tpy of a full range of dissolving pulp products including viscose, ethers, and acetates, this week announced the appointment of Central National-Gottesman Inc. (CNG), New York, N.Y., as Cosmo's exclusive worldwide sales and marketing representative
Learn More...
|
Domtar Corp., Montreal, Que., Canada, this week completed its acquisition of Xerox's paper and print media products business in the U.S. and Canada, as agreed to this past March 21
Learn More...
|
Metso, Finland, this past week approved a demerger plan to transfer all of the assets, debts, and liabilities of its Pulp, Paper, and Power businesses to a newly-formed company that will be named Valmet Corp
Learn More...
|
Georgia-Pacific, Atlanta, Ga., USA, this week announced that an entity controlled by Georgia-Pacific, GP Cellulose Group LLC, has extended the expiration of its previously announced tender offer for all of the outstanding shares of common stock of Buckeye Technologies Inc., Memphis, Tenn
Learn More...
|
PaperlinX Limited, Australia, this week reported that its Danish operations, PaperlinX CC&Co, has acquired Cadorit AB, Sweden, for A$1.1 million
Learn More...
|
Sappi Fine Paper North America, Boston, Mass., USA, this week announced that it is a recipient of IDG's CIO magazine (Framingham, Mass., USA) 2013 CIO 100 award
Learn More...
|
Japanese general heavy equipment manufacturer IHI Corp. and Voith Paper, Germany, have founded Voith IHI EcoSolutions GmbH & Co.
Learn More...
|
Containerboard/Packaging
Iggesund Paperboard, Sweden, reports that its new biofuel boiler is ready for operation in Workington, England, at a cost of 108 million pounds
Learn More...
|
Stora Enso, Finland, and Packages Ltd., Pakistan, have completed the process of establishing a joint venture called Bulleh Shah Packaging (Private) Limited, as announced last September
Learn More...
|
The U.S. paperboard industry's revenue for the year 2012 was reported at $29.3 billion, with an estimated gross profit of 37.53%
Learn More...
|
|
New Products
Clariant, Muttenz, Switzerland, this week launched the world's most highly-concentrated, urea-free liquid optical brightening agent (OBA) for printing and writing papers
Learn More...
|
Iggesund Paperboard, Sweden, is advising customers to expect an upgrading of its folding box board Incada
Learn More...
|
Twin Rivers Paper Company, South Portland, Maine, USA, a producer of lightweight specialty packaging, label, and publishing papers, has released an optimal packaging paper for dry and wet wax applications
Learn More...
|
Published Pricing
DuPont, Wilmington, Del., USA, this week announced that it will increase prices on all of its titanium dioxide products sold in North America, Europe, the Middle East, Africa, Latin America, and the Asia Pacific regions effective July 1
Learn More...
|
Lecta, the second largest European coated woodfree paper-manufacturing group, made up of Condat, Cartiere del Garda, and Torraspapel, has announced a price increase for its one- and two-side CWF (coated woodfree) papers
Learn More...
|
People
Fortress Paper Ltd., Vancouver, B.C., Canada, reports the election of five directors at its annual general and special meeting of shareholders last month
Learn More...
|
Georgia-Pacific Paper Chemicals, Atlanta, Ga., USA, has named Mark Zempel North American Sales Manager
Learn More...
|
Metso, Finland, has appointed Pasi Laine, M.Sc in Engineering, president and CEO of the new company to be demerged from Metso Corp. and named Valmet Corp. (see article in Pulp & Paper section above)
Learn More...
|
Stora Enso Group, Finland, has appointed Treasurer Jyrki Tammivuori acting CFO, effective July 1
Learn More...
|
Travels with Larry
Based in Atlanta, Ga., USA, American Process Inc. (API) was founded by Theodora Retsina, CEO, in 1994, as a consulting practice serving the forest products industry
Learn More...
|
TAPPI News
TAPPISAFE is proud to sponsor the PPSA 70th Annual Safety and Health Conference June 9-12 in Williamsburg, Va., USA.
Learn More...
|
This PAPTAC course can help you develop bioenergy strategies, better understand emerging technologies, strategic implementation.
Learn More...
|
This course is ideal for engineers and other technical people who need a better understanding of wet end chemistry. The course is designed for anyone that is involved with wet end operations as well as anyone training staff working in this area.
Learn More...
|
All proceeds from this tournament support the Northeast PIMA /TAPPI Scholarship Fund. Register ASAP as spots fill quickly. We accept checks and all major credit cards.
Learn More...
|
This one-hour webinar on June 19 will cover various methods of operator training.
Learn More...
|
TAPPI member Jim Atkins suggests we embrace change to be a success.
Learn More...
|
Join more than 7,000 TAPPI members across the world with 650-plus years of industry experience.
Learn More...
|
This year's kick-off Golf Outing is being held at Mid-Vallee Country Club in De Pere, Wis. An afternoon shotgun scramble golf outing is planned with dinner to follow. Prizes will be awarded and individual pin events will be held.
Learn More...
|
Helmut Stark became a member of TAPPI in 1981 and was recognized as a TAPPI Fellow in 1997. He was a presenter at multiple TAPPI conferences and workshops and authored or co-authored numerous books, articles, and technical papers for the industry.
Learn More...
|
Don't miss your chance to attend this popular course at the TAPPI Training Center in Peachtree Corners, Ga., USA, which sold out last year.
Learn More...
|
The 8th Annual International Conference on Nanotechnology for Renewable Materials is scheduled for June 24-27, 2013, in Stockholm, Sweden, at the KTH Royal Institute of Stockholm.
Learn More...
|
TAPPI Press features new titles coming to print and new e-books.
Learn More...
|
PPMA has launched its first ever Best Place to Work Award, which is open to all companies in the forest products industry and will look not only at corporate life but also at how employees feel about their work environments. .
Learn More...
|
Learn how to enhance your Operator Training Program from some of the leading experts in the Industry.
Learn More...
|
Nominations for the major TAPPI 2014 awards are due by August 1, 2013.
Learn More...
|
This course, August 5-6, is efficiently and expertly planned and taught by one of the world's most recognized educators in the pulp and paper industry, Dr. Michael Kocurek, Emeritus Professor, North Carolina State University.
Learn More...
|
With only 25 seats left, register now to reserve your spot.
Learn More...
|
TAPPI's 2013 CorrExpo will be held in Indianapolis, Ind., USA, October 7-9, 2013.
Learn More...
|
This once-in-a-lifetime event will expand public awareness, foster further connection, and provide outstanding opportunities for collaboration, growth, and investment in our future for all of those involved.
Learn More...
|
As TAPPI's 100th year approaches, we are looking for donations to the TAPPI Library.
Learn More...
|
Register now for the class where you will learn to understand OSHA, avoiding citations that could cost millions of dollars. Teach your company how to lower fatalities and near-misses.
Learn More...
|
|
Find us on Facebook
Network with us on LinkedIn
Follow us on Twitter
|
Weekly Spotlight
Research and Markets, Dublin, Ireland, this week added the Supplier Relations US, Irvine, Calif., USA, new report Pulp Mills Industry in the U.S. and its International Trade (2013 Q2 Edition) to its offering. The 161-page report includes the most recent information on the domestic market, global market, and overseas growth opportunities.
The new report also provides the most current data available, such as shipments, inventory, and trade data through March 2013, and forecasts up to 2017 accounting for the affects of the recent economic recession.
The industry's revenue for the year 2012 was reported at $5.2 billion, with an estimated gross profit of 33.6%. Import was valued at $3.2 billion from 24 countries. The industry also exported $6.0 billion worth of merchandise to 125 countries. Adding import value to and subtracting export value from the industry's shipment value, the total domestic demand for the industry in 2012 was $2.4 billion.
More information about the new report is available online.
Back To Top
|
Domtar Corp., Montreal, Que., Canada, together with U.S. Federal and State of North Carolina officials, are inviting the media to attend a press event to mark the inauguration of a commercial-scale lignin separation plant at its Plymouth, N.C., mill—the first U.S. facility of its type in more than 25 years. Officials scheduled to be at the event on Friday, June 7, 8:30 a.m. to 1 p.m. ET include: Tom Vilsack, secretary, U.S. Department of Agriculture; G.K. Butterfield, U.S. House of Representatives; John D. Williams, president and CEO of Domtar; Michael Edwards, SVP, Pulp & Paper Manufacturing, Domtar; and Dennis Askew, VP and mill manager, Domtar.
The ceremonies will include a tour of the lignin separation plant, presentations on the commercial applications of lignin from federal officials and Domtar leaders, and a panel discussion with industry experts and customers. The production of Domtar's BioChoice™ lignin provides a bio-based alternative to the use of petroleum and other fossil fuels across a wide range of applications. This includes adhesives, agricultural chemicals, carbon products, coatings, dispersants, fuels and fuel additives, natural binders, resins, and thermoplastics.
Lignin is a fundamental building block of wood fiber historically underutilized in the pulp manufacturing process. With rising energy prices, the economics of petroleum-based substrates in the making of consumer goods are shifting. This provides tremendous business opportunities for plant-based materials, Domtar notes.
The press event will help explain the technology and its market applications, as well as the potential to secure jobs in rural communities by leveraging an abundant, underused, renewable material.
Interested media should contact Stefan Nowicki, manager, communications and government relations, Domtar Corp., at 803-802-8099 x68099.
Back To Top
|
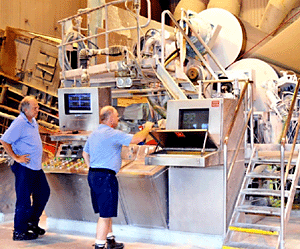 The Catalyst Paper mill in Port Alberni, B.C., Canada, foresees a labor shortage looming on the horizon. Fred Chinn, general manager at the mill, said in an Alberni Valley Times article this past week that the company and mill are coming out the other side of their bankruptcy issues and will be stronger than ever, but first they have to figure out how to replace the skilled employees who are retiring on a regular basis from the Port Alberni operation.
"We have to educate people on the possibilities," Chinn explained. "There are lots of jobs here that people don't even know about." He said that in the past 18 months the paper mill has hired 60 workers, most of those to replace retiring employees.
Chinn further noted in the article that when the layoffs hit in the 1990s, many of the younger workers were the first to go because they did not have enough seniority to keep their jobs. That left the mill with a workforce that consisted of mostly men of similar ages and experience levels. Now, a lot of those employees have put in more than 30 years with the company, and they are ready to retire.
