 |
|
Weekly Spotlight
Domtar Corp., Montreal, Que., Canada, this week reported that it will participate with Wisconsin Electric Power Co. (We Energies) to build a $255 million biomass power plant at Domtar's Rothschild, Wis., USA, paper mill.
Learn More...
|
The Sustainable Forestry Initiative (SFI), Washington, D.C., USA, has awarded a total of $35,200 in grants to nine community-based projects to support forestry education activities and green building for low-income families.
Learn More...
|
The latest listing of job openings in the TAPPI Career Center include management and process engineering positions
Learn More...
|
2015 is the 100 year anniversary of TAPPI and an excellent time to celebrate the successes of this industry and the people and companies who have contributed to it. Vote on the logo in the poll located under the TCC Connects ad in the right column.
Learn More...
|
Market Roundup
Total U.S. kraft paper shipments in May were 131,800 tons, an increase of 0.2% compared with May 2010, but up 1.5% compared with April 2011
Learn More...
|
Total U.S. boxboard production last month (May) decreased by 1.5% compared with May 2010, but increased 1.0% from April 2011
Learn More...
|
Much of the increase has been the result of higher wood fiber costs
Learn More...
|
U.S. NBSK prices rose $20/metric ton to a record $1,040/mton in June
Learn More...
|
Will International Paper's bid for Temple-Inland table any effort to boost containerboard prices?
Learn More...
|
Pulp & Paper
Ahlstrom, Finland, this week reported that it will invest a total of EUR 7 million at its Stenay plant in France to be able to produce lower grammage grades, enhancing the quality of one-side coated papers for metalized labels and flexible packaging
Learn More...
|
Boise Inc., Boise, Idaho, USA, and the Alabama Treasure Forest Association (ATFA) announced this week that private forestlands belonging to members of ATFA have earned Forest Management certification from the Forest Stewardship Council (FSC), a first for any forestlands in the state.
Learn More...
|
Canfor Pulp Innovation, the research and development division of Canfor Pulp Limited Partnership (CPLC), Vancouver, B.C., Canada, tomorrow (June 24) is conducting the opening of its new laboratory in Burnaby, B.C.
Learn More...
|
Catalyst Paper, Richmond, B.C., Canada, reports that it has achieved Forest Stewardship Council (FSC) controlled wood and chain-of-custody certifications at its three Canadian manufacturing operations.
Learn More...
|
Clearwater Paper Corp., Spokane, Wash., USA, this week celebrated the grand opening of its newest tissue facility at Shelby N.C., in Cleveland County.
Learn More...
|
International Paper, Memphis, Tenn., USA, has been named one of the Top 100 Best Places to Work in IT by IDG's Computerworld magazine, Framingham, Mass.
Learn More...
|
Kruger Inc., Montréal, Qué., Canada, reports that it will take market-related production shutdowns at its Trois-Rivières, Brompton, and Wayagamack mills in Québec beginning today (June 23) and extending to June 28
Learn More...
|
Metsä Tissue, Espoo, Finland, part of the Metsäliitto Group, this week signed an agreement to become a licensed manufacturer and seller of Georgia-Pacific's Lotus® consumer tissue brand in Russia
Learn More...
|
Mohawk Fine Papers Inc., Cohoes, N.Y., USA, has signed a non-binding letter of intent to buy the business of Bravo Solutions Inc., Elmira, N.Y.
Learn More...
|
Norske Skog Saugbrugs AS, Halden, Norway, has started up another paper machine (PM 6) following an extensive fire in the mill's thermomechanical pulp plant in early February
Learn More...
|
Visy's Tumut pulp and paper mill in New South Wales (NSW) Australia, this past weekend celebrated its 10th anniversary and the official opening of a stage two expansion at the mill
Learn More...
|
American Industrial Partners (AIP), New York, N.Y., USA, has agreed to acquire the worldwide hardwoods and industrial products business unit from Weyerhaeuser Co., Federal Way, Wash
Learn More...
|
Weyerhaeuser Co., Federal Way, Wash., USA, this week launched Weyerhaeuser Solutions Inc. (WSI), a new subsidiary offering a full range of consulting and management services designed to help clients develop, manage, and commercialize forest assets.
