 |
|
Weekly Spotlight
NewPage Corp., Miamisburg, Ohio, USA, has successfully completed its financial restructuring and has officially emerged from Chapter 11 bankruptcy protection pursuant to its Modified Fourth Amended Chapter 11 Plan
Learn More...
|
SCA, Philadelphia, Pa., USA, makers of the Tork® brand of away-from-home tissue products, has announced the publication of its third annual Tork Report, a comprehensive look at sustainability issues and hygiene practices among North American businesses and consumers
Learn More...
|
The newly formed TAPPI Process & Project Engineering Committee is conducting a survey to better determine what capital project strategies today's pulp and paper mills are implementing to stay in-tune and competitive under progressively lean operating conditions
Learn More...
|
Below is the latest listing of job openings in the TAPPI Career Center
Learn More...
|
Market Roundup
Total U.S. kraft paper shipments in November totaled 120,400 tons, a decrease of 11.2% compared with the prior (October 2012) month
Learn More...
|
U.S. industry consumption of recovered paper this past November was 2.36 million tons, which is 5% lower than in October 2012
Learn More...
|
Total U.S. printing and writing (P&W) paper shipments decreased 4% in November, compared with November 2
Learn More...
|
Pulp & Paper
Catalyst Paper, Richmond, B.C., Canada, reports that the sale of its Elk Falls site in Campbell River to Pacifica Deep Sea Terminals did not close and the sale agreement has been terminated
Learn More...
|
Clearwater Paper Corp., Spokane, Wash., USA, has completed the next phase of its newest tissue facility at Shelby, N.C., with the startup of a new through-air-dried (TAD) tissue machine
Learn More...
|
NewPage Corp., Miamisburg, Ohio, USA, has announced members of its new board of directors
Learn More...
|
SCA, Sweden, is divesting its Austrian publication paper mill in Laakirchen to Heinzel Group
Learn More...
|
Containerboard/Packaging
U.S. Containerboard production fell 1.5% this past November, compared with the prior month (October), but rose 1% over the same month in 2011
Learn More...
|
Total U.S. boxboard production this past November increased by 2.1%, compared with November 2011, and increased 1.7% from the prior month (October)
Learn More...
|
Uni Core Holdings Corp. (UCHC), a Hong Kong-based holding company, reports that it has filed for bankruptcy protection for its Shenzhen Factory of the APT Paper Group (APT), one of UCHC's subsidiaries
Learn More...
|
The Paper and Paperboard Container Manufacturing Industry in China will grow at a CAGR of 11.23% during the period 2011-2015, according to a newly offered report by Research and Markets, Dublin, Ireland
Learn More...
|
Mondi SCP, South Africa, has announced plans to invest EUR 28 million in green energy projects at its Ružomberok mill in Slovakia
Learn More...
|
|
New Products
VTT Technical Research Centre of Finland, along with Finland-based Fortum, Metso, and UPM, reports to have developed a technique that enables the cogeneration of heating energy and bio-oil in the same power plant cost-effectively and sustainably
Learn More...
|
Because of the increasing demand for fiber-based packaging made with renewable materials, Stora Enso Specialty Papers, Finland, has broadened its MediaSet basis weight offering
Learn More...
|
Published Pricing
Metsä Fibre, Finland, increased the price of its Botnia Nordic Pine (NBSK—northern bleached softwood kraft) in Europe, effective January 1
Learn More...
|
Södra, Sweden, also raised the price of its softwood pulp in Europe, effective January 1
Learn More...
|
Stora Enso, Finland, has also informed its clients of an increase in NBSK (northern bleached softwood kraft) pulp process that became effective January 1
Learn More...
|
People
Clearwater Paper Corp., Spokane, Wash., USA, announced two key divisional executive appointments, effective January 1
Learn More...
|
David Allen, PaperlinX's (Australia) Interim CEO since August 2012, has been appointed full-time CEO of the company
Learn More...
|
Jaana Rinne has been appointed SVP, Human Resources, and a member of Pöyry PLC's Group Executive Committee
Learn More...
|
TAPPI News
January 30 Webinar Provides New Ideas on Monitoring and Assessment.
Learn More...
|
This long-runningTAPPI course that covers industry essentials returns January 7-10 in St. Petersburg, Fla., USA., providing information on how each individual part of a paper mill influences another.
Learn More...
|
If you're planning a career in the industry, this event will put you on the cutting edge of some groundbreaking technology. The summit will be held January 19-21, 2013 in Raleigh, N.C., USA.
Learn More...
|
Deadline for award nominations from the PIMA Division of TAPPI is January 15.
Learn More...
|
The TAPPI Shipping, Receiving, and Warehousing (SRW) Workshop, April 9-10, 2013 in Nashville, Tenn., USA, is the paper industry's premier educational and networking forum for the entire paper industry supply chain.
Learn More...
|
Sustainability Manufacturing: First and Goal! Papers are now being accepted for the 2013 technical program.
Learn More...
|
Tissue360 Forum topics include an overview of hygienic product market drivers, raw material usage and supply, wet and dry end additives, latest hybrid tissue making technology, and runnabilit-operational tips.
Learn More...
|
Active in the Polymers, Extrusion, Adhesives, Coatings, and Extrusions (PLACE) division since 1988, TAPPI member Ginger Cushing says she "has a darn good time."
Learn More...
|
The deadline has been extended to January 11, 2013, and must be submitted using the TAPPI Speaker Management System.
Learn More...
|
The DIctionary of Paper, Fifth Edition, is an essential reference tool for everyone in the industry, with definitions for more than 5,300 terms commonly used in the pulp and paper industry.
Learn More...
|
The current economy has affected many schools' endowment funds, resulting in decreased support of student scholarships. The good news is TAPPI has stepped in to help.
Learn More...
|
Learn from Ken Blanchard whose books on leadership have sold more than 20 million copies, and Mark Miller, who worked his way up from a factory line worker to vice president of one of the largest fast-food chains in the country.
Learn More...
|
After 2012 record attendance, PaperCon 2013 will bring together a wider slate of industry professionals in Atlanta, Ga., USA. April 27 - May.1.
Learn More...
|
Don't miss out on this chance to put your company's brand in front of key industry professionals who have a vested interest in your product.
Learn More...
|
Key benefits of safety training DVDs include being extremely cost effective, efficient, and portable. Playable 24/7 in any U.S. player or computer.
Learn More...
|
The International Mechanical Pulping Conference, sponsored by PI, TAPPI, PAPTAC, SPCI, and PTF to be held June 3-5, 2014, in Helsinki, Finland, has Calls for Papers due by Feb. 28, 2013.
