 |
|
Weekly Spotlight
This report by Pöyry Management Consulting is the latest in an on-going series in Over the Wire Tissue Edition that draws on expertise from Pöyry's global offices to update readers on opportunities and challenges facing tissue producers today
Learn More...
|
Cascades Inc., Kingsey Falls, Que., Canada, this week reported that its Norampac division will close its containerboard mill in Burnaby, B.C., Canada
Learn More...
|
This past Friday, September 16, the shuttered Katahdin paper mills in Millinocket and East Millinocket, Maine (USA), were purchased in escrow by New Hampshire investor Cate Street Capital, with plans to restart both facilities and employ as many as 250 workers by mid-October
Learn More...
|
Why is ozone bleaching scarce in North America and widely used elsewhere?
Learn More...
|
The Dissolving Pulp Forum at this year's TAPPI PEERS Conference, October 2 -5, at the Oregon Convention Center in Portland, Ore., USA, examines the still-evolving specialty cellulose "gold rush" from three basic perspectives
Learn More...
|
The Canadian federal government should take heed of the Canadian Boreal Forest Agreement (CBFA), an unexpected marriage between conservationists and industry that is helping protect the environment and jobs while boosting Canada's image in the world
Learn More...
|
Market Roundup
Total U.S. printing and writing (P&W) paper shipments decreased 6.4% in August compared with August 2010
Learn More...
|
U.S. Containerboard production was flat compared with July 2011, as was the month-over-month average daily production, down just 0.3%
Learn More...
|
Total U.S. boxboard production decreased by 2.7% compared with August 2010, and decreased 0.9% from last month
Learn More...
|
Total U.S. kraft paper shipments in August were 139, 700 tons, a decrease of 5.4% compared with August 2010
Learn More...
|
Pulp & Paper
The equipment, machinery, real estate, and all contents of the 23 acre industrial complex that was Blue Heron Paper Co. is being auctioned off to the public
Learn More...
|
This week Alain Lemaire, president and CEO of Quebec, Canada-based Cascades, and Luc Langevin, president and COO of Cascades Specialty Products Group, inaugurated the recent addition of $3.7 million in new deinking equipment at the Cascades Fine Papers Group, Breakey Fibres mill, Breakeyville, Que.
Learn More...
|
Rayonier, Jacksonville, Fla., USA, this week signed an agreement to acquire approximately 250,000 acres of timberlands from Joshua Timberlands LLC and Oklahoma Timber LLC for $330 million
Learn More...
|
Increased growth was added to the Group's strategic agenda in 2010
Learn More...
|
Södra Cell also has ordered from Vaahto Pulp & Paper Machinery, Finland, a revamp of pulp dryer TM 5 at its Mönsterås chemical pulp mill in Sweden
Learn More...
|
Containerboard/Packaging
With six locations in California, Marfred significantly augments Amcor's position in the market
Learn More...
|
International Paper & Sun Cartonboard Co. has ordered from Metso, Finland, a coated board production line for its mill in China
Learn More...
|
International Paper Co., Memphis, Tenn., USA, reports that its Beaverton Bag Plant in Oregon celebrated its fiftieth anniversary this past week
Learn More...
|
KapStone Paper and Packaging Corp., Northbrook, Ill., USA, has been ranked twentieth overall on Fortune's annual list of the 100 Fastest Growing Companies and were ranked the second fastest in the Industrial category
Learn More...
|
After increasing at a CAGR of 1.65% during the review period, the Argentine packaging industry is expected to grow at a CAGR of 4.62% throughout the forecast period until 2015
Learn More...
|
Starting the beginning of this week (September 19), students and non-professional packaging designers from around the world will be able to submit their work to SCA's Design Challenge 03
Learn More...
|
Stora Enso, Finland, has ordered from POM Technology, Finland, a compact approach flow system for the new testliner machine at its Ostroleka Mill in Poland
Learn More...
|
xpedx, Cincinnati, Ohio, USA, a business of International Paper, Memphis, Tenn., reports that it has expanded its North American network of package design with the opening of a new package design center in its Cincinnati location
Learn More...
|
Nanotechnology
A new report released by MarketResearch.com, Rockville, Md., USA, reveals that the global carbon nanotube market is expected to grow at a CAGR of 56.5% over the period 2010-2014
Learn More...
|
|
People
James W. (Jim) Alexander has been promoted, from COO to president and COO of Container Graphics Corp., Cary, N.C., USA
Learn More...
|
He will assume his new position at the beginning of December.
Learn More...
|
Wayne Clogg, West Fraser's SVP, Woodlands, Vancouver, B.C., Canada, has announced his intention to retire at the end of 2011
Learn More...
|
TAPPI News
October 5-7, 2011 conference in Portland, Oregon covers latest innovations in pulp bleaching technology, equipment, mill applications and processes
Learn More...
|
Deadlines approaching for submitting abstracts for three program tracks
Learn More...
|
Avoid lines and register online for the October 2-5 conference in Portland
Learn More...
|
TAPPI members to elect three new members to the Board of Directors
Learn More...
|
Annual fall meeting & conference at the University of Maine, Orono, on Oct. 13, will cover a full range of issues on and applications for Bioproducts
Learn More...
|
Conference theme, "Work Safely, Accidents Happen in a Split Second," stresses importance of safety in the work place. Areas covered include how to work safely, work place violence and electrical safety standards
Learn More...
|
Biennial conference and exhibition in Amsterdam, October 11-14, 2011 is exclusively dedicated to forest products logistics.
Learn More...
|
November 22-23, 2011 conference will cover pulp technology developments, innovative applications in key end-uses, wood fibre composites and new products.
Learn More...
|
Conference in Munich, Germany, Nov. 8-11, 2011 covers new developments in water, waste water and energy.