Learn More...
|
Containerboard/Packaging
Ahlström Capital, Helsinki, Finland, and the Accent Equity, Stockholm, Sweden, investment fund are combining their operations in the packaging industry to form a new group to be known as Arch Packaging Group AB
Learn More...
|
Cartones America, Cali, Colombia, a privately-owned, Andean Region producer of containerboard, corrugated boxes, clay-coated paperboard, spiral tube board, and specialty board packaging products, has successfully started up PM 3 at its Cali mill following a major rebuild by the Italian company Toscotec
Learn More...
|
International Paper Co., Memphis, Tenn., USA, this week said it will indefinitely shutdown the No. 3 paper machine at its Valliant Mill in Oklahoma on November 1
Learn More...
|
Sonoco Recycling Inc., a wholly owned subsidiary of Sonoco, Hartsville, S.C., USA, and Shoosmith Brothers Inc., this past week opened The Recycling Center, a landfill diversion facility that will be operated by Sonoco Recycling at the Shoosmith Brothers landfill in Chester, Va
Learn More...
|
Nonwovens
Buckeye Technologies Inc., Memphis, Tenn., USA, this week announced plans to close its Delta, B.C., Canada, airlaid nonwovens facility by the end of calendar 2012
Learn More...
|
|
Published Pricing
DuPont Titanium Technologies. Wilmington, Del., USA, has announced a price increase of $0.25 per pound, or as permitted by contract, for all DuPont™ TiPure® titanium dioxide (TiO2) grades sold in North America (U.S. and Canada).
Learn More...
|
Energy
The Nature Conservancy (TNC), Arlington, Va., USA, and the Sustainable Forestry Initiative (SFI, Washington, D.C., this week launched a pilot project to help bioenergy companies in the U.S. support responsible forest management through their procurement of woody biomass
Learn More...
|
People
Boise Inc., Boise, Idaho, USA, announced that Jeff Lane resigned his position as SVP of the company's packaging operations effective yesterday (June 22).
Learn More...
|
KiOR Inc., Pasadena, Texas, USA, a cellulosic fuels producer, reports that former Secretary of State Condoleezza Rice has agreed to join its board of directors, starting in July.
Learn More...
|
Panther Systems, Vancouver, Wash., USA, has named Phil Farmer as its new CEO.
Learn More...
|
TAPPI News
Major association honors include Gunnar Nicholson Gold Medal, TAPPI Fellow, Distinguished Service and Outsanding Local Section Member Awards
Learn More...
|
August 23, 2011, meeting in Wisconsin Rapids, WI. includes golf outing and dinner
Learn More...
|
Paper Industry Students Must Apply by August 1, 2011
Learn More...
|
Two-day Conference Nov. 9-10 in Barcelona, Spain covers wide range of recovered paper issues and topics
Learn More...
|
TAPPI Fellow, active in Corrugated Containers Div. and known for research on corrugated board, passed away May 28
Learn More...
|
Popular couse to be held August 8-9, 2011 in Norcross, Georgia, provides fundamental knowledge of all key kraft operations
Learn More...
|
Course covers properties and manufacturing technology of tissue grades
Learn More...
|
|
Find us on Facebook
Network with us on LinkedIn
Follow us on Twitter
Over the Wire
Please vote on the 100 Year Logo.
|
Big 100 Logo
|
|
Yellow Ribbon Logo
|
View Results
|
Weekly Spotlight
Domtar Corp., Montreal, Que., Canada, this week reported that it will participate with Wisconsin Electric Power Co. (We Energies) to build a $255 million biomass power plant at Domtar's Rothschild, Wis., USA, paper mill. The company's board of directors has approved revised agreements with We Energies and the Wisconsin PSC to allow the project to move forward. Construction is expected to begin soon, with site preparation underway this week. The Boldt Co. of Appleton is the construction manager and general contractor, and Poyry Group is the architect and engineering firm working on the project.