Catalyst is now having a difficult time attracting young skilled workers. "We are trying to encourage youth to chase jobs that are available here," Chinn said. "It allows them to stay in the Valley."
But the lure of high-paying positions in Alberta is hard to compete with, especially after coming out of the financial challenges Catalyst has faced in the past couple of years. But some people, the article noted, see the opportunity that lies within their hometown.
Richard Martell, for example, was hired at the paper mill a year ago. He had worked in the paper industry before, but most recently was commuting over the Hump to work in health care. Working on the paper machine at Catalyst means he can stay close to his family."For me it's about family," he said. "I want to be close to them. It's a lifestyle choice, and I want to be here." He said that opportunities have come up in the past in Alberta, and he can understand the temptation of the money that can be made in camp-style jobs. But he said it always came back to priorities. His is being close to his wife and children.
In about a month, the article continues, Richard Van Herwaarden, will retire from a career that has challenged him for more than three decades. He is a maintenance carpenter, and he said the company offered him a great career, one he would recommend to anyone. But he has also seen a lot change in his time at the mill. "When I first started in the trades in 1980 it was like a small city here," he said. "There were tradesmen everywhere. People made their careers here after the war. The workload has decreased, but we need people here, and it will always offer a fulfilling career."
Van Herwaarden said the mill employed approximately 1,500 people back then, a number that has shrunk to around 340 in recent years.
Finding a way to attract workers is one of the most challenging aspects of Chinn's job. He said it is important that people understand the mill might not offer as many jobs as it once did, but there are still lots of opportunities. One way to attract young workers is to host an open house for educators. In the near future, they hope to invite staff from the high school in to tour the mill and learn what opportunities exist in Port Alberni. He said more people have to consider the trades as a great option. One way they can promote that is by offering more opportunities for apprenticing at the mill.
The Port Alberni mill operates two paper machines with a total capacity of 340,000 metric tpy, split between coated papers (224,000 metric tpy) and directory paper (116,000 metric tpy). In the photo, Gary Knutson (l) and David Best monitor paper machine coater operations at the mill.
Back To Top
|
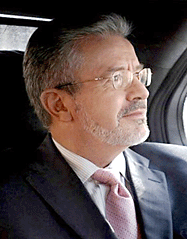 Ilim Group, St Petersburg, Russia, this week reported that Paul Herbert's contract as CEO of the company, which is jointly owned by International Paper, Memphis, Tenn., USA, will end this June 30. Herbert has been serving as CEO of the Ilim Group for six years.
Ilim Group Chairman Zakhar Smushkin expressed gratitude to Herbert for the contribution he has made to the growth and success of Ilim Group. "Paul has managed to build an atmosphere of trust and mutual understanding between Russian shareholders and the shareholders of International Paper. In six years, the company under Paul's leadership reached strategic goals set out at the start of the joint venture, and is completing the largest investment program in the industry of more than $1.5 billion. From the whole Ilim Group, I want to thank Paul and wish him continued success."
IP Chairman and CEO John Faraci said that "Paul will leave a lasting legacy on the people and companies he has worked with throughout his 47-year career in the industry. He spent 21 years with IP with his last six years at IP/Ilim in Russia. His work spans almost every continent—in places like Canada, Chile, Brazil, U.S., Belgium, Germany, Spain, France, China, India, and Russia. The breadth and depth of his global experience is unmatched in the industry. We thank Paul for his many significant contributions and wish him the best in the years ahead."
Franz Joseph Marx has been nominated as the candidate for next CEO of Ilim Group. Franz is currently president of International Paper, Russia. Prior to joining IP, he was partner and managing director at the Boston Consulting Group. Franz began his professional career with BASF and has worked throughout Europe, China, Middle East, and Africa.
"Franz has a diversified international experience. He knows Russia and our industry very well. We hope that he will be able to apply all of his experience gained in the world's leading companies and International Paper, Russia in the new broader role," Smushkin said.
Faraci added that "Franz has achieved solid results and demonstrated his strong leadership since he joined IP in 2008. He led the IP Russia team to a record financial performance last year and delivered six consecutive record quarters. His extensive experience in the region makes him the right fit for this important leadership position at Ilim."
Back To Top
|
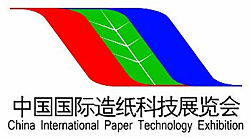 TAPPI has reserved exhibit space in the prestigious China International Paper Expo and Conference (CIPTE) to be held Sept. 23-25, 2013, in the National Agriculture Exhibition Center (New Hall), Beijing. The Expo is attended by more than 6,000 highly qualified buyers, mill employees, and others from China and around the world. Space is very affordable ($1,450 for a 36 m2 booth), but limited.
The goal of this conference is to:
- Promote the development of China's paper industry
- Display technical achievements of the paper industry
- Provide a communication platform for the enterprises of paper and relative industries.
This exhibit is attended by pulp and paper professionals from across China and the Pacific Rim. If you are interested, you must book your booth by July 1.
More information is available online.
Back To Top
|
The U.S. Postal Service Office, Denver, Col., USA, is seeking sources interested in and capable of providing paper and/or envelope products. This is not a solicitation, USPS emphasizes, noting that there is no Request for Proposal (RFP) or Solicitation to download, and no contract will be awarded from this announcement.
Interested suppliers will be required to demonstrate recent, specialized experience and technical competence in relation to the supply of paper and/or envelope products. Interested suppliers should furnish the following information:
- Provide company name, address, telephone number, and email address.
- State size status—Other than Small (OTS), Small Business (SB), Small Disadvantaged Business (SDB) to include Section 8(a) participants, Woman Owned Small Business (WOSB), Historically Utilized Business Zone (Hubzone), Service Disabled Veteran Owned Small Business (SDVOSM), Veteran Owned Small Business (VOSB), Historical Black Colleges and Minority Concerns (HBCU/MI), Indian organizations and Indian-Owned economic enterprises.
- Provide no more than three references for no more than three of the most recent and relevant contracts performed within the past three years. Include name, address, telephone number, and email address of references. Also, provide a brief description of the work performed, role of the paper or envelopes to include whether the work was self-performed or subcontracted out, total contract value, and period of performance.
There is one subcontracting limitation in regard to this announcement: the prime contractor is required to perform at least 50% of the labor with its own employees.
Email responses to this request for information are preferred, and should be sent to John Q. Bennett. All questions also must be submitted via email. The due date and time for responses to this announcement is Thursday, June 6, at 12:00 p.m. Mountain Time. Failure to comply with the establish time will disqualify potential suppliers for consideration. Responses should be limited to no more than 10 pages. Do not submit product literature
When responding via email, in the subject line put the following: Paper and Envelope Product Initiative.
The prequalification of suppliers is scheduled for completion by early September and the RFP is scheduled for release before the end of September. The prequalification as well as the RFP source selection process will be conducted using the USPS eSourcing system, Emptoris eRFx module.
Emptoris is an eSourcing solution that automates, standardizes, and streamlines the sourcing of supplies, services, equipment, transportation, and facilities. All suppliers interested in doing business with the USPS must register in Emptoris. Suppliers can access the eRFx registration module online. Simply click on the "Register Supplier Organization" hyperlink, and follow the instructions and prompts to complete the registration process. You will need a DUNS (Dun & Bradstreet) number and NAICS (North American Industry Classification System) code to register in the USPS sourcing system.
No reimbursement will be made for any costs associated with providing information in response to this announcement or any follow-up information requests. The purpose of this announcement is to gain knowledge of capabilities and qualifications of interested contractors. Responders must be able to pass security checks, have insurance, and meet other regulations requiring access to government installations.
Back To Top
|
U.S. consumers continue to go green, with 78% saying they buy green products and services, a steady increase from 69% last year, according to the Fifth Annual Tork Sustainability Study. The study was conducted by Harris Interactive on behalf of SCA, Philadelphia, Pa., USA, makers of the Tork® brand of away-from-home tissue products.
Why people are buying green products appears to be shifting, as more consumers say they buy green products because they are better for their health. This year, 20% of consumers cited health reasons as why they bought green products, up from 14% last year. That percentage increases to 26% for adults between 18 and 44 years old. Those who say they buy green products because it's better for the environment are virtually unchanged, at 47% this year, compared with 48% last year.
The sustainability survey was conducted online by Harris Interactive in May 2013 among 2,068 U.S. adults aged 18 and over. It also shows that Americans are split when it comes to paying more for products if they could be guaranteed of ethical and responsible manufacturing practices. According to the survey, 43% of Americans said they would pay more, while 44% said they would not.
The survey found that having children under the age of 18 in the household has a significant impact on consumer decisions. More adults with children in their household (78%) say they know how to determine if green claims and statements are true compared with 72% without children. Also, adults with children in the house are significantly more likely to pay more for responsible and ethically sourced products (51%) than those without children (39%).
"People are paying more attention to health when choosing to buy green, and I believe that adults are more aware when children are in the house. It suggests this trend will continue as future consumers are being raised with these values," said Mike Kapalko, Sustainability Marketing Manager for SCA's North American away-from-home professional hygiene business. "While this survey shows Americans are split on the idea of paying more for ethically and responsibly manufactured products, a recent USA Today article stated that nine of ten Americans will boycott companies that engage in irresponsible business practices. It's not a matter of paying more, but willingness to pay at all. Clearly there is a case for companies needing to be green, be good, or be gone."
SCA chose to release the results of the survey this past Wednesday (June 5) to recognize World Environment Day, a United Nations observance of environmental issues.
Back To Top
|
Market Roundup
The following are excerpted sections from current issues of Wood Resources Quarterly (WRQ), which is published by Wood Resources International, Seattle, Wash., USA.
Global Timber Markets
Sawlog prices in the 1Q/13 were up in practically all regions covered by the WRQ, but they were still generally lower than they were in the 1Q/12. The biggest increases from the previous quarter occurred in the Western U.S., Latvia, Finland, and Sweden. The Global Sawlog Price Index (GSPI) was up 2.4% to $86.33/cubic meter from the 4Q/12, the biggest quarter-to-quarter increase since early 2011.
