 |
|
Weekly Spotlight
Cascades Inc., Kingsey Falls, Que., Canada, a producer of green packaging and tissue products, has been named recipient of a "Phare" Award presented by Korn/Ferry - Les Affaires, organizers of the contest that recognizes corporate governance and social responsibility
Learn More...
|
Metsä Board Corp., Finland, reports that a fire broke at the reel warehouse of its Gohrsmühle mill in Germany early in the morning of February 15
Learn More...
|
To update its award-winning PAPERbecause campaign, Domtar Corp., Montreal, Que., Canada, this week announced a new series of videos that take a humorous approach to highlight the irreplaceable value of paper
Learn More...
|
The keynote speaker for the OpEx Maintenance and Reliability Workshop at TAPPI PaperCon 2013 in Atlanta, Ga., USA, on April 30, will be John Yolton with SKF, a highly respected paper industry reliability expert
Learn More...
|
Members of the American Pulp & Paperworkers' Resource Council (PPRC), McGehee, Ark., USA, this past week visited Washington, D.C., to educate members of the U.S. Congress and administration officials on the impact of legislative and regulatory decisions both on the environment and on the families and communities that depend on forest products manufacturing for their livelihood
Learn More...
|
TAPPI's newest publication, Tissue360° magazine, and TAPPI tissue experts have organized a comprehensive technical forum for PaperCon 2013 in Atlanta, Ga., USA, April 28 – May 1
Learn More...
|
The webinar will present and discuss an overview of tissue making to achieve desired tissue properties, especially softness and bulk
Learn More...
|
The TAPPI Tissue Properties & Manufacturing Course will be held on April 27-28, 2013, in Atlanta, Ga., USA, and co-located with 2013 PaperCon and the Tissue Forum
Learn More...
|
Below is the latest listing of job openings in the TAPPI Career Center
Learn More...
|
Market Roundup
Forest2Market, Charlotte, N.C., USA, reports that it has begun providing its Lake States subscribers with its Forest2Mill Delivered Price Benchmark, the first transaction-based market price report available in the region.
Learn More...
|
Pellet exports from the two primary pellet-producing regions on the North American continent, the U.S. South and British Columbia, continued to increase in the 3Q/12 and reached a new record of 860,000 tons, according to North American Wood Fiber Review (NAWFR), Seattle, Wash., USA
Learn More...
|
Global market pulp NBSK (northern bleached softwood kraft) prices last month rose ~$20-$25 per metric ton m/m, to $893 per metric ton
Learn More...
|
Pulp & Paper
Ahlstrom, Helsinki, Finland, this week said that its head office, as previously reported, will move to the Töölönlahti area in the center of Helsinki at the end of February
Learn More...
|
Cascades, Candiac, Que., Canada, reports that its Antibacterial paper towel has been named a 2013 Edison Awards Finalist in the Consumer Packaged Goods: Cleaning Solutions category
Learn More...
|
Catalyst Paper, Richmond, B.C., Canada, has agreed, subject to court approval, to sell its approximately 50% interest in Powell River Energy Inc. and Powell River Energy Limited Partnership to Powell River Energy Trust
Learn More...
|
Domtar Corp., Montreal, Que., Canada, is furthering its partnership with Recyclebank, New York, N.Y., USA, by supporting that organization's Recyclebank Green Schools Program that awards schools grant money for student projects that will make a positive environmental impact on their communities
Learn More...
|
Duni, Malmö, Sweden, reports that it will enter into trade union negotiations with the intention to close one of three production units of its Sweden-based Rexcell Tissue & Airlaid AB subsidiary
Learn More...
|
Arctic Paper S.A., Poland, presented a public takeover bid to shareholders of Rottneros AB, Stockholm, Sweden, this past November, and has extended the acceptance period to February 26
Learn More...
|
Södra, Sweden, has decided to divest its Tofte chemical pulp mill in Norway
Learn More...
|
Containerboard/Packaging
Boise Inc., Boise, Idaho, USA, this week announced key investments in the converting operations of its Packaging business
Learn More...
|
Gorham Paper and Tissue, Gorham, N.H., USA, has expanded its capability to make packaging papers with up to 25% wet strength, color, and grease resistance
Learn More...
|
Iggesund Paperboard, Sweden, reports that production of Invercote at its Iggesund, Sweden, mill in 2012 surpassed all of that facility's previous environmental achievements
Learn More...
|
Menasha Packaging Co., Neenah, Wis., USA, reports that its Folding Carton Group has expanded its capabilities while enhancing its ability to respond to accelerated lead times, thanks to a recent multi-million dollar capital investment
Learn More...
|
Resolute Forest Products, Montreal, Que., Canada, might be in a position to decide what it will do with its Fort Frances, Ont., mill later this spring, according to a report this week by the Times Online, an Internet news publication of the Fort Frances Times newspaper
Learn More...
|
Smurfit Kappa's Hoya mill, Germany, has successfully started up its PM 2, following a major rebuild of the dryer section by Andritz, Graz, Austria
Learn More...
|
|
New Products
Arjowiggins Graphic, France, has launched its Innovative 100% recycled, high speed Inkjet paper
Learn More...
|
Pump specialists Michael Smith Engineers, UK, has recently added a new range of magnetically coupled vane pumps to the pumps and pumping systems it offers
Learn More...
|
VoithPaper, Germany, has launched the NanoPro roll cover for calenders
Learn More...
|
Published Pricing
Kemira, Finland, this week announced price increases on all list and off-list pricing for its acrylic acid and acrylamide-based polymer products in North America
Learn More...
|
SCA Containerboard, Sundsvall, Sweden, this week announced a price increase for its unbleached kraftliner of EUR 40 per metric ton in continental Europe and £ 35 per ton in the U.K.
Learn More...
|
Following a recently announced coreboard price increase, Sonoco-Alcore S.a.r.l., Brussels, Belgium, this week announced that it will increase prices of all tube and core-related products by 5.5%
Learn More...
|
People
Tembec, Montreal, Que., Canada, reports that Yvon Pelletier, EVP, Specialty Cellulose and Chemical Group, will be leaving the company, effective February 22, and that Christian Ribeyrolle has been appointed EVP, Specialty Cellulose
Learn More...
|
The Newark Group, Cranford, N.J., USA, has appointed Paul Spitale VP of Sales for Converted Products
Learn More...
|
Fortress Paper Ltd., Vancouver, B.C., Canada, has appointed Yvon Pelletier president of its dissolving pulp business, effective February 25
Learn More...
|
TAPPI News
TAPPI's Annual Business Meeting will be held on March 12 via teleconference.
Learn More...
|
Two to choose from: Innovation in Safety (February 21) and Increasing Paper Machine Agility (March 13).
Learn More...
|
Introductory level webinar offers overview of tissue manufacturing for softness and bulk.
Learn More...
|
Organized by tissue experts, this comprehensive technical forum will cover all aspects of tissuemaking.
Learn More...
|
The TAPPI Tissue Properties & Manufacturing Course will be held on April 27-28, 2013, in Atlanta, Ga., USA, co-located with PaperCon 2013 and the Tissue Forum.
Learn More...
|
PaperCon will feature Executive Panel with leaders from International Paper, NewPage, Verso, and Soundview.
Learn More...
|
Long-time TAPPI member Gopal Goyal is quick to advise young industry professionals to get involved with TAPPI because it really pays dividends when it comes to their careers.
Learn More...
|
Highly regarded industry leaders to speak on April 29 at Papercon '13 in Atlanta, Ga., USA.
Learn More...
|
One of TAPPI's most exciting new products, the laminated and wall-sized 2013 Pulp & Paper "Mills of the World" Map, is now available through TAPPI Press with a twenty dollar discount for members.
Learn More...
|
Introductory course on printing methods and applications is designed for those who need to understand print quality, attend print trials, trouble shoot print problems, or are generally new to printing operations.
Learn More...
|
The Virginia-Carolina TAPPI Local Section Winter Conference, to be held in Richmond, Va., USA, on February 25, will focus on Boiler MACT and Bioenergy developments.
Learn More...
|
Expand your knowledge, improve your personal network, and learn ways to generate innovation at PaperCon.
Learn More...
|
Register now for the class where you will learn to understand OSHA, avoiding citations that could cost millions of dollars. Teach your company how to lower fatalities and near-misses.
Learn More...
|
Advance your career by presenting! Call for Papers underway for three of TAPPI's most important fall events.
Learn More...
|
David Schirmer, Vice President and General Manager, Hearst Enterprises, will Keynote SRW Workshop this April.
Learn More...
|
This valuable reference for everyone involved in converting and printing is now available from TAPPI Press.
Learn More...
|
Attend TAPPI's SRW Workshop in April and be a part of this dedicated group of mills, carriers, warehouses and printers as they collaborate to reduce in-transit damage to rolls of paper.
Learn More...
|
The International Mechanical Pulping Conference, sponsored by PI, TAPPI, PAPTAC, SPCI, and PTF to be held June 3-5, 2014, in Helsinki, Finland, has Calls for Papers due by Feb. 28, 2013.
Learn More...
|
TAPPI and NCSU are partnered again for the first of three introductory level courses for industry professionals that cover the entire pulping and papermaking process.
Learn More...
|
Strengthen your understanding of the corrugating process and linerboard and medium performance properties and manufacture with TAPPI's Linerboard Medium & Corrugated Box Manufacture Course, April 15-16, at the Holiday Inn in Neenah, Wis., USA.
Learn More...
|
April 16-18, 2013 - Join industry veteran Dick Target, founder of On Target Consultants, as he helps attendees identify and address downtime issues and develop a better understanding of machine calibration and how to maintain proper board caliper during the converting process.
Learn More...
|
PaperCon 2013 to feature session focusing on effective labor/management teams that yield positive business results.
Learn More...
|
This book takes the reader through the process of making paper, pointing out where interruptions can occur and where elements added to the system can cause problems in that part or subsequent parts of the papermaking process.
Learn More...
|
|
Find us on Facebook
Network with us on LinkedIn
Follow us on Twitter
|
Weekly Spotlight
Cascades Inc., Kingsey Falls, Que., Canada, a producer of green packaging and tissue products, has been named recipient of a "Phare" Award presented by Korn/Ferry - Les Affaires, organizers of the contest that recognizes corporate governance and social responsibility. For the past 11 years, the event has honored companies and boards of directors who stand apart for ethical practices and excellence in corporate governance. This year, the judges decided to look at corporate governance specifically in regard to social responsibility. Cascades captured first prize in the "Corporate" category.
