 |
|
Weekly Spotlight
However, the overall economy grew for the 37th consecutive month
Learn More...
|
Verso Paper Corp., Memphis, Tenn., USA, this week launched the Verso Forest Certification Grant Program, an initiative aimed at increasing certified fiber and certified acreage on lands near the company's four paper mills
Learn More...
|
Montréal, Qué., Canada-based Tembec Inc. and Resolute Forest Products this week reached agreement with environment groups, northern towns, and a first nations community on a plan to protect a critical caribou habitat in northeastern Ontario, Canada, in the first of what the industry pledges will be a series of such deals across the country
Learn More...
|
Georgia-Pacific, Atlanta, Ga., USA, recently stood up for 50 incoming college freshmen who were stand-outs among their high school peers
Learn More...
|
Market Roundup
North American NBSK (northern bleached softwood kraft) market pulp prices for June are flat from May at $900/metric ton (ranging between $600 and $1,100 per metric ton)
Learn More...
|
According to Wood Resources International (WRI), Seattle, Wash., USA, the global pulp market is currently mired in uncertainty
Learn More...
|
Pulp & Paper
Catalyst Paper Corp., Richmond, B.C., Canada, this past week received approval for its reorganization plan from the Supreme Court of British Columbia
Learn More...
|
Domtar Corp., Montréal, Qué., Canada, this week released its 2011 Sustainable Growth Report, unveiling 35 key performance indicators that will shape the company's sustainability efforts out to 2020
Learn More...
|
DeZurik Inc., Sartell, Minn., USA, has agreed to acquire Hilton Valve Inc. of Redmond, Wash., a producer of fabricated large diameter and custom knife gate valves, effective July 9
Learn More...
|
Fibria, Brazil, this week reported that it has closed on the sale of its forest and land assets in Bahia State, Brazil, for a total price of R$235 million
Learn More...
|
International Paper, Memphis, Tenn., USA, this week announced that it has finalized the sale of its Ontario and Oxnard, Calif., containerboard mills to New-Indy Containerboard LLC, along with its New Johnsonville, Tenn., containerboard mill to Hood Container Corp
Learn More...
|
RockTenn, Norcross, Ga., USA, this past week released its inaugural Corporate Sustainability Report, which affirms the company's long-standing commitment to sustainability and outlines its 2020 sustainability goals
Learn More...
|
The agreement is for an EPC contract consisting of both engineering and commissioning at site
Learn More...
|
UPM, Hllsinki, Finland, is buying back ("redeeming") the Myllykoski power plant from Vamy Oy in accordance with a previous commitment
Learn More...
|
Containerboard/Packaging
In 2015, the global containers and packaging market is forecast to have a value of $596.8 billion, an increase of 21.6% since 2010
Learn More...
|
Amcor, Australia, has purchased Wayne Richardson Sales, one of the largest independently owned packaging distributors in Australia with a network of eight distribution centers across the country
Learn More...
|
Chesapeake Corp., U.K., this past week announced plans to invest in some revolutionary new digital carton production equipment that will ensure it "continues to lead the field in fast-response packaging solutions."
Learn More...
|
SCA, Stockholm, Sweden, this week reported that the previously announced divestment of its packaging business, excluding the two kraftliner mills in Sweden, has now been completed
Learn More...
|
|
New Products
Appleton, Appleton, Wis., USA, producer of NCR Paper brand carbonless paper, this week introduced Appleton Digital Paper, a line of digital sheets that includes synthetic polyester, paper-film laminate, pressure sensitive, and Fluorescents
Learn More...
|
Energy
Karlstads Energi AB, Sweden, has ordered from Andritz, Graz, Austria, a new biomass-fueled boiler for its Combined Heat and Power (CHP) plant at Hedenverket in Sweden
Learn More...
|
People
BASF Group, Ludwigshafen, Germany, has named Dr. Bärbel Arnold-Mauer VP of Corporate Brand Management
Learn More...
|
PaperlinX Ltd., Australia, reports that Wayne Johnston, deputy CFO and executive GM of Corporate Services, has been appointed as an additional Company Secretary, effective July 1
Learn More...
|
Walki, Finland, has appointed Carlo van Houtum VP, Sales and Marketing for its Paper Packaging Business Area and Business Line Reel Wrap
Learn More...
|
Travels with Larry
Back in 1991, during my days with Republic Paperboard in Hutchinson, Kan., USA, a gentleman set up an appointment with me to discuss a "revolutionary idea for our mill to utilize a new feedstock that was abundant in the treeless state of Kansas."
Learn More...
|
TAPPI News
To provide more students access to its expert faculty and outstanding curriculum, the 2012 TAPPI Linerboard/Medium Manufacture Course is re-locating from the TAPPI Training Center to the Atlanta Hilton Northeast. Register by July 9 to take advantage of the best rates. Save even more when you register three or more.
Learn More...
|
Nowhere is the adage ‘Knowledge is Power' more true than the TAPPI Linerboard/Medium Manufacture Course, August 7-9 at the TAPPI Training Center in Norcorss, Ga., USA.
Learn More...
|
Sessions in Pulping, Engineering, Environmental, Recycling and Sustainability focus on building a sustainable future.
Learn More...
|
A first-time, unique program for the TAPPI PEERS Conference, this one-day seminar explores the latest reliability strategies today's mills are implementing to stay in-tune and competitive under progressively lean operating conditions. October 14,15,18, 2012.
Learn More...
|
This July 12th webinar explores adhesion through oxidation in the extrusion coating process and how Time in the Air Gap (TIAG) affects adhesion for extrusion coating primed and unprimed paper and film.
Learn More...
|
The TAPPI Introduction to Kraft Pulping and Bleaching Course is an excellent way to network and learn among peers. It's coming up soon, August 13-14, 2012 at TAPPI Headquarters in Norcross, Ga., USA.
Learn More...
|
TAPPI and PPSA have announced the Safety Management Leadership Course to be held at TAPPI headquarters in Norcross, Ga., August 15-16.
Learn More...
|
Build knowledge and confidence with this introductory course to be held August 15 - 16 at TAPPI headquarters in Norcross, Ga., USA.
Learn More...
|
Atlanta, GA, USA. This year's course, Aug. 21-23 at TAPPI Headquarters, will teach expanded energy reduction strategies.
Learn More...
|
IBBC to focus on advancements and commercialization of bio-conversion technologies that leverage forest products manufacturing infrastructure. October 17-19 in Savannah, Georgia, USA.
Learn More...
|
October event includes tour to Herty Advanced Material Development Center.
Learn More...
|
This new text, available from TAPPI Press, is written to assist production engineers, supervisors, and industry scientists find quick solutions to today's immediate challenges. Discount available for TAPPI members.
Learn More...
|
Finding ways to measure, eliminate, or control growth associated with microbiology problems has been the cornerstone of TAPPI member Linda Robertson's fascinating career.
Learn More...
|
Have a chance to fund local TAPPI and PIMA industry scholarships at this August 14 recreational and social event. An afternoon shotgun scramble of golf is planned with dinner to follow.
Learn More...
|
Join us on Tuesday, August 28, at the Grand View Lodge, Preserve Course, in Pequot Lakes, Minn., USA.
Learn More...
|
The Nonwovens Engineers and Technologists Division (NET) of TAPPI will co-locate its annual Innovative Nonwovens Conference (NETInc) next year with PaperCon 2013, April 28 - May 1 in Atlanta, Ga., USA.
Learn More...
|
This manual provides a basis for common knowledge of terms, definitions, and methods of correction of corrugated operational defects. The manual illustrates and provides causes and remedies for hundreds of defects affecting corrugated boxes. Special discount for TAPPI members.
Learn More...
|
Awards that may be presented next year are the Gunnar Nicholson Gold Medal Award, the Herman L. Joachim Distinguished Service Award, the Paul W. Magnabosco Outstanding Local Section Member Award, and the TAPPI Fellow Award.
Learn More...
|
Know someone excelling in your industry R&D field? Nominate them for the William H. Aiken Prize for R&D. Nominations are due by August 1.
Learn More...
|
Fully searchable CD-ROM contains more than 125 presentations and papers presented at the world's largest pulp and paper technical program in New Orleans, La., USA, this past April 22 - 25.
Learn More...
|
TAPPI members save $10 on this new reader-friendly text offering a comprehensive look at risk analysis and it's implementation in the Nanotechnology industry.
Learn More...
|
A comprehensive account of how nanomaterials are synthesized and processed, this book (now available through TAPPI Press) presents the theory and technology of introducing nano-based materials as value-added elements into product manufacturing.
