 |
|
Weekly Spotlight
Economic activity in the U.S. manufacturing sector contracted in November following two months of modest expansion, while the overall economy grew for the 42nd consecutive month
Learn More...
|
The newly formed TAPPI Process & Project Engineering Committee is conducting a survey to better determine what capital project strategies today's pulp and paper mills are implementing to stay in-tune and competitive under progressively lean operating conditions
Learn More...
|
Below is the latest listing of job openings in the TAPPI Career Center
Learn More...
|
Market Roundup
Total U.S. printing and writing (P&W) paper shipments decreased 2% in October compared with October 2011, primarily driven by declines in uncoated mechanical shipments
Learn More...
|
The global pulp market started to recover this fall after having been in decline for more than a year
Learn More...
|
U.S. industry consumption of recovered paper in October was 2.49 million tons, 6% higher than in September 2012
Learn More...
|
Domestic log prices in Western Russia did not decline long-term as the Russian government had hoped when Russia increased log export tariffs to 25% in April 2008
Learn More...
|
Total U.S. kraft paper shipments were 128,300 tons in October, a decrease of 5% compared with the prior month
Learn More...
|
Pulp & Paper
American Eagle Paper Mills, Tyrone, Pa., USA, this week introduced Eagle Armour Copy paper
Learn More...
|
C&S Paper, China, has brought a new 28,000 metric tpy tissue machine on-stream at its mill in Chengdu City, Sichuan Province
Learn More...
|
NewPage Corp., Miamisburg, Ohio, USA, will launch its Supercalendered Delivery Promise program beginning next month
Learn More...
|
Croatian-based PAN Papirna Industrija, together with China International Investment Stock, will build a new pulp and paper mill in Slatina, in northeast Croatia
Learn More...
|
Twin Rivers Paper Co., South Portland, Maine, USA, a producer of lightweight specialty packaging, label, and publishing papers, has begun production of a fluorochemical-free, oil and grease-resistant paper
Learn More...
|
UPM, Finland, has successfully started up new Andritz (Graz, Austria) equipment for a fiberline modernization at its Kymi mill in Kouvola, Finland
Learn More...
|
Containerboard/Packaging
Both U.S. containerboard and boxboard production in October increased by 2.6% compared with October 2011, and both grades increased 0.5% from the previous month
Learn More...
|
Iggesund Paperboard, Sweden, says its 2012 Christmas card "has all of the requirements to be a classic that many people will keep for a long time."
Learn More...
|
The India-based producer of high-quality corrugated packaging materials becomes a central component of MWV's packaging platform in India and a key element of the company's plans to grow in emerging markets
Learn More...
|
Smurfit Kappa Group, Dublin, Ireland, has completed the acquisition of Orange County Container Group (OCCG) for a total cash consideration of $340 million (EUR 260 million), subject to customary post completion price adjustments
Learn More...
|
Sonoco Alcore S.a.r.l., Brussels, Belgium, a business of Sonoco, Hartsville, S.C., USA, and South Africa-based Mondi signed a multi-year agreement by which Sonoco Alcore began managing all on-site core production operations at the Mondi Syktyvkar mill in Russia on December 1
Learn More...
|
United Paper Industries Co., Kuwait, has ordered from PMT Italia (Italy) a major rebuild of its No. 1 sack kraft, fluting, and test liner machine in the Shuaiba Industrial Area of Kuwait
Learn More...
|
|
New Products
Ahlstrom, Finland, has developed a PFOA-free (contains no Perfluorooctanoic acid) version of its Ahlstrom Coralpack range, a flexible packaging paper for direct wrapping and packing of numerous grease-containing food products
Learn More...
|
BTG Instruments has officially opened a service center in Hyderabad, India, to fully support customers in the growing Indian paper industry
Learn More...
|
Deepak Nitrite Ltd. (DNL), India, a producer of organic, inorganic, and fine chemicals, reports that it is entering the global fluorescent brightening agent (FWA) market from its integrated plant in India
Learn More...
|
Smurfit Kappa, Dublin, Ireland, reports that technical experts in the design department at its operations in Herzberg, Germany, were recently presented with an interesting challenge—to optimize the existing transport packaging for premium hair care products
Learn More...
|
Published Pricing
Imerys Pigments for Paper and Packaging, Atlanta, Ga., USA, this week announced a price increase for kaolin, effective January 1, subject to any provisions in individual customer contracts
Learn More...
|
People
Boise Inc., Boise, Idaho, USA, this week announced that Judy Lassa will become EVP and COO of the company on January 1
Learn More...
|
International Paper, Memphis, Tenn., USA, this week reported that Carl Gunter will be the new mill manager of the company's Prattville, Ala., containerboard mill, replacing Don Forst, who has been named director of IP's Capital and Manufacturing Service and is relocating to Loveland, Ohio
Learn More...
|
Sonoco, Hartsville, S.C., USA, this week announced that M. Jack Sanders will become president and CEO of the company, effective April 1, 2013, when Harris E. DeLoach Jr., retires as an active employee after more than 27 years with Sonoco
Learn More...
|
TAPPI News
Active in the Polymers, Extrusion, Adhesives, Coatings, and Extrusions (PLACE) division since 1988, TAPPI member Ginger Cushing says she "has a darn good time."
Learn More...
|
Event held October 1-4 in Atlanta, Ga., USA, had more than 5,000 attendees and 286 total exhibits.
Learn More...
|
If you have not reserved your seat yet, consider saving more than $900 with your early registration - this is your last chance for early registration savings!
Learn More...
|
If you're planning a career in the industry, this event will put you on the cutting edge of some groundbreaking technology. The summit will be held January 19-21, 2013 in Raleigh, N.C., USA.
Learn More...
|
The TAPPI Shipping, Receiving, and Warehousing (SRW) Workshop, April 9-10, 2013 in Nashville, Tenn., USA, is the paper industry's premier educational and networking forum for the entire paper industry supply chain.
Learn More...
|
This long-runningTAPPI course that covers industry essentials returns January 7-10 in St. Petersburg, Fla., USA., providing information on how each individual part of a paper mill influences another.
Learn More...
|
Don't miss out on this chance to put your company's brand in front of key industry professionals who have a vested interest in your product.
Learn More...
|
Key benefits of safety training DVDs include being extremely cost effective, efficient, and portable. Playable 24/7 in any U.S. player or computer.
Learn More...
|
This part of the "Making Pulp and Making Paper" CD-ROM series is available to TAPPI members for a $39 discount off the list price.
Learn More...
|
The current economy has affected many schools' endowment funds, resulting in decreased support of student scholarships. The good news is TAPPI has stepped in to help.
Learn More...
|
After 2012 record attendance, PaperCon 2013 will bring together a wider slate of industry professionals in Atlanta, Ga., USA. April 27 - May.1.
Learn More...
|
This text covers fundamentals and processes from chemical composition of pulp to technology, production, and the environmental impact of bleaching. TAPPI members are eligible to receive a special $62 discount on this text's list price.
Learn More...
|
Joel Weldon, one of the most sought after corporate speakers in North America, provides the keynote address on Monday, April 29 at PaperCon 2013. His "Innovation Generation" address explores how industries like paper can adapt to changing consumer habits and cost containment pressures.
Learn More...
|
Learn from Ken Blanchard whose books on leadership have sold more than 20 million copies, and Mark Miller, who worked his way up from a factory line worker to vice president of one of the largest fast-food chains in the country.
Learn More...
|
Tissue360 Forum topics include an overview of hygienic product market drivers, raw material usage and supply, wet and dry end additives, latest hybrid tissue making technology, and runnabilit-operational tips.
Learn More...
|
Running The Gauntlet is a rough-and-tumble guide for running and driving change through the business gauntlet.
Learn More...
|
People who desire to lead from the middle of organizations face unique challenges, and they are often held back by myths that prevent them from developing their influence. Dr. Maxwell debunks the myths.
Learn More...
|
The International Mechanical Pulping Conference, sponsored by PI, TAPPI, PAPTAC, SPCI, and PTF to be held June 3-5, 2014, in Helsinki, Finland, has Calls for Papers due by Feb. 28, 2013.
Learn More...
|
|
Find us on Facebook
Network with us on LinkedIn
Follow us on Twitter
|
Weekly Spotlight
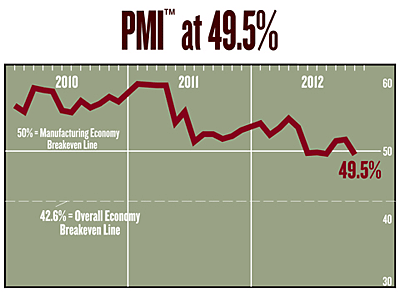 Economic activity in the U.S. manufacturing sector contracted in November following two months of modest expansion, while the overall economy grew for the 42nd consecutive month, according to the nation's supply executives in the latest Manufacturing ISM (Institute for Supply Management) Report on Business®. The report was issued this week by Bradley J. Holcomb, CPSM, CPSD, chair of the ISM Manufacturing Business Survey Committee, Tempe, Ariz., USA.