"We are very proud of this acknowledgement. At Cascades, we believe that all organizations have a moral duty to be socially responsible, that is, to take concrete steps toward incorporating social, environmental, and economic issues into their operations. As you may know, we have quite a history in this area. Sustainable development and social responsibility are an integral part of our mission, vision, and management philosophy," explained President and CEO Alain Lemaire.
The panel of judges acknowledged Cascades' stellar performance, highlighting its three-year sustainable development plan, which is based on the results of a broad consultation of all of the company's stakeholders including clients, suppliers, employees, shareholders, local communities, and environmental groups.
Back To Top
|
Metsä Board Corp., Finland, reports that a fire broke at the reel warehouse of its Gohrsmühle mill in Germany early in the morning of February 15. The fire was put out later that day and a fire watch was installed. The fire did not spread outside of the reel warehouse, and no personal injuries occurred.
Sheeting operations at the site will be stopped for some time due to the fire, and customers will be informed about the possible impacts on the deliveries in due course, the company noted. It added that the fire is not expected to have any material impact on Metsä Board's total folding boxboard deliveries or any material result impact for Metsä Board.
Metsä Board produces cast coated Chromolux papers and has folding boxboard sheeting operations that were launched in autumn 2012 at the Gohrsmühle mill.
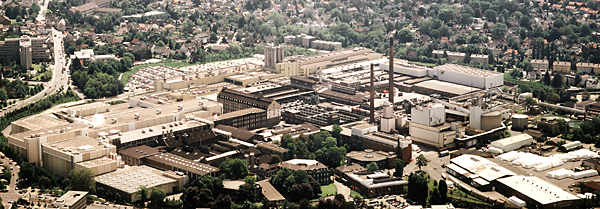
Back To Top
|
To update its award-winning PAPERbecause campaign, Domtar Corp., Montreal, Que., Canada, this week announced a new series of videos that take a humorous approach to highlight the irreplaceable value of paper. The 30-second spots mark the third wave of videos in the campaign that showcases the effectiveness and sustainability of paper.
While the initial videos featured satirical office settings and exaggerated pressures to go paperless, the four new videos bring that comedy to everyday situations, ranging from a bridal shower to a business lunch. For example:
- A husband disappoints his wife on their anniversary by choosing to send an e-card instead of a paper card with a handwritten note
- A woman at a bridal shower receives a hideous vase, but she's relieved once she locates the receipt, showing how paper can make any gift the perfect gift
- A man using his home computer can't get his new router to work because there are no paper instructions, and he cannot log on to download the PDF
- A waiter at a restaurant butchers his customers' orders by not writing them down.
- The videos will debut in March on the websites of The New York Times, National Geographic, and other news outlets. They will also be featured on PAPERbecause.com, Domtar.com, YouTube and Facebook.
"The PAPERbecause campaign has always promoted the responsible use of paper and the need to balance print vs. pixels, and we wanted to illustrate several instances of when paper is the most effective way to communicate on a logical and emotional level," said Paige Goff, Domtar's VP of Sustainable Business and Brand Management. "Our previous office videos reminded people how Domtar has long been a leader in sustainable paper production, but with the new videos, we wanted to focus on everyday life."
Since PAPERbecause debuted in 2010, it has won many awards from the public, the print industry, and marketers.
"We've been very pleased with the recognition PAPERbecause has received, and we think it speaks to a bigger point," Goff said. "Even after 2,000 years, there are times when no substitute for paper will suffice."
Back To Top
|
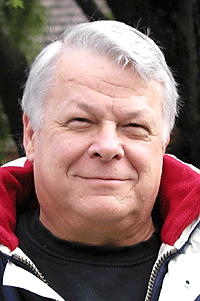 The keynote speaker for the OpEx Maintenance and Reliability Workshop at TAPPI PaperCon 2013 in Atlanta, Ga., USA, on April 30, will be John Yolton with SKF, a highly respected paper industry reliability expert who will explore "The Continuing Journey to Asset Reliability Improvement." As Yolton notes, "with the NAM pulp and paper market contracting, only the most reliable equipment can provide a competitive advantage. Data demonstrates that there is clearly a return on investment for those ‘best' within the pool of competitors."
What do the "best" do to achieve this extra measure of competitiveness? Yolton's presentation will identify and discuss the primary issues associated with the Top 3%, e.g., the "best" and the "rest." "It might surprise you to find that ‘soft' issues play an important and vital role in the transformation and journey from the ‘rest' to the ‘best,'" Yolton says. His presentation includes a case study analysis at Daishowa-Marubeni International's 500,000 metric tpy chemical pulp mill in Canada.
The opening keynote session also includes presentations by Bill Wick of American Industrial Metrology on "A Holistic Approach to Paper Machine Alignment" and Dave Cutnaw of SKF on "Maintenance and Asset Reliability Strategies—Developing a Foundation for Success."
More information about PaperCon 2013 and the OpEx Maintenance and Reliability Workshop, including registration procedures, is available online. Also available online is the 2013 OpEx Workshop program.
Back To Top
|
Members of the American Pulp & Paperworkers' Resource Council (PPRC), McGehee, Ark., USA, this past week visited Washington, D.C., to educate members of the U.S. Congress and administration officials on the impact of legislative and regulatory decisions both on the environment and on the families and communities that depend on forest products manufacturing for their livelihood.
The PPRC is a grassroots organization of hourly employees of the forest products industry who educate on issues that impact jobs in their industry. More than 80 PPRC members from across the U.S. visited Washington to discuss issues including the regulatory burden that is impacting American manufacturing, product labeling programs that benefit foreign manufacturers, the highest and best use of wood, and ensuring the competitiveness of the U.S. forest products industry.
In addition to meeting with their members of Congress, PPRC members met with administration officials of the White House and the Office of Management and Budget. Legislative and administration visits totaled 418 during the three days.
"At a time when everyone in our country is concerned about the loss of manufacturing jobs, our U.S. forest products industry is important to our nation's economy, representing about 5% of the total U.S. manufacturing GDP," said Patti Barber, PPRC chairwoman. "It employs 900,000 people—many in small, rural communities—and generates total wages of $50 billion in communities across our country."
Issues that PPRC members addressed included:
- USDA Biobased Market Programs. Forest industry products do not receive the Biopreferred Label even though they are nearly 100% biobased fiber content, while competitors' products can be as little as 25% and receive the Biopreferred Label. This gives preference to foreign competition, while excluding the mature U.S. forest products industry.
- Biomass/Renewable Energy. The forest products industry has always sought to use the "whole tree." Fibers from the tree are used to manufacture high-value pulp and paper products. The waste byproducts are used to create energy through co-generation. Free markets, not government mandates and incentives, should determine the highest value use of wood.
- Cumulative Regulatory Burden. EPA should examine the sustainability of its regulatory program to embrace a balanced approach so costly air and other regulations will protect the public's health while preserving family wage manufacturing jobs. Numerous pending regulations could cost tens of thousands of American manufacturing jobs and billions in capital expenditures.
- Clean Water. The Clean Water Act and its implementing regulations are one of our nation's most successful and wide-ranging environmental programs. The program regulates pollution at its source and involves a comprehensive federal and state regulatory system for issuance of permits and water quality standards. Issuing the administration's Draft Jurisdictional Guidance or regulations based on that guidance would radically impact the original intent of the Clean Water Act and would be detrimental to American manufacturing.
- Forest Roads. The PPRC supports legislation to preserve the treatment of forest roads as non-point sources under the Clean Water Act.
- Truck Weights. The PPRC supports legislation to allow states to increase the weight limit on trucks traveling on interstate highways.
"The vital work of the PPRC is to help elected and appointed officials understand how critical the forest products industry is to the health of the U.S. economy and the environment. We believe in balancing our environmental needs while securing existing manufacturing-based jobs in our local communities," Barber said.
According to the PPRC, the U.S. is one of the world's most diverse exporters of sustainable forest products. Exports account for about 15% of total U.S. forest products sales. The industry also generates economic benefits from indirect exports, such as domestic sales of paper, paperboard, and wood packaging materials used to package and transport goods exported by other U.S. industries.
More information about PPRC is available online.
Back To Top
|
TAPPI's newest publication, Tissue360° magazine, and TAPPI tissue experts have organized a comprehensive technical forum for PaperCon 2013 in Atlanta, Ga., USA, April 28 – May 1. Covering all aspects of tissue making, the Tissue Forum includes eight information- and data-packed sessions beginning Monday afternoon and continuing through Wednesday morning of PaperCon. The program is open to all full PaperCon registrants.
The Forum's eight sessions focus on tissue and hygiene product market trends and developments, the latest chemical, fiber, water, energy, control, and converting technologies, and explore new and emerging production technologies, with a special full-session look at yankee dryer issues and concerns. All material presented at Tissue Forum has been carefully selected and reviewed by TAPPI members with extensive tissue expertise, and most of the presentations include a written paper.
In Session T1 beginning after the lunch break on Monday, Esko Uutela of RISI presents a data-rich analysis of the global tissue business and trends in North America. Complementing Uutela's presentation, Lindsay Gervais of Poyry International examines the fiber side of the tissue industry with a detailed report on developing cost, quality, and sustainability issues in the global tissue arena. Session T2 on Monday afternoon covers "Chemistry Solutions for Tissue Making" with a paper by Yuping Luo of Kemira Chemicals that examines the newest generation of wet strength resins for towel grades, and a close-up look at new approaches to evaluating and enhancing tissue softness by Timothy Patterson of Ashland Water technologies..
Session T3 on Tuesday morning examines "Fiber Usage and Supply for Tissue" from four different fiber type perspectives. Fernando Pescatori Silva of Eldorado Brasil updates attendees on eucalyptus fibers. Xuejun Zou of FPInnovations provides a current overview of softwood kraft pulps for tissue making, and Medwick Byrd of North Carolina State University looks at nonwood raw materials as a possible fiber source for tissue and specialty products. The recycled fiber sourcing side is covered by Dave Anderson of SCA. Leading up to lunch, Session T4 explores "Water and Energy Strategies for Tissue," with presentations by Thomas Jenn of Kimberly-Clark on conducting tissue machine audits to reduce fiber losses and improve pulp yield, maximizing post pressure roll solids with advanced press fabric structures by Roger Banks of AstenJohnson, and engineering effective void volume in tissue production by Glen Harvey of Xerium Technologies.