Learn More...
|
Wet End Chemistry is the eleventh of 15 CD-ROMs in the Making Pulp and Paper CD-ROM Series. Through this highly interactive, self-paced CD-ROM, participants learn wet end chemistry terms, concepts, and processes.
Learn More...
|
|
Find us on Facebook
Network with us on LinkedIn
Follow us on Twitter
|
Weekly Spotlight
Economic activity in the U.S. manufacturing sector contracted in June for the first time since July 2009. However, the overall economy grew for the 37th consecutive month, according to the nation's supply executives in the latest Manufacturing ISM Report On Business. The report was issued this week by Bradley J. Holcomb, chair of the Institute for Supply Management Manufacturing Business Survey Committee, Tempe, Ariz., USA.
"The PMI registered 49.7%, a decrease of 3.8 percentage points from May's reading of 53.5%, indicating contraction in the manufacturing sector for the first time since July 2009, when the PMI registered 49.2%. The New Orders Index dropped 12.3 percentage points in June, registering 47.8% and indicating contraction in new orders for the first time since April 2009, when the New Orders Index registered 46.8%.
The Production Index registered 51%, and the Employment Index registered 56.6%. The Prices Index for raw materials decreased significantly for the second consecutive month, registering 37%, which is 10.5 percentage points lower than the 47.5% reported in May. Comments from the panel range from continued optimism to concern that demand may be softening due to uncertainties in the economies in Europe and China."
Of the 18 manufacturing industries, seven are reporting growth in June, in the following order: Furniture and Related Products; Printing and Related Support Activities; Fabricated Metal Products; Miscellaneous Manufacturing; Electrical Equipment, Appliances and Components; Machinery; and Primary Metals. The nine industries reporting contraction in June (in order) are: Nonmetallic Mineral Products; Apparel, Leather and Allied Products; Paper Products; Plastics and Rubber Products; Chemical Products; Computer and Electronic Products; Petroleum and Coal Products; Food, Beverage, and Tobacco Products; and Transportation Equipment.
The seven industries reporting growth in new orders in June (in order) are: Printing and Related Support Activities; Furniture and Related Products; Miscellaneous Manufacturing; Fabricated Metal Products; Primary Metals; Electrical Equipment, Appliances and Components; and Paper Products. The 10 industries reporting a decrease in new orders during June (in order) are: Nonmetallic Mineral Products; Wood Products; Plastics and Rubber Products; Petroleum and Coal Products; Chemical Products; Food, Beverage, and Tobacco Products; Transportation Equipment; Computer and Electronic Products; Machinery; and Apparel, Leather, and Allied Products.
The eight industries reporting growth in production during the month of June (in order) are: Fabricated Metal Products; Furniture and Related Products; Miscellaneous Manufacturing; Machinery; Printing and Related Support Activities; Electrical Equipment, Appliances and Components; Transportation Equipment; and Computer and Electronic Products. The four industries reporting a decrease in production in June are: Paper Products; Chemical Products; Food, Beverage, and Tobacco Products; and Apparel, Leather, and Allied Products. Six industries reported no change in production in June compared with May.
Of the 18 manufacturing industries,11 reported growth in employment in June in the following order: Fabricated Metal Products; Furniture and Related Products; Machinery; Miscellaneous Manufacturing; Electrical Equipment, Appliances and Components; Printing and Related Support Activities; Petroleum and Coal Products; Primary Metals; Chemical Products; Food, Beverage, and Tobacco Products; and Transportation Equipment. The four industries reporting a decrease in employment in June are: Nonmetallic Mineral Products; Apparel, Leather and Allied Products; Paper Products; and Computer and Electronic Products.
The Inventories Index registered 44% in June, which is 2 percentage points lower than the 46% reported in May. This month's reading indicates that respondents are reporting that inventories are contracting, which has been the case in eight of the last nine months. An Inventories Index greater than 42.8%, over time, is generally consistent with expansion in the Bureau of Economic Analysis' (BEA) figures on overall manufacturing inventories (in chained 2000 dollars).
The five industries reporting higher inventories in June are: Wood Products; Furniture and Related Products; Electrical Equipment, Appliances and Components; Machinery; and Food, Beverage, and Tobacco Products. The 10 industries reporting decreases in inventories in June (in order) are: Primary Metals; Nonmetallic Mineral Products; Petroleum and Coal Products; Chemical Products; Apparel, Leather and Allied Products; Paper Products; Miscellaneous Manufacturing; Computer and Electronic Products; Transportation Equipment; and Fabricated Metal Products.
More information is available online.
Back To Top
|
Verso Paper Corp., Memphis, Tenn., USA, this week launched the Verso Forest Certification Grant Program, an initiative aimed at increasing certified fiber and certified acreage on lands near the company's four paper mills. The program will provide startup funding to encourage and assist landowners, consulting foresters, and other stakeholders in developing innovative new projects that will help expand and maintain certification in Verso's wood procurement zones.
"Verso's Forest Certification Grant Program helps us meet two important sustainability commitments," says Verso SVP for Manufacturing and Energy Lyle Fellows. "By encouraging expanded forest certification, we're advancing responsible management practices that keep U.S. forests vibrant and healthy. We're also helping to increase the available supply of certified fiber which, in turn, allows us to keep our pledge to provide paper products that help our customers meet their own sustainability objectives," he says.
Verso SVP for Sales, Marketing, and Product Development Mike Weinhold explains that "Verso already uses a high percentage of fiber that's certified to credible forest management certification standards—about 70%—but the availability of certified fiber in the U.S. remains limited with only about 28% of privately owned U.S. land certified. With customer demand for certified paper products increasing significantly, it's vital that we do all we can to make sure the supply of certified fiber keeps pace."
The Forest Certification Grant Program builds on Verso's track record of successful forest certification expansion initiatives. In 2011, the company completed a two-year group certification project in partnership with several of its customers and other stakeholders that resulted in an additional 1.4 million certified acres in Maine. In 2009 and 2010, a Verso grant to the Trust to Conserve Northeast Forestlands resulted in 160,000 additional certified acres across six Northeast states. Verso regularly encourages certification through collaboration with state forestry associations and certification organizations, and through its relationships with private landowners.
Anyone interested in learning more about the Verso Forest Certification Grant Program or in obtaining a grant application may contact Greg Barrows.
Back To Top
|
Montréal, Qué., Canada-based Tembec Inc. and Resolute Forest Products this week reached agreement with environment groups, northern towns, and a first nations community on a plan to protect a critical caribou habitat in northeastern Ontario, Canada, in the first of what the industry pledges will be a series of such deals across the country, according to a report by the Canada-based Globe and Mail news service.
Executives from both paper companies were among the partners who unveiled the agreement covering some 3 million hectares at a news conference at the provincial legislature last Thursday. The province must approve the plan, and Natural Resources Minister Michael Gravelle--who praised the effort--pledged speedy review, the newspaper reported.
According to the Globe and Mail, under the deal, some 835,000 hectares in the Abitibi River forest—an area roughly the size of Yellowstone Park in the U.S.—will be excluded from timber harvesting to protect the threatened woodland caribou, considered a bellwether species whose fate reflects the health of the ecosystem.
Tembec president Jim Lopez said the deal not only represents good environmental policy, but will ensure the company's sawmills have access to wood supply that will sustain operations for the foreseeable future. "The best plan for the environment is the best economic plan as well," he said, noting that Tembec will now work at implementing similar deals across its operations in Ontario, Quebec, and British Columbia under a two-year-old Boreal Forest Agreement that includes 19 companies and nine environmental groups.
Back To Top
|
Georgia-Pacific, Atlanta, Ga., USA, recently stood up for 50 incoming college freshmen who were stand-outs among their high school peers. These graduates are getting help with their educational expenses through the Georgia-Pacific Foundation Employees' Children Scholarship program.
One of 2012's recipients, Matthew O'Shaughnessy, a graduate of Milton (Ga.) High School, and an incoming freshman at the Georgia Institute of Technology, said that "the Georgia-Pacific Scholarship is really an amazing opportunity for me to be able to attend the college of my dreams and major in what I've always wanted to do (electrical and computer engineering)."
GP annually awards 50 four-year scholarships to qualifying children of its employees across the U.S. so that approximately 200 students are receiving support in any given year. Since the program's start in 1988, GP has awarded more than 1,250 scholarships, totaling approximately $10 million. This year, students from 17 states received scholarship awards.