"The PMI registered 49.5%, a decrease of 2.2 percentage points from October's reading of 51.7%, indicating contraction in manufacturing for the fourth time in the past six months. This month's PMI reading reflects the lowest level since July 2009 when the PMI registered 49.2%. The New Orders Index registered 50.3%, a decrease of 3.9 percentage points from October, indicating growth in new orders for the third consecutive month. The Production Index registered 53.7%, an increase of 1.3 percentage points, indicating growth in production for the second consecutive month. The Employment Index registered 48.4%, a decrease of 3.7 percentage points, which is the index's lowest reading since September 2009 when the Employment Index registered 47.8%.
Comments from the panel this month generally indicate that the second half of the year continues to show a slowdown in demand. Respondents also express concern over how and when the fiscal cliff issue will be resolved.
Of the 18 manufacturing industries, six are reporting growth in November in the following order: Petroleum and Coal Products; Paper Products; Furniture and Related Products; Electrical Equipment, Appliances and Components; Food, Beverage and Tobacco Products; and Computer and Electronic Products. The 11 industries reporting contraction in November (in order) are: Apparel, Leather, and Allied Products; Wood Products; Primary Metals; Transportation Equipment; Chemical Products; Fabricated Metal Products; Miscellaneous Manufacturing; Nonmetallic Mineral Products; Plastics and Rubber Products; Machinery; and Printing and Related Support Activities.
The seven industries reporting growth in new orders in November (in order) are: Petroleum and Coal Products; Paper Products; Plastics and Rubber Products; Machinery; Computer and Electronic Products; Electrical Equipment, Appliances, and Components; and Furniture and Related Products. The nine industries reporting a decrease in new orders during November (in order) are: Nonmetallic Mineral Products; Apparel, Leather, and Allied Products; Primary Metals; Chemical Products; Transportation Equipment; Fabricated Metal Products; Food, Beverage, and Tobacco Products; Miscellaneous Manufacturing; and Printing and Related Support Activities.
The eight industries reporting growth in production during the month of November (in order) are: Wood Products; Electrical Equipment, Appliances, and Components; Paper Products; Food, Beverage, and Tobacco Products; Furniture, and Related Products; Miscellaneous Manufacturing; Computer and Electronic Products; and Fabricated Metal Products. The seven industries reporting a decrease in production in November (in order) are: Primary Metals; Nonmetallic Mineral Products; Apparel, Leather, and Allied Products; Chemical Products; Transportation Equipment; Machinery; and Printing and Related Support Activities.
Of the 18 manufacturing industries, seven reported growth in employment in November in the following order: Textile Mills; Paper Products; Petroleum and Coal Products; Primary Metals; Furniture and Related Products; Food, Beverage, and Tobacco Products; and Machinery. The 10 industries reporting a decrease in employment in November (in order) are: Wood Products; Plastics and Rubber Products; Apparel, Leather, and Allied Products; Electrical Equipment, Appliances and Components; Miscellaneous Manufacturing; Computer and Electronic Products; Fabricated Metal Products; Transportation Equipment; Chemical Products; and Printing and Related Support Activities.
The full text version of the Manufacturing ISM Report on Business is available online.
Back To Top
|
The newly formed TAPPI Process & Project Engineering Committee is conducting a survey to better determine what capital project strategies today's pulp and paper mills are implementing to stay in-tune and competitive under progressively lean operating conditions. To participate anonymously in this survey (no participant/mill information requested), please use the online link below. This survey will take only a few minutes to complete.
Online Capital Projects Survey
If you are interested in learning the results of the survey or would like more information on the new TAPPI Process & Project Engineering Committee, please contact Craig McKinney at TAPPI. Your participation is very much appreciated.
Back To Top
|
Below is the latest listing of job openings in the TAPPI Career Center. The current listing includes job openings for a variety of positions, including process engineer, purchasing analyst, sales managers, safety manager, shift supervisor, papermaking technology manager, research scientist, engineering intern, technical sales rep, and director of operations. Current, specific job openings at companies and locations in the TAPPI Career Center include:
Employer |
Title |
Location |
Confidential |
Process Engineer |
Denver, Col. |
Norpac-Weyerhaeuser |
Engineering Internship |
Longview/Spokane, Wash. |
Catalyst Paper |
Oper. Spec., Stock Prep/Bleaching |
Powell River, B.C., Canada |
Kruger Products |
Papermaking Technology Mgr. |
Crabtree, Que., Canada |
Catalyst Paper |
Purchasing Analyst |
Prince George, B.C., Canada |
Louisianna Pacific |
Senior Research Scientist |
Nashville, Tenn. |
New Indy Containerboard |
Shift Supervisor |
Ontario, Calif. |
Mocon |
Act. Mgr., Permeation/Outside Sales |
California |
CiDRA Chemical Mgt. |
Sales Engineer, Southeast Region |
Alabama |
RockTenn |
Safety Manager |
Eaton, Ind. |
BTG Americas |
Technical Sales Rep. |
Atlanta, Ga. |
Crane & Co. |
Dir. of Operations - Nonwovens |
Dalton, Mass. |
Crane & Co. |
Quality-Proc. Anal. Mgr.-Nonwovens |
Dalton, Mass. |
Crane & Co. |
Sales Manager - Nonwovens |
Dalton, Mass. |
More information about these jobs is available online.
Back To Top
|
Market Roundup
Total U.S. printing and writing (P&W) paper shipments decreased 2% in October compared with October 2011, primarily driven by declines in uncoated mechanical shipments, according to the AF&PA (Washington, D.C., USA) recently released October 2012 Printing-Writing Paper Report. Additional key findings of the report include:
- October shipments of coated free sheet papers increased year-over-year for the fifth time in the past 12 months, reaching the highest level since September 2010
- Shipments of uncoated free sheet paper in October increased 2% over the same period in 2011, with mill inventories at the lowest level since July 1995
October uncoated mechanical paper shipments decreased 23% compared with October 2011, with YTD shipments down 16% relative to the previous year.
Back To Top
|
The global pulp market started to recover this fall after having been in decline for more than a year, according to Wood Resources Quarterly (WRQ), Seattle, Wash., USA. World shipments increased 11% from July to September. Softwood pulp (NBSK—northern bleached softwood kraft) prices have trended downward for more than a year from their record highs in the summer of 2011. This relatively long-lasting price decline seems to have come to an end this fall and higher prices are currently being negotiated.
Hardwood pulp (BHKP—bleached hardwood kraft pulp) prices have not experienced the same price fall as NBSK prices, WRQ notes. The recent price trends for pulp have resulted in a minimal price differential between softwood and hardwood pulp.
More information is available online.
Back To Top
|
U.S. industry consumption of recovered paper in October was 2.49 million tons, 6% higher than in September 2012, according to the AF&PA (Washington, D.C., USA) October 2012 U.S. Recovered Fiber Monthly Report. Consumption was up across all grades except for newspapers, which remained at its September low and was 25% lower than in October 2011. Year-to-date total consumption in 2012 is 4% lower than during the same period last year.
U.S. exports of recovered paper remained approximately flat, dropping 1% in September compared with August. Average export $/ton figures were lower across all grades when compared with the prior month. Year-to-date exports of recovered paper in 2012 are 7% lower than during the same period in 2011.
Back To Top
|
Domestic log prices in Western Russia did not decline long-term as the Russian government had hoped when Russia increased log export tariffs to 25% in April 2008, according to the Wood Resource Quarterly (WRQ), Seattle, Wash., USA. Initially, domestic log prices fell when the tariffs were implemented, but from the 1Q/09 to the 3Q/12, the average softwood sawlog price (in ruble terms) went up by 2%, WRQ notes.
When Russia joined the World Trade Organization (WTO) in August 2012, the government was forced to reduce these export taxes to 13% and 15%, respectively, for spruce and pine logs. Despite these tariff reductions, there is not likely to be a major increase in the flow of logs from Western Russia to Finland, the major destination for Russian logs. Finnish sawmills close to the Russian border will continue to buy mostly from the domestic market in Finland, using only marginal volumes from Russia when the costs are competitive.
Over time, as lumber markets improve in Europe, exporting sawmills in Finland will need additional sawlogs, and it is therefore likely that Finland will increase its reliance on Russian sawlogs again. However, log trade between the two countries will never return to the same levels as before the implementation of the export tariffs because Finnish sawmills have now established other log sources. The decline in trade has been dramatic the past eight years, from a record high of 6.4 million cubic meters down to an estimated 600,000 cubic meters this year. Sawmills in Western Russia have kept up production relatively well during the summer months this year despite the weak lumber demand in Europe because markets in Western Europe account for a fairly small share of the Russian export volumes, WRQ explains. Instead, Egypt and former CIS countries are the major destinations for softwood lumber produced in the Western provinces of Russia, and these markets have stayed fairly healthy and even improved during 2012.