Learn More...
|
|
Find us on Facebook
Network with us on LinkedIn
Follow us on Twitter
|
Weekly Spotlight
This report by Pöyry Management Consulting is the latest in an on-going series in Over the Wire Tissue Edition that draws on expertise from Pöyry's global offices to update readers on opportunities and challenges facing tissue producers today. The concluding section of this report was inadvertently omitted in the most recent (September 13) issue of the tissue edition, and so the entire report is being repeated below, with corrections, for the benefit of both Over the Wire and Over the Wire Tissue Edition readers.
The cost of fiber is a key value driver for both recycled and virgin producers of tissue. At current price levels for both virgin and recycled fiber, tissue profitability margins are being squeezed. As virgin pulp prices begin to fall from peak levels, the cost differential between virgin and recycled tissue producers may narrow.
In this From the Experts report, Pöyry analyzes the current pricing environment and estimates how much sorted office paper (SOP) prices need to increase by for recycled tissue producers to approach the cost of manufacturing for virgin producers. Finally, Pöyry takes a look at the impact of declining uncoated free sheet demand on sorted office paper prices.
Historical SOP Prices
After falling rapidly at the end of 2008, sorted office paper prices have since dramatically recovered to levels that are higher than they were before the economic recession.
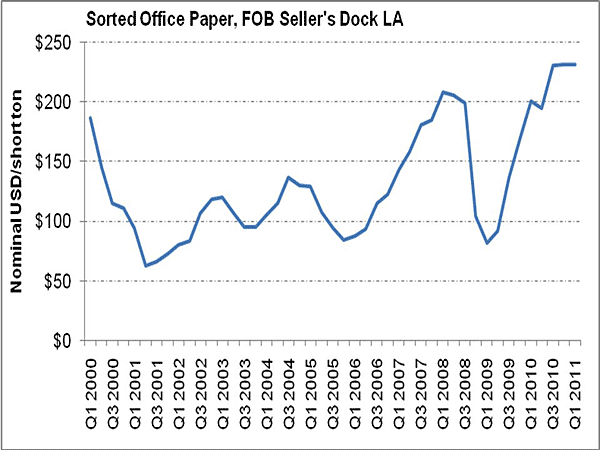
Figure 1. Historical SOP Prices Source: Official Board Markets, Pöyry Analysis
Historically, there has been a strong correlation between prices of SOP and market virgin hardwood pulp. However, as virgin pulp prices have begun to fall from peak levels and SOP prices remain high, there may be a decoupling effect. As the gap between virgin and recycled fiber costs narrows, manufacturing costs may drive a shift in fiber furnish in favor of virgin pulp.
Manufacturing Cost Perspectives: Recycled vs. Virgin At current price levels, North American virgin tissue producers' costs are estimated to be almost $300/short ton higher than for recycled tissue producers (on a weighted-average basis). Despite myriad manufacturing process differences between the two, the cost of fiber accounts for more than 90% of this differential. As such, changes in furnish cost and wastepaper quality will be the main drivers in closing the gap between the two. Given current trends for virgin pulp and SOP prices, the gap between virgin- and recycled-tissue manufacturing costs will likely narrow in coming years.
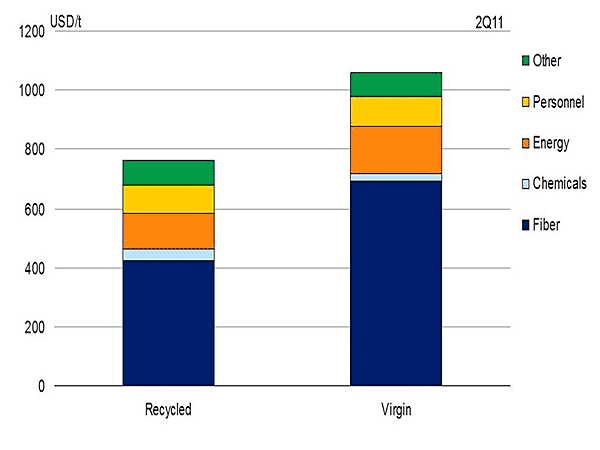
Figure 2. Weighted-Average Manufacturing Costs for AFH Bath Tissue
For example, Mill A produces virgin and recycled bath tissue on a crescent-former tissue machine. Equipped with a deink plant, their pulper-to-reel yield is approximately 65%. At current fiber price levels, the cost of producing tissue at Mill A is 50% higher for virgin tissue than for recycled tissue. But what might the cost differential look like in 2015?
If all input costs are held constant with the exception of the cost for SOP, an average increase of 18%/yr would be sufficient to push the manufacturing cost of recycled tissue above that of virgin tissue. Given that SOP prices have increased at an average rate of 20%/yr over the last five years, this scenario is not inconceivable.
Conversely, holding all input costs the same with the exception of virgin fiber costs, an average decrease of 13%/yr would be required to have a break-even between the cost of manufacturing recycled and virgin tissue. However, this scenario is neither probable nor is it in line with current virgin price forecasts. Using current market-pulp price forecasts, SOP prices would have to increase at an average rate of 12%/yr for the cost of recycled tissue to surpass the cost of virgin tissue at Mill A.
An increase in SOP price of 12-18 %/yr over the next five years is possible given current trends. However, the Pöyry forecast for SOP prices does not indicate that this is a probable outcome. And although furnish cost will be the main driver in narrowing the manufacturing cost gap, it is important to note that recycled tissue production also has greater chemical needs, requires more energy and personnel, and is burdened by the challenge of degrading quality in their raw material.
The Drivers: Impact of Declining Uncoated Free Sheet Demand
What factors may push SOP prices to continue on a steep upward trend? A key factor is the availability of sorted office paper, which is impacted by the production of and demand for uncoated free sheet (UCFS) papers. Demand for UCFS has fallen at an average annual rate of 4%/yr since 2001. Pöyry's current forecasts indicate that demand will continue on this structural decline at an average rate of -3%/yr until 2015.