"This project is an innovative way to improve our mill's competitiveness and environmental performance while providing more green power to the State of Wisconsin," said John D. Williams, president and CEO of Domtar. "Wood is a renewable resource that can be used for producing pulp, paper, and electricity, and we are proud to leverage our expertise in sustainable fiber procurement." The project is expected to create some 400 construction jobs and 150 permanent jobs in the surrounding community, including jobs for independent wood suppliers and haulers. Wood, waste wood, and sawdust will be used to produce 50 MW of green electricity for the grid and to support Domtar's papermaking operations in Rothschild under a steam supply agreement. The project will result in a highly efficient use of biomass resources and Domtar mill's infrastructure while allowing Domtar to retire less efficient boilers, virtually eliminating its use of fossil fuels at the mill. The construction is expected to take 30 months for a startup by the end of the third quarter of 2013. Domtar is approximately 75% energy self-sufficient across its North American manufacturing footprint of 13 pulp and paper mills. The average Domtar pulp and paper facility draws approximately 87% of its thermal energy (energy required to make steam) from renewable fuels such as biomass and spent cooking liquor.
The photo below illustrates the $255 million biomass plant that will be built at Domtar's mill in Rothschild.
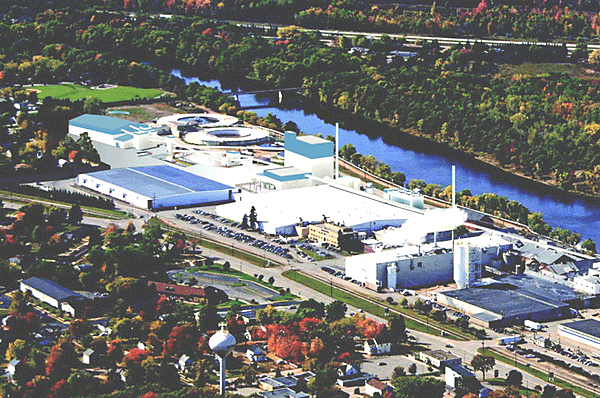
Back To Top
|
The Sustainable Forestry Initiative (SFI), Washington, D.C., USA, has awarded a total of $35,200 in grants to nine community-based projects to support forestry education activities and green building for low-income families. The projects are an extension of the SFI Conservation and Community Partnerships Grant Program, which has committed more than $1 million to date to help build knowledge, support landowner outreach, strengthen global supply chains, and deliver countless benefits in forests and communities across the U.S. and Canada. Partner contributions will leverage additional resources, raising the total value of the projects to $4.2 million.
In recognition of International Year of Forests 2011, SFI announced earlier this year it would award grants for smaller, community-based projects. Through the involvement of partners, the total value of the nine projects announced this week will be close to $100,000.
Dick Brinker, Dean Emeritus at Auburn University's School of Forestry and Wildlife Sciences and a member of the SFI Board of Directors, said the education projects are important for the future of North America's forests. "We need to actively reconnect our youth to the forest and outdoors if we want to conserve forests now and in the future," he said. "By supporting these projects, SFI and its partners are creating the responsible citizens and future resource professionals we will need to keep our forests strong and healthy."
The SFI-funded community projects include:
- The Chattahoochee Chapter Society of American Foresters will invite Boy and Girl Scouts in the Metropolitan Atlanta area to its Walk in the Forest Field Day where they can learn about the forestry profession and benefits of sustainable forestry
- The Evans Lake Forest Education Society will host a Forest Education Symposium for educators at its center in Squamish, B.C., Canada
- The Forest Foundation will arrange field trips for high school students and teachers in California to help them learn about sustainable forest management
- The Hardwood Forestry Fund will plant 23,000 hardwood seedlings on idle agricultural land in Wisconsin to maintain ecological and economic success of the forest
- Lauderdale County Habitat for Humanity will sponsor a Habitat home using SFI-certified products and certified to the ANSI National Green Building Standard
- The Mississippi SFI Implementation Committee will sponsor incentives for team competition in National FFA Association and 4-H forestry contests to promote awareness of sustainable forestry among students and their leaders, educators, and advisors
- The National 4-H Forestry Invitational will show youth how forests grow, the role forests play in their own lives, and how forests are managed to provide multiple benefits
- National Housing Endowment will receive funding to cover certification fees for 25 Habitat for Humanity homes to be green certified to the ANSI National Green Building Standard
- The Northwest Natural Resources Institute will show teachers how forest professionals manage lands as part of its annual Natural Resources Teacher Workshop in Washington State.