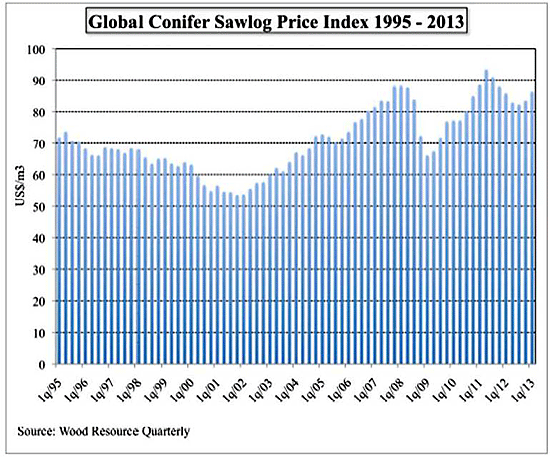
Global Pulpwood Prices
Wood fiber prices were generally down in North America and up in the rest of the world during the 1Q/13. The Softwood Wood Fiber Price Index (SFPI) in the 1Q/13 was practically unchanged at $99.90/odmt from the 4Q/12. The SFPI has inched downward for seven consecutive quarters and is currently down 8.8% from the most recent peak in 2Q/11. The biggest changes in U.S. dollar terms in the 1Q/13 were the declines in chip prices in Eastern Canada (-12.4%), Japan (-8.6%), Western Canada (-7.8%), and the U.S. Northwest (-4.2%). The biggest increases came in France (+10%) and Germany (+6.9%).
Hardwood fiber prices were down in Asia and Eastern Canada in the 1Q, while they were slightly higher in Europe and Latin America compared with the 4Q/12. The Hardwood Wood Fiber Price Index (HFPI) fell by 1.1% to $103.66/odmt in the 1Q/13, and was 12% below the all-time high in the 3Q/11.
Global Pulp Markets
Global production of market pulp was 2.7% higher the first two months of this year than for the same period in 2012. Prices for NBSK (northern bleached softwood kraft) pulp have trended upward for six months and were in April about $845/metric ton in Europe. BHKP (bleached hardwood kraft pulp) prices have moved up at about the same rate.
Global Biomass Markets
The wood pellet export industry in North America has grown exponentially in a relatively short period of time. The export value has increased from an estimated $40 million in 2004 to almost $400 million in 2012. Pellet prices were close to, or at, record-high levels in all of the major markets in Europe in the 1Q/13.
More information is available online.
Back To Top
|
Total U.S. boxboard production increased by 1.7% compared with April 2012 and increased 2% from last month, according to the AF&PA (Washington, D.C., USA) April 2013 U.S. Paperboard Report released this week. Unbleached kraft boxboard production decreased over the same month last year but increased compared with last month.
Total solid bleached boxboard and liner production increased compared with April 2012 and increased compared with last month. The production of recycled boxboard increased compared with April 2012 but decreased when compared with last month.
Back To Top
|
Pulp & Paper
Asia Pulp and Paper (APP), Jakarta, Indonesia, this week issued a report on progress, which is the third report in relation to its June 2012 Sustainability Roadmap. This week's report comes 12 weeks after the company's announcement to end deforestation across its entire supply chain. The latest report includes a new online monitoring dashboard that shares key implementation data on the ground.
Key highlights of the report include:
- By August 31, 2013, APP pulp mills will stop receiving natural forest wood or mixed tropical hardwood (MTH) felled prior to the no deforestation commitment announced this past February. APP says that it welcomes the involvement of NGOs in the monitoring of this process, as part of the Independent Observer program.
- The introduction of a pilot version of The Forest Trust's (TFT) online monitoring dashboard allows interested parties to access up-to-date technical information relating to the assessments. The dashboard will enable stakeholders to review progress on the ground and to see boundary maps, High Carbon Stock (HCS), and High Conservation Value (HCV) progress and FCP protocols. The dashboard can be viewed online.
- HCS assessments are currently taking place and are designed to test the amount of carbon the forests contain as well as how valuable they are to ecosystems and communities in the area.
- HCV assessments are also underway for all 38 APP suppliers in Indonesia, with the completed first stage of 11 concessions due in September 2013 and the second stage of 27 concessions due in April 2014. TFT and APP technical teams have completed analysis of satellite data as part of the HCS study and have formed an on-the-ground field verification team.
- APP says that it continues to encourage broad NGO and civil society engagement in the monitoring of the implementation of its FCP. Transparency is vital, the company adds, noting that as it is working with vast areas of land where social conflicts are prevalent, the task is challenging and it welcomes the engagement of NGOs and other stakeholders.
Back To Top
|
Cosmo Specialty Fibers Inc., Cosmopolis, Wash., USA, an affiliate of The Gores Group, which produces 140,000 tpy of a full range of dissolving pulp products including viscose, ethers, and acetates, this week announced the appointment of Central National-Gottesman Inc. (CNG), New York, N.Y., as Cosmo's exclusive worldwide sales and marketing representative. CNG will provide Cosmo with a range of services, including sales and marketing representation through its network of international offices. CNG will also assume responsibility for trade services functions, including logistics, documentation, and customer service.
"CNG's global sales resources, and its logistics and customer service platform will allow us to penetrate new markets, improve operating efficiencies, and deliver the best possible customer service," said Michael Entz, CEO of Cosmo. "CNG has an impressive set of capabilities and resources that provide a natural fit for Cosmo. We are excited about the partnership and all of the opportunities that it will provide."
Warren Pullen, SVP, Global Pulp Group of CNG, added that "Cosmo has long been known for the superior performance of its western hemlock dissolving pulps. Mike has assembled an impressive team of professionals, and we see already that there is an excellent fit between our two organizations. Together, we have committed to providing our customers with the highest-quality specialty cellulose and the utmost in service and reliability."
Founded in 1886, Central National-Gottesman is an international marketer of pulp and paper. The company sells more than 4 million tons of product annually through sales offices in 28 U.S. cities and 23 countries worldwide.
Back To Top
|
Domtar Corp., Montreal, Que., Canada, this week completed its acquisition of Xerox's paper and print media products business in the U.S. and Canada, as agreed to this past March 21. The transaction includes a broad range of coated and uncoated papers and specialty print media including business forms, carbonless, and wide-format paper formerly distributed by Xerox.
The addition of a globally-recognized brand to Domtar's existing portfolio of paper products will allow Domtar to better serve its customers, the company notes. More information about the Xerox paper and print media portfolio of products is available online.
Back To Top
|
Metso, Finland, this past week approved a demerger plan to transfer all of the assets, debts, and liabilities of its Pulp, Paper, and Power businesses to a newly-formed company that will be named Valmet Corp. An application will be made to list the shares of Valmet on the NASDAQ OMX Helsinki stock exchange. In relaed action, the company also appointed Pasi Laine president and CEO of the new company ( see article in the People section below).
Following the demerger, Metso's current Mining and Construction and Automation businesses would remain in the current company, which would continue to operate under the Metso name. Valmet would initially have the same ownership structure as Metso and would be totally independent without any cross-ownership between Metso and Valmet.
The demerger will require the approval of an extraordinary general meeting of Metso and the registration of the completion of the demerger with the Finnish Trade Register following the creditor hearing process pursuant to the Finnish Companies Act. If approved, the planned registration date of the completion of the demerger is December 31, and public trading in new Valmet shares on NASDAQ OMX Helsinki is expected to commence as soon as possible thereafter.
Jukka Viinanen, Metso's chairman of the board, says that the company's board recommends that shareholders approve the demerger. "After carefully reviewing various alternatives that would accelerate the implementation of Metso's strategy and its growth, the board has concluded that spinning off Metso's Pulp, Paper and Power businesses through a demerger offers the best potential to increase the focus and ambition of Valmet and Metso and the implementation of their respective distinct growth strategies. The board believes that this, together with the creation of two attractive investment alternatives, would also create strong potential to increase value for Metso's shareholders."
Matti Kähkönen, Metso's president and CEO, adds that "as a long-standing Metso employee, I am proud that our Pulp, Paper and Power businesses have developed into a strong globally leading company over the past decade and are now ready to take their next steps as an independent company. The Valmet name reflects the long heritage of these businesses and symbolizes their exceptional engineering achievements. Based on preliminary feedback, I am convinced that both our customers and our personnel—in the Pulp, Paper and Power businesses and in the Mining and Construction and Automation businesses—would benefit from the independent governance and strategy that two separate companies would offer. Both Valmet and Metso would be sizeable, globally leading businesses with strong balance sheets. Strengthening their respective cultures, goals, and agility to execute their strategy through a demerger would enable them to realize their full potential in the future."
Metso plans to hold an extraordinary general meeting on or about October 1 to decide on the demerger and other board proposals based on the demerger plan.
Back To Top
|
Georgia-Pacific, Atlanta, Ga., USA, this week announced that an entity controlled by Georgia-Pacific, GP Cellulose Group LLC, has extended the expiration of its previously announced tender offer for all of the outstanding shares of common stock of Buckeye Technologies Inc., Memphis, Tenn., at $37.50 per share, net to the holder in cash, to 5:00 p.m., New York, N.Y. (Eastern) time on Monday, June 17, 2013, unless further extended.
The depositary for the tender offer has advised Georgia-Pacific that approximately 32,095,420 shares have been validly tendered and not properly withdrawn in the offer. This represents approximately 80% of the 40,127,758 shares of Buckeye Technologies' common stock issued and outstanding, on a fully-diluted basis, as of June 4.
The tender offer and withdrawal rights were previously scheduled to expire at midnight New York City time on June 4.
Back To Top
|
PaperlinX Limited, Australia, this week reported that its Danish operations, PaperlinX CC&Co, has acquired Cadorit AB, Sweden, for A$1.1 million. Cadorit is based in Borås (southwest Sweden) and specializes in digital solutions for the sign and print industry. It has annual revenues of approximately A$3.2 million. The purchase price represents an EBIT multiple (pre-synergies) of approximately five times the 2012 earnings of the acquired business.
PaperlinX CEO Dave Allen noted that "the acquisition of Cadorit is consistent with the group strategy of expanding our revenue streams beyond our traditional commercial print offering via organic growth and/or complementary bolt-on acquisitions. We are extremely excited about the opportunity that this acquisition brings to PaperlinX as it will provide a platform to becoming a leading supplier of visual technology and packaging solutions in this region."
The acquisition was completed on June 1 and was funded out of the local credit facilities of PaperlinX CC.
Back To Top
|
Sappi Fine Paper North America, Boston, Mass., USA, this week announced that it is a recipient of IDG's CIO magazine (Framingham, Mass., USA) 2013 CIO 100 award. The 26th annual award program recognizes Sappi's Ringer Detection System project at the Somerset Mill for exemplifying the highest level of operational and strategic excellence in information technology (IT).