The steady demand for sawlogs by the sawmills in Northwest Russia coupled with the fairly tight log supply resulted in close to record-high price levels (in ruble terms) throughout the year, a development in contrast to many log markets in Europe where log prices have fallen the past six months, as tracked by the WRQ.
More information is available online.
Back To Top
|
Total U.S. kraft paper shipments were 128,300 tons in October, a decrease of 5% compared with the prior month, according to the AF&PA (Washington, D.C., USA) October 2012 Kraft Paper Sector Statistics Report. Total inventory was 72,900 tons in October. Both unbleached and bleached kraft paper shipments decreased year-over-year.
Back To Top
|
Pulp & Paper
American Eagle Paper Mills, Tyrone, Pa., USA, this week introduced Eagle Armour Copy paper. This new, recycled, multipurpose copy paper is treated with silver ion technology to provide antimicrobial protection to the paper itself against unwanted microorganisms such as mold, mildew, fungus, and non-pathogenic bacteria.
"American Eagle Paper Mills is proud to have successfully manufactured this paper to incorporate an antimicrobial agent within the paper without sacrificing its performance or appearance," said John Ferner, president of American Eagle Paper Mills. "The Rochester Institute of Technology performed laboratory tests on the print quality and found no noticeable difference on the treated paper versus the untreated control paper," Ferner continued.
According to BiomasterUSA LLC, supplier of the EPA registered antimicrobial silver technology used in the Eagle Armour Copy paper, silver is an element found naturally in the environment and has long been regarded as a versatile antimicrobial agent. The silver ions interact with a wide range of molecular processes within microorganisms, resulting in a range of effects from inhibition of growth, loss of energy production, and prevention of DNA replication and new cell formation.
"Additional testing performed at an independent microbiology laboratory on the antimicrobially treated copy paper demonstrated a 99.9% reduction in non-pathogenic bacteria versus untreated paper and that the antimicrobial agent lasts for the lifetime of the paper," said Ferner. "This copy paper is ideal for use in hospitals, clinics, doctor offices, dental offices, long term care and assisted living facilities, restaurant and food service facilities, schools, offices, and more."
The copy paper is 92 bright and is manufactured using recycled 50% and 100% post-consumer and industrial waste content.
The antimicrobial treatment can also be incorporated into all of American Eagle Paper Mill's product lines, which include uncoated commercial printing papers, along with wove and kraft envelope converting grades.
Back To Top
|
AS Estonian Cell, Kunda, Estonia, has ordered a new slab press and a baling line rebuild from Metso, Finland. Startup is scheduled for July 2013. The value of the order was not disclosed.
Metso's delivery will include design, supply, and erection of the equipment including a slab press and a partial baling line. The project will also include relocation of existing machinery to enable Estonian Cell to make full use of its new equipment. The new slab press and upgraded baling line will produce more than 500 air-dried metric tons of bleached aspen BCTMP (bleached chemi-thermomechanical pulp) per day.
The equipment to be supplied, together with Metso's experience and know-how of slab press and baling technology, will enable AS Estonian Cell to continuously produce high-quality bleached aspen BCTMP and improve availability of existing equipment.
AS Estonian Cell belongs to the Heinzel Group, headquartered in Vienna, Austria. The mill produces bleached aspen BCTMP mainly for the European markets. The company has 85 employees and a net annual sales of some EUR 70 million.
The order received is Metso's fourth slab press unit sold in the past 12 months, according to Andreas Lindstedt, Metso sales manager.
Back To Top
|
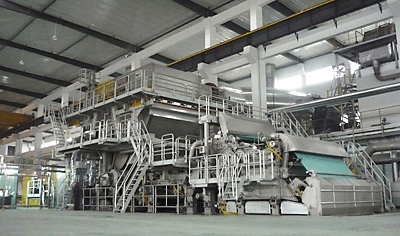 C&S Paper, China, has brought a new 28,000 metric tpy tissue machine on-stream at its mill in Chengdu City, Sichuan Province. The new machine, supplied by Italy-based Toscotec, has a wire width of 3.6 meters and a design speed of 1,600 meters/min.
Another two identical units from Toscotec will come online soon at the company's mill in Jiangmen city, Guangdong province. The first of the two additional machines is expected to startup in December, and the second will come online early next year.
C&S Paper also will install four other tissue units that it plans to bring online in 2013, raising its total capacity to more than 520,000 metric tpy. Two of these four new tissue machines, with a combined capacity of 59,000 metric tpy, have already been ordered from Toscotec. These will be erected at the Chengdu site, with startup scheduled for the second half of 2013. One of the machines will have a trim width of 3.55 meters and a design speed of 1,650 meters/min, and will be able to produce tissue at a rate of 32,000 metric tpy. The other tissue machine, with a trim width of 2.85 meters and a design speed of 1,700 meters/min, will have a production capacity of 27,000 metric tpy.
Back To Top
|
NewPage Corp., Miamisburg, Ohio, USA, will launch its Supercalendered Delivery Promise program beginning next month. Effective with confirmed orders having a requested delivery date on or after January 1, NewPage will assure that supercalendered paper will be provided to meet each and every press date.
"The Duluth, Minn., mill has been delivering on our commitments for 25 years," said Dawn Polaski, customer service manager at the NewPage Duluth mill. "We are thrilled to continue this legacy by offering the Supercalendered Delivery Promise." The Supercalendered Delivery Promise is available to all customers requesting shipments of supercalendered paper in the U.S. (excluding Alaska and Hawaii) from the NewPage Duluth mill.
"We are pleased to offer our customers the extra assurance that their paper will arrive when and where it is needed," added Ethan Haas, GM, Supercalendered Papers. "Our customer service, operations, and logistics teams have consistently proved that they have the focus, follow-through, and longevity that are superior to many other supercalendered mills in North America. Our geographical location has always provided a logistical advantage to our customers. This program will allow us to further reduce the supply risk to our customers' supercalendered papers purchasing programs."
NewPage owns paper mills in Kentucky, Maine, Maryland, Michigan, Minnesota, and Wisconsin. These mills have a total annual production capacity of approximately 3.5 million tons of paper.
Back To Top
|
Croatian-based PAN Papirna Industrija, together with China International Investment Stock, will build a new pulp and paper mill in Slatina, in northeast Croatia, EUWID Pulp and Paper, Germany, reports. According to PAN Papirna Industrija, a financing agreement worth EUR 320 million has already been signed with the Chinese investment group who will hold a 70% stake in the joint venture company Dravacel. The other 30% will be held by PAN Papirna Industrija.
Construction of the greenfield facility is to start in April next year and the entire project is scheduled for completion in 2015, Marinko Mikulić, CEO of PAN Papirna Industrija told EUWID. Upon completion, Dravacel would have a production capacity of 250,000 metric tpy of pulp and 330,000 metric tpy of coated graphic paper. The new mill also would produce up to 200,000 metric tpy of recycled and virgin-fiber packaging paper at the Slatina site, once the company had transferred and refurbished the paper machine from its paper mill in Zagreb, which is scheduled for closure in the middle of next year, Mikulić explained in the EUWID report.
Dravacel will reportedly use a perennial grass hybrid, miscanthus giganteus, as a feedstock for pulp and paper production. In addition, a geothermal power plant is to be build at the site to provide power to the pulp and paper mill.
Back To Top
|
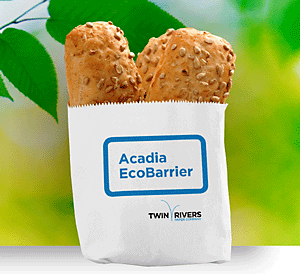 Twin Rivers Paper Co., South Portland, Maine, USA, a producer of lightweight specialty packaging, label, and publishing papers, has begun production of a fluorochemical-free, oil and grease-resistant paper. Used in food service and quick serve restaurant (QSR) packaging, Acadia® EcoBarrier offers the same functionality and performance of the company's Acadia brand, with oil and grease resistance achieved without the use of fluorochemicals.
"The QSR and food service industry are increasingly seeking fluorochemical-free alternatives for their packaging designs. Acadia EcoBarrier answers this need," said Dave Deger, director of Business Development and Marketing. "We believe this product will play an important role in the future as part of our comprehensive and growing portfolio of packaging papers."
Twin Rivers' packaging papers are known for their excellent printability and convertability, with high performance in secondary processes such as coating, waxing, foil and film laminating, and metalizing.
Acadia, an uncoated machine-finished paper, is available in a basis weight range of 15-75 lb and Bladepak C1S coated paper is available in a basis weight range of 35-73 lb. All are FDA-compliant, meeting the requirements for direct food contact.
Twin Rivers Paper Co. has operations in Maine and New Brunswick.