Learn More...
|
|
Find us on Facebook
Network with us on LinkedIn
Follow us on Twitter
|
Weekly Spotlight
NewPage Corp., Miamisburg, Ohio, USA, has successfully completed its financial restructuring and has officially emerged from Chapter 11 bankruptcy protection pursuant to its Modified Fourth Amended Chapter 11 Plan that was confirmed on Dec. 14, 2012, by the U.S. Bankruptcy Court for the District of Delaware in Wilmington.
In conjunction with the Plan, NewPage closed on its exit financing, consisting of a $500 million term loan facility led by Goldman Sachs Lending Partners LLC and a $350 million revolving credit facility led by J.P. Morgan Securities LLC.
"This is an exciting day for all of us at NewPage," said George F. Martin, president and CEO. "We have successfully completed our restructuring, and we have emerged as a financially sound company. This step helps to solidify our position as the leading North American producer of printing and specialty papers. We look forward to continuing to provide our customers with exceptional service and high-quality products, operating safe and efficient mills, and being a responsible community member."
Jay A. Epstein, SVP and CFO, added that "through the reorganization process, we significantly reduced our debt and emerged with a sustainable capital structure. Our exit facility will provide ample liquidity to meet all of our working capital and capital investment needs."
NewPage is a producer of printing and specialty papers in North America with $3.5 billion in net sales for 2011. The company owns paper mills in Kentucky, Maine, Maryland, Michigan, Minnesota, and Wisconsin. These mills have a total annual production capacity of approximately 3.5 million tons of paper. The company's product portfolio includes coated, specialty, supercalendered, and uncoated papers.
Back To Top
|
SCA, Philadelphia, Pa., USA, makers of the Tork® brand of away-from-home tissue products, has announced the publication of its third annual Tork Report, a comprehensive look at sustainability issues and hygiene practices among North American businesses and consumers. The 2012 Tork Report, titled "The Sustainability Gap," highlights areas where companies have made progress in improving sustainability goals but also identifies trends that have taken a step backward. The survey was conducted online by Harris Interactive among 1,015 U.S. and 555 Canadian business professionals and 2,114 U.S. adults age 18 and over.
In 2012, 64% of U.S. companies said they had (or were putting) a sustainability plan in place, nearly double the 38% of companies that reported this in 2011. Furthermore, 31% of U.S firms and 30% of Canadian firms say their sustainability plans are having a positive impact on the bottom line.
The 2012 Tork Report combines original research conducted by Harris Interactive with commentary and additional research regarding sustainability and hygiene from several sources, providing a comprehensive look at one of society's most important concerns—how we take care of our resources.
"We've seen sustainability continue to be important to consumers and business alike," said Mike Kapalko, sustainability marketing manager for SCA AfH Professional Hygiene in North America. "A real area of concern is the gap—companies reporting they have sustainability plans, yet ignore the risks to their business from climate change, severe weather, or unhealthy employee habits."
While most companies have acknowledged sustainability as a necessary part of doing business, "most have not thrown their full weight behind the effort," writes sustainability expert and Tork Green Hygiene Council member Josh Radoff. In his call to action for companies to push further, he notes "we've approached the end of Corporate Sustainability 1.0, where the low-hanging fruit has been picked, and the basic levels of expectations have been met. Thus, there is a large gap between the status quo and the next level of achievement—the effort to dig down to the core of a company's social and environmental impact."
For businesses and consumers to get to the next level of achievement in sustainability, the 2012 Tork Report points to initiatives that can help. These include:
- Reducing food waste: Americans waste 40% of the nation's food supply, the single biggest contributor to solid waste in landfills
- Adding a universal sustainability index—a guide to help consumers and companies make smarter product choices—was deemed a good idea by three-quarters of people surveyed
- Reduce the amount of "green washing," or false claims by companies that tout a product's environmental benefits.
Sustainability plans should include the health of a company's workforce, as reflected in the popular notion of the three P's—People, Planet, and Profit. Yet, as a whole, we don't do a good job of taking care of ourselves, the 2012 Tork Report finds.
There is a substantial gap in understanding why it is important to wash our hands. Most people wash their hands after using the restroom—although 33% of men don't. We also don't wash our hands after using the most germ-infested items we touch each day. Less than half of Americans wash their hands after using gym equipment, handling money, or taking public transportation. Why does this matter? Because countless items such as microwave door handles, elevator buttons, and restaurant menus are more germ-infested than restrooms, the report points out.
A downloadable copy of the 2012 Tork Report is available online.
Back To Top
|
The newly formed TAPPI Process & Project Engineering Committee is conducting a survey to better determine what capital project strategies today's pulp and paper mills are implementing to stay in-tune and competitive under progressively lean operating conditions. To participate anonymously in this survey (no participant/mill information requested), please use the online link below. This survey will take only a few minutes to complete.
Online Capital Projects Survey
If you are interested in learning the results of the survey or would like more information on the new TAPPI Process & Project Engineering Committee, please contact Craig McKinney at TAPPI. Your participation is very much appreciated.
Back To Top
|
Below is the latest listing of job openings in the TAPPI Career Center. The current listing includes job openings for a variety of positions, including shift supervisor, maintenance manager, director of engineering, maintenance training manager, papermaking technology manager, and engineering intern. Current, specific job openings at companies and locations in the TAPPI Career Center include:
Employer |
Title |
Location |
Canfor Pulp |
Shift Supervisor |
Prince George, B.C., Canada |
Canfor Pulp |
Fibreline Manager |
Prince George, B.C., Canada |
Canfor Pulp |
Maintenance Manager |
Prince George, B.C., Canada |
First Quality Enterprises |
Multiple Eng. Positions |
Anderson, S.C. |
First Quality Enterprises |
Director of Engineering |
Anderson, S.C. |
First Quality Enterprises |
Director of Reliability & Maintenance |
Anderson, S.C. |
Kruger Products |
Papermaking Technology Manager |
Crabtree, QC., Canada |
KTG USA |
Electrical/Instrumentation Technician |
Memphis, Tenn. |
Longview Fibre |
Maintenance Training Manager |
Longview, Wash. |
Norpac-Weyerhaeuser |
Engineering Internship |
Longview, Wash. |
More information about these jobs is available online.
Back To Top
|
Market Roundup
Total U.S. kraft paper shipments in November totaled 120,400 tons, a decrease of 11.2% compared with the prior (October 2012) month, AF&PA (Washington, D.C., USA).reports in its November 2012 Kraft Paper Report issued late last month. November bleached kraft paper shipments increased 21.2% year-over-year.
Unbleached kraft paper declined 15.7% year-over-year. Total month-end inventory increased 4.3% to 76,000 tons in November, compared with October 2012 month-end inventories.