SFI created the Conservation and Community Partnerships Grant program in 2010 to build upon the more than $1.2 billion SFI program participants have contributed since 1995 for research activities, including forestry research, science, and technology. The SFI 2010-2014 Standard is based on 14 core principles that promote sustainable forest management, including measures to protect water quality, biodiversity, wildlife habitat, species at risk, and Forests with Exceptional Conservation Value, and encourages community involvement.
Back To Top
|
The latest listing of job openings in the TAPPI Career Center include management and process engineering positions, reflecting a growing need for experienced paper industry personnel in these areas. Current job openings in the TAPPI Career Center include:
Company |
Title |
Sonoco Products |
Company Manager - Primary Materials Technology |
Rayonier |
Manager, Chemical Byproducts |
Kimberly-Clark Corporation |
Engineering Technical Leader I/II |
Ashland Hercules Water Technologies |
Support Engineer - Sales |
GAF Materials Corporation |
Process Engineer - continuous process experience |
GAF |
Process Engineer - near Dallas, TX (Ennis) or Bakersfield, CA (Shafter) |
International Finance Corporation |
Senior/Principal Pulp and Paper Industry Specialist |
Jacobs Engineering |
Senior Process Engineer IV-Pulp and Paper |
Weidmann Electrical Technology Inc |
Process Engineer |
Presto Absorbent Products, Inc |
Electrical Engineer |
Signature Search |
Sales Engineer |
GL&V USA INC |
Product Manager, Refiners- North America |
More information about these jobs is available online.
Back To Top
|
2015 is the 100 year anniversary of TAPPI and an excellent time to celebrate the successes of this industry and the people and companies who have contributed to it. Our celebration will focus on the innovative discoveries and breakthroughs developed by academic and industrial research groups over the past 100 years. This will generate enthusiasm for the past as well as the creative future of the global pulp, paper, packaging, and converting industries.
As part of the anniversary we are developing a 100 year logo. Please take a look at the two logos below, and vote for "Yellow Ribbon logo" or "Big 100 logo" in the poll located at the end of the column to the right under the TCC Connects ad. Thank you!
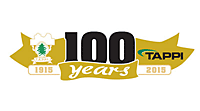
Yellow Ribbon logo |
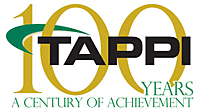
Big 100 logo |
Back To Top
|
Market Roundup
Total U.S. kraft paper shipments in May were 131,800 tons, an increase of 0.2% compared with May 2010, but up 1.5% compared with April 2011, according to the AF&PA (Washington, D.C., USA) May 2011 Kraft Paper Sector Report released this week. Total inventory was 72,600 tons.
Additional key findings from the report include:
- Total unbleached kraft shipments decreased over the same month of last year.
- Total bleached kraft shipments were up compared with May 2010.
Back To Top
|
Total U.S. boxboard production last month (May) decreased by 1.5% compared with May 2010, but increased 1.0% from April 2011, according to the AF&PA (Washington, D.C., USA) May 2011 U.S. Paperboard Report released this week.
Additional key findings in this report include:
- Unbleached kraft folding production increased over the same month last year, and increased over April 2011
- Solid bleached boxboard and linerboard production decreased from May 2010
- The production of recycled folding decreased compared with May 2010, but increased compared with April 2011
Inventory of solid bleached kraft paperboard fell in May.
Back To Top
|
The cost of manufacturing pulp has trended upward in most regions of the world the past two years, Wood Resources Quarterly ( WRQ), Seattle, Wash., USA, reports. Much of the increase has been the result of higher wood fiber costs, which, depending on pulp grade and region, currently vary between 48% and 72% of the total variable production costs, according to Fisher International, .