Sappi's Ringer Detection System project utilizes an innovative smart camera technology that minimizes costly downtime on paper machines by detecting defects that can occur during the production of coated paper. On an annual basis, the impact to yield by minimizing roll failures is equivalent to $1.5 million.
"This award is really an acknowledgement of the entire cross-functional team at the Somerset Mill," said Anne Ayer, VP of corporate development and CIO, Sappi Fine Paper North America. "I am impressed by the collaborative efforts of the team to creatively develop a state-of-the-art solution that directly contributes to the bottom line of the mill and the company. This is also a reflection of the broader Sappi IT team objectives to work closely with our business partners to drive valuable innovations."
Executives from the winning companies will be recognized at the CIO 100 Symposium and Awards Ceremony, to be held Tuesday evening, August 13, at The Broadmoor in Colorado Springs, Colo.
Back To Top
|
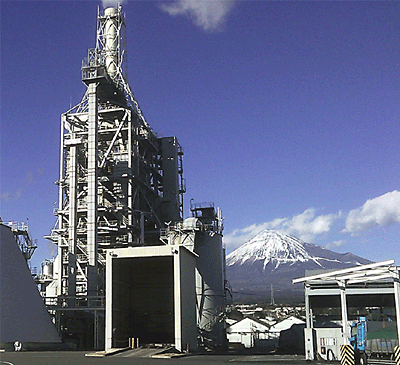 Japanese general heavy equipment manufacturer IHI Corp. and Voith Paper, Germany, have founded Voith IHI EcoSolutions GmbH & Co. The joint venture, in which Voith and IHI each hold a 50% interest, is being technically managed by Voith Paper and will be headquartered in Heidenheim, Germany.
The joint venture provides complete thermal fluidized bed power plants especially for the paper industry. They facilitate an effective and environmentally friendly combustion of solid waste materials, which also generates electrical energy and steam, Voith notes.
Stationary and circulating fluidized bed technologies are part of the joint venture. The big advantage of these combustion technologies, according to Voith, is that only small amounts of emissions are generated by the process of energy production. Fluidized bed power plants thus facilitate adherence to the strictest guidelines for environmental protection. Also, Voith adds, this type of power plant is extremely efficient in operation, while the waste materials that come about in paper production can be optimally utilized for thermal power generation.
The new joint venture further expands Voith Paper's expertise in combustion technologies and offers its customers value-enhancing recycling systems with the use of fluidized bed technology. Voith already has an offer in this market with its CTC (controlled thermal conversion) technology. The use of CTC means that the paper sludge that accumulates in the preparation of recovered paper can be converted into reactive minerals. In addition, Voith IHI EcoSolutions now supports paper producers with completely integrated combustion solutions that are tested and further developed in IHI's own development center.
Back To Top
|
Containerboard/Packaging
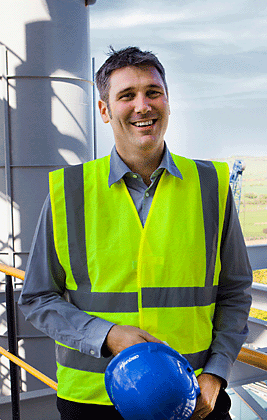 Iggesund Paperboard, Sweden, reports that its new biofuel boiler is ready for operation in Workington, England, at a cost of 108 million pounds. The purpose is to supply the mill's entire energy requirements with self-produced energy in the form of steam and electricity.
Many nearby residents, the company notes, have seen the new structure being built on the mill site but so far few have realized that Iggesund's investment will also create a sustainable long-term market for biofuel in the local county of Cumbria. Iggesund will need 500,000 metric ton of combustible material annually. As a result, the company has launched a campaign to interest local farmers in cultivating energy forest in the form of willow.
"We've developed a package of measures that includes technical advice, financial support for the transition, and a harvesting and transport service, all based on long-term contracts," explains Ulf Lofgren (see photo), financial director and a member of the team who developed the offer, which was launched under the name of "Grow Your Income".
Britain's environment department, Defra, has identified large parts of Cumbria as being highly suitable for the cultivation of energy crops. The new market for these crops should be considerably larger than just Iggesund's requirements, as it is widely expected that energy produced from fossil sources like coal and oil will become far more expensive in the future.
Iggesund's investment is not due to any immediate need. The new boiler's fuel supply is already ensured for several years to come. However, it does take three years for newly planted willow seedlings to produce their first crop.
Already this spring, Iggesund has planted its own willow crop on about 10 hectares close to the mill for demonstration purposes. The company has also launched a website with information about energy crop cultivation, Iggesund's offer, and how participants in the project can share information with each other.
"We're not expecting Cumbria to become covered by energy crops but we do believe this can be a convenient way for farmers to gain an additional source of income," Lofgren says. "We can take care of harvesting and transporting the crop, and we will be offering index-linked contracts so farmers can count on a reliable, inflation-protected source of income for the long term."
Back To Top
|
Stora Enso, Finland, and Packages Ltd., Pakistan, have completed the process of establishing a joint venture called Bulleh Shah Packaging (Private) Limited, as announced last September. Stora Enso's initial shareholding is 35% with a commitment to increase the shareholding at the agreed value to 50% at a later stage subject to certain conditions being met. The agreed value for 100% of the joint-venture company is approximately $108 million (EUR 83 million) on a cash and debt free basis. The cash consideration for the 35% shareholding amounted to approximately $39 million (EUR 30 million) in the second quarter of 2013.
The joint venture will, to a large extent, provide packaging products to key local and international customers in the fast-growing Pakistani market.
"We are pleased that we can now start to operate the new joint venture in Pakistan. The market has growing demand for packaging products and paperboard that offers an attractive growth opportunity for us," said Mats Nordlander, EVP, Stora Enso Renewable Packaging.
Following the acquisition, Stora Enso's share of the Bulleh Shah Packaging joint venture are being reported as part of the Renewable Packaging Business Area, beginning June 1.
Back To Top
|
The U.S. paperboard industry's revenue for the year 2012 was reported at $29.3 billion, with an estimated gross profit of 37.53%, according to an updated report by Supplier Relations US, Irvine, Calif., USA, titled Paperboard Mills Industry in the U.S. and its International Trade (2013 Q2 Edition). Import was valued at $1.8 billion from 44 countries. Research and Markets, Dublin, Ireland, has now added the report to its offering.
The industry also exported $5.8 billion worth of merchandise to 143 countries. Adding import value to and subtracting export value from the industry's shipment value, the total domestic demand for the industry in 2012 was $25.3 billion.
Back To Top
|
New Products
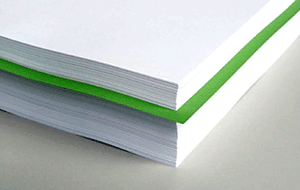 Clariant, Muttenz, Switzerland, this week launched the world's most highly-concentrated, urea-free liquid optical brightening agent (OBA) for printing and writing papers. New disulphonated Leucophor® ACK contains no environmentally-harmful additives, decreases OBA requirements for papermakers, and lowers transport costs and carbon footprint, the company notes.
Leucophor ACK is an ultra-concentrated aqueous solution specially designed to give state-of-the-art effectiveness while satisfying the most demanding environmental requirements. The unique, patented, new generation urea-free optical brightener is primarily intended for stock application in sized and unsized papers. Free of additives such as urea and glycols, the REACH-registered brightener contributes less to the overall nitrogen and COD content of backwaters and effluent. Leucophor ACK fulfils the requirements of Nordic Swan, EU Eco Flower, and BfR, Clariant points out.
From an efficiency perspective, papermakers look to use less active agent to achieve good brightness or whiteness for their application. The highly substantive, ultra-concentrated stilbene brightener exhibits high build up, even at extremely low concentrations, thanks to its strength and high affinity to the paper fiber. Compared with current disulpho chemistries, Leucophor ACK shows improved performance on stock addition to both virgin and recycled fiber, and in pigmented coating applications, particularly those containing PVOH as a secondary binder. It also allows greater flexibility and higher solids' contents in CMC and starch/CMC pigmented coatings, according to Calriant.
The OBA's higher strength supports fewer deliveries and reduced storage volumes for paper mills. It therefore generates better sustainability through savings in product quantity and logistics, plus a lower transport carbon footprint, as well as easier handling. Leucophor ACK liquid is also particularly suitable for unsized tissue, neutral-sized and heavy loaded papers, and is one of the most effective OBAs for use in wood-containing grades, such as improved newsprint and SC grades.
Back To Top
|
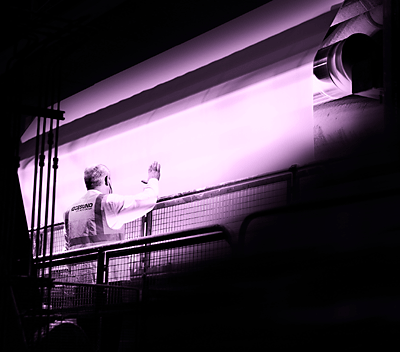 Iggesund Paperboard, Sweden, is advising customers to expect an upgrading of its folding box board Incada. Beginning this autumn, Incada will be whiter and lighter and also have a number of improved properties affecting printability. Incada Exel, which is more targeted as a packaging board, will also have improved stiffness. For grammages over 300 gsm, this gain will be as much as 10% to 15%.
"This enables our customers to reduce their packaging weights while keeping the same protection for the contents," explains Robin Lewis, technical product manager for Incada.
The stiffness improvements have also led to a revision of Incada Exel's grammage range to better suit the demands of the current customer base. Other substantial improvements have been made to the odor and taste properties so that Incada now comes in under the Robinson testâ detection limit of 0.6. The whiteness is increased by 7.5 units to 120 on the CIE scale. There also are improvements in the L value, which is critical for color reproduction. Runnability is also improved, so Incada will now be able to function even better in customers' processes.
"Incada was introduced in 2001 and since then we've made many small changes to improve its quality," Lewis says. This is a big leap forward and it will definitely strengthen our market position."
The biggest change of all in relation to the production of Incada, though, has nothing whatsoever to do with printability or the economy of customers' production processes. Incada is manufactured at Iggesund Paperboard's mill in Workington, England. This spring the mill changed its energy source from fossil natural gas to biomass, which is burned in a new high-tech power plant. Overnight, the mill eliminated its fossil carbon emissions from more than 190,000 metric tpy to zero. The reduction is the equivalent of taking more than 65,000 cars off the road every year (see article in Containerboard/Packaging section above). .