"By helping these employees' children cover their ever-increasing education costs, we are rewarding their hard work and academic success, and helping prepare tomorrow's community leaders," said Curly M. Dossman Jr., president of the GP Foundation.
The GP scholarship program is administered by the National Merit Scholarship Corp. and is open to children of all active, full-time employees of GP in the U.S. The award is $2,000 per year for up to four years of full-time college undergraduate study, for a total maximum award of $8,000.
Back To Top
|
Market Roundup
North American NBSK (northern bleached softwood kraft) market pulp prices for June are flat from May at $900/metric ton (ranging between $600 and $1,100 per metric ton), according to Mark Wilde, senior analyst with Deutsche Bank. Wilde reports that most printing and writing paper and packaging grades are also flat from May, including newsprint, LWC papers, coated and uncoated free sheet, linerboard, and solid bleached sulfate (SBS) grades.
Newsprint prices, according to Wilde, are at $640 per metric ton this month (ranging between $415 and $800 per metric ton). LWC (lightweight coated) papers (No. 5 – 40 lb.) are at $880 per ton, ranging from $680 to $1,240 per ton. Coated free sheet papers (No. 3 Rolls- 60 lb.) are at $975 per ton, ranging from $720 to $1,100 per ton. Uncoated free sheet (20 lb. – Repro Bond) is at $1,060 per ton, ranging between $650 and $1,200 per ton.
Linerboard is at $640 per ton in June, ranging from $310 to $700 per ton. SBS grades are at $1,135 per ton, ranging between $570 and $1,200 per ton.
Back To Top
|
According to Wood Resources International (WRI), Seattle, Wash., USA, the global pulp market is currently mired in uncertainty. The market is uncertain, for example, when China will move into the buying mode, where the European economy is heading, and whether low spot prices for softwood market pulp will push pulp mills in Europe and North America to take market-related downtime.
In this environment, WRI says, pulp mills are trying to squeeze their costs to remain competitive and to be able to run at full capacity. Because, according to Fisher International, wood fiber costs currently account for 52% - 71% of total production costs, depending on region of the world, the primary focus in cost-cutting has been on reducing the price mills pay for wood chips and pulpwood over the past six months.
This has created the situation in which many fiber suppliers have been forced to accept lower prices for their fiber. As a consequence, wood fiber prices fell throughout the world in the 1Q/12, which caused the two global wood fiber price indices to decline to their lowest levels in more than a year.
WRI's Wood Resource Quarterly report shows the Hardwood Wood Fiber Price Index (HFPI) experienced the biggest decline, falling by 3.5% from the 4Q/11 to $109.67/odmt. Since its all-time high last fall, the HFPI has come down 7% in just two quarters. Wood costs were down the most in Europe and Japan. The price premium for hardwood fiber over softwood fiber is currently the lowest since 1Q/11.
In addition, the Softwood Wood Fiber Price Index (SFPI) fell a more modest 0.4% from the previous quarter, which was 4% lower than in the spring of 2011. Softwood fiber price trends were mixed, with increases in Oceania, Chile, and the U.S. South and falling prices in Europe, Western Canada, and Japan.
Softwood chip prices in British Columbia fell 25% from the previous quarter, according to WRI's North American Wood Fiber Review, and are currently 18% lower than last fall when prices were at a 16-year high.
In Europe, softwood pulp log prices fell 1% - 6% in local currencies in the 1Q/12 compared with the previous quarter, and are now back down to price levels last seen in 2010.
With continued soft pulp and paper markets during the second quarter, wood fiber costs are likely to continue to weaken in many key markets around the world in the coming months, WRI concludes.
More information is available online.
Back To Top
|
Pulp & Paper
Catalyst Paper Corp., Richmond, B.C., Canada, this past week received approval for its reorganization plan from the Supreme Court of British Columbia. The company's second amended plan under the Companies' Creditors Arrangement Act (the Amended Plan) received 99% support from creditors.
Court approval of the reorganization plan comes only five months following Catalyst Paper's entry into creditor protection on January 31. A confirmation hearing under the Chapter 15 process of the U.S. Bankruptcy Court for the District of Delaware (the U.S. Court) is expected to occur the middle of this month. Approval from both courts is required before the company can complete its reorganization.
"Today's court order is a major milestone in our drive to emerge from creditor protection efficiently and quickly," said President and CEO Kevin J. Clarke. "We said from the outset that our objective was to put our company on stronger financial footing for the future and we are proceeding at a rapid pace to do just that. We're in discussion now with lenders to secure the necessary exit financing and expect to complete the reorganization process in the near term."
The Court also authorized and directed Catalyst to take all actions necessary to implement the Amended Plan and Catalyst is working towards implementation, which is subject to a number of conditions, including the company obtaining an order of the U.S. Court recognizing that the Sanction Order is in full force and effect in the U.S. and that Catalyst Paper shall have entered into agreements with respect to a new ABL Facility and, if necessary, Exit Facility, satisfactory to the Majority Initial Supporting Noteholders, in consultation with the Initial Supporting Unsecured Noteholders.
Back To Top
|
Domtar Corp., Montréal, Qué., Canada, this week released its 2011 Sustainable Growth Report, unveiling 35 key performance indicators that will shape the company's sustainability efforts out to 2020. This sustainability framework builds on years of industry leadership in forestry certification, mill-level environmental performance, and longstanding ENGO collaborations.
This year also marks the first time Domtar is issuing a level-checked "B" Global Reporting Initiative (GRI) report, as well as the first time that outside perspective from sustainability experts in the private sector and civil society is being featured.
"The release of a key performance indicator framework is an important milestone in our long-term sustainability strategy," noted John D. Williams, Domtar president and CEOr. "By addressing sustainability in a systematic way we are making this company more resilient, better able to seize opportunities for innovation and growth, as well as more open to constructive input from our shareholders, customers, suppliers, and environmental partners. All of this supports our evolution from papermaker to fiber innovator that positions us for success over the long term."
More information is available online (in the Sustainability Section).
Back To Top
|
DeZurik Inc., Sartell, Minn., USA, has agreed to acquire Hilton Valve Inc. of Redmond, Wash., a producer of fabricated large diameter and custom knife gate valves, effective July 9. The combining of Hilton products and operations with those of DeZurik creates one of the broadest knife gate and engineered valve companies in the industry.
DeZurik will acquire all Hilton products and production capability. Hilton operations will continue as a stand-alone business in its Redmond facility that includes engineering and manufacturing to produce valves up to 144 in. in dia. The Hilton name will be retained as a brand of DeZurik.
Consolidated sales activity will be coordinated between DeZurik and Hilton through a worldwide sales and service organization and with continuing product technical and project engineering support provided by Hilton.
Hilton valve lines are used on water, wastewater, energy, process, and hydro applications with emphasis on problem solving and unique designs built to any U.S. and international standard. Founded in 1952, the company was one of the first knife gate valve producers. In 1983, its operations were redirected to focus exclusively on the design and manufacture of fabricated knife gate and other specialty valves.
Back To Top
|
Fibria, Brazil, this week reported that it has closed on the sale of its forest and land assets in Bahia State, Brazil, for a total price of R$235 million. The assets include some 16,100 hectares of eucalyptus plantations.
Caravelas Florestal S.A., controlled by Fundo Florestas do Brasil FIP, made a closure payment of R$200 million to Fibria, and will pay the remaining R$35 million this November 14, after completing due diligence.
Back To Top
|
International Paper, Memphis, Tenn., USA, this week announced that it has finalized the sale of its Ontario and Oxnard, Calif., containerboard mills to New-Indy Containerboard LLC, along with its New Johnsonville, Tenn., containerboard mill to Hood Container Corp. By completing these transactions, the company satisfies its divestiture obligations under its February 2012 settlement agreement with the U.S. Department of Justice.
The settlement agreement, in which the company agreed to divest the three mills, was entered into in connection with the company's acquisition of Temple-Inland.
Back To Top
|
RockTenn, Norcross, Ga., USA, this past week released its inaugural Corporate Sustainability Report, which affirms the company's long-standing commitment to sustainability and outlines its 2020 sustainability goals. The company's 2020 goals are to:
- Reduce energy use by 10%
- Reduce greenhouse gas emissions by 10%
- Reduce water use by 12%
- Reduce solid waste by 15%
- Achieve chain-of-custody certifications for 100% of facilities
- Improve employee safety by 30%.