Back To Top
|
U.S. industry consumption of recovered paper this past November was 2.36 million tons, which is 5% lower than in October 2012, according to the AF&PA, Washington, D.C., USA. AF&PA's November 2012 U.S. Recovered Fiber Monthly Report notes that inventories increased for most grades. Year-to-date total consumption for 2012 was 4% lower than during the same period of 2011.
U.S. exports of recovered paper showed strong gains across all grades, except for high grade deinking. Corrugated exports increased to levels not seen since April 2011. Year-to-date exports of recovered paper in 2012 are 6% lower than during the same period in 2011.
Back To Top
|
Total U.S. printing and writing (P&W) paper shipments decreased 4% in November, compared with November 2011, according to the AF&PA (Washington, D.C., USA) November 2012 Printing-Writing Paper Report published in late December. Three out of the four major P&W paper grades posted decreases compared with the prior November report, with coated free sheet posting the only year-over-year increase.
Additional key findings included:
- November shipments of coated free sheet (CFS) papers increased year-over-year for the sixth time in the past 12 months. CFS shipments increased 1%, compared with November 2011, to 330,800 tons, the fourth highest total in 2012.
- While uncoated free sheet (UFS) paper shipments decreased 2% compared with November 2011, to 705,500 tons, October exports increased year-over-year for the third consecutive month. Year-to-date shipments of UFS paper were down 3% compared with the same months in 2011. Exports of UFS increased year-over-year in October, up 15%. Year-to-date UFS exports are up 11% in 2012 compared with the same 10 months of 2011.
- November uncoated mechanical (UM) paper shipments decreased 24%, compared with November 2011, the twentieth consecutive month of year-over-year decline.
- November shipments of coated mechanical (CM) papers decreased 5% compared with November 2011. Year-to-date shipments of CM were down 5% compared with the same 11 months in 2011.
Back To Top
|
Pulp & Paper
Catalyst Paper, Richmond, B.C., Canada, reports that the sale of its Elk Falls site in Campbell River to Pacifica Deep Sea Terminals did not close and the sale agreement has been terminated. The sale of the 400-acre industrial site and adjacent properties was initially expected to close on Sept. 5, 2012. A non-refundable prepayment of a portion of the purchase price was received and the transaction timeline was extended multiple times up to the ultimate deadline of Dec. 18, 2012.
"It's disappointing that this transaction with Pacifica could not be completed even with the extended timeline. This is a fully serviced property in an excellent location and we remain confident that the right fit between site and buyer will be found that will bring new jobs and opportunities to Campbell River," said Kevin J. Clarke, Catalyst president and CEO. "In the meantime, site personnel are maintaining safety, security, and environmental requirements and complying with all applicable legislation."
The former pulp and paper site was indefinitely curtailed in 2009 and closed permanently in 2010. It has since been decommissioned with removal of chemicals, process wastes, and key papermaking equipment. The landfills remain intact as does the wastewater system that continues to operate in preparation for the site's redevelopment to other industrial uses. The Elk Falls mill began operations in 1952, and at its peak, produced 784,000 metric tpy of pulp, paper, and kraft paper.
Catalyst Paper produces specialty mechanical printing papers, newsprint, and pulp. With three mills located in British Columbia, Catalyst has a combined annual production capacity of 1.5 million metric tons.
Back To Top
|
Clearwater Paper Corp., Spokane, Wash., USA, has completed the next phase of its newest tissue facility at Shelby, N.C., with the startup of a new through-air-dried (TAD) tissue machine. Upgrades to a second TAD machine, located at the company's North Las Vegas, Nev., mill, have also been completed. The enhancements enable the facility to produce TAD ultra-bathroom tissue and household towels.
In regard to the Shelby startup, Gordon Jones, chairman and CEO, noted that "construction of all phases to date of the nearly one-million-square-foot facility came in on-time and on-budget. The dedication and support of Clearwater Paper's 200 Shelby employees have already made this facility a huge success."
New production and distribution capability at Shelby is expected to increase the company's ultra and premium offerings to existing southern and East Coast customers. Collectively, the two TAD machines will create new opportunities to expand the company's private label consumer tissue business around a national manufacturing footprint, supplying these key products to customers across the U.S.
"The completion of the flagship facility in Shelby fulfills one of Clearwater Paper's primary business strategies — to focus on growing the consumer products segment of the company," said Linda Massman, president and COO. "Combined with the recent upgrade at our North Las Vegas facility, these two important projects have helped Clearwater Paper achieve our goal of a coast-to-coast manufacturing footprint focused on best serving our private label customers."
Brian Hoaglund, expansion project leader, said that "we clearly owe a big thanks to the hundreds of contractors who have worked methodically night and day for two years to build one of the finest tissue manufacturing complexes in the world. We worked seamlessly with government agencies from Shelby, Cleveland County, and the state of North Carolina throughout the process."
Clearwater Paper's Las Vegas TAD machine was completed in 2004 to fill a void in the private label tissue marketplace, which lacked a leading national brand equivalent (NBE) ultra-premium quality paper towel product. Since the machine became operational, Clearwater Paper has been a leading supplier of TAD paper towels to regional and national private label retailers in the U.S.
"The Las Vegas upgrade was a success for many reasons including excellent project management," said Bill Copenspire, VP consumer products manufacturing. "We completed significant pre-installation work before the scheduled outage and had very good communication between Clearwater Paper and an army of vendors."
"Clearwater Paper can add NBE TAD bath tissue to our product lineup at a time when the ultra-quality tier is the highest growth segment in bath tissue," said Bruce Woodlief, director of marketing. "The addition of TAD bath provides retail customers with a significant quality improvement over their existing conventional ultra-bath product."
Clearwater Paper produces consumer tissue, away-from-home tissue, parent roll tissue, machine glazed tissue, bleached paperboard, and pulp at 15 facilities in the U.S. and Canada. The company is a supplier of private label tissue to major retailers and wholesale distributors.
Back To Top
|
NewPage Corp., Miamisburg, Ohio, USA, has announced members of its new board of directors. Mark A. Angelson, former Chicago deputy mayor and CEO of RR Donnelley who also led World Color Press out of bankruptcy and guided its combination with Quad/Graphics, has been named chairman. He will be joined by paper industry leaders Robert M. Amen, former president of International Paper, and John F. McGovern, former CFO of Georgia-Pacific.
Robert J. Bass, a member of the audit committee of Groupon and a recently retired vice chairman of Deloitte, also has been named to the board, along with Paul E. Huck, SVP and CFO of Air Products & Chemicals, Lisa J. Donahue, managing director in the Turnaround and Restructuring Practice of AlixPartners, and Eric D. Muller, managing director in the Principal Investment Area of Goldman Sachs. George F. Martin, CEO for NewPage, is the only continuing member of the board.