"This adds even more power to our sales message. Paperboard is widely seen as a very sustainable packaging material. By changing our energy source and upgrading Incada, we are now at the top of the folding box board market in terms of both product properties and sustainability," Lewis concludes.
The new Incada can be ordered this autumn with deliveries beginning in November.
Back To Top
|
 Twin Rivers Paper Company, South Portland, Maine, USA, a producer of lightweight specialty packaging, label, and publishing papers, has released an optimal packaging paper for dry and wet wax applications, Acadia® Waxing. These uncoated, machine-finished papers offer high absorbency for dry wax pickup and excellent holdout for wet wax pickup, resulting in superior performance for common applications such as burger, sandwich, and taco wraps, the company notes.
"Offering our customers more specialty packaging options is critical in this market. Acadia Waxing answers this need by providing a packaging solution specifically designed for dry and wet wax packaging applications," said Marcel Fortin, business development manager.
Back To Top
|
Published Pricing
DuPont, Wilmington, Del., USA, this week announced that it will increase prices on all of its titanium dioxide products sold in North America, Europe, the Middle East, Africa, Latin America, and the Asia Pacific regions effective July 1, or as contracts allow as follows:
- $200 per metric ton for DuPontTi-Pure® titanium dioxide grades sold in the Asia Pacific and Latin America regions
- $200 per metric ton for DuPontTi-Pure titanium dioxide grades sold in the dollar markets or EUR 160 per metric ton in Eurozone markets in the Europe, Middle East, and Africa region
- $0.08 per pound for DuPont Ti-Pure titanium dioxide grades sold in the North America region with the exception of DuPont RPS Vantage™ titanium dioxide products sold into paper and paperboard applications, which will be managed separately.
DuPont Titanium Technologies operates plants at DeLisle, Miss.; New Johnsonville, Tenn.; Edge Moor, Del.; Altamira, Mexico; and Kuan Yin, Taiwan, all of which use the chloride manufacturing process. The company also operates a mine in Starke, Fla. Technical service centers are located in Paulinia, Brazil; Mexico City, Mexico; Mechelen, Belgium; Dzerzhinskiy, Russia; Kuan Yin, Taiwan; Ichon, Korea; Shanghai, China; Hyderabad, India; and Wilmington, Del., to serve the Latin American, European, Middle Eastern, Asian, and North American markets.
Back To Top
|
Lecta, the second largest European coated woodfree paper-manufacturing group, made up of Condat, Cartiere del Garda, and Torraspapel, has announced a price increase for its one- and two-side CWF (coated woodfree) papers. Taking into consideration the manufacturing cost levels and the rising input costs, "the price increase is inevitable," the company notes.
The new prices will become effective with paper deliveries beginning in early July.
Lecta has nine factories divided into two production systems. By far the larger of the two is the coated fine paper system that encompasses five mills—in Italy (Riva del Garda), in France (Le Lardin St Lazare), and in Spain (Motril, Sant Joan Les Fonts, and Zaragoza), with a production capacity of 1,427,000 metric tpy. The smaller production system is the Torraspapel specialty group in Spain with five plants (Almazán, Berrobi-Uranga, Leitza, Sarrià de Ter, and Zaragoza) and a wide variety of complex converting, coating, and finishing machines, with a production capacity of 309,000 metric tpy and 123,000 metric tpy of uncoated woodfree and base paper.
Back To Top
|
People
Fortress Paper Ltd., Vancouver, B.C., Canada, reports the election of five directors at its annual general and special meeting of shareholders last month. The five nominees, with votes for/votes withheld are: Chadwick Wasilenkoff, 96.99%/3.01%; Per Gundersby, 97.00%/3.00%; Richard O'C. Whittall, 96.03%/3.97%; Joe Nemeth, 93.41%/6.59%; and Anil Wirasekara, 97.48%/2.52%.
Also at the meeting, shareholders approved the appointment of PricewaterhouseCoopers Chartered Accountants as auditors of the corporation for the ensuing year, the unallocated stock options under the corporation's amended and restated stock option plan, and the adoption of a shareholder rights plan.
The formal report of voting results with respect to all matters voted upon at the meeting is available online.
Fortress Paper operates internationally in two distinct business segments: dissolving pulp and security paper products. The company operates its dissolving pulp business at the Fortress Specialty Cellulose Mill in Canada, which is also in the process of expanding into the renewable energy generation sector with the construction of a cogeneration facility. The company also is seeking to expand its dissolving pulp capacity with the recent acquisition of Fortress Global Cellulose Mill at Lebel-sur-Quévillon, Qué., Canada, which Fortress is evaluating to convert into a dissolving pulp mill and re-start the cogeneration facility. The company operates its security paper products business at the Landqart Mill in Switzerland, where it produces banknote, passport, visa, and other brand protection and security papers, and at its high security production and research facility in Canada, where it manufactures optically variable thin film material.
Back To Top
|
Georgia-Pacific Paper Chemicals, Atlanta, Ga., USA, has named Mark Zempel North American Sales Manager. With more than 20 years of industry experience prior to joining GP Paper Chemicals, Zempel has held various functional and management roles in the paper and paper chemicals industries including process engineering, sales, marketing, customer service, and product management. Most recently, he was a sales manager supporting the Americas for AkzoNobel Pulp and Performance Chemicals.
Zempel holds a master's degree in business administration from Kennesaw State University and a bachelor of science degree in paper process engineering from Western Michigan University.
Back To Top
|
Metso, Finland, has appointed Pasi Laine, M.Sc in Engineering, president and CEO of the new company to be demerged from Metso Corp. and named Valmet Corp. (see article in Pulp & Paper section above). Laine is currently president of Metso's Pulp, Paper and Power business, and he will continue in this position until assuming the duties of the president and CEO of the new company. He has been a member of the Metso Executive Team since 2006.
"Metso's board of directors has studied the requirements of the new position carefully and has considered both external and internal candidates. Our target has been to find the best possible person for the role of president and CEO of Valmet Corp. Pasi Laine has had a long and successful career at Metso, holding various management positions in Metso's Automation and Pulp, Paper and Power businesses," said Jukka Viinanen, chairman of the board of Metso.
"It is an honor to be given this new opportunity to develop Metso's Pulp, Paper and Power business as an independent company and implement our business strategy and accelerate growth. Our goal is to be the leading global technology and service provider for the pulp, paper, and power industries. The new Valmet will be a modern and dynamic listed company," Laine said.
If Metso's extraordinary general meeting approves the demerger of Metso, the appointment will take effect on the planned registration date of the demerger, December 31, 2013. Metso plans to hold an extraordinary general meeting on or about October 1.
Matti Kähkönen will continue as president and CEO of Metso Corp. Until the demerger, Laine will continue as president of Metso's Pulp, Paper and Power business, reporting to Kähkönen.
Back To Top
|
Stora Enso Group, Finland, has appointed Treasurer Jyrki Tammivuori acting CFO, effective July 1. As announced in April, the current CFO, Karl-Henrik Sundström, will head the company's new Printing and Living Division, combining the current Printing and Reading Business Area and Building and Living Business Area beginning in July.
The process of recruiting a new CFO is advancing, Stora Enso reports.
Back To Top
|
Travels with Larry
PROCESS (according to Webster): A method of manufacturing something, a moving forward, to submit something to a treatment, preparation, or process.
PROCESS (according to API): PINCH, WATER CLOSE™, GREEN POWER+®, and AVAP®.
Based in Atlanta, Ga., USA, American Process Inc. (API) was founded by Theodora Retsina, CEO, in 1994, as a consulting practice serving the forest products industry. Since that time, API has shown steady growth to the tune of more than 80 employees with locations in Atlanta, Thomaston, Ga., Alpena, Mich., Greece, Brazil, and Romania (the company's employee count went from just 19 to 80 in the past 1.5 years). API has seven granted patents, and more than 50 patents pending in the biorefinery space.
Eric Fletty and I were invited by Kim Nelson, PhD VP of Government Affairs & Environmental Quality, to visit API's Atlanta offices this past May 29. We met with Kim and one of API's newest employees, Bahador Bakhtiari, Ph.D. Business Development director, Process Integration. Bahador just arrived from Montreal in the past two months after spending four years working in a similar capacity with Natural Resources Canada, CanmetEnergy (in the photo below (l-r) are Larry Montague, Kim Nelson, and Bahador Bakhtiari).
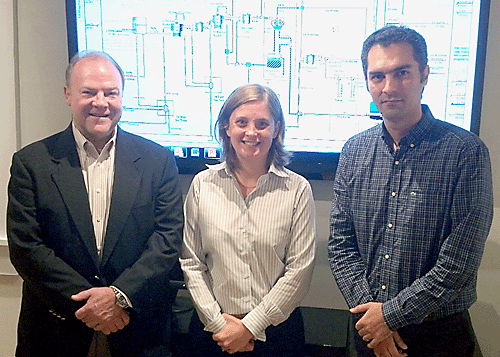
API is comprised of two business divisions that deliver process integration into pulp and paper mills and biorefineries. Steve Rutherford, COO, has led the Project Engineering group at API since 1997. Prior to joining API, Rutherford was Engineering VP of Parsons & Whittemore Inc., a global tier-one pulp and paper design-build, owner, and operator, and served at project director level for the $1.1 billion construction and commissioning of Alabama River (market pulp) and Alabama Pine Newsprint mills in Perdue Hill, Ala.
Back to the definitions of PROCESS according to API:
- PINCH is a systematic analytical process that allows pulp and paper mills to minimize steam use through operational changes and heat recovery projects. By reducing steam use, PINCH can significantly reduce operating costs associated with steam generation. Process integration is key—the principle of analyzing the entire processes as an integral system, and not just a collection of individual departments.
- WATER CLOSE is a technology that allows pulp and paper mills to minimize fresh water use while meeting flow and water quality demands. By identifying strategic water reuse opportunities, WATER CLOSE can significantly reduce operating costs associated with fresh water pumping and filtering, effluent treatment, steam use, and fiber and chemical losses.
- GREEN POWER+ is a cellulosic technology that co-locates with pulp and paper mills and biomass power plants. The hemicelluloses are selectively extracted into monomer sugars. The resulting sugars are fermented into cellulosic ethanol. The process configuration enables Green Power+ to convert the hemicelluloses to higher value added products; cellulosic ethanol, and/or renewable chemicals (demonstration plant is located in Alpena, Mich.).