"RockTenn has been producing paper-based packaging from recycled materials since our founding in 1936," said Jim Rubright, chairman and CEO of RockTenn. "Our core business activities were founded on recycling products that create economic value by reusing materials otherwise bound for waste streams.
"Our belief is that our operations can be more than consistent with an environmentally sustainable planet. We can be part of the solution and have a net positive impact on the environment," Rubright continued. "These formal sustainability goals are further evidence of our ongoing commitment to our environment, our people, and our performance."
Jessica Kimbrough, chair of RockTenn's Sustainability Council and VP, marketing, Consumer Packaging, noted that "this report provides a summary of our approach to sustainability, progress toward our goals, and examples of excellence and sustainability in action throughout our company. While we have made significant progress, we know there is opportunity to improve and we will constantly aspire to do so."
RockTenn's full Sustainability Report is available online.
Back To Top
|
Södra Cell, Växjö, Sweden, has contracted Citec Oy Ab, Vaasa, Finland, to deliver a new tall oil plant to its mill in Tofte, Norway. The agreement is for an EPC contract consisting of both engineering and commissioning at site.
Södra Cell's new plant at Tofte will have the capacity to produce 25,000 metric tpy of tall oil. Crude tall oil is a spin-off from the production of pulp. It is biologically degradable and consists of fatty acid (30%-35%), resin (20%-25%), and pitch (35%). Refined tall oil is used, for example, as fuel, in paint and as a raw material in flavoring and cosmetics.
"This is a breakthrough for our tall oil solution. Citec is offering a unique tall oil solution unmatched by competitors on the market," said Hans Paulsson, industry area director, Process and Manufacturing at Citec.
Södra Cell is organized into four business areas: Södra Skog – timber raw products, forestry services; Södra Timber – wood products; Södra Cell – paper pulp; and Södra Interiör – interior wood products.
Back To Top
|
UPM, Hllsinki, Finland, is buying back ("redeeming") the Myllykoski power plant from Vamy Oy in accordance with a previous commitment. The redemption is included in the reserves made in connection with the Myllykoski paper mill restructuring plans, the company notes.
Vamy Oy's power plant, located in Myllykoski, Finland, is a combined heat and power plant that has been producing energy mainly to the UPM Myllykoski mill. The power plant has used mainly biofuels and also peat and natural gas as raw materials. The power of the main boiler of the power plant is 88 MW.
Vamy Oy, an affiliated company of Vattenfall AB (100% owned by the Swedish state), is one of Europe's largest generators of electricity and largest producer of heat. UPM consists of three business groups: Energy and pulp, Paper, and Engineered materials. The group employs around 24,000 people and has production plants in 16 countries.
Back To Top
|
Containerboard/Packaging
In 2015, the global containers and packaging market is forecast to have a value of $596.8 billion, an increase of 21.6% since 2010, according to a new report titled Containers & Packaging: Global Industry Guide published by Research and Markets, Dublin, Ireland. In 2015, the global containers and packaging market is forecast to have a volume of 300.6 million metric tons, an increase of 13.2% since 2010.
The new report covers the Global, European, and Asia-Pacific markets and has individual chapters on five major markets (France, Germany, Japan, the U.K., and the U.S.). It also includes a five-year forecast of the industry.
Paper is the largest segment of the global containers and packaging market, accounting for 40.1% of the market's total value, the report notes. The Americas accounts for 36.8% of the global containers and packaging market value.
More information is available online.
Back To Top
|
Amcor, Australia, has purchased Wayne Richardson Sales, one of the largest independently owned packaging distributors in Australia with a network of eight distribution centers across the country. Wayne Richardson, a distributor of a broad range of industrial packaging and packaging consumables to small and medium size customers, has sales of approximately $50 million and more than 2,700 customers.
The purchase multiple was approximately 6.5 times fiscal year 2012 EBITDA and the acquisition is expected to deliver returns in excess of 20% by year three.
Amcor Managing Director and CEO Ken MacKenzie said that "the purchase of Wayne Richardson Sales improves the value proposition of Amcor's existing packaging business and strengthens our market position. It brings to Amcor a new and more effective channel to small and medium sized packaging customers. The combined business will provide new products as well as additional services and enhanced technical support for customers."
Back To Top
|
Chesapeake Corp., U.K., this past week announced plans to invest in some revolutionary new digital carton production equipment that will ensure it "continues to lead the field in fast-response packaging solutions." Chesapeake noted that the equipment will further extend its digital capability, already well established for label production, "helping to drive even greater reductions in lead times and delivering tangible benefits to customers."
In addition to new digital printing presses from HP Indigo and Landa, Chesapeake is also planning to install a digital finishing capability, enabling the company to become the first packaging manufacturer to offer a fully integrated digital solution for the production of folding cartons.
Dougie Potter, Chesapeake's technical services director, said that "over the next 12 months, the installation of this new state-of-the-art equipment, linked to innovative front-end order handling, will provide a fantastically effective solution for quick-response, small-order quantities. It will also help to reduce product inventory and obsolescence."
Chesapeake also has signed an agreement to invest in the latest digital carton cut-and-crease technology from Highcon, including the Euclid digital press unveiled at the recent Drupa exhibition, which, the company notes, is the world's first completely digital production cutting and creasing machine. The system removes the need to use a die for production by implementing new polymer and laser technologies instead, reducing machine setup time to minutes.
"We have been following the progress of the Highcon technology for some time," said Dougie Potter, "and were impressed by the machine's performance, live at Drupa. We believe the addition of this unique digital solution will not only complement our existing equipment, but will—crucially—offer hugely enhanced flexibility to better serve the current and future needs of our customers."
Back To Top
|
SCA, Stockholm, Sweden, this week reported that the previously announced divestment of its packaging business, excluding the two kraftliner mills in Sweden, has now been completed. The buyer is U.K.-based DS Smith and the purchase price amounts to EUR 1.7 billion on a debt-free basis. SCA's two kraftliner mills in Sweden are not included in the transaction as they are well integrated with SCA's forest products operations.
The divested operations have approximately 12,000 employees.
Back To Top
|
New Products
Appleton, Appleton, Wis., USA, producer of NCR Paper brand carbonless paper, this week introduced Appleton Digital Paper, a line of digital sheets that includes synthetic polyester, paper-film laminate, pressure sensitive, and Fluorescents. Engineered for both dry and liquid toner printing platforms, the new digital products are suitable for applications such as menus, ID cards, maps, labels, horticulture tags, manuals, lumber tags, point-of-purchase signage, bumper stickers, and shelf talkers, among others.
Appleton Digital Polyester is water-, tear- and weather-resistant, has a durable print surface that does not need to be over-laminated and can withstand high-heat printing up to 400° F. The stock is white, C2S, and can be printed on high-heat dry toner and offset equipment. It is available in 5, 6, 8, 11, and 14 mil calipers. Applications include ID cards, menus, luggage tags, outdoor signage, manuals, children's books, point-of-sale signs, etc. The 11-mil stock is KODAK NEXPRESS qualified.
Appleton Digital Paper-Film Laminate features a paper-film-paper construction that is water- and tear-resistant that converts like paper and prints without special inks or set ups. These products are manufactured using a solvent-free lamination process that results in stability and flatness for consistent runnability. The uncoated products are appropriate for high-heat dry toner and offset printing, and come in four calipers—3.5, 4.5, 7.0, and 9.5 PT. The white, C2S product is suitable for high-heat dry toner, HP Indigo, and offset applications, and is available in 10.5 PT. Applications include perforated ID cards, menus, tags, wristbands, shelf talkers, index cards, sporting licenses, maps, etc.
Appleton Digital Pressure Sensitive is available in white and clear flexible vinyl, and clear polyester. All products feature high durability for indoor and outdoor applications that require moisture, heat, and chemical resistance. Two adhesive options include permanent and ultra-removable. The clear polyester is 2.0 mil, and the vinyl products are 3.4 mil. The pressure sensitive products can be printed on high-heat dry toner, HP Indigo, and offset equipment. In addition, all of the pressure sensitive products are HP Indigo certified, and the white flexible vinyl product is KODAK NEXPRESS qualified. Applications include window decals, bumper stickers, display case signage, appliance labels, CD labels, horticulture labels, deli signs, etc.
Appleton Digital Fluorescents are available in six colors (lime, lemon, raspberry, strawberry, orange, and peach), each 8.0 PT. The fade-resistant surface delivers long life, and accepts markers without smudging. Appleton Fluorescents are coated, rather than dyed, which makes them more durable at withstanding drips and bleeding from incidental water exposure. The paper can be imaged with high-heat dry toner and offset equipment. Possible applications include store signage, price tags, banners, packaging, labels, posters, direct mail, etc.