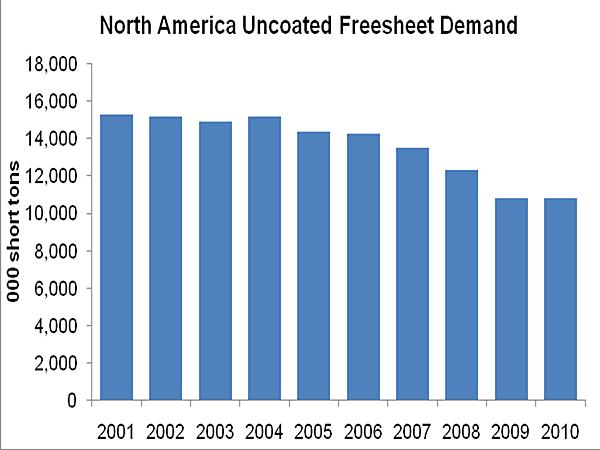
Figure 3. Uncoated Free Sheet Demand in North America, 2001 – 2010
As a result, the availability of recycled office papers will decline accordingly. Potentially an offset to this adverse impact, the collection rate of recycled office papers may improve. Currently, the SOP collection rate is around 50%, which is very low in comparison with OCC (old corrugated containers), for example.
Final Thoughts
As pulp prices decline from peak levels, the manufacturing cost differential between virgin and recycled producers will likely narrow. Under one scenario using current market-pulp price forecasts, SOP prices would have to increase at an average rate of 12%/yr for the cost of recycled tissue to surpass the cost of virgin tissue for a hypothetical mill example.
As a tissue producer facing rising input costs, it is imperative to prepare for the future and manage product pricing strategies accordingly.
Back To Top
|
Cascades Inc., Kingsey Falls, Que., Canada, this week reported that its Norampac division will close its containerboard mill in Burnaby, B.C., Canada. The Burnaby mill has an annual capacity of 128,000 short tons and specializes in the production of 100% recycled linerboard, medium, and gypsum. Nearly 100 employees will be affected by the closure, which will be effective on December 1, at the latest. The mill's production will be redirected progressively towards other Norampac facilities.
"This decision was made to mitigate the negative impact of several factors such as the strength of the Canadian dollar, as well as very high labor and recycled fiber costs. In addition, the mill's profitability has been below our expectations for a few years and we could not pursue our operations under such conditions" said Marc-Andre Dépin, president and CEO of Norampac.
At the same time, Norampac's management also announced that it has reached an agreement with regard to the sale of its Burnaby property.
Back To Top
|
This past Friday, September 16, the shuttered Katahdin paper mills in Millinocket and East Millinocket, Maine (USA), were purchased in escrow by New Hampshire investor Cate Street Capital, with plans to restart both facilities and employ as many as 250 workers by mid-October. Brookfield will remain the mills' owner until the deal is finalized later this month. The closing in escrow allows Cate Street to operate the mills while the company awaits the transfer of environmental permits from Brookfield that legally cannot occur until September 27.
According to reports by the Bangor Daily News (BDN), Maine Gov. Paul LePage's office announced the creation of the new Great Northern Paper Co. with Cate Street Capital as parent company. Great Northern is expected to employ up to 250 workers in East Millinocket, which has been idled since last April, and may hire as many as 500 between it and the Millinocket mill over the next two years. The company said it plans to invest $20 million - $25 million in the east Millinocket mill.
The 250 or so workers hired in East Millinocket starting next week will help it fill already-placed orders from a European customer for virgin newsprint by October 30. Market conditions will dictate restart of the Millinocket mill, which closed in September 2008, idling 150 workers.
Reactions to the late-Friday deal were flowing in by the weekend, the BDN reported. U.S. Sen Olympia Snowe was among the first to proffer congratulations, calling the sale "a seminal moment for the Katahdin region."
Rep. Mike Michaud, a former papermaker at Great Northern Paper in East Millinocket, noted that "we have a proud tradition of papermaking in the region that has been around since my father and grandfather worked in the mills. So many in this region have worked hard to bring it back, and despite the sale and the announcement of hires, there are many that remain without work. While this isn't a solution to all of our challenges, it's clearly an important and positive step in the right direction that we can work to build on moving forward."
Back To Top
|
Why is ozone bleaching scarce in North America and widely used elsewhere? Does partial replacement of chlorine dioxide with ozone cut costs without affecting pulp properties? How should oxygen delignification systems be designed to achieve 75% delignification?
These are a few examples of the technical questions that will be addressed by industry knowledge leaders at the 2011 International Pulp Bleaching Conference
The International Pulp Bleaching Conference to be held October 5-7 in Portland, Ore., USA, will focus on the newest developments and research advances in the pulp bleaching field, including the latest mill experiences, current practices, low-cost conversion solutions, performance, environmental concerns, networking opportunities, and other relevant issues shaping the industry.
The complete list of technical sessions is available online.
This conference is held every three years and will comprise a single track program, featuring nine technical sessions (including a poster session), mill tour, dinner cruise, and a special plenary session. More information and registration are available online.
Back To Top
|
The Dissolving Pulp Forum at this year's TAPPI PEERS Conference, October 2 -5, at the Oregon Convention Center in Portland, Ore., USA, examines the still-evolving specialty cellulose "gold rush" from three basic perspectives. Following a Sunday afternoon (October 2) opening presentation by global consultants, The dp Group, on latest process developments and technologies worldwide, suppliers including Andritz and Metso, will explore systems approaches being used in several major conversion and expansion projects underway around the world. Jacobs Engineering then examines options, directions, and considerations for companies evaluating dissolving pulp production. The Sunday sessions are capped by a special panel session with seven experts in the arena, including speakers from the earlier sessions. This discussion session responds to specific, submitted questions and comments from the attendee audience.
On Monday morning (October 3), the Forum shifts focus with a special bridge session into the main PEERS program that looks at current market developments around the world and the developing outlook for dissolving pulp production and demand for the next two to three years. During this session, RISI and Poyry International will examine the dissolving pulp "path" into the foreseeable future and explore forces likely to control progress as well as setbacks along the way, including recent successes as well as failures of global cotton crops.