- AVAP is a cellulosic technology that fractionates any biomass via the proprietary, patented use of SO² and ethanol into cellulose, lignin, and hemicelluloses. The cellulose and hemicelluloses are then converted into sugars. The sugars are high purity and low cost, making them ideal feedstock for downstream conversion into bio-based chemicals and biofuels. The lignin is burned as fuel in the boiler (demonstration plant is located in Thomaston, Ga.).
API has long been a very impressive company. Their accomplishments have gained the attention of GranBio out of Brazil to the point that GranBio announced on April 16, 2013, that it has invested in the North American Cleantech Company American Process Inc. (API). GranBio completed the acquisition of a 25% equity investment of API.
More information on API is available online.
More information about TAPPI is also available online
Remember, there are two types of people in our industry; TAPPI members and those who should be.
Until next time...
Larry
Back To Top
|
TAPPI News
TAPPISAFE is proud to be a sponsor of the Pulp and Paper Safety Association (PPSA) 70th Annual Safety and Health Conference - " The Human Element of Safety", June 9 -12, 2013 in Williamsburg, Va., USA.
Join speakers from MWV, Weyerhaeuser Company, Domtar, Safe Start, and International Paper, to hear the latest on how human behavior will proactively help prevent, detect and control events before they occur. The conference will feature updates from OSHA, member company case studies, and PPSA's popular legal update.
Join professionals from across the country to discuss the importance of safety and the human impact on safety.
Sponsorship opportunities are still available.
Register soon for the best rates. For more information visit "The Human Element of Safety" website.
Back To Top
|
On behalf of PAPTAC and Course Leader, Paul Stuart of EnVertis and Ecole Polytechnique, we are pleased to inform you of PAPTAC's first biorefinery course, to be held June 9-11 at the Sheraton Wall Center in Vancouver, ahead of the PACWEST conference. We hope that you can join us!
View the complete course brochure and registration
This PAPTAC biorefinery course will seek to provide the knowledge and tools for forest industry leaders, technology providers, and consultants to develop bioenergy strategies and better understand emerging bioenergy technologies and their design/implementation in a business strategy.
More specifically, the course is intended for corporate and mill leadership – including mill managers and senior technical staff – who wish to become more knowledgeable about biorefinery implementation strategy and design methods, and who seek to identify and select the best biorefinery strategy for their mills. A total of 19 expert instructors from across North America and Europe will share their experience during the three days, generally structured as follows:
Day 1: Advanced Biorefinery Fundamentals
Day 2: Setting Biorefinery Strategy
Day 3: Biorefinery Techno-Economics and Case Studies
The course format has been designed to encourage exchange between instructors and participants, and a copy of the newly-released book of "Integrated Biorefineries: Design, Analysis, and Optimization" will be included in the registration price. For your information, the same course will also be offered by TAPPI and co-sponsored by PAPTAC this September in Green Bay, Wis., USA. Learn more about that course.
We look forward to being in touch with you regarding this opportunity.
For information, contact Carmie Lato from PAPTAC at 514-392-6969
Back To Top
|
Your registration in the next few days will be one of the few reaining seats open for the popular TAPPI Introduction to Wet End Chemistry Course taking place June 11-13, 2013 at the TAPPI Training Facility in metro Atlanta, Ga., USA.
"This course is ideal for engineers and other technical people who need a better understanding of wet end chemistry," notes Scott Springmier, Manager, Pulp and Paper for TAPPI. "The course not only covers the key technologies, chemical additives and terminology but it also delves into the use of papermaking additives to change paper properties, improve runnability and reduce costs."
The course is designed for anyone that is involved with wet end operations as well as anyone training staff working in this area. New engineers with a strong technical background but lacking papermaking process knowledge would also benefit. Instructors focus this 3-day interactive training on innovative wet end chemistry principals and the use of additives to change or create new paper products. Through case studies, break-out sessions and networking with others in the course, attendees will learn how to implement new technology to improve efficiency and product quality, reduce machine downtime and off-specification production, select and use of papermaking chemicals, and troubleshoot problems.
Topics covered include: basic water chemistry, fibers and fines, starch, dry and wet strength agents, alum chemistry, rosin sizing, synthetic sizes, dyes, fillers, retention systems and deposit and pitch control. The impact of recent regulatory developments and how changes in fiber quality are impacting wet end operations are also reviewed.
The three course instructors are respected experts in wet end chemistry. Martin A. Hubbe, Ph.D., is Professor, Department of Forest Biomaterials, North Carolina State University. He began his career with American Cyanamid before joining International Paper Company as a research associate and later principal scientist. Larry Anker, Ph.D., is Sizing and Wet Strength Applications Group Leader for Ashland Hercules Water Technologies. He earned a B.S. in Chemistry, Mathematics and Physics from Washington and Lee University and Ph.D. in Chemistry at Penn State University. Przem Pruszynski, Ph.D., is Global Technical Specialist for Nalco. He holds an M.S. in Analytical Chemistry and Ph.D. in Physical Organic Chemistry from University of Poznan, Poland, where he taught for 12 years. He's authored nearly 100 papers, holds several patents and has taught numerous technical courses.
View the workshop schedule to see the specific topics covered.
Back To Top
|
Northeast PIMA/TAPPI Annual Scholarship Tournament
Friday, June 14 at Fox Ridge Golf Club, Auburn, Maine, USA.
Registration deadline is June 7.
Registration 6:30 a.m. to 7:45 a.m. Shotgun start 8:00 a.m. sharp.
All proceeds from this tournament support the Northeast PIMA/TAPPI Scholarship Fund. Register ASAP as spots fill quickly. We accept checks and all major credit cards.
We accept donated swag for prizes – interested donors please contact Mark Reed or Micki Meggison (contact info below).
• Fee: $100 per player (golf cart, BBQ, prizes, range, etc.)
• Hole Sponsorship: $100
• BBQ + Hole Sponsorship: $200 (additional recognition and signage at BBQ)
Three ways to enter:
1. Online Entry:
Fill out the registration form.
2. Mail Completed Flyer or team player names (or company name with hole and/or BBQ sponsorship choice) and check to:
Micki Meggison
Sappi Fine Paper NA
P.O. Box 5000
Westbrook, ME 04098
3. Fax completed flyer or team player names (or company name with hole and/or BBQ sponsorship) and payment information to:
Attn: Tanya Hickson c/o NE PIMA Local Section Golf Tournament
Secure Fax: 240.396.5973
Back To Top
|
Free Webinar: "Providing Operator Training to the Workforce"
The Pulp and Paper Manufacturers Association is proud to offer a free webinar on June 19: "Providing Operator Training to the Workforce of the Future."
The one-hour informational webinar will be presented by NPT2, the National Network of Pulp and Paper Training Technology. NPT2 was created under a National Science Foundation grant to provide training to your workforce with the skills needed to operate equipment, produce quality product, and to understand the technical aspects of their assignment, so that employees are truly engaged in and understand their work.
The webinar will cover various methods of operator training, including the more advanced educational training used by the paper industry around the world; introduction to the newest and most advanced curriculum of e-learning available, developed by industry experts; and how mills can customize learning.
The webinar will be facilitated by Michael J. Kocurek, PhD, Professor Emeritus, Paper Science & Engineering, North Carolina State University, and the Director of NPT2 at Alabama Southern.
The webinar, sponsored by the National Science Foundation and hosted by Alabama Southern, will begin at 11:00 a.m. est. and will appeal to human resource professionals, operations and manufacturing employees, process engineers, and others needing to stay current on operational training issues. To participate, please register online.
The pulp and paper industry is currently facing a serious shortage of trained workers who understand both what happens and why things happen. The crisis is dramatic due to ongoing retirement of a generation of seasoned workers who represent decades of experience. This is a challenge to the industry--but also an opportunity to train and create a more technologically advanced workforce.
This webinar will segue into the one-day Operator Training Workshop, sponsored by the National Science Foundation and Alabama Southern, in Thomasville, Ala., on July 18. (see article below titled Operator Training Conference and Workshop Set for July 18 at Alabama Southern).
Back To Top
|
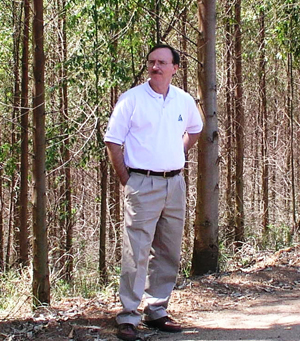 What do buggy whips and TAPPI membership have in common? If you ask member Jim Atkins, he'll tell you it is change – revolutionary, fast-moving, and ever constant change. But that's where the similarities end.
To keep ahead of the advances occurring every day in our industry, you need to have an advantage," Jim says, "and the best place to jump in with both feet is with membership in TAPPI." And, Jim talks from experience. He's been a member since 1975, joining shortly after receiving his degree in Chemistry from the University of North Carolina. For him, being prepared has been the best way to turn change into opportunity. "Embracing change is key to future success. You can continue to make buggy whips or you can embrace the opportunities that change offers." And TAPPI, he says, is the best way to do that.
Find out more by reading this month's Member Spotlight. Spotlight participants are recommended by fellow members and staff. If you would like to nominate a member just send their name (or names) to MemberSpotlight@tappi.org. We will forward a spotlight questionnaire to fill out and return.
We look forward to seeing you in the Spotlight!
Back To Top
|
As TAPPI is getting ready to celebrate its 100th Year Anniversary in 2015, we were wondering how much industry expertise we have in this great group of professionals.
So, we decided to post a discussion question on our TAPPI Social Media outlets. We asked, "How many years of paper and/or packaging experience do you have?"
Who knew such a simple question would have such an impressive response.
With more than 7,000 TAPPI members, all over the world, we have counted 650-plus years of industry experience! Now you probably can't find that anywhere else . So why don't you join us?
From those "born" into the industry to third generation professionals. From paper to packaging, to sustainability, environment, tissue, converters, and consulting. This TAPPI network has something for everyone.
Become a part of this unique community of paper and packaging professionals, and add your expertise to our group, and network with others to learn something new.
Visit our website to learn more today!
Back To Top
|
The Lake States TAPPI/North Central PIMA golf outing will take place August 13.
For more information, see the event announcement.
This year's kick-off Golf Outing is being held at Mid-Vallee Country Club in De Pere, Wis..An afternoon shotgun scramble golf outing is planned with dinner to follow. Prizes will be awarded and individual pin events will be held.
Those submitting their registration with their fee, postmarked by August 9, will be assigned holes on a first-come, first-served basis. Later registrations will be assigned as space is available. Foursome sponsors and all singles will be notified of their hole assignment at the course on the day of the event.