More information about the Appleton Digital Paper line is available online.
Back To Top
|
Energy
Karlstads Energi AB, Sweden, has ordered from Andritz, Graz, Austria, a new biomass-fueled boiler for its Combined Heat and Power (CHP) plant at Hedenverket in Sweden. Startup is scheduled for the end of 2014. The scope of delivery includes the complete boiler island (fuel bin to flue gas fan outlet), based on Andritz's Bubbling Fluidized Bed (BFB) design that combines high efficiency with excellent environmental performance.
The boiler will burn wood-based fuels (logging waste, sawmill chips, and bark) that are widely available in the region to generate steam at the rate of 127 t/hr, equal to 88 MW of thermal power.
According to Karlstads Energi, construction of the new CHP facility will allow the municipality to phase out all energy production using fossil fuels and increase production of electricity from renewable resources. "The completion of this plant will enable us to secure a long-term electricity and district heating supply with sustainable and renewable fuels, using highly efficient and environmentally friendly technology," said Mats Preger, CEO of Karlstads Energi.
Back To Top
|
People
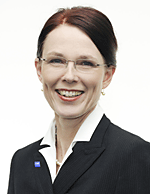 BASF Group, Ludwigshafen, Germany, has named Dr. Bärbel Arnold-Mauer VP of Corporate Brand Management. She succeeds Susanne Marell, who will assume a new position outside of BASF. Arnold-Mauer is responsible for branding, industry group communications, plastics and industry affairs, and sustainability relations, reporting to Elisabeth Schick, SVP communications and government relations.
BASF is a global chemical company with sales of some EUR 73.5 billion in 2011 and more than 111,000 employees as of the end of the year.
Back To Top
|
PaperlinX Ltd., Australia, reports that Wayne Johnston, deputy CFO and executive GM of Corporate Services, has been appointed as an additional Company Secretary, effective July 1. James Orr will cease to be a Company Secretary of PaperlinX, effective June 30, the company notes.
Back To Top
|
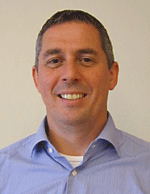 Walki, Finland, has appointed Carlo van Houtum VP, Sales and Marketing for its Paper Packaging Business Area and Business Line Reel Wrap. Van Houtum has worked for several years in sales and marketing management positions at Myllykoski Group, Sappi Group, and most recently the delfortgroup in Tervakoski, Finland.
Back To Top
|
Travels with Larry
Back in 1991, during my days with Republic Paperboard in Hutchinson, Kan., USA, a gentleman set up an appointment with me to discuss a "revolutionary idea for our mill to utilize a new feedstock that was abundant in the treeless state of Kansas." I informed him that we were a recycled mill and did not use trees as a feedstock, but to come over to my office anyway to talk.
During our meeting, he showed me his idea of using wheat straw as the base feedstock to make recycled paperboard. I thought it was a novel idea and I would discuss this concept with our mill team. As most folks in our industry at that time, our team said are you nuts? This will never work. What was the guy smoking? I then bowed my head and went back to the safe confines at my corporate office.
Now fast forward some 21 years later. Let me set the stage.
A mill is using wheat straw that used to be burned in the fields (creating pollution in the air). The straw is being used almost exclusively in the mill's tissue and printing paper machines at SHANDONG TRALIN PAPER CO., LTD. located in Shandong, China.
TAPPI Fellow Michael Sun organized my trip to China. He especially wanted me to see the process and the effluent water that comes out of this mill. The COD discharge is less than 30 milligrams per liter, which beats the national China standard of 100 milligrams per liter.
Our gracious hosts, for this mill visit, were Chen Songtao, chief senior engineer, and Yang Ji Hui, vice general manager of production.
History. The mill is located on 2,000 acres and employs approximately 6,000 workers. It started up in 1975 and was nearly closed down in 2000 due to environmental issues. Mill management had a choice to make—either go green or shut down. And as they say..."the rest is history." They reasoned that "developed countries use wood to make paper. We don't have much wood so we have to use something else. In this case, we chose wheat straw." This solved many issues that had historically been associated with leaving wheat straw in the fields after harvest, such as insect issues, pollution from burning the fields, and 800 million tons per year of agricultural waste.
Raw Materials. Annually, the mill collects 1.5 million tons of wheat straw that contains approximately 1.2 million tons of usable material, which then yields 600,000 tons of paper. In addition, they also purchase between 100,000 and 150,000 tons of softwood market pulp.
Turn Around. The mill has done such a good job with this process that the Chinese government has taken notice to the tune of approving its printing and writing paper (made on the P&W paper machine) for school text books. Their paper products were also selected to be used at the 2011 Shanghai World Expo.
Our group pictured in front of a display of some of the products and awards that they have received.
The Future. By 2015 the government wants the mill to expand wheat straw usage to 2 - 2.5 million tons per year. This should become a reality after Shandong Tralin Paper's million dollar expansion project is completed. The China Agriculture Department's National Reform & Development Committee is encouraging the mill to help ease pollution from the wheat straw still being burned, and to create more jobs.
Sustainability. Within a 500 kilometer area around the mill, there is an estimated 23.8 million tons of wheat straw available for collection. Currently, less than 20% is being collected for all uses. Shandong Tralin Paper reports that 1 acre of planted wheat yields 1.2 tons of wheat straw.
Digesters. Rather than working with continuous digesters, the mill chose to go with a system of 64 batch digesters and control system. The benefits of this system include a reduced environmental footprint and improved access to raw materials. These non-wood based products can compete with high end tissue.
Product Lines. In addition to tissue and towel grades, the mill also manufactures printing and writing grades as well as molded pulp.
Full Circle. Production of all products from this mill totals 700,000 metric tons per year. Any black liquor generated is dried and granulized and sold as fertilizer for plants and crops.
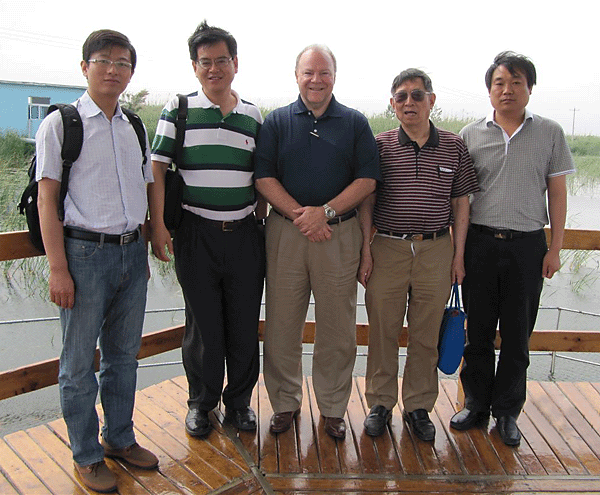
Left to right: Tian Chao, Michael Sun, Larry Montague, Chen Songtao, Yang Ji Hui.
More information about this company that is doing something that others have stated could not be done is available online.
More information about TAPPI is also available online.
There are two types of people in our industry: TAPPI members and those who should be.
Until next time....
Back To Top
|
TAPPI News
To provide more students access to its expert faculty and outstanding curriculum, the 2012 TAPPI Linerboard/Medium Manufacture Course is re-locating from the TAPPI Training Center to the Atlanta Hilton Northeast.
Register by July 9 to take advantage of the best rates. Save even more when you register three or more.
This intermediate level course, August 7-9, is designed to:
- Increase participants' understanding of linerboard and medium performance properties and how they are achieved
- Build confidence in interacting more knowledgeably within the mill, with suppliers, and with currugators.
- Improve manufacturing operations, to help produce a more competitive product.
View the full course schedule.
For those who require an overview background on pulp & papermaking technology, there will be an optional one-day introduction to P&P on Monday, August 6, prior to the beginning of the main course on Tuesday. This supplemental session is intended for corrugators, new P&P mill and supplier personnel, and those without exposure to pulp and paper operations. A separate registration is required for this seminar.
Back To Top
|
Faculty at the TAPPI Linerboard/Medium Manufacture Course will offer more than 250 years of collective experience.
Nowhere is the adage ‘Knowledge is Power' more true than the TAPPI Linerboard/Medium Manufacture Course, August 7-9 at the TAPPI Training Center in Norcorss, Ga., USA. With its expert faculty and countless opportunities to interact one-on-one with each one, this course is like having a group of consultants at your fingertips ready to help you solve the problems you encounter at your facility.