More information, including registration, is available online for the Dissolving Pulp Forum and 2011 PEERS, as well at the 2011 International Pulp Bleaching Conference being held at the Oregon Convention Center immediately following PEERS, on October 5-7.
Back To Top
|
The Canadian federal government should take heed of the Canadian Boreal Forest Agreement (CBFA), an unexpected marriage between conservationists and industry that is helping protect the environment and jobs while boosting Canada's image in the world. That was the view expressed earlier this week at a panel at the Museum of Nature in Ottawa held to celebrate National Forest Week and the International Year of the Forest. The panel included Avrim Lazar, president and CEO of the Forest Products Association of Canada (FPAC), Richard Brooks, the forests campaign coordinator for Greenpeace, and Tim Gray, the program director for the Ivey Foundation.
The landmark Boreal Agreement, signed in May 2010, brought together nine conservation groups and 21 forest companies belonging to FPAC. The two sides agreed to lay down arms and instead work together to change the old paradigm of the environment versus the economy into one that recognizes the need for both environmental conservation and a healthy industry.
Avrim Lazar of FPAC says the CBFA is the single most recognized and celebrated environmental initiative coming out of Canada for the past decade and he suggests Canada can capitalize on that internationally. He has already been asked to explain the collaborative win-win approach that underpins the agreement in Washington and other parts of the U.S. as well as in Europe, while other resource industries in Canada have also shown interest.
Lazar says the government can also look to the CBFA for lessons about conservation planning, job protection, and resolving conflicts.
The CBFA is now making significant strides to turn the agreement into concrete change on the ground that will protect the Boreal forest and threatened wildlife species while also protecting the people who rely on the Boreal for their economic prosperity and traditional way of life. The CBFA Secretariat is also working on caribou protection plans, world leading forest management practices, market outreach, and deepening relationships with First Nations and provincial governments.
Back To Top
|
Market Roundup
Total U.S. printing and writing (P&W) paper shipments decreased 6.4% in August compared with August 2010, according to the AF&PA's (Washington, D.C., USA) August 2011 Printing-Writing Paper Report released this week. All four major P&W PAPER grades posted decreases compared with last August. U.S. purchases (shipments + imports – exports) of P&W papers decreased 10% in August. Total P&W paper inventory levels decreased 4% compared with July 2011.
Some points of interest from the report include:
- July exports of uncoated free sheet increased year-over-year for the fifth straight month
- Shipments of coated free sheet decreased year-over-year for the ninth consecutive month
- Coated mechanical purchases decreased year-over-year for the fifth consecutive month
- Uncoated mechanical shipments decreased year-over-year for the fifth consecutive month following 15 consecutive months of year-over-year increases.
Back To Top
|
U.S. Containerboard production was flat compared with July 2011, as was the month-over-month average daily production, down just 0.3%, according to the AF&PA's, Washington, D.C., USA, August 2011 U. S. Containerboard Statistics Report released this past week. The containerboard operating rate for August 2011 was down 2.0 points over August 2010 to 97.5% and 0.3 points from July's operating rate.
Additional key findings from the report include:
- Linerboard production was down over last year
- Medium production showed a slight decline from July 2011.
Back To Top
|
Total U.S. boxboard production decreased by 2.7% compared with August 2010, and decreased 0.9% from last month, according to the AF&PA's (Washington, D.C., USA) August 2011 U.S. Paperboard Report published this week. The report shows that:
- Unbleached kraft folding production increased over the same month last year, and increased from last month
- Total solid bleached boxboard and liner production decreased compared with August 2010, and decreased from last month
- The production of recycled folding decreased compared with August 2010, but increased when compared with last month
- Inventory of solid bleached kraft paperboard decreased in August.
Back To Top
|
Total U.S. kraft paper shipments in August were 139, 700 tons, a decrease of 5.4% compared with August 2010, AF&PA (Washington, D.C., USA) reports in its August 2011 Kraft Paper Sector Report issued this week. Total inventory was 71,900 tons. Additional key findings from the report include:
- Total unbleached kraft shipments decreased compared with August 2010; however, year-to-date shipments were up compared with the same eight months last year
- Total bleached kraft shipments were up compared with the same month last year for the fifth consecutive month.
Back To Top
|
Pulp & Paper
This week marks a new beginning for Oregon City, Ore., USA. The equipment, machinery, real estate, and all contents of the 23 acre industrial complex that was Blue Heron Paper Co. is being auctioned off to the public. The 100-year-old mill shut its doors earlier this summer as increasing competition for wastepaper from China made it impossible to continue profitable operations.
Disposition of the Blue Heron assets was assigned by a trustee of the court to a joint venture that includes Capital Recovery Group, Rabin Worldwide, Perry Videx, and Go-Dove. A public auction is being held his week through today (September 22) beginning at 10 am PDT. Online bidding is available.
Back To Top
|
This week Alain Lemaire, president and CEO of Quebec, Canada-based Cascades, and Luc Langevin, president and COO of Cascades Specialty Products Group, inaugurated the recent addition of $3.7 million in new deinking equipment at the Cascades Fine Papers Group, Breakey Fibres mill, Breakeyville, Que. Strategically focused on producing high quality deinked kraft pulp, this strategic investment will drive improvements in the quality of Cascades' fine papers, while also protecting jobs, the company notes.
Started in 2010, this initiative required the addition of several types of equipment, including a flotation cell, washers/thickeners, a disperser, and a clarifier, and it also involved the expansion of the building located in Breakeyville. According to Lemaire, "this investment shows our commitment to maintaining our competitive edge in a down economy and challenging market situation. We believe that innovation is the key to our company's growth."
As a result of this investment, the mill's pulp quality has greatly improved. Visible dirt and glue residue have each decreased 50%, while the whiteness has slightly increased. "We consider this to be a very significant benefit, especially as the quality of raw materials—wastepaper to be recycled—is declining more and more. We believe this investment will allow us to remain competitive in continuing to offer high quality recycled products," Langevin said.