Back To Top
|
A native of Austria, Dr. Helmut Stark earned his doctorate degree in pulp and paper mechanical engineering from Graz Technical University. While attending school, he worked as a development engineer at the R & D Centre of J.M. Voith GmbH in Heidenheim, Germany. In 1968, he took a position as project leader and chief engineer for Borregaard Industries Ltd. in Hallein. Three years later, he transferred to J.M. Voith AG in St. Pölten as director of its Paper Machine Building Department. He remained with Voith until accepting his position at Graz Technical University in 1977. In 1976, Dr. Stark was named a full professor of paper and pulp technology. From 1985 to 1989, he served as dean of the Mechanical Engineering Department.
A TAPPI member since 1981, Stark presented at the 1988 TAPPI Coating Conference and at the 1995 TAPPI Emerging Technologies Workshop. He was elected a TAPPI Fellow in 1997.
Stark authored and co-authored some 50 articles and books and approximately 70 technical papers on fundamental and applied research aspects of process engineering and machinery design, alternative fibrous raw materials, environmentally benign pulp production, and physico-chemical testing methods. He is recognized as the scientific organizer of the annual Austrian Paper Technology Conference in Graz , and he served as program committee chairman for the 1993 EUCEPA Conference in Vienna.
Back To Top
|
The TAPPI Best Practices on the Corrugator Course, June 25-27 at the TAPPI Training Center in Peachtree Corners, Ga., USA.
Top 10 Reasons to Register for TAPPI's Best Practices on the Corrugator Course:
#10 Gain the knowledge you need to troubleshoot most operational problems.
#9 Learn how you can maintain quality while reaching maximum corrugator speeds.
#8 Network with peers to find solutions to your quality issues.
#7 See on-site videos of conditions producing defects and how they can be resolved.
#6 Learn from industry-renown instructors Tom Pearce, Pearce Corrugated Consulting; Dan Dyson, Vice President of Production for Avista Solutions International, Inc.; Jon Porter, Senior Instructor/Process Specialist, Fosber America; Robin A. Sommers, Engineering Manager, Donahue & Associates; and Peter Snyder, National Account Salesman, Harper/Love Adhesive.
#5 Bring your defects to the experts—and to your colleagues in the room—to get guidance on how to overcome your production problems.
#4 Find out how you can get the maximum yield of boxes from the paperboard consumed.
#3 Take home new ideas and operational methods to improve production.
#2 Analyze your mill's specific problems with course instructors and explore possible solutions.
And the Number 1 reason why you should register for the 2013 TAPPI Best Practices on the Corrugator Course is...
With all of these great reasons, how can you not afford to?
Last year's course sold out, so here's your chance to attend. If you work with a corrugator, this is your opportunity to learn how to:
- Increase productivity and improve quality
- Reduce excess waste
- Adopt the "Centerline Process" to achieve a product that is consistent on every shift
- Maintain quality while reaching maximum corrugator speeds
- Get the maximum yield of boxes from the paperboard consumed
- Troubleshoot the most common operational problems
- Recognize critical properties of paperboard, starch, adhesive, and how to control warp.
What to Bring with You: Your questions and issues related to corrugator operations and samples of your defects.
What You'll Take Home: New ideas and operational methods to improve production.
Want to know more? Here's the Proposed Course Schedule.
Put June 25-27 on your calendar and register now to lock in your participation before seats fill.
Back To Top
|
The existence of cellulose nanocrystals and cellulose nanofibrils has been known for several decades, yet recent advances in science, particularly in the field of nanotechnology, have revealed that these materials contain unique physical properties, particularly high strength properties. Researchers have been studying how these materials can improve paper properties and will present their latest finding this June 24-27 in Stockholm, Sweden, at TAPPI's 8th Annual International Conference on Nanotechnology for Renewable Materials at the KTH Royal Institute of Stockholm.
The program for this year's event has been released, and one session will focus on using cellulose nanofibers for improving retention and increasing strength in paper. Researchers from Aalto University in Finland will report on improved flocculation of both precipitated calcium carbonate (PCC) and kaolin with the addition of certain cellulose nanomaterials. Researchers from Papiertechnische Stiftung (PTS) in Heidenau, Germany, will report on the importance of adding fillers, celluloses, and compounding agents in the right order to achieve the best results. Researchers from VTT in Finland will report on ways to increase the strength of paper by using filler particles coated with nanoscale calcium silicate hydrate (CS) structures.
New reports at the conference will present some exciting advances for both within the pulp and paper industry and beyond. The technical program features cellulose nanomaterials in a variety of applications, including:
- Unique and Thin-Film Composites
- Filler and Coating Applications for Different Paper Grades
- Improved Barrier Properties for Packaging Applications
- Cellulose Nanomaterials as Films and Carriers in Medical Applications
- Nanopaper and Iridescent Colored Cellulose Films.
With more than 80 technical presentations, five keynote presentations, and 50 poster presentations, this year's conference is packed with the latest applications of renewable nanomaterials.
Watch for additional updates from TAPPI on how nanotechnology, and cellulose nanomaterials in particular, can be a transformative technology for the pulp and paper industry.
The 8th Annual International Conference on Nanotechnolgy for Renewable Materials is hosted by TAPPI's International Nanotechnology Division, which strives to collectively advance the responsible and sustainable production and use of renewable nanomaterials. More information is available online.
Back To Top
|
Paper Machine Wet Press Manual, Fourth Edition
Edited by: Richard A. Reese
Paper Machine Wet Press Manual provides an introduction to wet pressing technology in the paper industry and includes information on practical press section considerations on paper machines. The book provides an overview of press section equipment and key factors in optimizing press section performance. In addition, checklists are included to evaluate press section performance.
The book will be particularly useful to paper company personnel including paper machine superintendents, foremen, paper machine operators, process engineers, etc. Employees of suppliers to the paper industry involved in supplying press section equipment and evaluating press section performance will also find the book beneficial. The Paper Machine Wet Press Manual, Fourth Edition is a project of the Water Removal Committee of TAPPI's Engineering Division.
Item Number: 0102B042 • List Price: $124 • Tappi Member: $83
Starch and Starch Products for Wet End Application
By: Hans W. Maurer
Starch and Starch Products for Wet End Applications is a complement to Maurer's previous book, Starch and Starch Products in Surface Sizing and Paper Coating. His new book, Starch and Starch Products for Wet End Application, addresses issues in the preparation and application of starch and starch products for use in the wet stages of the papermaking process. This publication covers a wide range of subjects in starch utilization, ranging from the preparation of specific starch products to their use in papermaking for flocculation, retention, drainage, strength, and sizing control. Environmental issues in the use of starch and analytical procedures for starch analysis and charge characterization are also addressed.
Item Number: 0101R319 • List Price: $185 • Tappi Member: $125
E-BOOKS COMING SOON
Roll and Web Defect Terminology - E-Book
By: Jerome M. Gess and Paul H. Wilson
This book takes the reader through the process of making paper, pointing out where interruptions can occur and where elements that are added to the system can cause problems in that part or subsequent parts of the papermaking process. The aim of this book is to give papermakers and those involved in the papermaking process the information required to allow them to understand how to track down and solve problems at their source rather than where the problems surface.
Paper Machine Quality Control Systems - Volume 1: Measurement Systems and Product Variability - E-Book
By: Quality Control Systems Education Common Interest Group of the Process Control Division
This book describes in detail the measurement technology used in Quality Controls Systems (QCS). Individual chapters are devoted to the five most prevalent QCS measurements (basis weight, moisture, caliper, ash, and color) in the paper industry. Each of these chapters covers the physical principles involved in each measurement, sensor designs, various methods of implementation, and influence factors. A somewhat lighter coverage is given to 10 other QCS measurements that do not have such a broad installation base. Common issues that impact all sensors are explained, including how sensor performance is measured and reported, the impact of scanning processes, filtering, scanner designs and construction, and sensor calibration and correlation. Statistical methods are covered in depth from discrete one-dimensional variability to multi-dimensional variability. Guidance is provided for using these statistical methods to locate the sources of variability in the paper process. This book was written by the Quality Control Systems Education Common Interest Group of the Process Control Division.
COMING SOON IN PRINT
Production and Applications of Cellulose Nanomaterials
By: Alan W. Rudie, USDA Forest Service, Forest Products Laboratory,
Michael A. Postek, National Institute of Standards and Technology,
Robert J. Moon, USDA Frost Service, Forest Products Laboratory,
Michael A. Bilodeau, University of Maine
Cellulose nanocrystals and cellulose nanofibrils have been known for upwards of 50 years, but recent research suggesting very high strength properties and other unique physical properties have generated extensive interest in these materials. The book will be a collection of summaries on recently completed and on-going research with these high strength materials. This book will highlight cutting-edge research as well as leads on successful applications. Topics will include: production and modification, composites, other applications, modeling, and standards.
Back To Top
|
The Pulp and Paper Manufacturers Association (PPMA) has launched its first-ever Best Place to Work Award. The award is open to all companies in the forest products industry and will look not only at corporate life but also look at how employees feel about their work environments.
In conjunction with Majority Opinion Research Group, PPMA has started taking nominations for this award and will continue to accept nominations through July 1.
"This award is an exciting opportunity for PPMA to honor great companies. As an association that serves HR professionals, we know the value of the making your company a great place to work," said PPMA President Joe Thibaudeau, employee relations manager - Procter & Gamble - Green Bay, Wis., USA.
The award will be presented to the winner at the annual PPMA conference on October 23-25, 2013, in Milwaukee, Wis., USA. The winner will have the chance to speak with conference attendees about what makes his or her company the "Best Place to Work."
PPMA is a nonprofit association built around a community comprised of executives, managers, and human resource professionals from the pulp and paper industry. For its members, PPMA serves as a primary source of information on labor settlements and current human resource issues, governmenta,l and related operational issues.
To nominate your company for the Best Place to Work Award, use the online form.
Back To Top
|
Alabama Southern will host a one-day-only Operator Training Conference & Workshop. This complimentary event, funded by the National Science Foundation (NSF) in conjunction with NPT2, will help HR professional and mill leaders add value to their existing operator training programs and provide practical advice on how to create a more competitive and better trained workforce.
Date: Friday, July 18
Location: Alabama Southern, Thomasville, Ala.