You will learn from the best, including:
- Andy Kahra, Lorentzen & Wettre USA - More than 40 years papermaking experience
- Mike Kocurek, NC State - More than 40 years teaching Paper Technology and Properties to students and mill personnel
- Chuck Class, Klass Associates - More than 45 years papermaking and paper machine experience
- Rick Phillips, Asten-Johnson - More than 28 years press fabrics experience
- Jon Porter, Fosber America - More than 30 years teaching experience, 10 in corrugating
- Darren Swales, Kemira - More than 20 years experience in Wet End Chemistry
- Daryl Wells, Asten-Johnson - More than 27 years experience in papermaking
- Per-Olof Warendh, Lorentzen & Wettre USA - Moire than 35 years papermaking experience.
So that's a total of 250 years of combined experience and knowledge for attendees to draw upon, to learn from, and get answers to your problems.
Click here to view the bios of this expert faculty.
Only 25 individuals will be able to take advantage of this knowledge-packed team.
Register by July 9 to take advantage of the best rates. Remember, space is limited! Save even more when you register three or more.
Back To Top
|
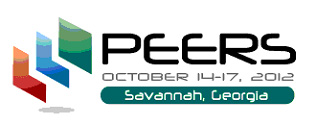
The 2012 TAPPI PEERS Conference, October 14-17 in Savannah, Ga., USA, has announced a detailed technical program. Five programming tracks of peer-reviewed sessions, Pulping, Engineering, Environmental, Recycling, and Sustainability, will answer the most pressing business and technical questions faced by pulp and paper companies as they manage raw materials, assets, regulatory requirements, and production assets.
Register now and save.
In addition to the in-depth, peer-reviewed technical program, Keynote Speaker Don Roberts, vice chairman of CIBC World Markets, will present " A Whirlwind Tour of Investment Trends and Issues in the Global Bio-Energy Space." PEERS will also offer exclusive networking opportunities and insight into new technologies that can help you optimize your mill operations.
The TAPPI PEERS Conference will be co-located with the International Bioenergy and Bioproducts Conference, creating a value-added opportunity for you to expand your learning, networking, and resources by attending both events. See you in Savannah!
Back To Top
|
Operating Excellence (OpEx) Maintenance and Reliability Seminar at PEERS
This is a first-time program for the 2012 TAPPI PEERS Conference.
Maintenance and reliability continue to be critical to the efficient operation of pulp and paper mills worldwide, just behind fiber and labor as top production cost factors.
This one-day seminar explores the latest reliability strategies today's mills are implementing to stay in-tune and competitive under progressively lean operating conditions.
The OpEx Maintenance and Reliability Track, included in your PEERS registration at no extra cost, is part of the Engineering Program.
If you are only interested in attending the OpEx Track, select the Single Day PEERS Registration for Thursday, October 18. This year's PEERS Conference includes a full program of educational opportunities for maintenance and reliability personnel, including:
- Sunday, Oct. 14: Fixed Equipment Maintenance Optimization System Course (Additional Fee)
- Monday, Oct. 15 - Wednesday, Oct. 17: Corrosion & Materials Engineering Track
- Thursday, Oct. 18: OpEx Maintenance and Reliability Track.
In addition, 2012 TAPPI PEERS Conference, October 14-17 in Savannah, Ga., features a detailed technical program. Five programming tracks of peer-reviewed sessions, Pulping, Engineering, Environmental, Recycling and Sustainability, will answer the most pressing business and technical questions faced by pulp and paper companies as they manage raw materials, assets, regulatory requirements and production assets.
Register now and save.
The TAPPI PEERS Conference will be co-located with International Bioenergy and Bioproducts Conference, creating a value-added opportunity for you to expand your learning, networking, and resources by attending both events.
See you in Savannah!
Back To Top
|
TAPPI PLACE Webinar - 2012 Conference "Best Extrusion Coating Paper"
Thursday, July 12, 2012
11:00 AM Eastern Daylight Time
Presented by Kelly Frey, of Chevron Phillips Chemical Co., and the recipient of the TAPPI 2012 PLACE Division Leadership and Service Award.
Optimizing Time in the Air Gap in Extrusion Coating for Improved Adhesion is the 2012 WINNER of the prestigious Dragan Djordjevic Award for best conference paper in extrusion coating or cast film.
This webinar explores adhesion through oxidation in the extrusion coating process and how Time in the Air Gap (TIAG) affects adhesion for extrusion coating primed and unprimed paper and film.
Benefits of Attending:
- Learn how optimizing TIAG for the extrusion coating process can potentially provide a significant cost savings and improvements in overall efficiency, and the quality of finished materials
- Gain a better understanding of how to improve adhesion through oxidation and how to optimize TIAG for their process
- Explore currently published time in the air gap (TIAG) recommendations in extrusion coating, for optimal adhesion, to determine if these current recommendations are still valid
- Get a detailed look at how TIAG affects adhesion in many different scenarios, from processing different polymers and substrate types, to various processing conditions.
Register now! Free for TAPPI Members.
Back To Top
|
The TAPPI Introduction to Kraft Pulping and Bleaching Course is an excellent way to network and learn among peers. It's coming up soon, August 13-14, 2012 at TAPPI Headquarters in Norcross, Ga., USA.
This course compiles two full weeks of material into two days of expert instruction in kraft pulp mill operations. If a formula could illustrate the content and benefit of this course, it might look like this:
1 Expert + 2 Days = Greater Ability multiplied by Improved Operations + 1.3 CEUs
Join peers from companies that have taken advantage of this training:
- Boise Paper Solutions
- Canexus
- Cariboo Pulp and Paper
- Domtar
- FM Global
- International Paper
- MeadWestvaco
- PH Glafelter
- Rayonier
- Tembec
- Weyerhaeuser.
Who should attend?
This course is ideal for anyone new to the kraft pulping process, particularly process engineers and operators. After completing this course, you should be able to:
- Describe and define kraft mill processes, equipment, operating variables and terminology, in order to increase ability to improve operations and pulp quality
- Recognize how one part of the process afects other operations, in order to increase awareness of thinking on a mill-wide scale
- Interpret the factors affecting the overall process in order to improve pulp quality and troubleshoot variations in quality
- Extend awareness of the complex environmental challenges associated with kraft pulp production.
Click here to view the Course Schedule.
You'll be able to find out exactly all that you'll be depositing into your valuable bank of knowledge. We look forward to seeing you at TAPPI Headquarters for this course in August 2012.
Back To Top
|
TAPPI and the Pulp and Paper Safety Association (PPSA) are pleased to announce their new course on workplace safety leadership and modern safety management principles, The Safety Management Leadership Course. The course will be held at TAPPI headquarters in Norcross, Ga., August 15-16.
The papermaking, conversion, and paper recycling industries have traditionally suffered from high workplace accident rates. Through a concentrated industry effort, the number of workplace injuries in the paper and pulp industry between 1994 and 2010 declined at a faster rate than the national rate for all private industries.
The Safety Management Leadership Course will provide managers and leaders with the best practices in safety for the paper and packaging industry that should help further reduce these workplace safety incidents. The course is designed for anyone involved in workplace safety including human resources, training, safety supervisors, team leaders, plant managers, project leaders, frontline supervisors, and safety committee participants.
The course will be led by industry expert and course chair Matthew Kanneberg from RockTenn.
"Participants in the course will be able to understand the fundamentals of safety and safety management principles, including recordkeeping, incident investigation, safety culture, managing change safely, understanding safety behavior, risk management, and measuring performance," Kanneberg said.
Course registration is limited to 30 participants so please register today at the course website. Early registration discounts are available.
Back To Top
|
The 2012 TAPPI Tissue Properties & Manufacture Course is coming to TAPPI headquarters in Norcross, Ga., USA., on August 15 -16. This two-day course is a comprehensive overview of the entire tissue manufacturing process taught by leading industry experts.
The focus of the course is on learning ways to improve tissue manufacturing operations and produce a higher quality final product.The Tissue Properties & Manufacture Course will provide participants with more confidence in understanding tissue performance properties and how they are achieved, steps to improve tissue manufacturing, and preparation for more advanced topics.
The course will be taught by Michael J. Kocurek, PhD, Professor Emeritus at North Carolina State University, along with a faculty of experienced industry professional. Last year, more than 95% of Tissue Properties & Manufacture Course participants reported that they had increased their ability to impact tissue performance and design by attending the course. Participants enjoyed the opportunity to learn and network with industry peers and receive instruction from multiple instructors.