Session T5 begins Tuesday afternoon with a focus on Premium Tissue Manufacturing Technologies. Dennis Jewitt of Metso Paper discusses advanced technologies for structured tissue products, Roberto Zane of Voith Paper explores premium tissue technologies that are enhancing the conventional tissue world, and tissue consultant Ed Graf reports on "air dried tissue" (ADT), an alternative to TAD and similar technologies. Session T6, completing Tuesday afternoon, provides a special review and analysis of the latest tissue control techniques. Doeung Choi of Ashland Water Technologies examines the use of process simulation in structured tissue and towel making, John Feola of Cristini North America presents a roundup of the latest process control tools to boost tissue machine performance, and Richard Falcoff of Alicona Corp. looks at 3D optical micro-measurement technology to quantify surface roughness with ISO traceable Sa values.
Wrapping up the Forum on Wednesday morning, Session T7 (CEU's provided) focuses directly on "Yankee Reliability," beginning with a presentation by Clive Butler of PMT on diagnosing surface chatter. Sam Archer of Nalco then looks more closely at the impact of chatter on yankee surface reliability, Jerry Vandoros of Kadant covers yankee doctor considerations for improving safety and reliability, and John Yolton of SKF explores reliability best practices in the global tissue industry. Session T8 on "Converting Efficiencies" features presentations by John Cork of Ibis International on process air filtration for tissue converting and Karl Hilden of Papertech on solving tissue production and converting problems using event capturing camera systems. Completing the Forum's final session on Wednesday morning, Futura analyzes key factors for enhanced converting performance.
More information about PaperCon 2013 and the Tissue360° Tissue Forum is available online, including online registration and the Tissue Forum program.
Back To Top
|
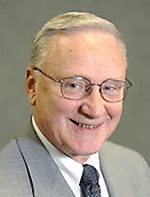 On March 6, from noon to 1:00 p.m., TAPPI will conduct a special Tissue Webinar. Instructed by Dr. Mike Kocurek, professor emeritus of Paper Science & Engineering at North Carolina State University and one of the world's most recognized educators in the pulp and paper industry, the webinar will present and discuss an overview of tissue making to achieve desired tissue properties, especially softness and bulk.
As Dr. Kocurek notes, achieving desired softness is dependent on many manufacturing variables, including fiber raw material (chemical, mechanical, recycled pulp), stock prep refining, wet end chemicals (debonders, softners, wet strength, etc.), tissue forming (conventional, wet molding), the method of drying (yankee, TAD), yankee coatings to achieve desired level of sheet adhesion to the shell, the creping doctor blade geometry and wear, calendering, and converting.
Professor Kocurek has taught paper properties and pulp and paper technology courses to students and in-mill short courses for technical personnel and operators for more than 40 years. He is the editor of 11 books, including the Pulp and Paper Manufacture series covering the entire field of pulp and paper. He has authored/co-authored 12 distance learning video courses, including Tissue Manufacturing Technology and the Introduction to Pulp & Paper series—again covering the entire field of pulp and paper
More information about the Tissue Webinar, including registration, is available online.
The webinar is a preview of content covered in TAPPI's two-day "Tissue Properties and Manufacturing" course being held April 27-28 in Atlanta, Ga., in conjunction with PaperCon 2013 (see article below). More information on the course is available online.
The webinar and course are excellent compliments to the Tissue360° Tissue Forum at PaperCon, an extensive program covering the latest tissue technologies, market trends, and runnability tips. More information on the Tissue Forum is also available online.
Back To Top
|
The TAPPI Tissue Properties & Manufacturing Course will be held on April 27-28, 2013, in Atlanta, Ga., USA, and co-located with 2013 PaperCon and the Tissue Forum. Both the Tissue Forum and Tissue Properties & Manufacturing Course are being sponsored by TAPPI's Tissue360° magazine.
This is a great opportunity to get the most out of your conference experience. The Tissue Properties course is designed for those who desire an introductory-to-intermediate level, comprehensive, and structured course on tissue properties, and the effect of manufacturing. This course precedes the Tissue 360° Forum at PaperCon, and is an excellent educational compliment to these technical sessions.
The course will be particularly helpful to non-technical professionals, technical process engineers, operators, suppliers, converters, and marketers with 0-5 years of experience in tissue manufacturing.
More information about the Tissue Properties & Manufacturing Course is available online.
Back To Top
|
Below is the latest listing of job openings in the TAPPI Career Center. The current listing includes job openings for a variety of positions including maintenance managers, electrical engineer, sales and service engineers, sales manager, mill manager, electrical engineer, executive director of a pulp and paper foundation, account sales/service reps, engineering intern, and R&D manager. Current, specific job openings at companies and locations in the TAPPI Career Center include:
Employer |
Title |
|
Albany International |
Applic. Eng. Forming Americas |
Wisconsin |
Albany International |
Sales and Service Engineer |
Florida |
Albany International |
Sales and Service Engineer |
NW Ore./SW Wash. |
Albany International |
Sales and Service Engineer |
B.C., Canada |
Boise Inc. |
PPS-Mgr., Production Plant |
Salt Lake City, Utah |
Boise Inc. |
Process Improvement Mgr. |
Georgia |
Boise Inc. |
R & D Technical Leader |
Idaho |
Boise Inc. |
Sales Manager |
Atlanta, Ga. |
Boise Inc. |
Maintenance Manager |
Salt Lake City, Utah |
Burrows Paper |
Electrical Engineer |
Mississippi |
Burrows Paper |
Maintenance Manager |
Pickens, Miss. |
Burrows Paper |
VP of Human Resources |
Little Falls, N.Y. |
Confidential |
R&D Manager |
Albany, N.Y. |
DuBois Chemicals |
Act. Sales and/or Service Rep. |
Green Bay, Wis. |
DuBois Chemicals |
Act. Sales and/or Service Rep. |
SW Ark./NE La. |
MeadWestvaco |
Human Resources Mgr.-Mill Ops. |
Cottonton, Ala. |
Michelman |
Global Tech. Mgr.-Paper Ctgs. |
Cincinnati, Ohio |
Michelman |
Reg. Sales Mgr.-Paper Ctgs. |
Cincinnati, Ohio |
Nalco |
Technical Sales Rep. |
Owensboro, Ky. |
NCR Corp. |
Chem. Eng./P&P-Paper/Ctgs. |
Georgia |
New Indy Containerboard |
Mill Manager (Paper Mill) |
Ontario, Calif. |
New-Indy Containerboard |
Maintenance Engineer |
Ontario, Calif. |
Norpac-Weyerhaeuser |
Engineering Internship |
Longview, Wash. |
Wash. P&P Foundation |
Executive Director |
Seattle, Wash. |
Wis. Inst. for Sust. Tech. |
Lab Director |
Stevens Point, Wis. |
Wis. Inst. for Sust. Tech. |
PM and Allied Lab Specialist |
Stevens Point, Wis. |
More information about these jobs is available online.
Back To Top
|
Market Roundup
Forest2Market, Charlotte, N.C., USA, reports that it has begun providing its Lake States subscribers with its Forest2Mill Delivered Price Benchmark, the first transaction-based market price report available in the region. According to the report, the Midwest delivered cost of total wood fiber (pulpwood and chips) was lower at the end of 4Q/2012 for all species. Aspen fell 2.8% over the course of the quarter, moving from $49.10 per ton in October to $48.89 per ton in November, and then to $47.73 per ton in December.
The delivered cost of hardwood fiber started the quarter at $51.51 per ton, fell to a quarterly low of $50.88 per ton in November, and then recovered nearly all that loss in December, ending at $51.31 per ton. Softwood total fiber remained steady in October ($52.78 per ton) and November ($52.77 per ton), but then fell to $52.04 per ton in December, a drop of 1.4%. All prices are in chip-equivalent tons (pulpwood less bark and accounting for fiber loss).
Peter Coutu, manager of Forest2Market's Midwest and Northeast office, worked with industry leaders in the Midwest throughout 4Q/2012 to develop a service that would meet the needs of consumers of wood fiber in the region. "It was great collaborating with them, and we look forward to expanding our relationships in the future as we improve and add to our Midwest product offerings."
"In this first report," said Coutu, "the data we supplied to our subscribers point to significant opportunities for adding value to the supply chain. The purpose of all Forest2Market products is to provide our customers with the market information they need to make better decisions and improve the performance of their businesses. We're confident that bringing the benchmark service that has been so successful in the South and the Pacific Northwest to the Midwest will bring a level of transparency to the market that will benefit all."
Coutu is currently working with industry leaders to develop a similar product in the Northeast.
Back To Top
|
Pellet exports from the two primary pellet-producing regions on the North American continent, the U.S. South and British Columbia, continued to increase in the 3Q/12 and reached a new record of 860,000 tons, according to North American Wood Fiber Review ( NAWFR), Seattle, Wash., USA, which compiles and publishes pellet trade based on customs data and surveys of pellet exporters each quarter. Shipments in the 3Q/12 were more than 70% higher than the same quarter in 2011. Pellet exports from the U.S. South have skyrocketed the past two years with a quadrupling to 485,000 tons from the 3Q/10 to 3Q/12. Canadian exports also have gone up the past few years, but at a slower pace.
Beyond the trade statistics tracking the rise of pellet export volumes, another spate of export pellet plant announcements detailed in the NAWFR emphasized the quickly growing trade relations that are being established between European power utilities and U.S. pellet producers. The most striking announcement came in mid-December when Drax, a U.K. power company, stated its intention to build two 450,000-ton pellet plants, one in the state of Louisiana and one in Mississippi. Most other export-oriented pellet plants, while invested in by European utilities, are separate U.S.-based entities, with supply agreements and MOU's defining the business relationship.
The three major European pellet import countries remain the U.K., the Netherlands, and Belgium, while Italy, Denmark, and Sweden are notably involved in pellet imports from North America, but on a much smaller scale. Denmark's Dong Energy utility, however, announced its intentions to switch to woody biomass at three of its coal plants, an action likely to add demand from the U.S. Southeast.
Announced U.S. South pellet export plants increased sharply in the second half of 2012. Export pellet facilities under construction, conversion, or redesigned will add an additional 1.7 million tons of capacity during 2013, as reported by the NAWFR. In addition to these plants that are already under construction, five additional plants have been announced, and if they are actually built on the disclosed sites, they would bring another 2.3 million tons of capacity into play by the end of 2014.
More information is available online.
Back To Top
|
Global market pulp NBSK (northern bleached softwood kraft) prices last month rose ˜$20-$25 per metric ton m/m, to $893 per metric ton, reports Mark Wilde of Deutsche Bank. Currently, prices are ˜$55-$60 per metric ton below year-ago levels. Overall shipments are up 3.0% y/y YTD, with much of that growth driven by strength in softwood (+4.1% y/y), Wilde notes.