The cost of wood is the cost component that often decides a pulp mill's competitive advantage in the global market place. Wood fiber costs (in U.S. dollar terms) have gone up because of high demand due to strong pulp markets, tight supplies of sawmill residues, and a weakening U.S. dollar against most other currencies, WRQ explains. Global pulp markets have bucked the trend forecasted by many analysts a year ago, it adds.
Rather than the predicted retraction in market pulp prices this spring, prices stayed strong and actually increased to record-high levels of more than $1,000 per ton for softwood market pulp (NBSK) in the month of April. The Softwood Wood Fiber Price Index (SFPI) increased 1.9% in the first quarter this year, reaching $105.60/o.d. metric ton, the highest level since the third quarter of 2008, just before the financial crises.
The SFPI is a weighted average of delivered wood fiber prices for the pulp industry in all regions tracked by WRQ. These regions together account for 85% -90% of the world's wood-based pulp production capacity. The U.S. Northwest, Europe, Chile, Australia, and New Zealand markets saw the biggest softwood fiber price increases in the first quarter of this year, while there were only modest price changes in the U.S. South, Canada, and Brazil, WRQ notes.
The Hardwood Wood Fiber Price Index (HFPI) was also up 1.9% from the fourth quarter of 2010, and is now close to an all-time high of $110.33. Fiber prices were up in many of the same markets as those for softwood fiber, with the highest increases in Europe, Australia, and Chile, and only small upward prices adjustments in Canada and Russia, WRQ reports.
Hardwood fiber costs even declined in the U.S. South. Both the SFPI and HFPI were almost 20% higher than two years ago. During most of the past 23 years since the launching of the wood fiber indices in the WRQ in 1988, the softwood price index has been higher than the hardwood price. This relationship reversed in late 2008, and the hardwood price index is now 4.5% higher than the softwood price index.
More information is available online.
Back To Top
|
U.S. NBSK prices rose $20/metric ton to a record $1,040/mton in June. Mark Wilde, senior analyst with Deutsche Bank, asks "is this is the last leg upward for pulp prices?" Chinese demand is soft and spot prices are down as much as $100/metric ton, he notes. Reports suggest that local NBSK prices in China are ˜$60 - $70/metric ton below international levels. In Europe, NBSK prices could rise further, mainly due to the weak U.S. dollar. Meanwhile, sluggish paper demand and record pulp prices are forcing non-integrated mills to curtail/shutdown production, Wilde reports.
Back To Top
|
Will International Paper's bid for Temple-Inland table any effort to boost containerboard prices? Wilde also asks. "Possibly, but not probably," he answers, adding that the central focus remains industry fundamentals—supply and demand as well as cost factors. "Recent data suggests that the economy is slowing. Escalating input costs and lower box prices are pressuring margins. With margin pressures mounting, we continue to expect an increase attempt by late summer. However, we aren't assuming a successful implementation in our forecasts," Wilde says.
Back To Top
|
Domestic old corrugated container (OCC) prices rose $7/ton to $162/ton in June, Wilde reports. Key drivers are lower OCC generation in the U.S., strong export demand, and expectation of higher OCC demand from the startup of several new machines in China, he explains.
Back To Top
|
Pulp & Paper
Ahlstrom, Finland, this week reported that it will invest a total of EUR 7 million at its Stenay plant in France to be able to produce lower grammage grades, enhancing the quality of one-side coated papers for metalized labels and flexible packaging. The investment will play a key role in responding to the current market needs for low-grammage papers, according to Jan Lång, CEO and president of Ahlstrom. The project is scheduled to be completed in mid-2012.
"As a leading player, we have been continuously improving our offering in flexible packaging and metalized labels. In addition to addressing our customers' specific needs, this investment will also have a highly positive impact on the overall quality of the production output and performance characteristics at the customers' end, Lång noted.
The Stenay plant is part of Ahlstrom's Label and Processing Business Area, which operates a total of six production sites in France, Germany, Italy, and Brazil.