NewPage is a producer of printing and specialty papers in North America with $3.5 billion in net sales for 2011. The company owns paper mills in Kentucky, Maine, Maryland, Michigan, Minnesota, and Wisconsin. These mills have a total annual production capacity of approximately 3.5 million tons of paper. The company's product portfolio includes coated, specialty, supercalendered, and uncoated papers.
Back To Top
|
SCA, Sweden, is divesting its Austrian publication paper mill in Laakirchen to Heinzel Group. In conjunction with the divestment, SCA and Heinzel Group have concluded a sales cooperation agreement.
In 2011 Laakirchen reported totaled sales of EUR 335 million and had more than 500 employees. The annual capacity amounts to more than 500,000 metric tons.
The initial purchase consideration is EUR 100 million with a possible maximum additional purchase price of EUR 100 million based on a two-year profit-sharing model. In conjunction with the transaction, an impairment of EUR 50 million has been recognized, which will be charged to profit in the fourth quarter of 2012.
The transaction is expected to be finalized in the first quarter of 2013 following approval by the relevant authorities.
In regard to the sales cooperation agreement, SCA Forest Products' and Heinzel Group's sales organizations complement each other and SCA will have a stronger representation on several markets for its publication paper, pulp, and kraftliner products. The sales collaboration is scheduled to come into effect when the transaction has been finalized.
Following the divestment of Laakirchen, SCA's remaining publication papers operations will be concentrated in Sweden, close to its forest holding.
Back To Top
|
Containerboard/Packaging
U.S. Containerboard production fell 1.5% this past November, compared with the prior month (October), but rose 1% over the same month in 2011, according to the AF&PA (Washington, D.C., USA) November 2012 U. S. Containerboard Statistics Report issued late last month. However, the month-over-month average daily production increased 1.7%.
The containerboard operating rate for November 2012 gained 0.6 points over October 2012, from 96.3% to 96.9%.
Back To Top
|
Total U.S. boxboard production this past November increased by 2.1%, compared with November 2011, and increased 1.7% from the prior month (October) , according to the AF&PA (Washington, D.C., USA) November 2012 U.S. Paperboard Report. Unbleached kraft boxboard production increased over the same month last year and increased compared with last month.
Total solid bleached boxboard and liner production increased compared with November 2011 and increased compared with last month. The production of recycled boxboard increased compared with November 2011 but decreased compared with the prior month (October)
Back To Top
|
Uni Core Holdings Corp. (UCHC), a Hong Kong-based holding company, reports that it has filed for bankruptcy protection for its Shenzhen Factory of the APT Paper Group (APT), one of UCHC's subsidiaries. The Shenzhen facility was negatively impacted by the downturn of the Chinese and worldwide economy coupled with a shortage of required cash flow to meet current production needs. APT Shenzhen has been struggling for a long time and management has decided to close it down.
UCHC's Board says it believes this move will allow the company to devote the expected cash savings to bolster the healthier APT Group's Qingdao and Suzhou factories, which remain fully operational. UCHC management's goal is to turn the remaining APT operations profitable within six months.
UCHC plans to soon initiate a Valuation Report and an Audit of Prosperous Agriculture Co., its farm business, to consolidate their financial results with the Group. UCHC recently appointed a New York-based investment advisor to aid in the business restructuring and an investment banker to potentially raise capital.
APT Paper Group, a wholly owned subsidiary of UCHC, headquartered in Shenzhen, Guangdong, China, was founded in November 1993. APT's products include honeycomb paper pallets, honeycomb paper panels, honeycomb paper cartons, honeycomb paper coffins, honeycomb paper cushions, paper slip-sheets, paper corner protectors, and corrugated paper products. APT holds patents throughout the world on many of its products. The company's customers include Walmart, Costco, Sam's Club, Sony, Nokia, DHL, Haier, and Hisense, among others.
Prosperous Agriculture, 51% of which is owned by UCHC, is headquartered in Xi'an, Shaanxi Province, China. It manufactures and distributes agricultural products.
Back To Top
|
The Paper and Paperboard Container Manufacturing Industry in China will grow at a CAGR of 11.23% during the period 2011-2015, according to a newly offered report by Research and Markets, Dublin, Ireland. The report, titled Paper and Paperboard Containerboard Manufacturing Industry in China 2011-2016, notes that one of the key factors contributing to this market growth is high domestic demand.
The paper and paperboard container manufacturing industry in China has also been witnessing the emergence of new technologies. However, the increasing competition from substitutes could pose a challenge to the growth of this market.
The key vendors dominating this market space are Tetra Pak China Ltd., Zhejiang Dashengda Packaging Co., Shanghai Zhonglong Paper Co., and Salfo Group Co. Other vendors mentioned in the report are JiaxingDahua Package Co., ZaozhuangHuarun Paper Co., Daye Group Co., Kangmeibao (Suzhou) Co., JinjiangYoulanfa Paper Co., and Quingshan Corp.
Commenting on the report, an analyst from TechNavio's team, creators of the study, said that "the paper and paperboard container manufacturing industry in China is witnessing the emergence of new technologies pertaining to the production of paper and paperboard containers. Vendors are continuously adopting new methods that allow them to reduce their production cost by incorporating technologically advanced equipment.''
According to the report, economic development in the developed parts of China is rapid and significant. In China, the demand for industrial products has increased considerably over the past few years. In addition, the demand for high-quality paper containers from consumers in China is propelling the production of paper and paperboard containers. The underdeveloped parts of the country also provide a potential market in the long-term because of the increasing disposable income of the people, rapid development in the economy, and the increase in urbanization in China.
Further, the report reveals that the availability of substitute products and their declining prices pose a major challenge for this industry.
Back To Top
|
Mondi SCP, South Africa, has announced plans to invest EUR 28 million in green energy projects at its Ružomberok mill in Slovakia. The investment includes a new recovery boiler at the mill to increase pulp production, reduce the mill's environmental footprint, and improve its overall cost position. The projects will cover improvements in chemical recovery and green energy and heat production during the pulp production process.
"Our objective is to increase pulp production, produce more green energy and further improve our carbon dioxide footprint. We are pleased that the Slovakian government is supportive of our long term presence in the country, which played an important role in our decision making," said Peter J. Oswald, CEO of Mondi's Europe and International division.
The new recovery boiler will be constructed over a two-year period with expected start up in the fourth quarter of 2014.
Peter Orisich, CEO of Mondi's Uncoated Fine Paper business, said that "Mondi has invested more than EUR 350 million in the mill over the past ten years to drive innovative production and operational improvements. This investment continues the development of Mondi SCP into a state-of-the-art facility in Slovakia."