Among the key regions, shipments to China are up 13.8% YTD. North America (-0.2% YTD) and Western Europe (-1.3% YTD) were both sluggish, Wilde says. The YTD operating rate for market pulp is at 92% (2011 = 90%), he adds. Current softwood inventories remain well below average at 25 days of supply. Hardwood is on the higher side of its historical average at 37 days of supply.
Back To Top
|
Pulp & Paper
Ahlstrom, Helsinki, Finland, this week said that its head office, as previously reported, will move to the Töölönlahti area in the center of Helsinki at the end of February. The company's current head office has been located in Salmisaari in the western part of Helsinki since the end of 2007.
Ahlstrom is a fiber-based materials company whose products include filters, medical gowns and drapes, diagnostics, wall coverings, flooring, labeling, and food packaging. The company has more than 3,800 employees in 28 countries on six continents.
Back To Top
|
Cascades, Candiac, Que., Canada, reports that its Antibacterial paper towel has been named a 2013 Edison Awards Finalist in the Consumer Packaged Goods: Cleaning Solutions category. The international awards program symbolizes the persistence and excellence personified by Thomas Alva Edison, inspiring creative minds to remain at the forefront of innovation, creativity, and ingenuity in the global economy. Award winners will be announced on April 25 at the Edison Awards Annual Gala, held in Chicago, Ill., USA.
The Cascades Antibacterial paper towel further reduces bacterial contamination and transmission by killing more than 99.99% of harmful bacteria almost instantly. By integrating a safe active ingredient into a dry format, the distinctly green-colored paper towel compensates for people's imperfect hygiene habits without changing the way they wash or dry their hands.
"We are honored to be considered for such a renowned award, among so many other great innovations," said Suzanne Blanchet, CEO of Cascades Tissue Group. "While our Antibacterial paper towel is a groundbreaking innovation, it also makes good common sense for human health. We believe the product will revolutionize the paper towel's role in proper hygiene because of its efficacy and because it doesn't require a change of habits. Now everyone can help control the spread of bacteria"
"More than any year, this year's slate of Finalists demonstrate the enormous value of teamwork, experimentation, consumer focus, market awareness and game-changing success," said Frank Bonafilia, Edison Awards' executive director. "It's exciting to see companies like Cascades continuing Thomas Edison's legacy of challenging conventional thinking."
Since 1987, the Edison Awards have recognized and honored some of the most innovative new products and business leaders in America. The ballot of nominees for the Edison Awards is judged by more than 3,000 senior business executives and academics from across the nation whose votes acknowledge the finalists' success in meeting the award criteria of concept, value, delivery, and impact.
Back To Top
|
Catalyst Paper, Richmond, B.C., Canada, has agreed, subject to court approval, to sell its approximately 50% interest in Powell River Energy Inc. and Powell River Energy Limited Partnership to Powell River Energy Trust, a Brookfield Renewable Energy affiliate, for $33 million. Powell River Energy Trust currently holds the other 50% stake in the Powell River Energy joint venture originally established in 2001.
"Sale of this energy asset to our joint venture partner enables a smooth operational transition, maintains reliable electricity supply for our Powell River paper mill under a power purchase agreement, and ensures we meet the terms of the plan of arrangement in a timely way," said President and CEO Kevin J. Clarke. All electricity generated by Powell River Energy will be sold to Catalyst under a power purchase agreement that expires in 2016 with possible extension to 2021 at Catalyst's discretion.
Pursuant to its plan of arrangement under the Companies' Creditors Arrangement Act ,which became effective Sept. 13, 2012, Catalyst is required to sell its stake in Powell River Energy and to distribute to certain unsecured creditors of Catalyst who did not elect to receive shares in Catalyst in settlement of their claims, their pro rata share of 50% of the net proceeds of the sale (which, given that many creditors elected to instead receive shares, will result in a distribution of approximately 40% of the net proceeds of the sale). The company will offer to purchase a portion of its Floating Rate Senior Secured Notes with the balance of the net proceeds. The sale is expected to complete in the first quarter of 2013 and is subject to various closing conditions. The company expects to apply to the British Columbia Supreme Court for approval of the sale in the next 10 days.
Catalyst Paper produces specialty mechanical printing papers, newsprint, and pulp. With three mills in British Columbia, Catalyst has a combined annual production capacity of 1.5 million metric tons.
Back To Top
|
Domtar Corp., Montreal, Que., Canada, is furthering its partnership with Recyclebank, New York, N.Y., USA, by supporting that organization's Recyclebank Green Schools Program that awards schools grant money for student projects that will make a positive environmental impact on their communities. Domtar will make more students' green projects a reality by contributing additional donation dollars, as well as awarding a year's supply of EarthChoice® Office Paper to the school with the most innovative project.
Each year, the Recyclebank Green Schools Program awards environmental project grants to schools in Recyclebank communities. Together, these schools, their students, and their communities work to encourage residents to donate points that Recyclebank transfers into real dollars for schools—thereby turning a community's green actions into funds for a local school. Since 2007, Recyclebank has granted close to $400,000 to more than 125 schools. This year, Domtar will award an additional $500 to every school that reaches 50% of its donation goal.
Since 2011, Domtar has been working with Recyclebank to increase awareness of the benefits of responsible paper production, use, and recycling. Past projects for Recyclebank members, sponsored by Domtar, have included educational gaming modules about responsible forestry, seasonal Web content about paper usage and recycling, and a rewards offer for EarthChoice Office Paper.
Back To Top
|
Duni, Malmö, Sweden, reports that it will enter into trade union negotiations with the intention to close one of three production units of its Sweden-based Rexcell Tissue & Airlaid AB subsidiary The unit, which produces and sells material focused on the hygiene products sector, is not profitable and the assessment has been made that acceptable profitability also cannot be achieved in the foreseeable future. The decision affects approximately 110 employees at its Rexcell subsidiary.
The closure of the production unit entails a one-off cost of SEK 83 million, which was incurred in the fourth quarter of 2012. However, it is calculated that Duni's net debt will fall in the long-term as a result of the closure. Sales from the production unit primarily involve external sales for the Tissue business area. The reduction in sales is not expected to have any negative impact on the Duni Group's operating income. It is estimated that the unit will be fully closed during the first quarter of 2014.
Back To Top
|
Arctic Paper S.A., Poland, presented a public takeover bid to shareholders of Rottneros AB, Stockholm, Sweden, this past November, and has extended the acceptance period to February 26. After Arctic Paper gained control of 51.3 % of the shares in Rottneros as of February 7, it requested that Rottneros convene an extraordinary general meeting of the company to elect a board of directors. However, since election of the board normally would occur at the company's annual general meeting (AGM) along with other usual AGM business, Rottneros' current board proposed that the AGM be moved forward rather than conducting the extraordinary general meeting. Arctic Paper has accepted this proposal.
Rottneros asked the Swedish Securities Council to consider whether this procedure, of bringing the AGM forward, complies with good stock market practice in this context. The Council confirmed that it does. Thus the AGM will be held on Friday, March 22, at 14.00 CET in the World Trade Center, Klarabergsviadukten 70, Plan 4, Section D, World Trade Center Conference, New York Room, Stockholm, Sweden.
Shareholders who wish to have an item of business dealt with at the AGM should present their proposals to the company no later than 12.00 CET, February 19, so they can be included in the meeting Notice. The Notice convening the AGM will be published in accordance with provisions of the Swedish Companies Act.
Back To Top
|
Södra, Sweden, has decided to divest its Tofte chemical pulp mill in Norway. The decision was made because of longstanding difficulties with unsatisfactory profitability at the mill, the company noted. Södra Cell's management has been given the task of creating a divestment plan for Södra's ownership of the mill, and the process to sell it has begun. Södra plans to end its involvement with the mill during the second quarter of this year.
"We have been attempting for some time now to make Södra Cell Tofte profitable. The commitment and expertise of the staff have kept quality and productivity at a high level, and they have fought valiantly to keep production costs low. Despite everything we've done, we are now forced to conclude that we have failed to reverse the trend," said Gunilla Saltin, acting CEO of Södra and president of Södra Cell.
The mill in Tofte was purchased by Södra in 2000. Its timber consumption is approximately 2 million cubic meters per year. Production capacity totals 400,000 metric tpy of chemical paper pulp. The mill employs 300 people.
Back To Top
|
Containerboard/Packaging
Boise Inc., Boise, Idaho, USA, this week announced key investments in the converting operations of its Packaging business. The largest capital improvement is the installation of a new 110-in. corrugator at the company's Central Texas Corrugated (CTC) sheet feeder facility in Waco, Texas, which is expected to start up in the third quarter of this year.
"We're excited about this new corrugator and several other investment projects, which are aimed at reducing operating costs, improving quality, and increasing production capabilities," said Dave Kunz, VP of Packaging. "Once installed, the new CTC corrugator will replace two existing corrugators, which will improve our operating efficiency and lower our costs. We expect the new corrugator will add 180,000 msf of low-cost production capacity, while simultaneously allowing us to reduce operating costs."
The company has also completed a recent rebuild of its corrugator at its converting facility in Salt Lake City, Utah. This rebuild has substantially increased the speed and throughput of the machine, reduced waste, and improved product quality. Additionally, the company has installed a new high-speed flexo machine at its converting facility in Wallula, Wash. This new machine replaces two older converting machines and improves efficiency through reduced set up time, along with lower operating costs.
"These investments are an important part of our plan to grow our Packaging business. We plan to continue making these types of investments in our Packaging system to meet changing customer needs, grow with our customers, and ensure that our facilities are safe, efficient, and cost competitive," said Alexander Toeldte, president and CEO of Boise Inc.
Boise Inc. produces a wide variety of packaging and paper products. Its range of packaging products includes linerboard and corrugating medium, corrugated containers and sheets, and protective packaging products. Boise's paper products include imaging papers for the office and home, printing and converting papers, and papers used in packaging, such as label and release papers.
Back To Top
|
Gorham Paper and Tissue, Gorham, N.H., USA, has expanded its capability to make packaging papers with up to 25% wet strength, color, and grease resistance, adding innovative functionality for demanding Quick Service Restaurant (QSR) and food applications.
"Gorham thrives on customization. A new customer experienced a supply chain disruption and quickly needed a colored, grease resistant paper with high wet strength for a carry-out food application. We knew we could do it," said Wayne Nablo, product manager. "The expectations for food packaging are great as the paper that holds your burger or fries must stay intact and look good while you eat. We worked side-by-side with the customer to engineer a colored paper to support its brand imaging objectives with high levels of wet strength and grease resistance for durability. We hit a home run in a matter of weeks."