Since 1985, the Breakey Fibres mill has specialized in the manufacture of recycled deinked kraft pulp, mainly used in the production of Cascades' fine papers, such as the Rolland Enviro100 family of products.
Cascades Specialty Products Group is a producer of industrial packaging, consumer product packaging, specialty papers, and recovery and recycling. The group has 48 business units located in North America and Europe and employs more than 2,500 people.
Back To Top
|
Rayonier, Jacksonville, Fla., USA, this week signed an agreement to acquire approximately 250,000 acres of timberlands from Joshua Timberlands LLC and Oklahoma Timber LLC for $330 million. The acquisition, expected to close in the fourth quarter of this year, will initially be funded using cash, Rayonier's revolving credit facility, and the assumption of existing debt of the sellers. Closing is subject to customary timberland transaction conditions.
"The quality and location of these timberlands make them an excellent strategic fit for Rayonier," said Lee M. Thomas, chairman and CEO of Rayonier. "This transaction is a major step forward in our strategy to grow and diversify Rayonier's timberland ownership while allowing for further expansion of our rural land sales program."
The timberlands are located in Mississippi, Louisiana, Oklahoma, and Alabama. Upon completion of the acquisition, Rayonier will own, lease, or manage some 2.7 million acres in 10 states in the U.S., and New Zealand.
Back To Top
|
SCA, Stockholm, Sweden, earlier this week (Monday, September 19) hosted the Capital Markets Day in Stockholm. The company's strategy of recent years of focusing on costs, cash flow, capital efficiency, and innovation remained firmly in place this year. Increased growth was added to the Group's strategic agenda in 2010.
"SCA has implemented key efficiency-enhancement measures and boosted the pace of its new product launches. We have managed to grow both in mature and emerging markets. Our global TENA and Tork brands, each which generate more than EUR 1 billion in annual sales, have strengthened their market shares. To capitalize on the growth opportunities in the hygiene operation, we have conducted acquisitions and investments in a number of growth markets, including Brazil, Russia, Turkey, Mexico, and Argentina," said Jan Johansson, SCA president and CEO.
Johansson pointed out that the completed action programs have reduced the cost base and made SCA a stronger company than it previously was. Focusing on cash flow has led to lower net debt and improved the debt payment capacity, giving SCA better means to grow. SCA will grow, it says, by reinforcing existing and establishing new market-leading positions. The aim is to reduce the number of local brands and increase the number of global brands.
"SCA is currently the world's third largest hygiene company and hygiene products now account for 60% of the Group's sales. The aim is to continue to grow by capitalizing on the growth opportunities created by the global population increase, improved prosperity, an aging population, and greater market penetration. We can also see a rising consumer interest in convenience and sustainability," said Johansson.
SCA's Group-wide financial target of a return on capital employed of 13% over the course of an economic cycle remains in place.
Back To Top
|
Södra Cell also has ordered from Vaahto Pulp & Paper Machinery, Finland, a revamp of pulp dryer TM 5 at its Mönsterås chemical pulp mill in Sweden, The revamp will boost production and output and improve runnability of the pulp dryer. The machine produces both softwood pulp and hardwood pulp.
Vaahto's order includes water removal elements, steam box, lead rolls, and suction roll technology, as well a major extension of the vacuum systems of the line. Installation, startup, and training services are also to be included.
The wire width of the machine is 4,650 mm and design speed 250 m/min. The maximum daily output of the dryer can reach 950 metric tons.
Equipment will be manufactured in Vaahto's workshops in Hollola and Tampere in Finland. Startup is scheduled for October 2012. The value of this kind of order amounts usually between EUR 5 and 7 million.
Back To Top
|
Containerboard/Packaging
Amcor Packaging Distribution (APD), Buena Park, Calif., USA, has acquired Marfred Industries, Los Angeles, Calif. With six locations in California, Marfred significantly augments Amcor's position in the market. The combined businesses will provide new products, additional services, and technical customer support.
With global headquarters in Melbourne, Australia, Amcor Ltd. has diversified operations in Australia, New Zealand, Europe, Asia, and the Americas. Amcor Packaging Distribution manufactures corrugated boxes through its Manufactured Packaging Products (MPP) division as well as distributes packaging and industrial supplies and provides engineered packaging solutions through its Landsberg division. Marfred was founded in 1963 and through its corrugated manufacturing, folding carton manufacturing, and packaging distribution services has become one of the largest independently owned packaging manufacturers in the U.S.
According to APD head Bernie Salvatore, "we are proud to join forces with Marfred. They have earned a significant reputation in the marketplace for outstanding customer service and innovative packaging solutions. The two companies share common histories, values, and a passion for exceeding customer expectations. Together, we look forward to the diverse solutions our combined capabilities will bring to our customers, co-workers, and suppliers."
Back To Top
|
International Paper & Sun Cartonboard Co. has ordered from Metso, Finland, a coated board production line for its mill in China. The value of the order will not be disclosed. However, according to Metso, a typical value of this kind of a production line is EUR 90-120 million, depending on the scope of the delivery and the production output.
Metso's delivery will include a complete coated board machine from headbox to winders, including stock preparation and approach flow systems, hoods with machine ventilation, and coating color preparation systems. Additionally, the full-scope automation delivery will include process, machine, and quality controls, web break monitoring and web inspection, as well as condition monitoring.
International Paper & Sun Cartonboard Co. is a joint venture co-established by International Paper Co. (Memphis, Tenn., USA) and Sun Paper Group of China. The joint venture combines International Paper's management and technology experience with Sun Paper Group's local resources and in-depth understanding of local market. The combined capacity of its three machines is 850,000 metric tpy and the net sales in 2010 were about EUR 530 million ($700 million).
Back To Top
|
International Paper Co., Memphis, Tenn., USA, reports that its Beaverton Bag Plant in Oregon celebrated its fiftieth anniversary this past week. The plant began operations on Sept. 16, 1961, producing environmentally friendly paper bags. "Our bags are a great environmental choice as they are recyclable, reusable, and produced using renewable resources," said Ron Gale, plant GM.