Mondi SCP is the largest integrated mill producing pulp and paper in Slovakia, with pulp production exceeding 500,000 metric tpy and uncoated fine paper production at 535,000 metric tpy. It is an international packaging and paper group, with production facilities across 29 countries and revenues of EUR 5.7 billion in 2011. The Group mainly produces packaging paper, converted packaging products, and uncoated fine paper. It has key operations in central Europe, Russia, and employs some 23,400 people.
Back To Top
|
New Products
VTT Technical Research Centre of Finland, along with Finland-based Fortum, Metso, and UPM, reports to have developed a technique that enables the cogeneration of heating energy and bio-oil in the same power plant cost-effectively and sustainably. VTT's technique is based on combining pyrolysis and fluidized bed technology. The new technique is expected to boost bio-oil production volumes considerably in the next few decades.
VTT received an innovation award for the new technology. The award was presented in December by the European Association for Research and Technology Organizations (EARTO).
"The innovation prize brings up the long-term work that VTT has done in developing renewable energy sources. EARTO wants to reward innovations that have significant societal and economic impact. The prize indicates that we have been successful in this work," says Anne-Christine Ritschkoff, EVP, Strategic Research, VTT.
Bio-oil has for a long time been pegged as the successor of fossil fuels as our future source of energy. However, large-scale commercial use of bio-oil in heat generation requires a cost-effective production technique. The new technique patented by VTT enables a considerable cut in the production cost of bio-oil.
Fast pyrolysis involves heating biomass such as forest industry waste to a high temperature to form gas. When the gas is cooled, it condenses into liquid known as bio-oil. Combining the pyrolysis process with traditional fluidized bed boilers used in power plants brings a range of efficiency gains. Producing bio-oil with the new technique is cheaper than in a separate pyrolysis process.
Bio-oil plants that are integrated into power plants are extremely energy-efficient, because the energy contained in the by-products of the pyrolysis process can be recovered in fluidized bed boilers. This is a significant improvement, because the by-products can contain as much as 40% of the original biomass's energy. In turn, lost heat from the power plant can be used in the bio-oil production process. Cogeneration offers higher efficiency than separate production, and the investment and operating costs of the plant are lower than in separate production.
The use of bio-oil has significant positive effects on the environment. By replacing fossil fuels with bio-oil in heat generation, carbon dioxide emissions can be cut by 70% – 90%. Sulfur emissions are also considerably lower.
The technique is due to enter commercial production towards the end of 2013 when the energy company Fortum opens its new integrated bio-oil and heating plant in the city of Joensuu in Finland. The plant is designed to produce 50,000 metric tons of bio-oil per year. The volume is enough to cover the annual heating needs of 24,000 average-sized homes.
VTT is involved in European standardization work to promote the commercialization of the innovation. There are currently around 200 power plants in Europe and North America that could be converted to include a bio-oil plant. This would mean more than 10,000 new jobs in the forestry and logistics sectors, for example.
A video about the technology is available online.
Back To Top
|
Because of the increasing demand for fiber-based packaging made with renewable materials, Stora Enso Specialty Papers, Finland, has broadened its MediaSet basis weight offering. MediaSet is now available in basis weights of 80, 90, and 100 gsm.
Specially developed for high-speed-converting, the paper is optimized for the production of packaging wrappers, including confectionery as well as labeling of cans and jars. Brand owners, printers, packers, and fillers can take advantage of a number of important properties of this sized, one-side-coated paper, the company notes.
The high-white, glossy surface of MediaSet, in conjunction with an outstanding offset printability, supports a high quality and freshness emphasized product presentation at the Point of Sale (POS). The high bulk, excellent runnability and very good glue adhesion allow high and highest speed in printing, converting, packaging, and labeling lines. This makes MediaSet also an economical choice for packaging production and labeling.
MediaSet, especially suitable for the production of food packaging, is produced at the Stora Enso Uetersen mill in Germany, from sustainably produced virgin fibers.
Back To Top
|
Published Pricing
Metsä Fibre, Finland, increased the price of its Botnia Nordic Pine (NBSK—northern bleached softwood kraft) in Europe, effective January 1. The new price is $840/metric ton, CIF Metsä Fibre's usual European ports.
All other terms regarding this grade remain as previously agreed, the company noted.
Back To Top
|
Södra, Sweden, also raised the price of its softwood pulp in Europe, effective January 1. The company's new price is $840.00 per metric ton.
Södra's business is organized into four business areas: Södra Skog (timber raw products, forestry services); Södra Timber (wood products); Södra Cell (paper pulp); and Södra Interiör (interior wood products). Some 4,000 people work for the company.
Back To Top
|
Stora Enso, Finland, has also informed its clients of an increase in NBSK (northern bleached softwood kraft) pulp process that became effective January 1. The increase is $20 per metric ton, taking the new price to $840 per metric ton in the European market.
Back To Top
|
People
Clearwater Paper Corp., Spokane, Wash., USA, announced two key divisional executive appointments, effective January 1. Thomas A. Colgrove, president of the pulp and paperboard division, has been named president of the consumer products division, succeeding Robert P. DeVleming, who will retire after a transitional period during the first half of 2013. Danny G. Johansen was promoted from VP of sales and marketing to president of the pulp and paperboard division.
"We look forward to the continued contributions from Tom and Dan in their new positions, and congratulate Bob on a long and successful career at Clearwater Paper," said Gordon Jones, chairman and CEO. "Tom and Dan are highly accomplished executives, each with more than 30 years of industry experience, and they have both been integral to our success. I am confident that, together with incoming CEO Linda Massman, they will successfully advance our strategic priorities and continue to deliver significant shareholder value."
Colgrove joined Clearwater Paper as VP of the pulp and paperboard division in 2009. Before joining the company, he was North American senior director, family care products, for Kimberly-Clark, where he was responsible for seven manufacturing facilities with 4,200 employees. Prior to joining K-C, he also served as VP of manufacturing for Central Paper Co., and held management positions with Procter & Gamble.
"Tom's extensive knowledge regarding running and managing major tissue operations will be a critical asset in helping drive stronger results for the company," said Clearwater Paper President and COO Linda Massman. "Tom has successfully led our pulp and paperboard division for more than three years, and we are fortunate to have an individual of his deep experience, which includes more than 33 years in consumer tissue products, leading our consumer tissue business."
Johansen joined the company in 1973 and during that time, has served in many leadership positions, including senior director of sales for pulp and paperboard, production and strategic planning manager for pulp and paperboard, and VP of the western wood products division. He was named VP of sales and marketing in 2008.