Time: 8:00 a.m.- 3:00 p.m CST
Discover new tools, learn best practices, and better equip your operator workforce. For more details or to register for the event, please contact Martha Wynn by email or by phone at 334.637.3194.
Back To Top
|
Nominations for the major TAPPI 2014 awards are due by August 1. The awards that may be presented in the upcoming year are:
Gunnar Nicholson Gold Medal Award - The Association's highest technical honor may be presented annually to recognize an individual or individuals for preeminent scientific and engineering achievements of proven commercial benefit to the world's pulp, paper, board, and forest products industries and the other industries that TAPPI serves.
Herman L. Joachim Distinguished Service Award - The Association's highest award for service may be presented annually to recognize leadership and service that have significantly and demonstrably contributed to the advancement of the Association.
Paul W. Magnabosco Outstanding Local Section Member Award - The highest honor for Local Sections may be presented annually to recognize an individual for outstanding leadership and exceptional service to one or more Local Sections, which have resulted in significant and demonstrable benefits to the Local Section members.
TAPPI Fellow - TAPPI Fellows are individuals who have been members of TAPPI for not less than 10 years prior to the nomination, and who have contributed meritorious service to the Association and/or the paper and related industries. Retiring members of the TAPPI Board of Directors become Fellows automatically at the end of their term.
The TAPPI Awards and Honors page has links to these awards that will show the qualifications required and links to the nomination forms that must be completed. You may submit all nomination forms by email to standards@tappi.org, or you may fax them to the attention of the awards department at +1-770-446-6947, or send them by mail to TAPPI, Awards Department, 15 Technology Parkway South, Peachtree Corners, GA 30092, USA.
Back To Top
|
The TAPPI Introduction to Kraft Pulping and Bleaching Course is coming August 5-6, 2013, at the TAPPI Training Facility.
This course is efficiently and expertly planned and taught by one of the world's most recognized educators in the pulp and paper industry, Dr. Michael Kocurek, Emeritus Professor, North Carolina State University. In just two days, you'll gain a valuable overview of kraft operations that would normally take nearly 15 days in other, more comprehensive training.
The TAPPI Introduction to Kraft Pulping and Bleaching Course is designed to:
- Expand overall understanding of kraft pulp mill operations
- Broaden awareness of how one part of the process affects other operations
- Demonstrate the affect of processes on kraft pulp quality
- Build confidence for better interaction among experienced process engineers and operators
- Help you troubleshoot product quality problems.
Participants will learn specifically about:
- Wood and fiber raw materials
- Preparation of wood and chips for pulping
- Preparation of white liquor
- Pulping terminology, pulp properties, and tests
- Batch and continuous cooking
- Kraft pulping chemical reactions
- Pulping variables and effects on properties
- Trends in kraft pulping and bleaching
- Brown stock washing
- Screening and cleaning
- Bleaching and oxygen delignification
- The pulp mill biorefinery.
Who Should Attend?
This course is ideal for anyone new to the kraft pulping process, particularly process engineers and operators.
Learning Outcomes
After successfully completing the course, participants should be able to:
- Describe and define kraft pulp mill processes, equipment, operating variables, and terminology, in order to increase ability to improve operations and pulp quality
- Recognize how one part of the process affects other operations, in order to increase awareness of thinking on a mill wide scale
- Interpret how the process variables affect pulp quality, in order to improve pulp quality and troubleshoot variations in quality
- Extend awareness of the complex environmental challenges associated with kraft pulp production.
Please register soon. Only 25 seats are available for this course to ensure the most beneficial interaction among attendees and the instructor.
Back To Top
|
The 2013 TAPPI Linerboard/Medium Manufacture Course, August 13-15 at the TAPPI Training Room, in Peachtree Corners, Ga., USA, is designed to help increase your understanding of linerboard and medium performance properties and manufacturing to improve corrugated box performance and runnability.
This intermediate-level course is ideal for process engineers and operators in linerboard and medium manufacturing facilities and converting plants with a more intermediate background. For those participants who require an overview background on pulp and papermaking technology, there will be an optional one day Introduction to P&P on Monday afternoon, August 12, prior to the beginning of the main course on Tuesday. This supplemental session is intended for corrugators, new P&P mill and supplier personnel, and those without exposure to pulp and paper operations.
If you are looking to increase your understanding of linerboard and medium performance properties and how they are achieved, build your confidence in interacting more knowledgeably within the mill with suppliers and with corrugators, and improve manufacturing operations to produce a more competitive product, then this course is for you.
There are only 25 seats are available for this course. Register now to reserve your spot.
Back To Top
|
The corrugated packaging and converting industry is heading for Indianapolis, Ind., USA, October 7-9, 2013, for TAPPI CorrExpo 2013. The JW Marriott is the waypoint where ideas turn into innovation. Join your colleagues to take advantage of highly-sought-after speakers, seminars, workshops, exhibits, and programs you don't want to miss:
- There will be two keynote presentations - Bob Chapman, CEO and chairman of Barry-Wehmiller, and Alexander Toeldte, president and CEO of Boise Inc.
- Extensive networking and sales opportunities on the sold-out exhibit floor
- Training and insight from the best in the industry
- A cutting-edge technology showcase exhibit of innovative trends and design
- Opportunity for one-on-one meetings with top-level attendees
- Problem solving with industry experts
- Numerous special events, including a welcome reception, golf tournament, gala at the Indianapolis Motor Speedway, and spouse/guest program
- Eye-opener sessions tackling timely topics affecting box plants today, with plenty of time for questions and interaction with the speakers
- Complimentary workshops on Wednesday afternoon for all registered exhibit visitors.
View the full program to see what's in store for you this October.
Register today.
Back To Top
|
The TAPPI Centennial Celebration will be a multi-year long series of outreach events and educational offerings showcasing the proud history and promising future of the global pulp, paper, packaging, and related industries. This once-in-a-lifetime event will expand public awareness, foster further connection, and provide outstanding opportunities for collaboration, growth, and investment in our future for all of those involved. Goals for the TAPPI Centennial Celebration are:
- To honor TAPPI's 100 years of connection, education, and advancement as a foundation for the sustainable success of our members, our industries, and the world we share
- To recognize the achievements of those who built our industry and to inspire those who seek to build its future
- To celebrate the contributions and innovations of the global pulp, paper, and packaging industries to human culture, commerce, health, and social advancement
- To sustain the industry and support its growth, vitality, and future through the TAPPI Foundation.
We invite you to be a part of this momentous event. The sooner you join us the more opportunities there are for recognition of your company, its products, and key innovations. Keep in mind that an early commitment allows you to spread your investment over multiple years' budgets.
For more information on sponsorship and volunteer opportunities please contact dbell@tappi.org.
The sponsorship prospectus can be downloaded online.
Back To Top
|
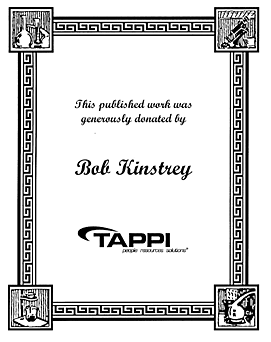
Do you have a history book gathering dust on your shelf? TAPPI's 100th year is coming soon and we are looking for donations to the TAPPI Library. Specifically, we are interested in histories of companies and mills in the paper and packaging industry (both producers and suppliers). Each donated book will have a bookplate in the front cover recognizing the donor. For more information please contact David Bell.
Please send books to:
c\o David Bell
TAPPI
15 Technology Parkway, South
Suite 115
Peachtree Corners, Georgia 30092
Back To Top
|
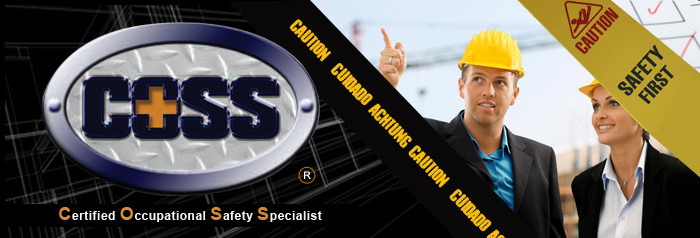
Are you ready to go further, faster in your safety career? The Certified Occupational Safety Specialist (COSS) class can take you there.
The COSS Class is Unique
Not only will you learn how to read and understand the OSHA 1910 and 1926 CFRs and help your company avoid OSHA citations that cost millions of dollars, but more importantly, by learning how to work safely on a job site, you can teach your company how to lower fatalities and near misses. Almost 47% of COSS graduates responding to our survey indicate that, since taking COSS, their company's injury rate and/or OSHA recordables have decreased by as much as 25% and others attest to as much as a 100% decrease!
Request a Course Outline & Syllabus for more information.
The class also addresses the psychology of safety, the true cost of an accident, hazard recognition, how to start up a health and safety program, behavior based safety, system safety, and much more!
What Will You Receive?
Upon successfully completing the class, you will obtain your national Certified Occupational Safety Specialist (COSS) designation, your OSHA 10-hr. card of completion in construction, and your OSHA 10-hr. card of completion in general industry.
National Program Recognitions
COSS is currently one of only 37 programs in the world recongnized and accredited by the American Petroleum Institute (API). In addition, the certifying body for construction education for colleges, universties and technical/trade schools, American Council for Construction Education (ACCE), has also recongnized our program. COSS is the only non-degree program to receive this national endorsement. Lastly, COSS has been established as a mandatory course for students in the Construction Management Program at Louisiana State University.
Program Content
The program consists of 40 hr. of hands on, face-to-face learning, which is delivered by an Authorized OSHA outreach trainer in both construction and general industry. Case studies and workshops are used extensively to bring learning objectives into focus. Guest speaker from areas such as OSHA and other governmental agencies are used to enhance the learning experience. Student presentations, daily quizzes, practical reviews, and a comprehensive final exam will allow you to demonstrate your competency.
Prerequisites
The only prerequisite for the COSS class is you must have a high school diploma or equivalent. In each class, we tend to have a mix of non-experienced, first time safety persons, as well as safety professionals who have been in the safety field for 20+ years. But, we have learned that regardless of the numbers of years of experience you have in safety, everyone leaves the COSS class with a wealth of knowledge!
Visit the COSS website for FAQs, testimonials and a list of clients that have taken COSS.
Register now.
If you would like more information on the COSS program, contact Beth Gordon at 877-610-2677.
Back To Top
|
|
|
TAPPI Over the Wire | 15 Technology Pkwy. S. | Norcross, GA 30092 USA | Voice: 770.446.1400 | Fax: 770.446.6947
|
 |