Back To Top
|
Boise Inc., Boise, Idaho, USA, and the Alabama Treasure Forest Association (ATFA) announced this week that private forestlands belonging to members of ATFA have earned Forest Management certification from the Forest Stewardship Council (FSC), a first for any forestlands in the state.
Boise collaborated with the ATFA and local landowners to apply for FSC certification of their managed forest lands. The company will now be able to purchase FSC certified fiber locally for use at its paper mill in Jackson, Ala.
"We are proud to be part of this historic moment in Alabama's forest history," said Thad Becton, Boise process improvement manager. "Sustainability is one of Boise's core values and this endeavor supports all three sustainability pillars—environmental, social, and economic—by supporting the local landowners and communities while continuing to purchase fiber from responsibly managed, certified forests."
Boise maintains a certification-neutral position and is active not only with FSC, but with the Sustainable Forestry Initiative (SFI) and the Programme for the Endorsement of Forest Certification (PEFC) as well as other sustainability organizations and initiatives.
In Alabama, private landowners manage 95% of the more than 23 million acres of the state's forests. "For the past 20 years, the ATFA and its members have been committed to responsible forest management practices and to educating all people, especially our children, about the many values society receives from well-managed privately owned family forest land," said James David Malone, executive director of the Alabama Treasure Forest Association. Malone added that the partnership between ATFA, Boise, and the National Wildlife Federation (NWF) that resulted in certification will allow ATFA to increase the educational outreach programs started with the NWF, and enable southern forest landowners that are or become members of ATFA to obtain a share of the market.
Back To Top
|
Canfor Pulp Innovation, the research and development division of Canfor Pulp Limited Partnership (CPLC), Vancouver, B.C., Canada, tomorrow (June 24) is conducting the opening of its new laboratory in Burnaby, B.C. During the ceremonies, CPLC will announce a major partnership with government and equipment suppliers for implementing breakthrough technologies at Canfor's mills. It also will announce a new university grants program for research collaborations with UBC and UNBC to complement its in-house activities in research and development.
The program begins at 11 a.m. with remarks by partners, ribbon cutting for the new lab, closing remarks, and lunch at noon. At tour of the new lab begins at 1 p.m. and the event closing is at 3 p.m.
CPLP is a global supplier of pulp and paper products with operations in the central interior of British Columbia. It owns and operates three mills in Prince George, B.C. which are among the lowest cost NBSK pulp producers in the industry. CPLP is the largest North American and third largest global producer of market NBSK Pulp and is the leading producer of fully bleached, high performance kraft paper. It employs some 1,200 people throughout the organization.
Back To Top
|
Catalyst Paper, Richmond, B.C., Canada, reports that it has achieved Forest Stewardship Council (FSC) controlled wood and chain-of-custody certifications at its three Canadian manufacturing operations. The company had already implemented FSC chain-of-custody at its recycle mill in Snowflake, Ariz., USA, as well as Programme for the Endorsement of Forest Certification (PEFC) chain-of-custody at its Canadian operations.
"Market demand for third-party verification that products come from well-managed forests is increasing," said Tom Crowley, SVP of sales and marketing. "This is the latest of many steps we've taken to ensure our paper products come with an excellent and credible environmental pedigree. FSC is well-known and well-regarded by many customers and we are now able to support this certification standard at all our mills."
Catalyst will include FSC certified products under its Sage product offer that combines fiber certification with carbon-neutral manufacturing and detailed mill-level environmental disclosure.
The new FSC certification applies to Catalyst's Crofton, Port Alberni and Powell River mills. Fiber supply comes mainly from sawmill waste (wood chips) from coastal British Columbia. Catalyst already receives some FSC-certified fiber at Port Alberni and is actively assessing potential additional sources of supply.
Catalyst can now apply the FSC controlled wood label to its Crofton pulp production, verifying that the fiber was harvested legally, with respect for traditional and civil rights, and does not come from genetically modified trees. Additionally, the FSC chain-of-custody enables Catalyst to label specific specialty printing papers as being made with fiber from FSC-certified forests.