"Dan's nearly 40 years of experience is both broad and deep at Clearwater Paper," Massman noted. "His intimate understanding of our customers and markets and his knowledge of our pulp and paperboard business make him a strong addition to our leadership team. On behalf of the entire management team and everyone at Clearwater Paper, I would like to thank Bob for his leadership and countless contributions to the company. Bob has been an integral part of our success, and we wish him the best in his retirement."
Clearwater Paper produces consumer tissue, away-from-home tissue, parent roll tissue, machine glazed tissue, bleached paperboard, and pulp at 15 manufacturing locations in the U.S. and Canada. The company is a supplier of private label tissue to major retailers and wholesale distributors. The company also produces bleached paperboard.
Back To Top
|
David Allen, PaperlinX's (Australia) Interim CEO since August 2012, has been appointed full-time CEO of the company. Allen joined PaperlinX in 2004 and previously served as managing director of the Robert Horne Group in the U.K. and subsequently as EVP of PaperlinX with responsibility for the U.K., Ireland, and Canada. His earlier background was in corporate and product strategy, sales and marketing, and GM in a range of sectors, including abrasives, industrial diamonds, and automotive with Saint-Gobain, Unicorn international, and the Rover Group.
PaperlinX's chairman, Michael Barker, noted that "the board has complete confidence that Mr. Allen is the person who can continue this rapid restructuring and return PaperlinX to profitability in the shortest possible time. Since Allen's appointment as the Interim CEO, we have identified and are implementing A$15 million of cost saving initiatives."
Back To Top
|
Jaana Rinne has been appointed SVP, Human Resources, and a member of Pöyry PLC's Group Executive Committee. She will take over the new duties this spring, and will report to Alexis Fries, president and CEO of Pöyry PLC. Rinne comes to Pöyry from Konecranes Plc, where she most recently worked as VP, Human Resources.
Pöyry is a global consulting and engineering company focused on balanced sustainability and responsible business.
Back To Top
|
Sappi Ltd., Johannesburg, South Africa, reports that Professor M. Feldberg, having reached the company's mandatory retirement age for non-executive directors, will retire from the Sappi Board of Directors on December 31, 2012. He will be succeeded as lead independent director, by Sir Nigel Rudd, who has been a director of Sappi for more than six years.
Back To Top
|
TAPPI News
Monitoring Tools and Strategies for the Detection and Control of Microbial Growth in Papermaking Systems
Wednesday, January 30, 12:00 p.m. to 1:00 p.m. (EST)
Microorganisms thrive in industrial systems, including paper manufacturing environments. Inadequate control of microbial growth can allow for spoilage and deposit formation that reduces process efficiency and product quality. This webinar will provide an overview of monitoring approaches that can be used to assess the performance of biocontrol programs and optimize treatment strategies for improved control of microbial spoilage and deposit formation.
Learn more and register for this FREE Webinar!
Who should attend: Anyone with an interest in deposit control and spoilage in industrial systems. The material is based on the 2008 "Monograph on Microbiology of Papermaking Systems," published by TAPPI Press, and available online. The webinar is open to TAPPI members and nonmembers.
Presenter: Dr. Laura Rice, Nalco Dr.
Laura Rice is a senior research scientist in Pulp and Paper Research at Nalco, an Ecolab company. She develops microbiological monitoring and control technologies for papermaking systems and provides on-site consulting and training for biocontrol applications. There is no cost to attend, but you must register.
Back To Top
|

Registration is now open for the TAPPI Introduction to Pulp and Paper Technology Course scheduled for January 7-10, 2013 in St.Petersburg, Fla., USA.
This is one of TAPPI's longest running courses. Why is this course one of our most popular?
Intro to Pulp and Paper Technology is unique in that it provides information on how each individual part of a paper mill influences another. This course allows you to understand how materials, pulping, and paper-making processes affect paper and board properties. You will also be delivered a broad overview of pulping and paper-making technology, including the entire pulping and paper-making process from raw materials and wood prep. to pulping and mill operations.
Four Reasons to attend Intro to Pulp and Paper Technology:
- Course pre-surveys will ensure this course meets attendees individual needs
- You will have networking opportunities during hourly breaks
- This course measures up the MOST training content in the SHORTEST amount of time
- You get the instruction of Dr. Michael Kocurek and can learn from his 45 years of experience on this topic.
Who benefits?
- Pulp and paper company employees - new technical/operating staff, operators, non-technical personnel, chemical and direct equipment suppliers, technical service professionals, and sales people.
This course is taught by Dr. Michael J. Kocurek, Professor Emeritus, Paper Science & Engineering at North Carolina State University. Dr. Kocurek is one of the world's most recognized educators in the field of pulp and paper industry science.
Back To Top
|

If you're planning a career in the pulp and paper (or packaging) industry, this event will put you on the cutting-edge of some groundbreaking technology.
Make plans now to attend the 2013 TAPPI-PIMA Student Summit, January 19-31, 2013, in Raleigh, N.C., USA.
This is a rare opportunity for advanced undergraduate and graduate students to meet face-to-face with industry leaders and gain valuable information on what forces are shaping the industry today - plus the added bonus of the inside track on employment and career development.
Program Session Topics:
- Mock Interview Session/Resume Critique
- Myth vs. Fact of the Industry
- Voith Fabrics Presentation
- Printed Electronics
- Future of Carbohydrates
- Career Path Panel: Grad School vs. Job
- BioEnergy
- Project Management.
The 2013 TAPPI-PIMA Student Summit includes:
- An Engineering Competition
- Networking and a Career Fair
- Scavenger Hunt
- Multiple Tours of Industry Facilities
- Interviews with Hiring Companies.
Sponsorships are available. For more information, contact David Bell.
Back To Top
|
Recognize Star Performers at Your Mill! Do you know of a star performer who deserves some recognition? Nominate them for one of the prestigious awards available from the PIMA Division of TAPPI. They will appreciate being honored at PaperCon and in Paper360° magazine.
The deadline for nominations is Jan. 15, 2013. Award descriptions and nomination details are available online. Questions? Contact Scott Springmier.
PIMA Awards include:
- PIMA'S Executive of the Year
- Mill Manager of the Year
- The Brookshire Moore Superintendent of the Year
- Technologist of the Year
- Ray H. Cross Community Service Award
- Delano L. "Del" Boutin Local Section Service Award
- Thomas F. Sheerin Sr. Service Award
- IT Service Award
- Kenneth H. Phillips Specialist Group Award
- Student of the Year Award.
Back To Top
|
The TAPPI Shipping, Receiving and Warehousing (SRW) Workshop, April 9-10, 2013, in Nashville, Tenn., USA, is the paper industry's premier educational and networking forum for the entire paper industry supply chain. The workshop provides anyone interested in the logistics and shipment of paper the opportunity to see new technology and hear experts on a wide range of topics – all under one roof - focused on reducing in-transit damage.