The Portland, Ore., City Council has recognized the benefits of paper and recently passed legislation limiting the use of plastic bags within city limits. The move is designed to lessen the impact on the environment. "Paper recycling is an environmental success story not only in the state of Oregon, but throughout the country. Paper bags are recycled at a rate between 50% and 72%, compared with 10% to 14% for plastic bags," said Craig Williams, GM of IP's Kraft Bag business. "This is an exciting time for the families and team members of the Beaverton Bag Plant to celebrate 50 years of service to the greater Oregon area, and to assist current and new customers with the transition from plastic," Gale said.
Back To Top
|
KapStone Paper and Packaging Corp., Northbrook, Ill., USA, has been ranked twentieth overall on Fortune's annual list of the 100 Fastest Growing Companies and were ranked the second fastest in the Industrial category. The ranking, from the September 26, 2011 issue of Fortune, is based on revenue growth rate, EPS growth rate, and three-year annualized total return to investors.
Roger Stone, CEO of KapStone, noted that "this is the second year we have placed in the top 20 of the 100 fastest growing companies as ranked by Fortune. We are diligently working to maintain our profitable growth rate."
KapStone Paper and Packaging Corp.is the parent company of KapStone Kraft Paper Corp., which operates paper mills in Roanoke Rapids, N.C., and North Charleston, S.C., a lumber mill in Summerville, S.C., and five chipping mills in South Carolina. The business employs approximately 1,600 people.
Back To Top
|
After increasing at a CAGR of 1.65% during the review period, the Argentine packaging industry is expected to grow at a CAGR of 4.62% throughout the forecast period until 2015, according to a new report by Research and Markets, Dublin, Ireland. Titled The Argentine Packaging Industry—Market Opportunities and Entry Strategies, Analyses, and Forecasts to 2015, the report is a top level overview of the Argentine packaging industry, giving a breakdown of sector by segments such as paper and board, flexible plastic, rigid plastic, metal, and glass. iCD Research also provide details of the top companies active across the packaging industry in Argentina, as well as analyzing the emerging trends and opportunities.
This report offers insights into market opportunities and entry strategies adopted to gain market share in the Argentine packaging industry. In particular, it offers in-depth analysis of the following:
- Market Opportunity and Attractiveness: Detailed analysis of current market size and growth expectations during 2010–2015
- Procurement Dynamics: Trend analysis of exports and imports of packaging material, along with their implications and impact on the Argentine packaging industry
- Industry Structure: Five forces analysis to understand various power centers in the individual industry segments and how they are likely to develop in the medium term
- Competitive Landscape: Analysis of key companies in the public and private sectors of the Argentine packaging industry
- Market Entry Strategy: Analysis of possible ways to enter the market along with an understanding of how existing operators have achieved this, including key contracts, alliances, and strategic initiatives
- Business Environment and Country Rrisk:: A range of drivers at country level, assessing business environment and country risk.
Back To Top
|
 Starting the beginning of this week (September 19), students and non-professional packaging designers from around the world will be able to submit their work to SCA's Design Challenge 03. This year's challenge is to create an innovative packaging design for LEGO's ‘Bricks and More' starter set and SCA's Tempo tissue box.
Participants that make it to the final will be invited to a workshop in one of SCA's Design Centers, including a visit to the factories of its two category sponsors. During this workshop, finalists will receive expert support and guidance to improve their designs before submitting them to the SCA Design Challenge final.
In addition to getting the chance to work with industry professionals and pitch their work to well-established designers, there will be EUR 14,000 in price money to be split among the finalists and internships at SCA Packaging for the category winners. Moreover, the winning concepts might even make it into production.
"This year, we are partnering up with two leading brand manufacturers and submissions to the Design Challenge need to focus around two very recognizable products. In addition, we are opening up the competition globally." says Katia Schotte, Communications Director at SCA Packaging. We believe this will make an interesting mix and will surely enrich the final shortlist."
Submissions to the SCA Design Challenge 03 will be accepted until December 4. More information is available online.
Back To Top
|
Stora Enso, Finland, has ordered from POM Technology, Finland, a compact approach flow system for the new testliner machine at its Ostroleka Mill in Poland. Startup is scheduled for the first quarter of 2013.
At a wire width of 8,600 mm and a design speed of 1,800 m/min, the new Narew PM 5 project will produce 455,000 metric tpy of testliner. The new machine is designed to produce lightweight testliner and recycled fluting in a basis weight range of 65-140 gsm.
The POM compact approach system delivery includes: two POMix Stock Processors for efficient stock mixing, three POMp Degassers for white water dearation, two POMlock suction leg sealing units, as well as compact process solutions and engineering for the whole approach flow system. Stora Enso's focus of this investment was on operational savings from improved drainage, cleanliness, and quality, as well as on space and especially energy cost savings, which all are met by POM System applications and principles.
POM Technology previously delivered several POM Degassing solutions to Stora Enso Varkaus and Imatra Mills in Finland. At the beginning of this year, the company will become part of Aikawa Fiber Technologies (AFT), which has manufacturing centers in Canada, China, Finland, Japan, and South Korea.
Back To Top
|
xpedx, Cincinnati, Ohio, USA, a business of International Paper, Memphis, Tenn., reports that it has expanded its North American network of package design with the opening of a new package design center in its Cincinnati location at 4510 Reading Road. The new package design center will allow the company to lower packaging costs for Cincinnati-area customers and increase their speed to market.