Gorham recently announced its food packaging offering, which includes bleached and unbleached paper with basis weight options ranging from 18 lb.-133 lb. that incorporates grease resistance, wet strength, and the ability to add color. The products are ideal for a range of QSRs and other food packaging including wraps, pouches, bags, and liners. The company makes various bases used for waxing, coatings, and laminations. All products are FDA compliant for direct food contact and available with certification to SFI, FSC, and PEFC chain-of-custody standards.
Nablo added that "we are filling a void in the food packaging market with our unique ability to achieve wet strength with color and grease resistance. In this competitive market, brand owners are looking for an edge. Our specialized capability and product development focus drive market innovation. We are confident our announcement will impact the next generation of food packaging."
Gorham targets niche technical markets with a broad portfolio of custom-engineered specialty packaging, converting, engineered, and printing papers in addition to tissue and towel. Using scale and leanness as an advantage, the company challenges industry convention with its manufacturing flexibility, product development lead times, and go-to-market strategy.
Back To Top
|
Iggesund Paperboard, Sweden, reports that production of Invercote at its Iggesund, Sweden, mill in 2012 surpassed all of that facility's previous environmental achievements. Despite record-high manufacturing levels, emissions of environmentally harmful substances were lower than ever before.
"In the paper industry, the environmentally harmful emissions, above all to water, are usually proportional to production, that is, the more you make, the more you emit," explains Anna Mårtensson, environmental manager at Iggesund Mill. "But 2012 was a very positive exception for us. Even though our production was the most it's ever been, our emissions were the lowest ever—or at least, as far back as we have reliable measurement data."
Over the years, Iggesund has taken a variety of steps to reduce its emissions, the company notes. Fairly early on, the mill began separating out the leftover fibers that had passed through the pulping process with the aid of mechanical purification in sedimentation basins. In the 1970s, another step was taken with the construction of an aerated lagoon, where microorganisms clean the wastewater to a higher standard. In 2009, the mill added a third stage, chemical purification, in which the wastewater is treated in the same way that drinking water is treated.
"Now we can clearly see the effects of the third stage," Mårtensson says. "The oxygen-consuming substances have been greatly reduced and nutrients like phosphorus and nitrogen, which are so harmful to the marine ecosystem in the Baltic Sea, have been almost halved."
Paper industry operations are so large in scale that it often takes time to change course, Iggesund continues, adding that the Iggesund Mill is working in a strategic, targeted way to reduce its impact on the local environment. "Not one investment decision is made without first considering the environmental aspects," Mårtensson notes. "That is the question we constantly ask every time we discuss how to develop our production. Things don't always move as fast as our critics would like, but systematic work on these issues is what gives results over time."
The Iggesund Mill has been making paper pulp on the same site for almost 100 years and has been refining the pulp into paperboard for 50 years. Half a century ago, the seabed outside of the mill was dead and environmentally harmful emissions were considerable. Today, it is not possible to distinguish between fish that live close to the mill and fish from unaffected reference areas. Sensitive species like seals and eagles that have been absent for many years from the mill's vicinity are now back and increasing in numbers, the company explains.
Over the past two years, Iggesund Paperboard has invested more than EUR 340 million in switching to production based on renewable energy. At Iggesund Mill alone, the company has invested more than EUR 100,000 a day for the past 10 years, always with a focus on the environmental consequences of its investments.
Back To Top
|
Menasha Packaging Co., Neenah, Wis., USA, reports that its Folding Carton Group has expanded its capabilities while enhancing its ability to respond to accelerated lead times, thanks to a recent multi-million dollar capital investment. The $6 million investment will let Menasha be more flexible and responsive when supporting the brand merchandising objectives of its customers by allowing more variety and complexity in the solutions offered, the company noted.
"In today's marketplace, consumer packaged goods customers seek innovative solutions as well as support of their speed-to-market needs," said James Snyder, GM of Menasha Packaging's Folding Carton facility. "This investment reflects Menasha's commitment to delivering both creative and efficient merchandising solutions for our customers."
The Folding Carton Group's investment includes a Heidelberg Speedmaster XL 106 offset printing press, a Bobst EXPERTCUT 106 LER blanking diecutter, a MGL International Tape Applicator, and a Heiber & Schroder WP 800 High-Performance Rigid Window Patcher.
Menasha Packaging is a provider of graphic consumer packaging, merchandising solutions, corrugated packaging, food packaging, shipping containers, and material handling solutions, and is home of the Retail Integration Group.
Back To Top
|
Resolute Forest Products, Montreal, Que., Canada, might be in a position to decide what it will do with its Fort Frances, Ont., mill later this spring, according to a report this week by the Times Online, an Internet news publication of the Fort Frances Times newspaper. During a conference call last week, coinciding with the announcement of Resolute's preliminary fourth quarter and 2012 results, Resolute president and CEO Richard Garneau said the company currently is looking to reposition the mill in Fort Francis.
An investigation is underway as to what kinds of grades the company can use, Garneau noted. "In two, three, four months, we should be in a position to determine what the future of the mill is going to look like," Garneau said during the conference call. "We're certainly optimistic that we can reposition the mill," he added. "There's a good fiber base, as you know.
"There is a large co-gen—45 MWt—that we are now running at probably two-thirds of its capacity," Garneau continued, adding that he thinks the local mill has advantages going for it that the company can utilize. "But we have to find the right niche and also find a way not to spend too much money to convert it," he stressed.
Resolute indefinitely closed the kraft mill and PM 5 at Fort Frances this past November, affecting some 235 employees. The kraft mill had an annual production capacity of approximately 200,000 metric tons of market pulp, while PM 5 had an annual capacity of 105,000 metric tons of groundwood specialty printing papers. At that time, the company said that it would be exploring alternative product possibilities for its Fort Frances pulp mill, which was idled in a manner that would protect the equipment.
Back To Top
|
Smurfit Kappa's Hoya mill, Germany, has successfully started up its PM 2, following a major rebuild of the dryer section by Andritz, Graz, Austria. As a result of the rebuild, Smurfit Kappa, one of the leading producers of paper-based packaging in the world with more than 41,000 employees in 32 countries, reports that it now is able to achieve its goals for capacity, product quality, and energy consumption.
Andritz's scope for rebuilding the testliner and fluting machine at Hoya included:
- Complete dismantling of the old dryer section and rebuilding it with new frame and rolls; installation of a PrimeRun web stabilization system; installation of ropeless tail-threading (PrimeFeeder); replacement of the old size press with a PrimeCoat Film film press; and installation of a new energy-recovery hood. Even with the reduction in basis weight for the lighter weight packaging paper, capacity was increased by 17%. In addition, formation was improved and energy consumption was significantly reduced.
- For the project's second phase, PM 2's output was increased by another 17%. Andritz moved the reel and enlarged the after-drying section by adding PrimeDry ST and PrimeDry DT dryers along with a PrimeRun web stabilization system. The new components have a design speed of 1,200 m/min, at a width at reel of 7,600 mm.
Back To Top
|
New Products
Arjowiggins Graphic, France, has launched its Innovative 100% recycled, high speed Inkjet paper. The portfolio is designed to run on all inkjet digital presses including the latest generation of machines.
"This inkjet portfolio complements the rest of our digital product offering. We see this product range as an innovative and alternative solution for printers and their corporate clients. These specially engineered, premium quality, web inkjet papers are already creating profitable new markets in transpromo and direct mail, with increasing commercial print applications," said Jean Charles Monange, sales and marketing director, Arjowiggins Graphic.
The Cocoon and Cyclus Jet families provide a combination of high performance at full press speed and Improve color depth in combination with ink consumption reduction. The new portfolio includes a choice of coated and uncoated papers with a range of high whiteness and grammages.
Cocoon Jet Pro is an uncoated inkjet paper with HP ColorPRO Technology, treated, and pigmented for demanding, full color inkjet printing, 100% recycled, with very high whiteness (150 CIE). Certified by Rochester Institute of Technology.
Cocoon Jet is a high performing, treated, and pigmented uncoated inkjet paper for high speed color inkjet printing, 100% recycled, with very high whiteness (150 CIE). Awarded two diamonds by Kodak and qualified by Oce for dye and pigment machines.
Cyclus Jet Premium is a hybrid uncoated paper for laser preprinting, offset, and inkjet printing, ideal for black and white and limited color printing. The paper is 100% recycled, with a whiteness of 135 (CIE). Oce qualified for both pigment and dye machines
Cocoon preprint is a preprint qualified uncoated paper with perfect offset quality and a first step towards B&W and color printed variable data with digital printing systems. The paper is 100% recycled with a whiteness of 150 (CIE).
Cyclus preprint is a preprint qualified uncoated paper, perfect offset quality, and a first step towards B&W and color printed variable data with digital printing systems. The paper is 100% recycled with a natural shade of 90 (CIE).
Back To Top
|
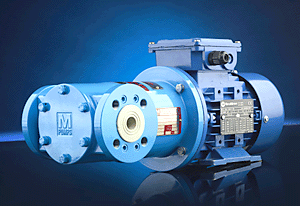 Pump specialists Michael Smith Engineers, UK, has recently added a new range of magnetically coupled vane pumps to the pumps and pumping systems it offers. The M Pumps series of vane pumps provide the important benefits of sealless, safe leak-free pumping and are available in plastic (polypropylene and PVDF) and stainless steel wet end construction. They also offer stainless steel multistage configurations for higher differential pressure applications.
In addition to their sealless, mag-drive design, M Pumps' three series of vane pumps are noted for their smooth, pulse-less, constantly accurate output, along with their ability to handle thin liquids at relatively high pressures. They are self-priming and some models can run dry for short periods. They are also able to compensate for wear through vane extension and have good suction lift capabilities. All M Pumps are designed for close-coupling to the motor, which minimizes the space footprint needed.
The pump illustrated (photo) is a new design that features a polypropylene pump head housed in a steel casing and is capable of withstanding system pressures up to 15 bar. It is designed for pumping water at six liters per min. at a differential head of 17 meters. The pump provides assurance of no leakage, thanks to its magnet coupling, smooth, pulse-less flows, and the capability to withstand high system pressures.