"The safe, damage-free shipment of paper products to customers around the world is a very important element of pulp and paper industry logistics," notes Larry N. Montague, TAPPI president and CEO. "A wide range of factors can cause damage during shipment and the SRW Workshop is the premier event focusing on how mills, and their customers, can lower costs and improve product quality by reducing damage to rolls during transit."
The SRW Workshop is an interactive and collaborative workshop put on by industry professionals representing the entire paper supply chain, including shippers, carriers, printers, and publishers. Presentations and collaborative discussions on topics including car quality, safe truck loading and securing, intermodal loading and securing, damage classification, inspection, and claims procedures are provided. Experts with extensive experience and practical background knowledge representing Class 1 railroads, intermodal providers, warehouses, shippers, and dunnage manufacturers are part of the extensive program offered during this two-day workshop.
For more information visit the SRW website.
Back To Top
|
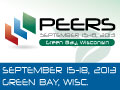
The 2013 TAPPI PEERS Conference, September 15-18 in Green Bay, Wis., USA., is the perfect forum for paper industry professionals both to acquire practical operating insights and to network with industry peers in technical sessions, tutorials, round tables, new technology sessions, and workshops.
Papers are now being accepted for the 2013 technical program; suggested topics are as follows:
- Fiber Processing
- Nonwood Fibers
- Steam and Power
- Recycling
- Enviornmental Management and Regulation
- Sustainability.
Abstracts on other relevant topics are welcome.
Learn more.
Once again, next year's PEERS Conference will be co-located with the International Bioenergy and Bioproducts Conference (IBBC).
Authors interested in presenting a paper should upload their abstract to TAPPI's Speaker Management System by March 1, 2013.
Abstracts should be 1-2 paragraphs in length. Authors will be notified of acceptance by March 28.
For more information, contact Craig McKinney, TAPPI Program Manager, at 1.770.209.7294
Back To Top
|
The Tissue360 Forum, organized by TAPPI tissue experts in conjunction with Tissue360 magazine, will be held April 29 - May 1, 2013 at PaperCon 2013 in Atlanta, Ga., USA. The forum will cover a wide range of tissue manufacturing and converting technologies and market trends. PaperCon 2013 will be the pulp and paper industry's largest technical conference and trade show.
"The inclusion of the Tissue360 Forum at PaperCon 2013 will add comprehensive coverage of this dynamic segment to the industry's best technical program," notes TAPPI President and CEO Larry Montague. "The forum will provide business insights and peer-reviewed technical papers covering developments in one of the industry's most rapidly growing and technically innovative grade sectors."
Tissue360 Forum topics will include an overview of hygienic product market drivers, raw material usage and supply, wet and dry end additives, latest hybrid tissue making technology and runnability/operational tips. All material will be selected and peer reviewed by TAPPI members with tissue expertise. The program is open to all full PaperCon registrants.
PaperCon brings together CEOs, mill managers, superintendents, scientists, process engineers, and suppliers for the largest pulp and paper technical program in the world. . No other event provides such a comprehensive program, networking opportunities, and trade fair among such a distinguished group of industry leaders.
Back To Top
|
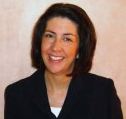 An Andreas Ahlbrandt winner, TAPPI member Ginger Cushing says being an active member of TAPPI's PLACE Division has served her professional development well by providing a solid network of packaging experts whose knowledge helped her win new business on many occasions. "They helped me understand the individual elements of packaging and how our components and processes work in concert," she said.
Cushing first joined TAPPI in 1988 when her colleagues at Mica, where she was a bench chemist, began urging her to do so. "They made me see it was the place to be," she said. Since then, she has held various chair positions, conducted courses, and has written and delivered numerous white papers. In addition to the Ahlbrandt award, Ginger was also named one of TAPPI's Finest Faculty for her participation in courses and symposia, and is a past recipient of the best paper and best session awards.
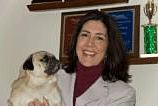 Ginger says being so active in TAPPI has provided many lasting benefits to her career, including a go-to network of packaging experts whose knowledge has helped her win new business on many occasions. "They help me understand the individual elements of packaging and how our components and processes work in concert."
If you would like to be featured in this section, or would like to suggest a fellow member to profile, please fill out the Membership Questionnaire and return it as an attachment to MemberSpotlight@tappi.org.
Find out more by reading this month's Member Spotlight.
Read the full TAPPI In-the-Spotlight to see this member's bio and related Q&A section.
Back To Top
|
The Call for Papers has been extended for the 2013 TAPPI International Conference on Nanotechnology for Renewable Materials, June 24-27, 2013, on the KTH Royal Institute of Technology Campus in Stockholm, Sweden. Abstracts must be entered into the TAPPI Speaker Management System by January 11, 2013.
This is a great opportunity to share your research findings with industry experts, scientists, health and safety specialists, legal and government policy makers, and leading researchers from around the world.
Participate as a Sponsor or an Exhibitor! There are several ways in which your organization can participate with a range of prices and benefits to meet your business objectives.
View the Prospectus.
Back To Top
|
Dictionary of Paper, Fifth Edition
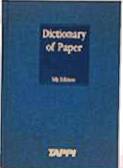
By Michael Kouris
An essential reference tool for everyone in the industry, this dictionary defines more than 5,300 terms commonly used in the pulp and paper industry.
The dictionary was revised and updated by a team of industry experts led by Michael Kouris, TAPPI JOURNAL Editor Emeritus. The 5th edition of The Dictionary of Paper is the most comprehensive dictionary ever published by TAPPI. 1996. 450 pages, hard cover.
This is also available in CD-ROM format.
View the Table of Contents
Product code: 0102B058
Member Price: $75.00
Non-Member Price: $112.00
Back To Top
|
TAPPI has scholarships to offer. You have a chance to apply for some green (funds to pay tuition, etc.) to fund a satisfying green career. These scholarships are available for graduate and undergraduate students with an interest in the pulp, paper, converting, and packaging industries. There are two general types of scholarships:
- TAPPI Division Scholarships
- William L. Cullison Memorial Scholarship.
What this message means to you:
If you're a student, here is a great way to apply for financial assistance for the 2013-2014 school year. Note that requirements will vary according to scholarship source, so you'll need to check the qualifications carefully. A reference document is available to guide you.
The deadline to apply for Technical Division Scholarships is February 15, 2013; the deadline for the Cullison scholarship is May 1, 2013. Mark your calendar now to allow yourself time to create an application that reflects the hard work you've been investing in your career.
If you are affiliated with a college or university, share this with your students, peers, or other staffers who work with students. They will be glad you did
If you're in the industry, perhaps you know of students worthy of scholarship assistance with their education, please pass this information along.