Back To Top
|
UPM, Finland, has successfully started up new Andritz (Graz, Austria) equipment for a fiberline modernization at its Kymi mill in Kouvola, Finland. This project is part of the mill's program to minimize effluents and upgrade production capacity. Andritz's scope of supply included a chip feeding system (TurboFeed) for the continuous digester, an oxygen delignification stage with Drum Displacer washer and knot separation, screening modernization, and modification of the A-stage bleaching process.
UPM's Kymi mill has "environmentally-friendly" integrated pulp and paper production with a high rate of energy self-sufficiency and biofuel usage. The mill produces bleached softwood and hardwood kraft pulp (total capacity 570,000 metric tpy), as well as coated and uncoated fine paper (830,000 metric tpy).
Back To Top
|
Containerboard/Packaging
Both U.S. containerboard and boxboard production in October increased by 2.6% compared with October 2011, and both grades increased 0.5% from the previous month, according to the AF&PA (Washington, D.C., USA) October 2012 U.S. Paperboard Statistics Report and its October 2012 U. S. Containerboard Statistics Report. The containerboard operating rate for October 2012 gained 0.1 points over September 2012, increasing from 96% to 96.1%. The month-over-month average daily production of containerboard, however, decreased 0.7%.
Unbleached kraft boxboard production decreased over the same month last year and decreased compared with last month. Total solid bleached boxboard and liner production increased compared with October 2011 and increased compared with the prior month. The production of recycled boxboard increased compared with October 2011 and increased compared with last month.
Back To Top
|
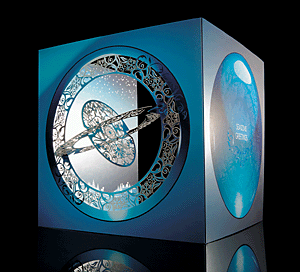 Iggesund Paperboard, Sweden, says its 2012 Christmas card "has all of the requirements to be a classic that many people will keep for a long time." The card was designed by the Netherlands-based van Heertum Design agency. For several years, Iggesund has been creating intricate Christmas cards that "demonstrate, and in the best cases stretch, the limits of what can be achieved with Invercote as the base material," the company explains.
The card's motif is a starry sky featuring both reindeer and celestial objects done in an extremely fine laser cut, complemented with several foils and then printed in three PMS inks. The tabs attaching the laser-cut sections to the rest of the card are so fine that they are hard to see, Iggesund notes, "and it is only thanks to Invercote's superior tear strength that the card stays in one piece," it adds.
"We want to produce more than a Christmas card, we want designers to challenge Invercote and give us something that reflects its essence," says Carlo Einarsson, director of market communications at Iggesund Paperboard.
Frans van Heertum, founder of van Heertum Design and winner of a number of awards for sophisticated printing projects, has done large, advanced projects a number of times using Invercote as the base material. One recent project is his contribution to Iggesund's Black Box Project, in which he printed a series of cards. Each paperboard sheet was printed using three different techniques and more than 30 inks and varnishes. The printed sheets then passed through various finishing stages a total of 14 times.
"I take on these projects because I want to know how far the material can be pushed," van Heertum says.,
This year's Christmas card is made of Invercote Creato 350 gsm and van Heertum Design VHD was responsible for both the design and implementation. The agency was assisted by a group of Dutch suppliers, including as the printers Drukkerij Tielen, Boxtel, and the foil printers Hensen Foliedrukkers, Oirschot, using foil supplied by Leonhard Kurz Benelux of Nijmegen. The characteristic laser cutting was done by Point to Paper, Waalwijk.
Back To Top
|
MeadWestvaco Corp., Richmond, Va., USA, this week announced the completion of its purchase of Ruby Macons Ltd. The India-based producer of high-quality corrugated packaging materials becomes a central component of MWV's packaging platform in India and a key element of the company's plans to grow in emerging markets. Financial results for Ruby Macons will now be reported as part of MWV's Industrial Packaging segment.
Ruby Macons is a global market leader in corrugated packaging materials in India. The company currently produces more than 150,000 metric tpy of containerboard at two mills containing three paper machines in and around the city of Vapi, Gujarat. These assets, as well as a significant expansion project underway, will significantly increase capacity and accelerate MWV's profitable growth in this fast growing region, the company noted.
"We are excited to welcome Ruby Macons into the MWV family, marking an important step forward in our long-term commitment to growth in India," said Peter C. Durette, SVP and chief strategy officer for MWV, who oversees the company's business in India.
Under the terms of the transaction, all Ruby Macons employees will become MWV India employees and the Ruby Macons management team will remain in place, including Ashraf Nathani, managing director, Ruby Macons, who becomes vice chairman and president of the business.
Nathani said that "this deal reflects the commitment of both organizations to India. We are proud to be joining forces with MWV and confident that the combination of our strengths will bring value for all our employees, customers and suppliers."
The acquisition of Ruby Macons expands MWV's presence in industrial packaging in India, which also includes a converting facility in Pune making rigid, humidity-resistant corrugated packaging for fresh fruits and vegetables, consumer goods, household appliances, and pharmaceuticals. MWV also delivers innovative packaging solutions for a variety of consumer goods markets in India, including healthcare, beauty and personal care, home and garden, and beverage. It also markets specialty chemicals for asphalt paving and other specialty chemicals markets.
Back To Top
|
Smurfit Kappa Group, Dublin, Ireland, has completed the acquisition of Orange County Container Group (OCCG) for a total cash consideration of $340 million (EUR 260 million), subject to customary post completion price adjustments. The $340 million cash consideration is being funded from the Group's existing cash resources.
OCCG is a corrugated and containerboard manufacturer with operations predominantly in Northern Mexico but also in the Southern U.S., and will form part of the Group's Latin America segment. OCCG employs 2,800 people (2,000 of whom are employed in Mexico), and is expected to generate at least $53 million of EBITDA for the full year 2012.
Gary McGann, Smurfit Kappa Group CEO, noted that the acquisition is "fully consistent with our declared growth strategy, complements our existing Mexican business, and increases our exposure to a demographically attractive and rapidly growing region. We remain comfortably within our stated leverage guidance of below three times and the acquisition delivers value through earnings accretion (year 1). Our focus now is on the effective integration of our businesses in the region, which gives us an exciting platform to continue to provide creative packaging solutions to both current and prospective customers."
Back To Top
|
Sonoco Alcore S.a.r.l., Brussels, Belgium, a business of Sonoco, Hartsville, S.C., USA, and South Africa-based Mondi signed a multi-year agreement by which Sonoco Alcore began managing all on-site core production operations at the Mondi Syktyvkar mill in Russia on December 1. According to the agreement, Sonoco will purchase Mondi's existing core equipment and then replace it with newer state-of-the-art technology equipment.
The new equipment will include one winder, one in-line cutting machine, and two off-line core cutters, as well as core drying chambers. In addition, Sonoco will manage 28 employees responsible for core production on site.
Mario Freissl, head of supply chain and procurement and a member of the board, said that "with this agreement, Mondi will receive more stabilized and reliable core quality, and gain access to Sonoco Alcore's operational and technological leadership."
Adam Wood, VP, Industrial Converting Europe, added that the agreement "allows Sonoco to expand its manufacturing footprint in a high-growth market, with the potential to serve additional customers from this location. It also demonstrates our ability to convert self-manufacturers, and aligns with our growth strategy in the Russian core market."
The Mondi Syktyvkar mill currently operates one board machine and three paper machines, producing up to 1 million metric tpy. Paper production includes office paper, offset paper, newsprint, and linerboard for corrugated medium. The Syktyvkar operations have more than 3,000 employees at the mill and an additional 3,000-plus people in the local forests harvesting wood for pulp and paper production. Since the acquisition of the German company Nordenia in 2012, Mondi also operates a plant that produces packaging in a central part of Russia.
Sonoco Alcore supplies industry-specific cores to a variety of markets including the paper, textiles, plastic film, and construction industries. With 28 manufacturing locations and five paper mills in Europe, the company can supply facilities anywhere in Europe, the Middle East, and Africa.
Back To Top
|
United Paper Industries Co., Kuwait, has ordered from PMT Italia (Italy) a major rebuild of its No. 1 sack kraft, fluting, and test liner machine in the Shuaiba Industrial Area of Kuwait. The 2.6-meter-wide machine produces the three grades mainly from local OCC (old corrugated containers).
The project is expected to improve production capacity and paper strength by adding a new press section with ÆGO™FLX Shoe DP, a new ÆGO™Sizer P, and a new ÆGO™Reel C. Other parts of the machine will also be modernized.
With startup of this project, planned for the fourth quarter of 2013, PMT will have the first ÆGO™FLX Shoe DP unit in the Middle East.