In terms of overall performance for the three series of pumps, the plastic pumps are capable of capacities up to 3,000 liters per hr., discharge pressures to 6 bar, and viscosities up to 10,000 cP. The stainless steel versions have similar output and viscosity handling capacities, but higher discharge pressures to 14 bar, while the multistage versions provide capacities up to 3,000 liters per hr., discharge pressures to 25 bar, and viscosities to 10,000 cP.
More information is available online.
Back To Top
|
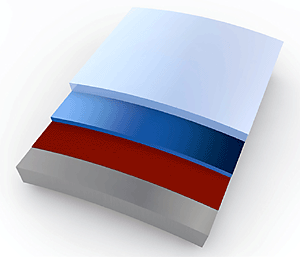 VoithPaper, Germany, has launched the NanoPro roll cover for calenders. The new roll cover provides a noticeable reduction of vibrations, the company notes. It is available for supercalenders, soft calenders, and multi-nip calenders.
The vibration resistant NanoPro cover provides reliable and consistent performance due to its unique attributes in areas where vibrations would normally restrict the performance of roll covers. In comparison with other conventional roll covers, it manages to further reduce vibrations, even under difficult conditions. Annual operating and maintenance costs are thus lowered. Also, the profile of NanoPro remains uniform due to its high level of wear and abrasion resistance, Voith emphasizes.
The multi-layer fiber-reinforced roll cover guarantees a uniform distribution of nanoparticles, Voith says. Customized components and the manufacturing process ensure that the NanoPro layers can withstand severe impact damages. NanoPro also distributes high compressive stresses evenly over the entire nip, providing the best possible sheet characteristics for gloss and smoothness and ultimate running behavior.
Back To Top
|
Published Pricing
Kemira, Finland, this week announced price increases on all list and off-list pricing for its acrylic acid and acrylamide-based polymer products in North America. The increases will vary depending on the product and will be effective for all deliveries on or after March 1, or as specific contract terms allow.
Kemira notes that while it continues to take actions to minimize the impact of increasing costs, it is necessary to adjust these prices to compensate for the rapid and recurring increases in key raw materials used in the manufacture of the polymer product lines.
Back To Top
|
SCA Containerboard, Sundsvall, Sweden, this week announced a price increase for its unbleached kraftliner of EUR 40 per metric ton in continental Europe and £ 35 per ton in the U.K. The increase becomes effective March 1.
SCA attributes the increase to the fact that containerboard markets remained strong at the end of 2012 and in the beginning of 2013. The demand in Europe, it notes, is healthy for both unbleached kraftliner and for testliner.
Back To Top
|
Following a recently announced coreboard price increase, Sonoco-Alcore S.a.r.l., Brussels, Belgium, this week announced that it will increase prices of all tube and core-related products by 5.5%. The price increase becomes effective March 1.
"This price increase is in response to lower European volumes and the continued inflationary cost pressures we experience in Europe, especially for energy, freight, chemicals, and labor," said Adam Wood, VP, Sonoco-Alcore.
Sonoco Alcore S.a.r.l. is wholly-owned by Sonoco, Hartsville, S.C., USA, and operates 29 tube and core plants and five paperboard mills in Europe.
Back To Top
|
People
Tembec, Montreal, Que., Canada, reports that Yvon Pelletier, EVP, Specialty Cellulose and Chemical Group, will be leaving the company, effective February 22, and that Christian Ribeyrolle has been appointed EVP, Specialty Cellulose. Ribeyrolle, who holds a chemical engineering degree from l'École Nationale Supérieure de Chimie de Clermont-Ferrand in France, has been with Tembec for 10 years.
Ribeyrolle joined the company in 2003 as manager of the pulp mill in Tartas, France, with an annual production capacity of 150,000 metric tons. In 2008, he was promoted to director of sales, Specialty Cellulose, and in 2009, he became SVP, Specialty Cellulose, and president, Tembec SAS (France).
Under Ribeyrolle's leadership, Tembec has invested more than EUR 50 million in the Tartas site, transforming its process and product mix. When he joined Tembec, specialty cellulose accounted for just 20% of production at Tartas. Today, the Tartas site manufactures 100% specialty cellulose and has become the company's best performing asset.
"Christian is a key member of Tembec's senior management team. He has led the transformation of the Tartas mill, making it a very profitable operation with a reputation that is recognized internationally in the specialty cellulose market. Christian's deep expertise, his more than 25 years of experience in the industry, and his skills as a manager have served to position Tembec among the global leaders in the specialty cellulose market. We are very pleased to count on his contribution to our executive team," said James Lopez, president and CEO of Tembec. "Christian has been a tremendous asset in the development of the specialty cellulose component of Tembec's business portfolio," he added.
"I would like to take this opportunity to thank Yvon Pelletier for his 32 years of service and recognize his commitment to the company during his tenure with Tembec. We wish Yvon well," Lopez said.
Currently, a $190-million investment project is underway in Tembec's Temiscaming, Que., Canada, specialty cellulose facility. A $120-million Phase 2 to this project is now under study. This investment will increase annual production of green electricity by up to 50 MW, reduce sulfur dioxide emissions by 70%, increase Temiscaming's annual production capacity of specialty cellulose, as well as make Temiscaming one of the world's lowest-cost specialty cellulose manufacturing facilities.
The overall project will increase Tembec's annual production capacity of specialty cellulose from the current 310,000 metric tons to 345,000 metric tons. The Temiscaming facility's production capacity will increase from the current 160,000 metric tons to 195,000 metric tons. Tembec's Tartas, France, specialty cellulose facility has a current production capacity of 150,000 metric tons.
Back To Top
|
The Newark Group, Cranford, N.J., USA, has appointed Paul Spitale VP of Sales for Converted Products. In this newly created position, Spitale will preside over the sales activities of both Newark Paperboard Products and Newark Custom Paperboard (formerly BCI).
Spitale previously was SVP of Sales with Sony Corp., where he was employed for 25 years. As a member of Sony's Management Committee, Spitale delivered high levels of growth and profitability with the company's retail partners. He played a pivotal role in the launch of the WEGA television. Spitale won the Sony Samurai Award twice as well as the CMO Award for outstanding marketing execution. During his time with Sony, he also authored A More Valued Success, a motivational book.
"We are very pleased to have Paul join The Newark Group," said Jim Carbine, SVP of Newark Custom Paperboard. "His ability to build new territories and expand opportunities is vital to the growth of the company."
Back To Top
|
Fortress Paper Ltd., Vancouver, B.C., Canada, has appointed Yvon Pelletier president of its dissolving pulp business, effective February 25. Pelletier has more than 30 years of experience in the pulp and paper industry and has held leadership roles in technical, operational, and commercial areas. Prior to joining the Fortress group, Pelletier was EVP of Tembec Inc., and president of its Specialty Cellulose and Chemical Group (see Tembec article below). As a senior executive at Tembec, Pelletier served as GM of various dissolving pulp and kraft pulp operations, and acted as SVP of the company's Kraft Pulp Division, overseeing three mills in Canada and two in France.
Pelletier's role at Fortress will include leading the company's dissolving pulp business, which currently operates through the Fortress Specialty Cellulose Mill and the Fortress Global Cellulose Mill. He replaces Peter Vinall, who has been with the corporation since 2010.
Chadwick Wasilenkoff, CEO of Fortress Paper, said that "we are very pleased to have someone of Yvon Pelletier''s extensive experience joining our team. Yvon has an intimate knowledge of the dissolving pulp industry, having lead complex mill operations and implemented many capital expenditure and upgrade projects, and has a proven record of success in improving business performance. We believe that Yvon''s appointment will provide enhanced strategic leadership to our dissolving pulp business, and that he possesses the technical skills and practical local expertise that will be a significant benefit in advancing our dissolving pulp projects and business objectives."
Fortress Paper operates internationally in three distinct business segments—dissolving pulp, specialty papers, and security paper products. The company operates its dissolving pulp business at the Fortress Specialty Cellulose Mill located in Canada, which is also in the process of expanding into the renewable energy generation sector with the construction of a cogeneration facility. The company also is seeking to expand its dissolving pulp capacity with the recent acquisition of the Fortress Global Cellulose Mill at Lebel-sur-Quévillon, Qué., which it intends to convert into a dissolving pulp mill and where it intends to re-start the cogeneration facility.
Fortress operates its specialty papers business at the Dresden Mill in Germany, where it is a producer of specialty non-woven wallpaper base products. The company operates its security paper products business at the Landqart Mill in Switzerland, where it produces banknote, passport, visa, and other brand protection and security papers, and at its Fortress Optical Facility in Canada, where it manufacturers optically variable thin film material.
Back To Top
|
TAPPI News
TAPPI Annual Business Meeting /Teleconference
TAPPI Headquarters
15 Technology Parkway S., Suite 115
Peachtree Corners, Ga., 30092 USA
March 12, 2013
1:00 pm - 1:30 pm EST
As a corporation, TAPPI must hold an annual Business Meeting. That meeting will be held March 12, 2013, via teleconference. Any interested TAPPI member may join us for a brief report on association business -- Larry N. Montague, TAPPI president and CEO
1. Opening Remarks/Antitrust Reminder - Norman Marsolan, TAPPI Board chair
This call will be held in accordance with TAPPI's Antitrust Policy and Procedures.
TAPPI's aim is to promote research and education, and to arrange for the collection, dissemination, and interchange of technical concepts and information in fields of interest to its members. TAPPI is not intended to, and may not, play any role in the competitive decisions of its members or their employees, or in any way restrict competition among companies.
2. Financial Report - Larry Montague, TAPPI president and CEO
3. Board Transition - Norman Marsolan, TAPPI Board chair, Tom Garland, TAPPI Board vice chair
4. Adjourn - Norman Marsolan, TAPPI Board chair
Please contact Mary Beth Cornell, +1 770-209-7210, for more information, including the teleconference number and password.
Back To Top
|
Two special TAPPI webinars on February 21 and March 13 provide inside previews of PaperCon 2013 in Atlanta, Ga., USA, April 27 - May 1
Webinar No. 1
Innovation in Safety: The Leading Edge of Leading Indicators
Thursday, Feb. 21, 2013 - 12:00pm - 1:00pm EST
Register to attend.
Learn how statistical analysis and data management can be used more effectively for safety performance management through a demonstration of a numerical system of leading indicators that can predict potential workplace accidents, helping mills to prevent them. Based entirely on objective, measurable data, this predictive system is an excellent resource for proactive safety management.
This discussion will focus on identifying, quantifying, and combining measurable parameters into a safety performance model that clearly defines both environmental risk and individual risk in a way that affords us necessary clues for an effective accident prevention program. Learn more.