"The key capability that we're gaining with the Cincinnati package design center is increased speed to market for our customers in the Tri-State area," said Chris Baum, xpedx's GM, Indiana, Kentucky, and Ohio Divisions. "Since xpedx is material neutral, we're able to manage the entire process from concept and design to assembly and delivery. As a sole source packaging supplier, we give our customers a simpler, faster path to bring their products to market."
xpedx's Cincinnati package design center will serve food service and retail packaging customers in Ohio, Kentucky, and Indiana. However, xpedx also has package design centers with additional areas of specialty nearby in Livonia, Mich., and Pittsburgh, Pa. The Cincinnati package design center can easily access automotive and manufacturing package design expertise from those centers, as well. Throughout North America, xpedx has a network of 10 package design centers and teams of design experts in 12 additional markets.
The new design center features xpedx's GlobalPKG software, which is web-based packaging development and management technology that allows for specification management to take place at any of xpedx's interconnected design centers in North America. The Cincinnati location also has ArtiosCAD, Kongsberg CAD, and a Gaynes Drop Tester.
"With these systems all in-house in Cincinnati, xpedx can quickly design, test and produce packaging that reduces costs and drives profitability," said Baum. "Customers can have all that work done in one place by the xpedx team, without having to coordinate multiple packaging vendors. Their products go to market faster with less cost."
xpedx creates material-neutral package designs using corrugated, folding carton, specialty foams, thermoformed plastics, molded fiber, and pulp and flexible packaging.
Back To Top
|
Nanotechnology
A new report released by MarketResearch.com, Rockville, Md., USA, reveals that the global carbon nanotube market is expected to grow at a CAGR of 56.5% over the period 2010-2014. The report, Global Carbon Nanotube Market 2010-2014," which covers the Asia Pacific region as well as the Americas and Europe, indicates that the market is being driven by the increased demand from the Aerospace and Defense industries.
According to an industry analyst, "being one of the strongest known materials, carbon nanotubes improve the strength of many materials used in various applications including Aerospace. In the area of defense, carbon nanotube fibers are being used in the advancement of composite armor systems for vehicles and body armors. These applications in the Aerospace and Defense industry have had a positive impact on market growth."
The report also highlights that high production costs could hinder the growth of this market. However, the emergence of several research initiatives in this field is expected to boost market growth. This market is also marked by a substantial decline in prices of these tubes.
Global Carbon Nanotube Market 2010-2014 examines the key trends, drivers, and challenges impacting the evolution of this market. Key questions answered in this report include:
- What will the market size be in 2014 and at what rate will it grow?
- What are key trends is this market subject to?
- What is driving this market?
- What are the challenges to market growth?
- Who are the key vendors in this market space?
- What are the opportunities and threats faced by each of these key vendors?
- What are the strengths and weaknesses of each of these key vendors?
Back To Top
|
People
James W. (Jim) Alexander has been promoted, from COO to president and COO of Container Graphics Corp., Cary, N.C., USA. Neil B. Saunders is passing on the role of president and remains the company's chairman and CEO.
Alexander has been COO of Container Graphics for the past nine years and "has done an excellent job," Saunders noted. "His promotion to president reflects my and the board of directors' continued confidence in his leadership. My title is being shortened, from president and CEO, to CEO. I look forward to working with Jim and his team for many years to come."
Alexander started with Container Graphics in 1976, and was most recently promoted to COO in 2002. Container Graphics is one of the world's largest manufacturers of printing plates and cutting dies for corrugated packaging production. The company operates 17 facilities worldwide.
Back To Top
|
Smurfit Kappa Recycling, U.K., has named Andrew Perkins commercial director. He will assume his new position at the beginning of December.
Perkins will join Smurfit Kappa Recycling from Aylesford Newsprint in the U.K., where he has been head of recycling for a business that handled 500,000 metric tons of material per year. His many years of experience in growing paper recycling businesses and increasing recovered paper supplies also includes a period at Biffa.
Smurfit Kappa Recycling's current commercial director Martin Blood, who has been with the company for more than 40 years, is stepping down from his current role, but will continue to work for the company on a part-time basis and will assist Perkins.
"I am delighted that Andrew will be joining us later this year as commercial director," said Simon Weston, managing director of Smurfit Kappa Recycling. "His many years of experience in the paper recycling business will add further strength to our team and I know he is looking forward to the fresh challenge."
Part of the world's largest fiber-based packaging group (Smurfit Kappa Group, Ireland), Smurfit Kappa Recycling provides a full spectrum of paper and board recycling solutions for businesses and organizations, including recovery of containerboard, office papers, and plastics and security shredding.
Back To Top
|
Wayne Clogg, West Fraser's SVP, Woodlands, Vancouver, B.C., Canada, has announced his intention to retire at the end of 2011. Clogg joined the company in 1980 and has served West Fraser in a number of senior management roles including, most recently, having overall responsibility for woodlands and fiber management for the company.
Hank Ketcham, West Fraser's chairman, president and CEO, noted that said "Wayne has been a key contributor to our success during his 32 years with us. He is a leader who reflects and has strengthened West Fraser's culture."
West Fraser is an integrated wood products company producing lumber, wood chips, LVL, MDF, plywood, pulp, and newsprint. The company has operations in western Canada and the southern U.S.
Back To Top
|
TAPPI News
IPBC Conference Brings Pulp Bleaching Industry Together To Address Developments and Research Advances
Why is ozone bleaching scarce in North America and widely used elsewhere? Does partial replacement of ClO2 with ozone cut costs without affecting pulp properties? How should oxygen delignification systems be designed to achieve 75% delignification?
These are a few examples of the technical questions that will be addressed by industry knowledge leaders at the 2011 Pulp Bleaching Conference.
The International Pulp Bleaching Conference, to be held Oct 5-7, 2011 in Portland, Oregon will focus on the newest developments and research advances in the pulp bleaching field: latest mill experiences, current practices, low-cost conversion solutions, performance, environmental concerns, networking opportunities and other relevant issues shaping the industry.
You can see the complete list of technical sessions in the technical program.
This conference is held every three years and will comprise a single track program, featuring 9 technical sessions (including a poster session), mill tour, dinner cruise, and a plenary session that you will not want to miss. Learn more and register at the event website.
Back To Top
|
Still time to register for TAPPI PEERS Conference, October 2-5, 2011 in Portland, Oregon.