Back To Top
|
New Products
Ahlstrom, Finland, has developed a PFOA-free (contains no Perfluorooctanoic acid) version of its Ahlstrom Coralpack range, a flexible packaging paper for direct wrapping and packing of numerous grease-containing food products, such as biscuits, pastries, coffee beans, fast food, take-away food, pizzas, popcorn for micro wave, butter and margarine, soup cubes, and others.
To produce grease resistant packaging papers, fluorochemicals are added in the paper production process. However, as Ahlstrom explains, deriving from the production process of these fluorochemicals, trace amounts of PFOA can be found as an unintended impurity. In January 2006, the U.S. Environmental Protection Agency (EPA) invited manufacturers of fluorochemicals to commit to reduce by 95% PFOA from their emissions and products content not later than by 2010 and to eliminate it totally by 2015.
To offer its customers a grease resistant paper free of this unintended impurity, Ahlstrom Group Product & Technology Development services designed the new generation of grease resistant papers. Now, the entire Ahlstrom Coralpack paper range is available on request in a New Generation (NG) version, free of PFOA.
The new product's paper range spans from 32 to 200 gsm and provides high performance paper characteristics such as printability, laminating, extrusion, and crimping. Coralpack is produced at Ahlstrom's Rottersac plant in southwestern France.
Back To Top
|
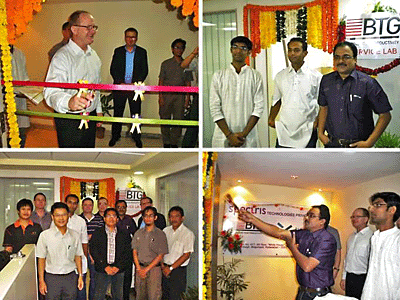 BTG Instruments has officially opened a service center in Hyderabad, India, to fully support customers in the growing Indian paper industry. The opening ceremony was conducted according to Indian tradition with a puja ritual for deity Ganesh with garlands, lighting the lamp, incense stick, coconut breaking, and food offerings for blessings.
The occasion also marked the start for a first service training in the facility that will further offer accredited repair, maintenance, upgrade, and calibration of BTG sensors, laboratory devices, and analyzers. A laboratory is available for sample testing and user training.
The Indian center is staffed by experienced BTG service engineers handling inside and outside service, spare part requests, and all application and sales inquiries.
BTG Instruments India is a division of Spectris group, India. The Hyderabad office is also home for another Spectris company PANalytical.
Back To Top
|
Deepak Nitrite Ltd. (DNL), India, a producer of organic, inorganic, and fine chemicals, reports that it is entering the global fluorescent brightening agent (FWA) market from its integrated plant in India. The site will supply about 200 million lb annually to the paper, detergent, and textile markets.
Noting that it is the only fully backward integrated producer of FWAs in the world, DNL says it will be able to leverage its manufacturing expertise with quality registered through the most stringent regulatory bodies worldwide and full spectrum technical support pre- and post-purchase.
The company's production site is located at Dahej, the largest of India's new "Islands of Excellence" initiatives, and features full access to port facilities, power, water, and other utilities, most raw materials, and road transport. The product itself will be sold in every variation of the diaminostilbene range and will be backed by an innovation team and application labs in all segments for testing and post-sales support, the company points out.
More information is available online.
Back To Top
|
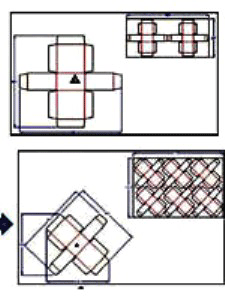 Smurfit Kappa, Dublin, Ireland, reports that technical experts in the design department at its operations in Herzberg, Germany, were recently presented with an interesting challenge—to optimize the existing transport packaging for premium hair care products. The tricky part was that no part of the construction could be changed.
To offer the best solution, the product designer at Smurfit Kappa went against convention and rotated the direction of the corrugations on the E-corrugated board. The twisted arrangement of the cuts on the punching sheet resulted in a considerable improvement in the layout. This led to customer savings of 20% in the packaging.
In addition, the improved technical characteristics meant that the diagonal corrugation achieved a roughly 13% higher BCT value (stacking compressing resistance, measured by a Box Compression Test). This also meant that the machine operation could be improved—with the improved flatness and uniform bending resistance of the grooves, the blanks are cut more smoothly and thus processed faster.
This packaging was recognized at the Smurfit Kappa Innovation Awards, winning in the industrial category.
Back To Top
|
Published Pricing
Imerys Pigments for Paper and Packaging, Atlanta, Ga., USA, this week announced a price increase for kaolin, effective January 1, subject to any provisions in individual customer contracts. The prices of kaolin produced in the U.S. and Brazil, including calcined kaolin products, will increase by 5% to 7%.
Imerys notes that cost increases in logistics, mining, chemicals, fuel, and power are key factors in the price increase decision. Despite its "continual improvement programs and cost reductions to mitigate these effects, the price increases are necessary to achieve a sustainable business," the company said.
Imerys Pigments for Paper and Packaging s a global producer of white pigments, manufacturing kaolin, talc, ground calcium carbonate (GCC), and precipitated calcium carbonate (PCC). The business group serves the international paper and packaging industries and employs 2,414 people at 47 industrial sites in 19 countries. It represents 23% of Imerys' sales.
Back To Top
|
People
Boise Inc., Boise, Idaho, USA, this week announced that Judy Lassa will become EVP and COO of the company on January 1. In her new role, Lassa will provide leadership for all of the company's business units.
"Judy has an exceptional track record of leading her teams to deliver excellent safety, operational, and financial performance," CEO Alexander Toeldte noted. "She is also deeply committed to developing people. I know Judy will make strong contributions as she takes on this well-deserved, expanded role."
Lassa began her 30-yr career with Boise at the St. Helens, Ore., mill as a process engineer after graduating from the University of Wisconsin-Stevens Point with a bachelor's degree in paper science and engineering. She moved to the Vancouver, Wash., mill in 1986 and then to the Portland , Ore., office as marketing services manager. In 1991, she became pulp mill/wood yard superintendent at DeRidder, La., and in 1994 returned to the Vancouver mill as paper operations manager. After working in a variety of operational and marketing roles, Lassa moved to Boise as GM of the packaging business in 1997. She became an officer in 2000 and SVP of the paper business in 2010.
Also effective January 1, Bob Warren, EVP and COO, will transition at his request to a non-officer role within the company. Warren will continue to work as an advisor to the senior management team and as a coach to leaders throughout the company.
"Bob has made pivotal contributions to our company and its predecessors over many years," says Toeldte. "He successfully led the paper business through the startup of Boise Inc. and transformed our supply chain organization to best-in-class status. Bob leads by focusing on possibilities and getting people to make them happen. We regret and respect Bob's desire to step back but are delighted that he will continue to contribute to the company."
Boise's range of packaging products includes linerboard and corrugating medium, corrugated containers and sheets, and protective packaging products. Boise's paper products include imaging papers for the office and home, printing and converting papers, and papers used in packaging, such as label and release papers.
Back To Top
|
International Paper, Memphis, Tenn., USA, this week reported that Carl Gunter will be the new mill manager of the company's Prattville, Ala., containerboard mill, replacing Don Forst, who has been named director of IP's Capital and Manufacturing Service and is relocating to Loveland, Ohio. Gunter most recently was manager of the company's s Pensacola, Fla., containerboard mill. He has some 30 years of experience in the paper industry.
IP concurrently named Brett DeJong mill manager at its Pensacola mill. DeJong most recently was operations manager at IP's Augusta, Ga., coated paperboard mill.
Back To Top
|
Sonoco, Hartsville, S.C., USA, this week announced that M. Jack Sanders will become president and CEO of the company, effective April 1, 2013, when Harris E. DeLoach Jr., retires as an active employee after more than 27 years with Sonoco. Sanders also was elected to Sonoco's board of directors, effective immediately, increasing the board to 13 members.
Sanders is currently president and COO of Sonoco and has global leadership, sales, and operating responsibility for all of the company's diversified packaging businesses. DeLoach is currently chairman and CEO, a position he has held since July 2000. He has been a member of Sonoco's board since 1998 and chairman of the board since 2005, and will remain its executive chairman following his retirement on March 31, 2013.
"During his 25-year career with Sonoco, Jack has played an integral role in helping to grow the company and successfully led many of our consumer, industrial, and protective packaging businesses," said DeLoach. "Jack is an extremely talented leader who has proven that he's ready to serve as Sonoco's eighth CEO over our 113-year history."
A graduate of Louisiana State University with a B.S. degree in finance, Sanders joined Sonoco in 1988 as national sales and marketing manager for the company's reels business. In 1992, he was asked to build and lead the development of Sonoco's new protective packaging business as its general manager. He was promoted in 1998 to division VP and GM of protective packaging.