Webinar No. 2
Increasing Paper Machine Agility with a Novel Grade Change Concept
Wednesday, March 13, 2013 - 12:00pm - 1:00pm EST
Register to attend.
A narrow grade mix and long grade runs were once common. Not today. Most machine make a wider set of products with many grade changes. A new grade transition concept makes such machines more competitive by increasing the stability and agility of the line. Unlike traditional programs, the new grade change concept replies on normal quality controls to move the machine from one grade to the next, quickly and smoothly in a closed loop. Learn more.
Back To Top
|
Overview of Tissue Manufacturing for Softness and Bulk Webinar
Wednesday, March 6, 2013 - 12:00 pm - 1:00 pm EST
This introductory level webinar will give you an overview of basic manufacturing factors, terminology, and operations that will affect and contribute to softness and bulk.
Topics will include:
- The Basic Components of Softness
- Fiber Raw Materials
- Chemical Additives
- Refining
- Tissue Formingand Pressing
- Yankee and Through-Air-Drying (TAD)
- Creping Operations
- Calendering and Converting.
This is a free webinar, but you must register to attend.
Back To Top
|
Tissue360 Forum @ PaperCon 2013
Monday, April 29 - Wednesday, May 1
Atlanta, Ga., USA
TAPPI's new Tissue publication, Tissue360o magazine, and TAPPI tissue experts have organized Tissue360 Forum, a comprehensive technical forum covering all aspects of tissuemaking. You will hear about the latest tissue technology, market trends, and pick-up some runnability/operational tips. The program is open to all full PaperCon registrants.
Program Overview:
Hygenic Products Market Overview
Session Chairs: Ken Patrick, Tissue360o
Chemistry Solutions for Tissue Making
Session Chair: Gary Furman, Nalco
Water and Energy Strategies for Tissue
Session Chair: Tom Jenn, Kimberly-Clark
Premium Tissue Manufacturing Technologies
Session Chair: Soren Eriksson, Metso
Tissue Controls and Measurement
Session Chair: Rene Naranjo, AstenJohnson
Yankee Reliability (CEUs provided)
Session Chair: Al Coons, Clearwater Paper
Converting Efficiencies
Session Chair: Kevin Brennan, Ashland Water Technologies
See the full Tissue360 Forum program.
PaperCon will take place April 27 through May 1, 2013 in Atlanta, Ga., USA. Designed by industry professionals, PaperCon brings together CEOs, mill managers, superintendents, scientsits, process engineers, and suppliers for the largest pulp and paper technical program in the world. No other such event provides such a comprehensive program, networking opportunites, and trade fair among such a distinguished group of industry leaders.
Learn more about PaperCon 2013.
Back To Top
|
The TAPPI Tissue Properties & Manufacturing Course will be held on April 27-28, 2013 in Atlanta, Ga., co-located with PaperCon 2013 and the Tissue Forum. This is a great opportunity to get the most out of your conference experience. This Tissue Properties course is designed for those who desire an introductory-to-intermediate level, comprehensive, and structured course on tissue properties and the effect of manufacturing. The course precedes the Tissue Forum at PaperCon 2013 and is an excellent educational component to these technical sessions.
This course will be particularly helpful to non-technical professionals, technical process engineers, operators, suppliers, converters and marketers with 0-5 years of experience in tissue manufacturing. Go to the course website to learn more.
Back To Top
|
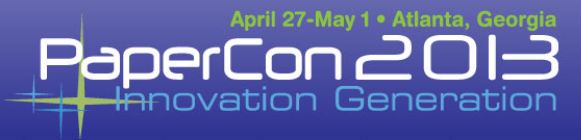
The highly-regarded Executive Panel on Monday, April 29, will illuminate how industry leaders are thinking and driving innovation in their companies.
See who's speaking.
Designed by industry professionals, PaperCon (April 27 - May 1 in Atlanta, Ga., USA) will bring together CEOs, mill managers, superintendents, scientists, process engineers, and suppliers for the largest pulp and paper technical program in the world. No other event provides such a comprehensive program with networking opportunities and trade fair among such a distinguished group of industry leaders.
Back To Top
|
Gopal Goyal often notes that it is the connections he made through membership in TAPPI that really helped launch his career. "I kept telling people that I have gotten more out of TAPPI than TAPPI has gotten out of me." Having joined back in 1985 while a graduate student in pursuit of an advanced degree in the pulp and paper field, Gopal attended his first TAPPI pulping conference and was deeply impressed with the depth and breadth of knowledge he found under a single roof.
"You could approach any of these experts and have a technical discussion, which helped me tremendously in focusing my graduate research," he said. That initial meeting led to nearly 30 years of active involvement, including an array of voluntary leadership positions. Since those early days, he has consistently found TAPPI to be a great venue for making connections with leading industry experts and establishing a global network of contacts. He also notes that the active volunteer role he pursues at TAPPI to this day helped him to develop and apply leadership and teambuilding skills at his job.
Find out more by reading this month's Member Spotlight.
Spotlight participants are recommended by fellow members and staff. If you wuld like to nominate a member just send their name (or names) to MemberSpotlight@tappi.org. We will forward a Spotlight Questionnaire to fill out and return.
We look forward to seeing you in the Spotlight!
Back To Top
|
The highly regarded panel on Monday, April 29, will illuminate how industry leaders are thinking and driving innovation within their companies.
See who's speaking.
Designed by industry professionals, PaperCon will bring together CEOs, mill managers, superintendents, scientists, process engineers, and suppliers for the largest pulp and paper technical program in the world. No other event provides such a comprehensive program, networking opportunities, and trade fair among such a distinguished group of industry leaders.
Back To Top
|
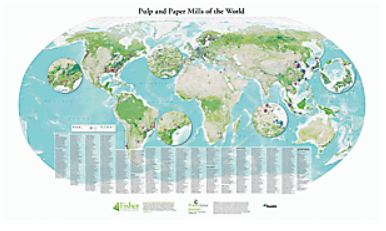
One of TAPPI's most exciting new products is the wall-sized, laminated 2013 Pulp & Paper "Mills of the World" Map.
A winning combination of high quality print and paper stock along with brilliant colors makes this the perfect map to frame and hang in your office. The "Mills of the World" map features include:
- Every mill in the world producing 50 tpd or more
- Major greenfield projects
- Design elements showing mill characteristics, forest cover, and typography
- 3 ft. x 5 ft. (or 0.99 x 1.5 meters) .
Each map will be shipped in a protective tube, ready for display.
Don't miss out on this popular item. Order your Pulp & Paper "Mills of the World" Map today.
Product code: 12PPMAP
Member Price: $299.00
Non-Member Price: $319.00
Back To Top
|
The Introduction to Traditional and Emerging Printing Technology Course will be co-located at the 2013 PaperCon Conference, April 27-29, 2013, in Atlanta, Ga., USA.
This is an introductory course on printing methods and applications, designed for those who need to understand print quality, attend print trials, trouble shoot print problems or are generally new to printing operations. It will be taught by printing experts from TAPPI's Coating and Graphic Arts Division and is an excellent complement to the Coating Program at PaperCon.
As an added bonus, the course will include a tour of Hewlett-Packard's new state-of-the art facility where production laser and inkjet presses will be demonstrated.
Course attendees may also join the Coating and Graphic Arts Opening Session where printing visionary Frank Romano is giving the keynote address. Learn more and register online.
Back To Top
|
The Virginia-Carolina TAPPI Local Section is hosting its Winter Conference in Richmond, Va., USA, on Monday, February 25, with a program focus on "Boiler MACT and Bioenergy Enhancement, Policy, and Standards." Speakers include Dr. Justin Baker of RTI International, Roger Leimbach of Metso Automation, Phil Sparks of Save Environmental, and Dr. Med Byrd, Director of the Department of Forest Biomaterials, North Carolina State University.
The conference will be held at the Hyatt Place Richmond Arboretum. Registration is open and table-top exhibit space can be purchased. The agenda and registration forms are both available online.
Back To Top
|
PaperCon Programs Now Available
Customize your learning and networking experience at PaperCon to best fit your professional needs. Bring back ideas, innovation that will help you be more effective and efficient.
Papermakers program will give you everything you need to know about paper machine performance evaluations, running mill trials, and product certification.
Eight peer-reviewed Coating sessions focus on scientific developments and practical tips. Highlighs include opacity enhancement with Ti02 and advancements in barrier coating.
PIMA Management sessions provide excellent insight for mill managers, production managers, and executives. This year's sessions will help you develop effective labor/management relationships and show you how to motivate today's employees.
The Tissue360 Forum provides a comprehensive peer-reviewed technical program unlike any other. You will learn about fiber, water, and energy savings, the latest softness and strength additives, and forming concepts.
The OpEx Reliability Workshop will help you improve reliability and maintenance in your mill. Operator driven reliability, alignment, education, and mill processes will be addressed by leading reliability experts.
The Young Professionals Program (YP) offers those new to the industry an unbelievable opportunity to gain basic industry knowledge and meet experienced industry leaders.
Back To Top
|
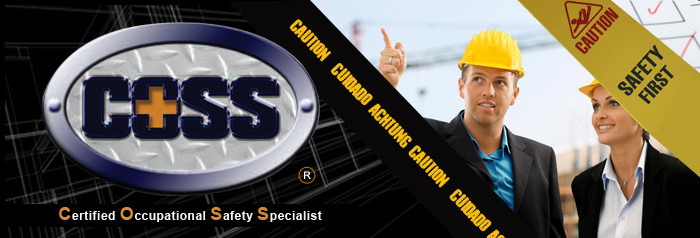
Are you ready to go further, faster in your safety career? The Certified Occupational Safety Specialist (COSS) class can take you there.
The COSS Class is Unique
Not only will you learn how to read and understand the OSHA 1910 and 1926 CFRs and help your company avoid OSHA citations that cost millions of dollars, but more importantly, by learning how to work safely on a job site, you can teach your company how to lower fatalities and near misses. Almost 47% of COSS graduates responding to our survey indicate that, since taking COSS, their company's injury rate and/or OSHA recordables have decreased by as much as 25% and others attest to as much as a 100% decrease!
Request a Course Outline & Syllabus for more information.
The class also addresses the psychology of safety, the true cost of an accident, hazard recognition, how to start up a health and safety program, behavior based safety, system safety, and much more!
What Will You Receive?
Upon successfully completing the class, you will obtain your national Certified Occupational Safety Specialist (COSS) designation, your OSHA 10-hr. card of completion in construction, and your OSHA 10-hr. card of completion in general industry.