Back To Top
|
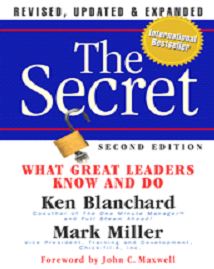
The Secret, Second Edition
What Great Leaders Know and Do
By: Ken Blanchard & Mark Miller
- Uses the popular "business fable" format that Ken pioneered
- Explains the five essential practices exhibited by the best leaders and provides practical ideas on how to make these a reality in your life.
At one time or another, everyone in a position of authority-whether in a multinational corporation or a local volunteer group-wonders what the key to great leadership is. And who better to answer that question than the team of Ken Blanchard, whose books on leadership have sold over 20 million copies, and Mark Miller, who worked his way up from line worker to vice president of one of the largest fast-food chains in the country. In The Secret, Blanchard and Miller use the uniquely accessible "business fable" format that Blanchard pioneered to get at the heart of what makes a leader truly able to inspire and motivate people. Debbie Brewster, recently promoted and struggling, finds herself about to lose her job due to poor performance. In an attempt to save her career, she enrolls in a new mentoring program offered by her company. Much to her surprise, Debbie finds her mentor is none other than Jeff Brown, the president of the company. Debbie decides that she is going to ask her new mentor the one question she feels she desperately needs answered: "What is the secret of great leaders?" Jeff's immediate answer-that great leaders serve their followers-completely flummoxes Debbie. Over the next 18 months, Jeff helps Debbie discover and explore five fundamental ways that leaders lead through service.
The Secret puts what Blanchard and Miller have learned about leadership in a form that anyone can easily understand, embrace, and pursue. It is a book that will benefit not only those who read it, but also the organizations they work in an the people who look to them for guidance.
The second edition includes revised and updated content including:
- A new foreword by John Maxwell
- A new resource section in the back matter summarizing key learning points
- A greater focus on the book's primary focus: servant leadership
- A more humanized protagonist
- Numerous other minor renovations throughout.
Ken Blanchard, coauthor of The One Minute Manager, the bestselling business book of all time!
Item #: 12SECRET
View the Table of Contents and Preview.
Member Price: $23.00
Back To Top
|
After a record attendance in 2012, PaperCon will bring together a wider assortment of CEOs, mill managers, superintendents, scientists, process engineers, and suppliers for the 2013 conference, scheduled for April 27 to May 1, in Atlanta, Ga., USA. PaperCon 2013 has expanded its already comprehensive technical program to include two new events covering tissue and nonwovens technology.
"PaperCon 2013 attendees will benefit from an expanded program providing additional learning and networking opportunities in several key areas," comments Larry N. Montague, TAPPI president and CEO. "Two co-located events - Tissue360º Forum and NETInc – will make new tissue and nonwovens tracks available to full conference registrants. Expanded coverage of these dynamic industry segments makes PaperCon an even more valuable resource."
PaperCon's large and comprehensive technical program, the industry's largest, offers a range of topics including Management (PIMA) Papermaking, Coating and Graphic Arts, Recycled Paperboard (RPTA Production - Technical Seminar), and Reliability (OpEx Workshop). An array of networking opportunities such as the PaperCon trade fair, receptions, lunches, and committee meetings, and a New Technology Showcase will make it the industry's must-attend event in 2013.
More information is available online.
Back To Top
|

The 2013 International Conference on Nanotechnology for Renewable Materials will be held June 24-27, 2013, on the campus of the KTH Royal Institute in Stockholm, Sweden.
TAPPI invites you to sponsor this exciting event.
Put your company's brand in front of key industry professionals who have a vested interest in your products. This internationally known event brings together leading researchers, industry experts, government representatives, and other stakeholders to share advances, perspectives, and discuss new ideas and breakthrough concepts on nanotechnology-based advances. Don't miss this valuable opportunity to meet key decision makers from a variety of industries while they're spending dedicated time learning and exploring ideas for the future.
As a sponsor or tabletop exhibitor, you will meet and interact with potential customers and industry leaders in this breakthrough technology area. Given the expanded program focus of the 2013 event, meeting participants will cross-cut a variety of industries and applications. This is a great opportunity to expand or enhance your marketing base with your expertise.
Please review the Sponsorship Prospectus and select the package that best meets your needs.
For sponsorship inquiries, please contact Raine Hyde at 1 770-209-7256.
For continually updated conference information please visit the event's website.
Take a look at the current list of participants.
Back To Top
|
TAPPI Press is known around the world as an industry-specific publisher of current, reliable, practical, and useful products that help members, students, and other readers enhance their technical knowledge to solve technical problems. TAPPI now offers safety training on DVD.
Key benefits of DVD training include:
- Extremely cost-effective, efficient, and portable
- Pay only for neccessary courses
- Simple, flexible, and reusable format
- No need for Internet connectivity
- Playable 24/7 in any U.S. DVD player or computer.
More information in available online for the following Safety Training DVDs:
- Arc Flash Safety DVD
- Bloodborne Pathogens DVD
- Combustible Dusts DVD
- Fire Safety DVD
- Forklift Safety DVD
- Hand and Power Tools DVD
- Hexavalent Chromium DVD
- Lockout Tagout DVD
- Slips, Trips and Falls DVD.
Back To Top
|
The International Mechanical Pulping Conference, sponsored by PI, TAPPI, PAPTAC, SPCI and PTF, will be held on June 3-5, 2014, in Helsinki, Finland. IMPC 2014 is a major part of PulPaper, one of the world's most premier pulp and paper exhibitions, coinciding with the 100th anniversary of PI, the Paper Engineers' Association.
The Conference Program Committee invites you to submit papers on the following topics:
- Energy saving in Mechanical Pulping process
- New applications and innovations
- Raw materials in Mechanical Pulping
- Advanced Mechanical Pulping technologies e.g.
- Process control and simulation
- Bleaching
- Water management and effluent treatment
5. Mill operations update e.g.
- Production cost saving technologies (energy and chemicals)
- Improving mechanical pulping business potential
6. Mechanical pulps in paper and board.
Authors interested in presenting a paper or a poster on these topics should submit an extended abstract (˜500 words) to impc2014@vtt.fi. Abstracts are due by February 28, 2013. Authors will be notified of acceptance by May 31, 2013 and final manuscripts are due March 31, 2014.
If you have any questions, please contact Sari Liukkonen, Chair of the Program Committee at +358 40 586 0384, or by e-mail at impc2014@vtt.fi.
Back To Top
|
|
|
TAPPI Over the Wire | 15 Technology Pkwy. S. | Norcross, GA 30092 USA | Voice: 770.446.1400 | Fax: 770.446.6947
|
 |