Sanders was elected a corporate officer and named VP, Industrial Products, North America, in 2001. He was subsequently named VP, Global Industrial products in January 2006 and assumed responsibility for all industrial converting businesses as SVP in July 2007. In 2008, he was named EVP, Industrial, with global operating responsibility for all of the company's businesses serving industrial markets, including Sonoco's tubes and cores, paper, reels, protective packaging, paperboard specialties, and recycling businesses. Prior to assuming his current position, Sanders served as EVP of Sonoco's Global Consumer businesses, where he was responsible for rigid paper and closures, rigid plastics, flexible packaging, and display and packaging businesses.
During DeLoach's 12 years as CEO, Sonoco has grown sales from $2.7 billion to a projected $4.75 billion at the end of 2012, while its asset base has nearly doubled to more than $4 billion. Also during his tenure, the company has returned approximately $1.6 billion to shareholders in cash dividends and share repurchases and has provided a total shareholder return of approximately 153% through Oct. 31, 2012. While he served as CEO, Sonoco made more than 50 acquisitions and Sonoco was transformed from primarily a company serving industrial packaging markets to a diversified global consumer, industrial, and protective packaging company.
Back To Top
|
Sonoco, Hartsville, S.C., USA, this week announced that John M. Colyer Jr. has been named SVP, Global Industrial Products and Protective Solutions, and Rob C. Tiede has been named SVP, Global Consumer Packaging and Services, according to M. Jack Sanders, president and COO, and the company's CEO-elect. These appointments are effective January 1.
Colyer, formerly VP, Global Industrial Converting, will have responsibility for the company's Global Paper, Tubes and Cores, Reels, Protective Solutions, and related support businesses. Tiede, formerly VP, Global Flexibles and Packaging Services, will have responsibility for the company's Corporate Customer program as well as its Global Rigid Paper, Closures, Rigid Plastics, Flexibles, and Display and Packaging businesses.
"John and Rob are veteran leaders of our global packaging businesses and have demonstrated an ability to build strong businesses and effective leadership teams," said Sanders. "John has been instrumental in optimizing our global industrial-related businesses and in pursing the acquisition of Tegrant Holding Corp., which led to the formation of our growing Protective Solutions business. Rob has successfully led efforts to rebuild our Flexible Packaging and Display and Packaging businesses, while evolving our marketing efforts and serving as executive sponsor for our IT systems integration."
Colyer has 29 years of experience with Sonoco and held numerous leadership and manufacturing positions in businesses serving industrial and consumer markets. He is a graduate of Southern Oregon State University with a B.S. degree in business administration.
Tiede joined Sonoco in 2004 as head of the company's Display and Packaging business following the acquisition of CorrFlex Graphics' point-of-purchase display and supply chain management business. He was named division VP and GM of Sonoco's Flexible Packaging division in 2007 and became VP, Global Flexibles and Packaging Services in 2009. Prior to joining Sonoco, Tiede was EVP of Graphic Packaging International, president of Sterling International, and president of Bostic Packaging/CorrFlex. He received a business administration diploma from Red River Community College in Winnipeg , Manitoba, Canada, and is a Canadian Charted Accountant.
In other executive appointments, Sonoco announced that Rodger D. Fuller, previously VP, Global Rigid Plastic and Corporate Customers, has been named group VP, Paper/Tubes and Cores, North America, reporting to Colyer. In this new position, effective January 1, Fuller will be responsible for improving the vertical integration of the company's North American Paper, Tubes and Cores, Recycling, and internal supply businesses.
Fuller joined Sonoco in 1985 and has held a number of senior leadership positions primarily in the company's Consumer Packaging segment, including running the global composite can, Rigid Plastics, and North America and European consumer products operations. Fuller graduated from Berry College with a B.S. degree in business administration and earned an MBA from Emory University.
With Fuller's appointment, R. Howard Coker, previously VP, Global Rigid Paper and Closures, has been given the additional responsibilities as group VP, Global Rigid Paper and Plastics, reporting to Tiede. The appointment is effective January 1. During his career at Sonoco, Coker has held numerous leadership positions, including VP, Rigid Paper and Closures, North America; division VP and GM, Sonoco Phoenix; director of sales and marketing, Rigid Paper and Plastics; and GM, Asia/Pacific, Rigid Paper, and Plastics. He is a graduate of Wofford College with a B.A. in business administration and holds an MBA in business administration from Wake Forest University.
Ronald G. Leach Jr., VP, Protective Solutions, has decided to retire from Sonoco, effective March 31, 2013. Replacing Leach will be Vicki B. Arthur, VP, Protective Solutions, reporting to Colyer. The appointment is effective April 1, 2013.
Arthur was previously VP, Global Corporate Customers, and division VP and GM of Sonoco's Kraft Corporate Customer team where she had global packaging relationship responsibility for the former Kraft Foods. She joined Sonoco in 1984 and held various finance positions, including staff VP and treasurer. Arthur graduated from the University of South Carolina with a B.S. degree in accounting and holds an MBA in business from Duke University. She is a Certified Public Accountant.
Leach, 55, joined Sonoco after serving as president and CEO of Tegrant. He was also president and CEO of Alloyd Co. and served as a GM of TriEnd Corp. and has held several other leadership roles in the packaging industry. Leach holds a B.S. degree in packaging engineering from Michigan State University.
Back To Top
|
TAPPI News
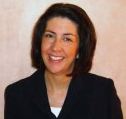 An Andreas Ahlbrandt winner, TAPPI member Ginger Cushing says being an active member of TAPPI's PLACE Division has served her professional development well by providing a solid network of packaging experts whose knowledge helped her win new business on many occasions. "They helped me understand the individual elements of packaging and how our components and processes work in concert," she said.
Cushing first joined TAPPI in 1988 when her colleagues at Mica, where she was a bench chemist, began urging her to do so. "They made me see it was the place to be," she said. Since then, she has held various chair positions, conducted courses, and has written and delivered numerous white papers. In addition to the Ahlbrandt award, Ginger was also named one of TAPPI's Finest Faculty for her participation in courses and symposia, and is a past recipient of the best paper and best session awards.
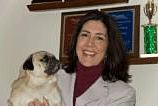 Ginger says being so active in TAPPI has provided many lasting benefits to her career, including a go-to network of packaging experts whose knowledge has helped her win new business on many occasions. "They help me understand the individual elements of packaging and how our components and processes work in concert."
If you would like to be featured in this section, or would like to suggest a fellow member to profile, please fill out the Membership Questionnaire and return it as an attachment to MemberSpotlight@tappi.org.
Find out more by reading this month's Member Spotlight.
Read the full TAPPI In-the-Spotlight to see this member's bio and related Q&A section.
Back To Top
|
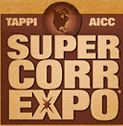
Final results now in for SuperCorr Expo 2012 clearly demonstrate that the event was a big success by any measure. Total attendance at the four-day conference and exhibit was more than 5,000, representing 52 countries from around the world, with 47% of attendees from box plants. SuperCorr Expo, held October 1-4, 2012, in Atlanta, Ga., was a joint venture of TAPPI and AICC.
"The strong attendance and large number of exhibitors at this year's SuperCorr Expo clearly demonstrate the value this event provides for the North American and international corrugated container industry," says Larry N. Montague, TAPPI president and CEO. " A comprehensive program designed to interest and educate attendees from all areas of the industry, and an exhibit featuring the latest in manufacturing technology and box plant operations, made this a must-attend event for manufacturers, vendors, and anyone interested in this industry."
Details on this year's event include the following: total number of exhibitors, 286; total exhibit space, 121,421 sq. ft.; total attendees, 5,050; paid conference attendees, 445; international countries represented, 52; attendees utilizing box plant group rate, 667; companies taking advantage of the box plant rate, 104; additional individual box plant or converter exhibit visitors, 1,399; exhibitor representatives, 2,184; proportion of box plant attendees to the total, 47%.
SuperCorrExpo is the largest corrugated industry trade show in the Western Hemisphere. Visitors get an up-close, hands-on look at the latest technology and innovation in corrugated box manufacturing and also participate in a wide range of educational sessions that provide attendees information on how to enhance the efficiency, productivity, quality, safety, and profitability of their operations.
SuperCorrExpo 2016 will be held in Orlando, Fla. USA, October 17-20. If you missed SuperCorrExpo 2012, please visit our site to view videos and photos of the Expo.
Back To Top
|
You'll be joining 33 other companies represented among the participants already registered...
Why should you attend?
The TAPPI Kraft Recovery Course is taught by 15 leading instructors with vast knowledge in specific areas of the kraft recovery process. Yes, 15 instructors - an impressive faculty panel.
This course is designed for pulp mill operators including:
- Engineers and superintendents new to the kraft recovery area
- Senior pulp mill operators
- Superintendents looking for new kraft recovery ideas or a refresher course
- Process engineers
- Technical sales and support staff from chemical, equipment, and consulting companies.
See the full course schedule (in downloadable pdf format)
Take a look at the impressive faculty experience planned for this course.