Avoid the lines and register now to attend the TAPPI PEERS Conference. To accommodate the record number of industry professionals planning to attend, we're keeping online registration open a few extra days. See who is attending. At TAPPI PEERS, you'll discover and explore mill-proven routes to higher efficiency, attend training workshops, network and share solutions, and see the latest products and services available to the marketplace – and gain a better understanding how of the entire mill process works together. Program highlights include: Keynote Speaker Miles P. Drake from Weyerhaeuser; Dissolving Pulp Forum; Pumped Systems Assessment Workshop; Sustainability Sessions and more.
Learn more about the TAPPI PEERS Conference.
Back To Top
|
Slate Announced for Election of 2012 TAPPI Board of Directors
TAPPI's 2011 Nominating Committee announced a slate of candidates for three director positions. The Candidates are: Michael Exner, Sr. VP-Containerboard Mills, RockTenn; Steven Shifman, President, Michelman Inc.; and Clayton Teague, Director (Recently Retired), National Nanotechnology Coordination Office.
Voting begins December 1, 2011. Per the TAPPI Bylaws members of the organization have until November 1, 2011 to review the slate.
Learn more about the slate and election process.
Back To Top
|
The Northeast Division of the Paper Industry Management Association / Technical Association of the Pulp and Paper Industry will hold its Annual Fall Meeting and Conference at Buchanan Alumni House, University of Maine on October 13, 2011. The Annual Meeting will feature an informative one-day conference entitled Bioproducts: Thinking Outside The Box. Topics to be discussed include nanotechnology, nanocellulose, biobased latices and biofuels.
The technical program will feature the following expert speakers:
- Dr. Phil Jones, Imerys (GA)
- Mr. Michael Billeveau, Sustainable Bioplastics of Maine
- Mr. Michael Bilodeau, UMaine Process Development Center
- Dr. Clay Wheeler, UMaine Chemical & Biological Engineering
- Dr.Yvon Durant, Itaconix (NH)
- Mr. Sean Ireland, Verso Paper – Bucksport Mill
- Dr. Doug Gardner, UMaine Wood Science & Technology
- Mr. Kevin Forrest, Exxon-Mobil (ME)
Who should attend?
Anyone involved in the research and innovation sector of our industry will find this a beneficial conference; mill and technical managers; superintendents, engineers, and supervisors responsible for production, and technical operations; suppliers to the industry.
Registration Form and Agenda
For registration information or for conference questions, please contact Pros Bennett, Phone: 207-949-4176 or e-mail pbennett@maine.edu or Jennifer Barr, Phone 207-856-4645 or email jennifer.barr@sappi.com. Costs: $100 - Includes continental breakfast and lunch.
Proceeds from Northeast PIMA/TAPPI events go towards the scholarship fund.
Back To Top
|
Empire StateTAPPI's Paper Mill Safety Conference (Work Safely, Accidents Happen in a Split Second) will be held October 27th at the Queensbury Hotel in Glens Falls, New York. Featured speaker Eric Giguere from DiVal Safety will present a paper entitled "The Buried Truth Uncovered." Eric's speaking engagements have proven to be a valuable tool for companies with a need for safety awareness. A work-related accident changed his life, and his goal is to try and prevent your family from having to go through what his family went through. Eric will make an impact on you and inspire all of us to work safely.
Other presentations will discuss work place violence and electrical safety standards. In addition, speakers from the Adirondack Safety Council, OSHA, and the Preferred Mutual Association will present. Safety representatives from area mills will also be on a mill safety panel.
Registration cost for attendees not associated with a paper mill or corrugating facility is $125 per person and exhibitors space and registration is $150. Send to: Kathy Russell, AFTEK, Inc., 740 Driving Park,
Rochester, NY 14613 by October 27, 2011
Registration Form and Agenda
Back To Top
|
The PPI Transport Symposium 19, October 11-14, 2011 in Amsterdam is the only biennial conference and exhibition exclusively dedicated to forest products logistics. This industry-leading program concentrates on the global trends, innovations and issues surrounding the transport, material handling, warehousing, and distribution of forest products.
For Further Information
Back To Top
|
The PTS Pulp Symposium will be held November 22-23, 2011 in Dresden. Symposium highlights include discussions focusing on pulp applications in end products including specialty papers, high-quality graphic papers and packaging papers.
Besides paper, the symposium will also focus on wood fibre composites and entirely new fibre-based products with specific properties. Other topics to be covered include nanotechnology and software-supported methods and models that will become key technologies in efficiently fine-tuning the supply of pulp to meet required product properties.
The conference will appeal to a wide range of companies and industry sectors including, pulp and paper mill production, pulp trade, chemical and equipment suppliers, engineers and developers involved with the production of composite materials, market research and procurement of fibrous raw materials staff, and universities and research institutes.
More information
Back To Top
|
On November 8-11, the 2011 PTS Environment Symposium will be held in Munich, Germany. The event will provide a comprehensive three-day program on new developments in the area of water, waste water and energy.
Topics covered during the first day include ecological relevance and sustainability, safety of paper products and related topics. The second day of the symposium is devoted to wastewater as a resource, mill experiences, safe plant operation, new aspects in biology and use of additives. Presentations on day three focus on political and legal framework conditions and on technical options for reducing energy costs.
The conference is targeted at managers, specialists and executive staff of the pulp and paper sector and its related industries whose central task is to reduce environmental impacts and minimize the outlays required for these areas. The program will appeal to staff responsible for energy issues, environmental experts, waste management officers, technical specialists and executives (plant, operations and production managers). In addition, engineering and consultancy firms, plant engineering and construction companies and chemical suppliers will find the program and networking opportunities to be of great interest and value..
For More Information
Back To Top
|
|
|
TAPPI Over the Wire | 15 Technology Pkwy. S. | Norcross, GA 30092 USA | Voice: 770.446.1400 | Fax: 770.446.6947
|
 |