National Program Recognitions
COSS is currently one of only 37 programs in the world recongnized and accredited by the American Petroleum Institute (API). In addition, the certifying body for construction education for colleges, universties and technical/trade schools, American Council for Construction Education (ACCE), has also recongnized our program. COSS is the only non-degree program to receive this national endorsement. Lastly, COSS has been established as a mandatory course for students in the Construction Management Program at Louisiana State University.
Program Content
The program consists of 40 hr. of hands on, face-to-face learning, which is delivered by an Authorized OSHA outreach trainer in both construction and general industry. Case studies and workshops are used extensively to bring learning objectives into focus. Guest speaker from areas such as OSHA and other governmental agencies are used to enhance the learning experience. Student presentations, daily quizzes, practical reviews, and a comprehensive final exam will allow you to demonstrate your competency.
Prerequisites
The only prerequisite for the COSS class is you must have a high school diploma or equivalent. In each class, we tend to have a mix of non-experienced, first time safety persons, as well as safety professionals who have been in the safety field for 20+ years. But, we have learned that regardless of the numbers of years of experience you have in safety, everyone leaves the COSS class with a wealth of knowledge!
Visit the COSS website for FAQs, testimonials and a list of clients that have taken COSS.
Register now.
If you would like more information on the COSS program, contact Beth Gordon at 877-610-2677
Back To Top
|
A Call for Papers is underway for these three co-located events:
The 2013 TAPPI PEERS Conference, September 15-18, 2013 in Green Bay, Wi., USA has announced the Call for papers. PEERS is the perfect forum for paper industry professionals both to acquire practical operating insights and to network with industry peers in technical sessions, tutorials, round tables, new technlogy sessions and workshops. Suggested topics and more information now available. Deadline for abstracts is March 1, 2013.
An Invitation to Present has been announced for TAPPI's 2013 International Bioenergy and Bioproducts Conference (IBBC), September 18-20, 2013 Green Bay, Wi., USA. IBBC is the only event dedicated to advancing biorefineries in the forst product industries, and for the first time will be ehld in the Midwest, providing an expanded focus on activities in Wisconsin and surrounding areas. Suggested topics and more information now available. Deadline for abstracts is March 1, 2013.
The International Program Committee for the 10th Research Forum on Recycling announces an Invitation to Present at the 2013 event, September 16-18, 2013 in Green Bay, Wi., USA. Research engineers, scientists, and practitioners are encouraged to submit presentation proposals on all aspects of recycling technologies and operations. Submissions describing both basic and applied research results will be considered. This year's event will provide participants an extraordinary opportunity to hear about the latest in recycling research, discuss mill operation issues, network with peers, and identify future research needs of the recycling community. Deadline for abstracts is March 1, 2013. Learn more.
Back To Top
|
David Schirmer, Vice President and General Manager of Hearst Enterprises will Keynote at Tappi's Shipping Receiving and Warehousing Workshop this April in Nashville. Schirmer is responsible for paper procurement for divisions of Hearst Corp. including Hearst Magazines and Hearst Newspapers and is one of principles of Newsprint Purchasing LLC.
Tappi's SRW Workshop, taking place April 9-10, focuses on reducing in-transit paper roll damage through collaborative discussions and best practices. Learn more about SRW.
Back To Top
|
Paper Roll Damage Expensive?
Attend TAPPI's SRW Workshop this April and be a part of this dedicated group of mills, carriers, warehouses and printers as they collaborate to reduce in-transit damage to rolls of paper.
The Shipping, Receiving and Warehousing Workshop is an affordable working meeting with presentations and collaborative discussions, engaging keynote speakers, and great opportunities for networking. It's something you can't afford to miss.
Why attend?
- Keynote Presentation by Dave Schirmer, Vice President and General Manager of Hearst Enterprises responsible for paper procurement for divisions of The Hearst Corporation.
- Presentations provided by experts from the class 1 railroads, intermodal providers, warehouses, shippers and dunnage manufacturers with extensive experience and practical background knowledge.
- Practical information sharing by all parties in the paper manufacturing supply chain in an interactive environment
- Excellent networking opportunity - paper buyers, paper companies, carriers, securing / damage prevention specialists, block and bracing manufacturers, safety experts - all under one roof.
Learn more about the Shipping, Receiving and Warehousing Workshop.
Back To Top
|
The International Mechanical Pulping Conference, sponsored by PI, TAPPI, PAPTAC, SPCI and PTF, will be held on June 3-5, 2014, in Helsinki, Finland. IMPC 2014 is a major part of PulPaper, one of the world's most premier pulp and paper exhibitions, coinciding with the 100th anniversary of PI, the Paper Engineers' Association.
The Conference Program Committee invites you to submit papers on the following topics:
- Energy saving in Mechanical Pulping process
- New applications and innovations
- Raw materials in Mechanical Pulping
- Advanced Mechanical Pulping technologies e.g.
- Process control and simulation
- Bleaching
- Water management and effluent treatment
5. Mill operations update e.g.
- Production cost saving technologies (energy and chemicals)
- Improving mechanical pulping business potential
6. Mechanical pulps in paper and board.
Authors interested in presenting a paper or a poster on these topics should submit an extended abstract (˜500 words) to impc2014@vtt.fi. Abstracts are due by February 28, 2013. Authors will be notified of acceptance by May 31, 2013 and final manuscripts are due March 31, 2014.
If you have any questions, please contact Sari Liukkonen, Chair of the Program Committee at +358 40 586 0384, or by e-mail at impc2014@vtt.fi.
Back To Top
|
TAPPI and NCSU are partnered again for the first of three introductory level courses for industry professionals that cover the entire pulping and papermaking process.
The 2013 Hands-On Workshop for Pulp and Paper Basics takes place March 4-8 at North Carolina state University in Raleigh, N.C., USA.
This workshop fills to capacity quickly, so reserve your place now so that you can:
- Find out how different processes affect paper properties
- Perform hands-on laboratory experiments to support your understanding of the process
- Run a pilot plant paper machine
- Solidify your knowledge from close interaction with professionals in small, interactive groups.
Be among the first 32 people to register for this five-day workshop, and you'll gain an invaluable overview of pulping, bleaching, chemical recovery, recycling, papermaking, and converting. You'll receive course notes, a CD, a polo shirt, and 3.7 CEUs!
This workshop is ideal for new process engineers, manufacturing operators and technicians, sales and service personnel, machine operators, and maintenance personnel -- everyone who wants a better understanding of the pulp and paper business.
Don't wait too long to register for the March 4-8 workshop. Two additional courses are being offered at NCSU in June and October for those who aren't able to attend the first event.
Back To Top
|
Strengthen your understanding of the corrugating process, and linerboard and medium performance properties and manufacture with TAPPI's Linerboard Medium & Corrugated Box Manufacture Course, April 15-16, at the Holiday Inn in Neenah, Wis., USA.
With an emphasis on helping attendees improve corrugating box performance and runnability, this popular introductory to intermediate level course is ideal for process engineers and operators in linerboard and medium manufacturing facilities and corrugating and converting plants.
Instructors Michael J. Kocurek, Professor Emeritus, of Paper Science & Engineering at North Carolina State University, and Jon Porter, Senior Trainer / Process Specialist for Fosber America will address:
- The Corrugated Session (1/2 day) will cover how to achieve the strongest bond and highest quality combinerboard. You'll learn about (1) the equipment, (2) starch, (3) corrugated process technology, and (4) importance of linerboard and medium properties and runnability.
- The Properties and Testing of Liner and Medium session (1/2 day) covers the tests, what they mean, and how the properties of the board affect the tests.
- The Pulp and Paper Mill Operations session (1 day) will cover the technology of the pulp and papermaking processes, and how they affect the quality, properties, tests, and runnability of the liner and medium.
View the proposed course schedule.
Register by March 15 to take advantage of the Early Bird registration discount. Join TAPPI or renew your membership for the best rates!
Back To Top
|
The TAPPI Troubleshooting "Flexos" and "Die Cutters" Sustain Board Caliper & Improve Printing Course is scheduled for April 16-18, 2013, in Neenah, Wis., USA. Join industry veteran Dick Target, founder of On Target Consultants, as he helps attendees identify and address downtime issues and develop a better understanding of machine calibration and how to maintain proper board caliper during the converting process.
Target will use an easy to understand format to help attendees improve the basic manufacturing process. Topics will include: methods to minimize caliper loss in the converting process; one-box set-up techniques; and waste reduction techniques. View the course schedule.
Take advantage of the Early Bird Registration discount before March 16. Join TAPPI or renew your membership for the best rates!
Back To Top
|
PaperCon Session: Insights into Effective Labor/Management Relationships
Organized by PPMA and PIMA
Monday, April 29, 2013 - 1:30-3:00pm
Many companies have embraced innovative processes for managing labor-management relationships. These processes result in better communication, more effective problem solving, and alignment around shared business goals. Attend this session at PaperCon, part of the PIMA Management Program, and hear examples of effective labor/management teams that yield positive business results. Panelists will share first-person testimonials and stories of challenge, frustration, and success.
Moderator:
Roger Hagan, Zilkha Biomass Energy
Panelists:
Steve Myers, mill manager, Thilmany Paper, Kaukauna, Wis.
Peter Tantalo, operations manager, RockTenn Solvay, Syracuse, N.Y.
Mike Rayome, director, human resources, Graphic Packaging, Wausau, Wis.
Karl Christianson, mill manager, RockTenn, Stevenson, Ala.
PaperCon will take place April 27 through May 1, 2013, in Atlanta, Ga, USA. Designed by industry professionals, PaperCon brings together CEOs, mill managers, superintendents, scientists, process engineers, and suppliers for the largest pulp and paper technical program in the world. No other event provides such a comprehensive program, networking opportunities, and trade fair among such a distinguished group of industry leaders.
Learn more about PaperCon 2013.
Back To Top
|
By: Jerome M. Gess and Paul H. Wilson
This book takes the reader through the process of making paper, pointing out where interruptions can occur and where elements added to the system can cause problems in that part or subsequent parts of the papermaking process. The aim of this book is to give papermakers and those involved in the papermaking process the information required to allow them to understand how to track down and solve problems at their source rather than where the problems surface.
Troubleshooting the Papermaking Process.
View the Table of Contents.
Product Code: 0101R298
Member Price: $106.00
Non-member Price: $161.00
Back To Top
|
|
|
TAPPI Over the Wire | 15 Technology Pkwy. S. | Norcross, GA 30092 USA | Voice: 770.446.1400 | Fax: 770.446.6947
|
 |