The hotel reservation cut off for the TAPPI rate is December 6.
Back To Top
|

If you're planning a career in the pulp and paper (or packaging) industry, this event will put you on the cutting-edge of some groundbreaking technology.
Make plans now to attend the 2013 TAPPI-PIMA Student Summit, January 19-31, 2013, in Raleigh, N.C., USA.
This is a rare opportunity for advanced undergraduate and graduate students to meet face-to-face with industry leaders and gain valuable information on what forces are shaping the industry today - plus the added bonus of the inside track on employment and career development.
Program Session Topics:
- Mock Interview Session/Resume Critique
- Myth vs. Fact of the Industry
- Voith Fabrics Presentation
- Printed Electronics
- Future of Carbohydrates
- Career Path Panel: Grad School vs. Job
- BioEnergy
- Project Management.
The 2013 TAPPI-PIMA Student Summit includes:
- An Engineering Competition
- Networking and a Career Fair
- Scavenger Hunt
- Multiple Tours of Industry Facilities
- Interviews with Hiring Companies.
Sponsorships are available. For more information, contact David Bell.
Back To Top
|
The TAPPI Shipping, Receiving and Warehousing (SRW) Workshop, April 9-10, 2013, in Nashville, Tenn., USA, is the paper industry's premier educational and networking forum for the entire paper industry supply chain. The workshop provides anyone interested in the logistics and shipment of paper the opportunity to see new technology and hear experts on a wide range of topics – all under one roof - focused on reducing in-transit damage.
"The safe, damage-free shipment of paper products to customers around the world is a very important element of pulp and paper industry logistics," notes Larry N. Montague, TAPPI president and CEO. "A wide range of factors can cause damage during shipment and the SRW Workshop is the premier event focusing on how mills, and their customers, can lower costs and improve product quality by reducing damage to rolls during transit."
The SRW Workshop is an interactive and collaborative workshop put on by industry professionals representing the entire paper supply chain, including shippers, carriers, printers, and publishers. Presentations and collaborative discussions on topics including car quality, safe truck loading and securing, intermodal loading and securing, damage classification, inspection, and claims procedures are provided. Experts with extensive experience and practical background knowledge representing Class 1 railroads, intermodal providers, warehouses, shippers, and dunnage manufacturers are part of the extensive program offered during this two-day workshop.
For more information visit the SRW website.
Back To Top
|

Registration is now open for the TAPPI Introduction to Pulp and Paper Technology Course scheduled for January 7-10, 2013 in St.Petersburg, Fla., USA.
This is one of TAPPI's longest running courses. Why is this course one of our most popular?
Intro to Pulp and Paper Technology is unique in that it provides information on how each individual part of a paper mill influences another. This course allows you to understand how materials, pulping, and paper-making processes affect paper and board properties. You will also be delivered a broad overview of pulping and paper-making technology, including the entire pulping and paper-making process from raw materials and wood prep. to pulping and mill operations.
Four Reasons to attend Intro to Pulp and Paper Technology:
- Course pre-surveys will ensure this course meets attendees individual needs
- You will have networking opportunities during hourly breaks
- This course measures up the MOST training content in the SHORTEST amount of time
- You get the instruction of Dr. Michael Kocurek and can learn from his 45 years of experience on this topic.
Who benefits?
- Pulp and paper company employees - new technical/operating staff, operators, non-technical personnel, chemical and direct equipment suppliers, technical service professionals, and sales people.
This course is taught by Dr. Michael J. Kocurek, Professor Emeritus, Paper Science & Engineering at North Carolina State University. Dr. Kocurek is one of the world's most recognized educators in the field of pulp and paper industry science.
Back To Top
|

The 2013 International Conference on Nanotechnology for Renewable Materials will be held June 24-27, 2013, on the campus of the KTH Royal Institute in Stockholm, Sweden.
TAPPI invites you to sponsor this exciting event.
Put your company's brand in front of key industry professionals who have a vested interest in your products. This internationally known event brings together leading researchers, industry experts, government representatives, and other stakeholders to share advances, perspectives, and discuss new ideas and breakthrough concepts on nanotechnology-based advances. Don't miss this valuable opportunity to meet key decision makers from a variety of industries while they're spending dedicated time learning and exploring ideas for the future.
As a sponsor or tabletop exhibitor, you will meet and interact with potential customers and industry leaders in this breakthrough technology area. Given the expanded program focus of the 2013 event, meeting participants will cross-cut a variety of industries and applications. This is a great opportunity to expand or enhance your marketing base with your expertise.
Please review the Sponsorship Prospectus and select the package that best meets your needs.
For sponsorship inquiries, please contact Raine Hyde at 1 770-209-7256.
For continually updated conference information please visit the event's website.
Take a look at the current list of participants.
Back To Top
|
TAPPI Press is known around the world as an industry-specific publisher of current, reliable, practical, and useful products that help members, students, and other readers enhance their technical knowledge to solve technical problems. TAPPI now offers safety training on DVD.
Key benefits of DVD training include:
- Extremely cost-effective, efficient, and portable
- Pay only for neccessary courses
- Simple, flexible, and reusable format
- No need for Internet connectivity
- Playable 24/7 in any U.S. DVD player or computer.
More information in available online for the following Safety Training DVDs:
- Arc Flash Safety DVD
- Bloodborne Pathogens DVD
- Combustible Dusts DVD
- Fire Safety DVD
- Forklift Safety DVD
- Hand and Power Tools DVD
- Hexavalent Chromium DVD
- Lockout Tagout DVD
- Slips, Trips and Falls DVD.
Back To Top
|
Towel and Tissue Papermaking is the last of the 15 CD-ROMs in the Making Pulp and Making Paper CD-ROM Series. Through this highly interactive, self-paced CD-ROM, participants learn towel and tissue papermaking terms, concepts, and processes.
Learning outcomes
After completing the Towel and Tissue Papermaking CD-ROM, participants should be able to:
- Explain how the manufacturing of towel and tissue grades is different from other grades of paper
- Describe the different types of tissue formers
- Explain the TAD process and its advantages and disadvantages.
Benefits for Everyone
The series is designed for anyone who would benefit from a working knowledge of the pulping and papermaking process, including:
- Paper machine operators
- Process and product engineers
- Sales and technical support staff
- New employees
- Students.
It will also be beneficial to experienced production or technical employees who need a more thorough understanding of a specific area of the operation, especially for cross-training purposes. New employees of chemical and equipment suppliers and paper industry consultants will also benefit from this series.
The complete set of 15 Making Pulp and Paper CD-ROMs
is also available.
Product code: MPP-15
Member Price: $78.00
Non-member Price: $119.00
Back To Top
|
TAPPI has scholarships to offer. You have a chance to apply for some green (funds to pay tuition, etc.) to fund a satisfying green career. These scholarships are available for graduate and undergraduate students with an interest in the pulp, paper, converting, and packaging industries. There are two general types of scholarships:
- TAPPI Division Scholarships
- William L. Cullison Memorial Scholarship.
What this message means to you:
If you're a student, here is a great way to apply for financial assistance for the 2013-2014 school year. Note that requirements will vary according to scholarship source, so you'll need to check the qualifications carefully. A reference document is available to guide you.
The deadline to apply for Technical Division Scholarships is February 15, 2013; the deadline for the Cullison scholarship is May 1, 2013. Mark your calendar now to allow yourself time to create an application that reflects the hard work you've been investing in your career.
If you are affiliated with a college or university, share this with your students, peers, or other staffers who work with students. They will be glad you did
If you're in the industry, perhaps you know of students worthy of scholarship assistance with their education, please pass this information along.
Back To Top
|
After a record attendance in 2012, PaperCon will bring together a wider assortment of CEOs, mill managers, superintendents, scientists, process engineers, and suppliers for the 2013 conference, scheduled for April 27 to May 1, in Atlanta, Ga., USA. PaperCon 2013 has expanded its already comprehensive technical program to include two new events covering tissue and nonwovens technology.
"PaperCon 2013 attendees will benefit from an expanded program providing additional learning and networking opportunities in several key areas," comments Larry N. Montague, TAPPI president and CEO. "Two co-located events - Tissue360º Forum and NETInc – will make new tissue and nonwovens tracks available to full conference registrants. Expanded coverage of these dynamic industry segments makes PaperCon an even more valuable resource."
PaperCon's large and comprehensive technical program, the industry's largest, offers a range of topics including Management (PIMA) Papermaking, Coating and Graphic Arts, Recycled Paperboard (RPTA Production - Technical Seminar), and Reliability (OpEx Workshop). An array of networking opportunities such as the PaperCon trade fair, receptions, lunches, and committee meetings, and a New Technology Showcase will make it the industry's must-attend event in 2013.
More information is available online.