The parallel Programme for the Endorsement of Forest Certification (PEFC) chain-of-custody systems will remain in place at Catalyst's Canadian mills to recognize fiber certified to two other widely recognized standards – Sustainable Forestry Initiative (SFI) and Canadian Standards Association (CSA).
Back To Top
|
Clearwater Paper Corp., Spokane, Wash., USA, this week celebrated the grand opening of its newest tissue facility at Shelby N.C., in Cleveland County. Gov. Bev Perdue, who has provided assistance to the project, was onsite to participate in the dedication.
"The dedication of this facility today ties back to one of Clearwater Paper's core business strategies—to focus on growing the consumer products segment of the company," said Gordon Jones, chairman, president and CEO of Clearwater Paper. "The fantastic level of support we have received from city, county and state officials in North Carolina has reinforced our decision to build this facility at Shelby."
Clearwater Paper has hired 100 local employees and expects to hire approximately 150 more workers before the project is completed. The project is expected to include seven converting lines capable of producing ultra-grades of private label tissue products and includes a Through-Air-Dried (TAD) paper machine, which is expected to be completed by the end of next year. The first two production lines have already started up at the site.
"Many critical commitments were made and fulfilled during this massive effort, demonstrating a great deal of dependability and integrity from all parties involved," said Vince Reese, Shelby plant manager. "But we are not done yet. Next comes our TAD paper machine, which will give us the ability to increase our premium and ultra tissue offering to better compete with nationally branded products."
When completed, the facility is expected to produce approximately 10 million cases of bathroom tissue and paper towels each year. The paper machine is expected to produce 70,000 tons annually.
Clearwater Paper manufactures consumer tissue, away-from-home tissue, hard roll tissue, machine glazed tissue, bleached paperboard, pulp, and wood products at 15 manufacturing locations in the U.S. and Canada. The company is a supplier of private label tissue to major retailers and wholesale distributors. This includes grocery, drug, mass merchants, and discount stores. The company has more than 3,800 employees.
Back To Top
|
International Paper, Memphis, Tenn., USA, has been named one of the Top 100 Best Places to Work in IT by IDG's Computerworld magazine, Framingham, Mass. IP was recognized as one of the Top 100 organizations that challenge its IT staff while providing great benefits and compensation. The company's ranking moved up 31 slots from 90th in 2010 to 59th in 2011. Honorees will be included in Computerworld's coverage along with results from the 18th annual Best Places to Work in IT survey.
"It's exciting that we've been recognized as one of the Best Places to Work in IT again this year," said John Balboni, SVP, CIO. "Our IT team members are committed to ensuring our daily operations are efficient and effective. They also play an integral role in helping our businesses and staff groups achieve their strategic direction."
IP's IT organization employs more than 1,200 IT professionals throughout its global operations. The group is responsible for designing, implementing, upgrading, and sustaining the information infrastructure, and systems that support and enable its worldwide operations.
"To be among the Best Places to Work in IT, it's not enough to seek out and hire the most talented IT professionals, offer them competitive pay, and provide great benefits," said Scot Finnie, editor in chief of Computerworld. "Smart IT people realize that they need to get up to speed on their employer's revenue opportunities. The organizations that made this year's Best Places to Work list are creating a work environment that both trains and encourages IT personnel to pursue business-driven priorities."
Back To Top
|
Kruger Inc., Montréal, Qué., Canada, reports that it will take market-related production shutdowns at its Trois-Rivières, Brompton, and Wayagamack mills in Québec beginning today (June 23) and extending to June 28. These shutdowns will allow the company to reduce the mills' total newsprint production by 9,000 metric tons and coated paper production by 4,000 metric tons.
Kruger produces publication papers, tissue, lumber and other wood products, corrugated cartons from recycled fibers, green and renewable energy, and wines and spirits. The company operates facilities in Quebec, Ontario, British Columbia, Newfoundland and Labrador, and the U.S.