The Tissue Properties & Manufacture Course is designed for professionals with limited or intermediate experience including;
- Tissue Mill Operators
- Technical Process Engineers
- Non-Technical Professionals
- Tissue Manufacturing personnel.
This is an introductory/intermediate level course. if you are looking for an advanced course on tissue, consider the next TAPPI Tissue Runnability Course.
There are only 25 spaces available for this popular course, so please register today at the course website.
Back To Top
|
TAPPI headquarters in Norcross, Ga., USA, will host the annual Improving Paper Machine Performance Course August 21 - 23. This course provides students the tools needed to evaluate the performance of their paper machines against industry standards and evaluate ways to improve performance and optimize efficiencies. This year the course schedule has been expanded to include an important area of operation- evaluating energy savings.
Dick Reese of Dick Reese and Associates will help attendees learn how to evaluate energy consumption. Reese has completed energy evaluations on more than 125 paper and pulp machines in 56 mills. Several mills have reduced annual energy cost by $1 million-plus by implementing recommendations from the energy evaluations.
After successfully completing this course, participants should be able to:
- Explain how to establish a paper machine performance audit
- Improve performance and optimize energy conservation and efficiency of your paper machine
- Determine the tools needed to benchmark paper machine operations
- Identify areas of PM performance that are sub-standard.
The educational material has been designed as an intermediate or advanced course for process engineers and mid- to upper-level manufacturing managers. Service technicians, sales personnel, and engineers within the chemical and equipment categories will also benefit by attending this course.
A degree in engineering or other technical field is suggested, but not required. A good working knowledge of the paper machine is recommended (this is not an introductory course). Please bring your laptop computer for this working course. If you don't have one you may share with another course participant.
There is only room for 25 course participants, so please register today.
For more information, please visit the course website.
Early registration, travel, and lodging discounts are available.
Back To Top
|
TAPPI's International Bioenergy and Bioproducts Conference, October 17-19, 2012 in Savannah, Georgia, USA will focus on advancements and commercialization of bio-conversions that leverage the forest products manufacturing infrastructure, providing you with a deeper analysis of the technology and economics involved in commercializing bio-refineries. Learn more about IBBC and see the entire technical program.
Keynote Speakers:
- Paul Spindler, Vice President of Technology at Catchlight
- John B. Crowe, Chairman and Chief Executive Office, Buckeye Technologies, Inc.
In addition, IBBC will include technical presentations, expert panels, case studies, and reports from projects that address:
- Feedstock and harvesting improvements to increase yield and quality of biomass
- Bioelectricity using combined heat and power (CHP)
- Bioconversion technologies for wood and biomass
- Production of chemicals and transportation fuels from wood and biomass
- Policies and incentives for bioconversion projects
IBBC will be co-located with the TAPPI PEERS Conference, creating a value-added opportunity for participants to expand their learning, networking and resources by attending both events.
Exhibit and Sponsorship opportunities are available. Contact Shane Holt at 800.369.6220, ext. 3345 for more information.
Back To Top
|
TAPPI's International Bioenergy and Bioproducts Conference, October 17-19, 2012 in Savannah, Ga., will include a tour to Herty Advanced Materials Development Center the morning of Wednesday, October 17. Chartered by the State of Georgia, Herty has leveraged its industry-proven laboratory and pilot capabilities to execute its strategic plan that includes significant emphasis in the biopower and biofuels areas. Herty's focus is on feedstock with current impact of more than $1.5 billion in alternative energy commercialization projects. Herty provides a hub location needed for rapid cost-effective development of biomass resources for energy production. Learn more about Herty and this tour.
IBBC will focus on technical advancements and commercialization of bioconversion technologies that leverage the forest products manufacturing infrastructure. Learn more about IBBC and see the entire technical program.
IBBC will also feature Keynote Speakers:
- Paul Spindler, VP of Technology at Catchligh
- John B. chairman and CEO, Buckeye Technologies Inc.
In addition, IBBC will include technical presentations, expert panels, case studies, and reports from projects that address:
- Feedstock and harvesting improvements to increase yield and quality of biomass
- Bioelectricity using combined heat and power (CHP)
- Bioconversion technologies for wood and biomass
- Production of chemicals and transportation fuels fromwood and biomass
- Policies and incentives for bioconversion projects'
IBBC will be co-located with the TAPPI PEERS Conference, creating a value-added opportunity for participants to expand their learning, networking and resources by attending both events.
Back To Top
|
This newly published information-packed volume provides practical, industry-focused approaches to operational issues, and includes a first-ever, complete examination of the ongoing environmental and staging changes that occurred after the discontinuation of chlorine usage in 1996.
Bleaching of Pulp, 5th Edition is written to assist production engineers, supervisors, and scientists find quick solutions to today's immediate challenges in modern bleaching. The text is also designed to help both novice and seasoned professionals quickly understand a wide range of operational issues.
Authors: Alan W. Rudie, Ph.D., and Peter W. Hart, Ph.D.
Together they have delivered the industry's premier text on bleaching technologies.
TAPPI Member Price : $155
List Price: $232
Back To Top
|
You can take the woman out of the mill, but you can never remove her love for paper and slime. Just ask microbiologist and TAPPI member Linda Robertson who, after building a highly successful and thoroughly enjoyable career in the paper industry for 30 years, retired in 2006 only to return after six short months.
Linda credits the fantastic network she's built through her involvement in TAPPI as one of the driving forces behind her highly successful career, and encourages anyone – no matter at what career stage they are – to develop. "The ability to present papers and publish, as well as meeting people all over the globe, staying in touch, and presenting papers are all beneficial when you are building a career."
Learn more about Linda's career by reading this month's Member Spotlight.
Spotlight participants are recommended by fellow members and staff. If you would like to nominate a member just send their name (or names) to MemberSpotlight@Tappi.org.
We will forward a Spotlight Questionnaire to fill out and return.
We look forward to seeing you in the Spotlight!
Back To Top
|
Join us on Tuesday, August 14, 2012, at the Mid-Valley Country Club in De Pere, Wis., USA. An afternoon shotgun scramble golf outing is planned with dinner to follow.
Your participation will help fund scholarships for local TAPPI and PIMA programs.
Multiple Prizes will be awarded and individual pin events will be held.
Those submitting registration with their fee, postmarked by August 9, will be assigned holes on a first-come, first-serve basis. Later registrations will be assigned as space is available. Foursome sponsors and all singles will be notified of their hole assignment at the course on the day of the event.
Check-in registration will be at the main entrance of the golf course club house. Golf clubs will be unloaded, tagged, and placed on golf carts for your assigned hole.
Beverage carts will also be available throughout the day on a cash basis. Lunch will be provided prior to tee-off, with the standard fine cuisine of brats, hamburgers, and beverage.
If you have any questions about this event, please contact Chris Wolslegel.
Full event information and registration details are available online.
Back To Top
|
Join us on Tuesday, August 28, at the Grand View Lodge, Preserve Course, in Pequot Lakes, Minn. A morning shotgun scramble golf outing is planned with lunch to follow.
Please remember, your participation will help fund scholarships for Lakes States TAPPI/North Central PIMA's Scholarship programs. Prizes will be awarded along with a putting contest and a raffle.
Reservation preference will be given to foursomes. Groups of two or less will be placed into foursomes pending availability. We will limit the number of participants to 128.
Entries will only be accepted with full payment. For entries received after August 16, the cost is $135.00 per person. Check-in registration will begin at 8:00 am.
If you have any questions about this event, please contact: Wfrawley@new.rr.com
Full event information and registration details are available online.
Back To Top
|
The Nonwovens Engineers and Technologists Division (NET) of TAPPI will co-locate its annual Innovative Nonwovens Conference (NETInc) next year with PaperCon 2013, April 28 - May 1 in Atlanta, Ga., USA.. The NETInc technical conference is a unique event developed by engineers and technologists to cover the latest market and technical developments and innovations in the global nonwovens industry.
"Co-location of the NETInc Conference at PaperCon 2013, the pulp and paper industry's largest event and most comprehensive technical conference, will provide attendees an expanded range of options to network and learn the latest cutting edge technical content," notes TAPPI President and CEO Larry N. Montague. "The nonwovens industry is a dynamic, rapidly growing segment of our industry that encompasses a wide range of raw materials, applications, and market segments, and it employs some of the most innovative technology in the industry. We're excited about the synergy provided by having these two industry leading events located in one venue."