Back To Top
|
This text, edited by Carlton W. Dence and Douglas W. Reeve, covers fundamentals and processes from the chemical composition of pulp to the technology, production, and the environmental impact of bleaching. Designed as both a textbook and a reference book, Pulp Bleaching: Principles and Practice explains what bleaching is, why pulp is bleached, and how bleaching is done.
The book also features discussions on several "hot topics" in pulp bleaching, including elemental chlorine free bleaching, totally chlorine free bleaching, enzyme assisted bleaching, and bleaching of recycled fiber. In addition, the book is key-word indexed and each chapter contains extensive references.
Pulp Bleaching: Principles and Practice
Product code: 0102B061
Member Price: $124.00
Non-Member Price: $186.00
Back To Top
|
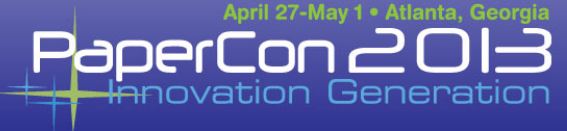

Joel Weldon, one of the most sought after corporate speakers in North America, will provide the keynote address on Monday, April 29 at PaperCon 2013. Weldon is an award winning speaker renowned for his well-researched, informative, and engaging presentations. At PaperCon, Weldon will be addressing "Innovation Generation," how industries like paper can adapt to changing consumer habits and cost containment pressures.
Weldon has been an idea consultant, sales trainer, and executive speech coach for many of the world's leading organizations and businesses for well over three decades. He's widely known as one of North America's most highly respected and sought-after corporate speakers. His presentations are known for effectively and specifically addressing each audience and their unique business and industry challenges, fears, risks, and opportunities.
Weldon is one of an elite group of speakers to have earned all four of the highest honors in the speaking profession. They include induction into the Speakers Hall of Fame, the coveted Communication & Leadership Award, The Golden Gavel, "for his profound impact on corporate America," and in 2006 being named "Legend of the Speaking Profession." He turned down a four-year college scholarship because he thought he wasn't "smart enough" to go to college. A former construction worker, he's living proof that human potential can be tapped, and your entire life transformed, when even one good idea is presented, accepted and acted upon.
PaperCon 2013 will feature the world's largest paper industry technical program. It has been expanded to include both tissue and nonwovens programs in 2013. PaperCon takes place April 27 through May 1, 2013, in Atlanta, Ga., USA.
Learn more about PaperCon.
Back To Top
|
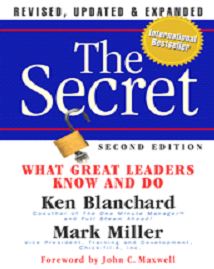
The Secret, Second Edition
What Great Leaders Know and Do
By: Ken Blanchard & Mark Miller
- Uses the popular "business fable" format that Ken pioneered
- Explains the five essential practices exhibited by the best leaders and provides practical ideas on how to make these a reality in your life.
At one time or another, everyone in a position of authority-whether in a multinational corporation or a local volunteer group-wonders what the key to great leadership is. And who better to answer that question than the team of Ken Blanchard, whose books on leadership have sold over 20 million copies, and Mark Miller, who worked his way up from line worker to vice president of one of the largest fast-food chains in the country. In The Secret, Blanchard and Miller use the uniquely accessible "business fable" format that Blanchard pioneered to get at the heart of what makes a leader truly able to inspire and motivate people. Debbie Brewster, recently promoted and struggling, finds herself about to lose her job due to poor performance. In an attempt to save her career, she enrolls in a new mentoring program offered by her company. Much to her surprise, Debbie finds her mentor is none other than Jeff Brown, the president of the company. Debbie decides that she is going to ask her new mentor the one question she feels she desperately needs answered: "What is the secret of great leaders?" Jeff's immediate answer-that great leaders serve their followers-completely flummoxes Debbie. Over the next 18 months, Jeff helps Debbie discover and explore five fundamental ways that leaders lead through service.
The Secret puts what Blanchard and Miller have learned about leadership in a form that anyone can easily understand, embrace, and pursue. It is a book that will benefit not only those who read it, but also the organizations they work in an the people who look to them for guidance.
The second edition includes revised and updated content including:
- A new foreword by John Maxwell
- A new resource section in the back matter summarizing key learning points
- A greater focus on the book's primary focus: servant leadership
- A more humanized protagonist
- Numerous other minor renovations throughout.
Ken Blanchard, coauthor of The One Minute Manager, the bestselling business book of all time!
Item #: 12SECRET
View the Table of Contents and Preview.
Member Price: $23.00
Back To Top
|
The Tissue360 Forum, organized by TAPPI tissue experts in conjunction with Tissue360 magazine, will be held April 29 - May 1, 2013 at PaperCon 2013 in Atlanta, Ga., USA. The forum will cover a wide range of tissue manufacturing and converting technologies and market trends. PaperCon 2013 will be the pulp and paper industry's largest technical conference and trade show.
"The inclusion of the Tissue360 Forum at PaperCon 2013 will add comprehensive coverage of this dynamic segment to the industry's best technical program," notes TAPPI President and CEO Larry Montague. "The forum will provide business insights and peer-reviewed technical papers covering developments in one of the industry's most rapidly growing and technically innovative grade sectors."
Tissue360 Forum topics will include an overview of hygienic product market drivers, raw material usage and supply, wet and dry end additives, latest hybrid tissue making technology and runnability/operational tips. All material will be selected and peer reviewed by TAPPI members with tissue expertise. The program is open to all full PaperCon registrants. An invitation to Present at the Tissue360 Forum has been issued. Industry professionals interested in presenting a paper, panel, roundtable, or poster on any of these topics should submit an abstract no later than November 20, 2012.
PaperCon brings together CEOs, mill managers, superintendents, scientists, process engineers, and suppliers for the largest pulp and paper technical program in the world. No other event provides such a comprehensive program, networking opportunities and trade fair among such a distinguished group of industry leaders.
Back To Top
|
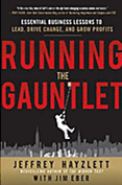
By: Jeffrey Hayzlett
Running The Gauntlet is a rough-and-tumble guide for running and driving change through the business gauntlet. The book divides into three parts that parallel the three parts of change that every business leader must face: Getting Ready, Getting Going, and Creating and Sustaining Momentum.
In each section, Hayzlett shows business leaders and owners how to develop the necessary mental, emotional, and (yes) physical toughness they must have for smart, strategic, and lasting change. Through this book, Hayzlett will force leaders to really get up in their own businesses – to take them over from the inside and drive change – gaining customers and profits in the process.
Readers will be able to efficiently assess what kind of change their business needs and then summon the vision, courage, and passion to enact it.
View the Table of Contents and Preview.
Hard cover. 256 pages.
Member Price: $26.00
Item #: 11RUNN
Back To Top
|
The 360° Leader by Dr. John C. Maxwell
People who desire to lead from the middle of organizations face unique challenges. They are often held back by myths that prevent them from developing their influence. Dr. Maxwell, one of the globe's most trusted leadership mentors, debunks the myths, shows you how to overcome the challenges, and teaches you the skills you need to become a "360° leader."
If you have found yourself trying to lead from the middle of the organization, as the vast majority of professionals do, then you need Maxwell's insights. You have a unique opportunity to exercise influence in all directions-up (to the boss), across (among your peers), and down (to those you lead).
The good news is that your influence is greater than you know. Practice the disciplines of 360° leadership and the opportunities will be endless... for your organization, for your career, and for your life.
View the Table of Contents and Preview.
Member Price: $25.00
Press Item #: 12LEAD
Back To Top
|
The International Mechanical Pulping Conference, sponsored by PI, TAPPI, PAPTAC, SPCI and PTF, will be held on June 3-5, 2014, in Helsinki, Finland. IMPC 2014 is a major part of PulPaper, one of the world's most premier pulp and paper exhibitions, coinciding with the 100th anniversary of PI, the Paper Engineers' Association.
The Conference Program Committee invites you to submit papers on the following topics:
- Energy saving in Mechanical Pulping process
- New applications and innovations
- Raw materials in Mechanical Pulping
- Advanced Mechanical Pulping technologies e.g.
- Process control and simulation
- Bleaching
- Water management and effluent treatment
5. Mill operations update e.g.
- Production cost saving technologies (energy and chemicals)
- Improving mechanical pulping business potential
6. Mechanical pulps in paper and board.
Authors interested in presenting a paper or a poster on these topics should submit an extended abstract (˜500 words) to impc2014@vtt.fi. Abstracts are due by February 28, 2013. Authors will be notified of acceptance by May 31, 2013 and final manuscripts are due March 31, 2014.
If you have any questions, please contact Sari Liukkonen, Chair of the Program Committee at +358 40 586 0384, or by e-mail at impc2014@vtt.fi.
Back To Top
|
|
|
TAPPI Over the Wire | 15 Technology Pkwy. S. | Norcross, GA 30092 USA | Voice: 770.446.1400 | Fax: 770.446.6947
|
 |