NETInc offers peer reviewed papers, expert speakers, and exclusive networking opportunities. A comprehensive technical program covers a wide range of products, innovative technologies, and topics including market trends, raw materials, fibers, and processing used in an array of applications including absorbent products, medical applications, building science, and many others.
TAPPI's NET Division covers the global nonwovens business and includes members and nonwovens experts from diverse markets and disciplines. It covers materials, equipment, and processes for the manufacture and use of nonwovens. The division's technical committees sponsor courses, conference sessions, roundtables, and TAPPI PRESS products, as well as networking and problem-solving opportunities.
Back To Top
|
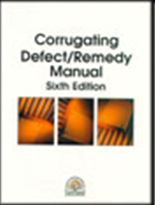 This manual provides a basis for common knowledge of terms, definitions, and methods of correction of corrugated operational defects. The manual illustrates and provides causes and remedies for hundreds of defects affecting corrugated boxes.
The manual is divided into four parts:
- Corrugated Problems
- Printing Problems
- Die Cutting Problems
- Finishing and Manufacturers' Joint Problems.
This manual is also available on a full-color, searchable CD-ROM.
Corrugating Defect / Remedy Manual, Sixth Edition
Product code: 0101R153
ISBN: 0898525152
Author: Carbone, J.T.
Format: Soft cover
Pages: 210
Member Price: $87.00
Non-member Price: $130.
Back To Top
|
Nominations for major TAPPI 2013 awards are due by August 1, 2012. The awards that may be presented next year are:
Gunnar Nicholson Gold Medal Award - The Association's highest technical honor may be presented annually to recognize an individual or individuals for preeminent scientific and engineering achievements of proven commercial benefit to the world's pulp, paper, board, and forest products industries and the other industries that TAPPI serves.
Herman L. Joachim Distinguished Service Award - The Association's highest award for service, may be presented annually to recognize leadership and service that have significantly and demonstrably contributed to the advancement of the Association.
Paul W. Magnabosco Outstanding Local Section Member Award - The highest honor for Local Sections may be presented annually to recognize an individual for outstanding leadership and exceptional service to one or more Local Sections, resulting in significant and demonstrable benefits to Local Section members.
TAPPI Fellow - TAPPI Fellows are Individuals who have been members of TAPPI for not less than 10 years prior to the nomination, and who have contributed meritorious service to the Assciation and/or the paper and related industries. Retiring members of the TAPPI Board of Directors become Fellows automatically at the end of their term.
The TAPPI Awards and Honors page has links to these awards and shows the qualifications required and links to the nomination forms that must be completed.
You may submit all nomination forms by email at standards@tappi.org, or you may fax them to the attention of the Awards Department at +1-770-446-6947, or send by mail to TAPPI, Awards Department, 15 Technology Parkway South, Suite 115, Norcross, Ga. 30092, USA.
Back To Top
|
The TAPPI International Research Management Committee requests that nominations be submitted for the William H. Aiken Prize for Research and Development. The award is given for outstanding accomplishments and/or contributions that have advanced the technology of paper and related industries in the R&D field.
The $500 prize is funded by an endowment from the estate of William H. Aiken, TAPPI President in 1967 - 1968, and VP of Technology for the former Union Camp Corp. at the time of his death in 1974. Dr. Aiken won the TAPPI Gold Medal, the association's highest honor, in 1971.
Nominations should be sent to David Bell (DBell@TAPPI.org) TAPPI Headquarters,15 Technology Parkway South, Norcross, Ga. 30092, USA, or by fax (+1 770-446-6947).
The deadline for nominations for the William H. Aiken Prize for Research and Development Award is August 1, 2012.
The nomination should contain a summary of the nominee's technical achievements, impact on the industry and peers, personal data (such as education and work history), and information of other pertinent activity (such as TAPPI activities).
Back To Top
|
PaperCon 2012 was held April 22 – 25, 2012, at the Sheraton New Orleans in New Orleans, La., USA.
The 2012 conference focused on "Growing the Future"- leveraging renewable, recyclable raw materials and developing human capital to ensure value for customers, long-term sustainability for shareholders, and a future for our peers.
New technology programs joining PaperCon 2012 included:
- Control Systems Conference
- RPTA Conference
- Inside and Outside the Box – Optimizing Paperboard Grades
- Sustainabililty Forum
- Procurement Forum.
PaperCon is designed by industry professionals, bringing together CEOs, mill managers, superintendents, scientists, process engineers, and suppliers for the largest pulp and paper technical program in the world. No other event provides such a comprehensive program, networking opportunities, and exhibit among such a distinguished group of industry leaders.
This CD-ROM contains more than 125 presentations and papers presented throughout the conference and is only available on this fully searchable CD-ROM. PaperCon 2012 Conference Proceedings.
View Table of Contents.
Product code: PAPERCD-12
Member Price: $74.00
Non-Member Price: $111.00
Back To Top
|
Interested in nanotechnology but can't bear to wade through detailed technical reports?
Individual reports on nanotechnology by research and marketing firms as well as governmental agencies are comprehensive and insightful. But they can also be tedious to read, expensive to procure, and generally unknown to non-experts interested in nanotechnology.
Offering a reader-friendly and affordable alternative to these options, Nanotechnology: Health and Environmental Risks introduces risk analysis as a tool for responsible environmental decision making in nanotechnology development. The text provides examples of past, present, and future technologies that demonstrate the need for and benefits of evaluating the risks of nanotechnology.
Access the most up-to-date and relevant information on the impact of Nanotechnology on our health and surroundings.
After outlining the steps of risk analysis, this book examines the opportunity costs inherent in present day nanotechnology development. It then introduces life cycle analysis, examining the toxicology of nanoscale materials, and the known impacts of specific nanoscale materials on human beings.
The text also covers environmental impacts and exposure, followed by chapters on the state-of-the-art tools that adapt life cycle thinking into risk analysis for nanotechnology. The final chapters describe current practices for managing the hazards and risks of nanoscale materials and explore the numerous international efforts that address the risks, science, and policies of nanotechnology.
Learn to recognize and overcome the risks involving nanotechnology. With full-color images and insights into the key health and environmental aspects of nanotechnology, this resource shows how risk analysis can play an important role in creating a sustainable future for nanotechnology.
Product code: 11NANOENV
Member Price: $42.00
Non-Member Price: $52.00
Back To Top
|
Authors: Wei-Hong Zhong and Bin Li, Jo Anne Shatkin, Russell G. Maguire, Vivian T. Dang, Gwen M. Gross, and Michael C. Richey
A comprehensive account of how nanomaterials are synthesized and processed, this book presents the theory and technology of introducing nano-based materials as value-added elements into product manufacturing. The book explains the fundamentals of vapor, liquid, solid phase, and biosystem-assisted nanoparticle syntheses, with sufficient analysis of each method to permit decisions on which is most productive, energy efficient, and safe. The text then confronts the problems of scaling up from lab-based syntheses to manufacturing and demonstrates how nanomaterials on the shop floor require new protocols of quality assurance and employee and environmental protection. The book concludes with case studies of individuals who endeavored to commercialize nanotechnologies for higher-volume production.
Nano Science and Nano Materials: Synthesis, Manufacturing, and Industry Impacts.
Product code: 12NSNM
Member Price: $129.00
Non-Member Price: $149.00
Back To Top
|
Wet End Chemistry is the eleventh of 15 CD-ROMs in the Making Pulp and Paper CD-ROM Series. Through this highly interactive, self-paced CD-ROM, participants learn wet end chemistry terms, concepts, and processes.
Learning outcomes
After completing the Wet End Chemistry CD-ROM, participants should be able to:
- Understand the reasons why papermakers use wet end additives in paper
- Describe commonly used functional additives
- Describe commonly used process additives.
Benefits for Everyone
The series is designed for anyone who would benefit from a working knowledge of the pulping and papermaking process, including:
- Paper machine operators
- Process and product engineers
- Sales and technical support staff
- New employees
- Students.
It will also be beneficial to experienced production or technical employees who need a more thorough understanding of a specific area of the operation, especially for cross-training purposes. New employees of chemical and equipment suppliers and paper industry consultants will also benefit from this series.
The complete set of all 15 Making Pulp and Paper CD-ROMs are also available.
Product code: MPP-11
Member Price: $78.00
Non-Member Price: $119.00
Back To Top
|
|
|
TAPPI Over the Wire | 15 Technology Pkwy. S. | Norcross, GA 30092 USA | Voice: 770.446.1400 | Fax: 770.446.6947
|
 |