Back To Top
|
Metsä Tissue, Espoo, Finland, part of the Metsäliitto Group, this week signed an agreement to become a licensed manufacturer and seller of Georgia-Pacific's Lotus® consumer tissue brand in Russia. In addition to the license contract, Metsä Tissue will purchase a selected portion of the finished goods stock of Lotus products in Russia. Metsä Tissue will then commence the production and sale of Lotus-brand products in Russia alongside its own consumer brands, Lambi and Mola. In 2010, Lotus consumer sales in Russia were around EUR 20 million.
With the agreement, G-P will refocus its Russian business on the away-from-home market. It will continue to manufacture, sell, and market its Lotus consumer brand throughout the rest of the EMEA region. The parties expect to close the deal at the end of the third quarter, after which Metsä Tissue will initiate Lotus brand production and sales to Russian customers.
The agreement strengthens Metsä Tissue's position in the Russian consumer tissue market, making it the second-biggest supplier in the branded category. "The deal is a natural progression of Metsä Tissue's commitment to developing our business in Russia", says Hannu Kottonen, CEO of Metsä Tissue.
Metsä Tissue entered the Russian market in 2004. Since then, the company has established two offices in the Moscow region and in 2008 launched consumer and away-from-home product converting operations in Naro Fominsk.
Back To Top
|
Mohawk Fine Papers Inc., Cohoes, N.Y., USA, has signed a non-binding letter of intent to buy the business of Bravo Solutions Inc., Elmira, N.Y. Bravo is a supplier of specialty synthetic and paper substrates for digital printing. The acquisition will include all brands and certain assets, including manufacturing capacity for converted products, which will remain in Elmira.
Bravo substrates are designed and engineered for both toner and wet-ink printing systems. Mohawk plans to fully integrate the Bravo portfolio, including pressure sensitive, synthetic substrates, integrated products, embedded card sheets, and magnetic materials into the existing Mohawk digital product offering, creating the most extensive portfolio of digital substrates in the world.
According to Thomas D. O'Connor Jr., Mohawk's chairman and CEO, "an acquisition of Bravo will be a strategic opportunity for Mohawk and its customers. We are committed to expanding our offerings to the growing digital print market. These premium substrates represent high value, high volume opportunities for printers, merchants and their customers."
Following the acquisition, Ray Mahar, founder of Bravo, will join Mohawk as director of Sales, Digital Specialty Substrates. In this new position, he will be responsible for business development and sales for both the current Bravo line and an expanded portfolio being developed by Mohawk. The companies are working together to agree on definitive purchase documentation as quickly as possible so as to smoothly transition sales of all products to Mohawk by early third quarter.
Back To Top
|
Norske Skog Saugbrugs AS, Halden, Norway, has started up another paper machine (PM 6) following an extensive fire in the mill's thermomechanical pulp plant in early February. SC magazine paper from PM 6 has already been delivered to customers. The company says it will startup its final machine (PM 5) next week.
"We are very pleased to see that the first deliveries of paper to pressrooms confirm that production is at the same quality level as before the fire," says Norske Skog's CEO Sven Ombudstvedt.
On February 2, fire caused damage to part of the TMP plant that supplies fiber to the paper machines at the Saugbrugs mill, stopping all production at the mill. Normal production was subsequently started at one paper machine (PM 4), which produces about 10,000 metric tons per month. PM 6 started up on June 8 and was in full production from week 24. PM 5 will start up on the June 27.
Norske Skog Saugbrugs has a production capacity of 545,000 metric tpy of SC magazine paper. It employs 550 people.
Back To Top
|
Visy's Tumut pulp and paper mill in New South Wales (NSW) Australia, this past weekend celebrated its 10th anniversary and the official opening of a stage two expansion at the mill. According to a report by The Daily Advertiser in NSW, some 3,500 people attended the opening and mill tour and heard Premier Barry O'Farrell open the expansion, which includes a new paper machine, new pulp production line, and an expanded wood yard.
Recalling his late father Richard's dream to build the world's most sustainable, modern, and efficient kraft paper mill, Anthony Pratt said he was "proud that stage two of the mill had earned Visy Tumut world-wide praise as a shining example of a sustainably managed mill with a low environmental footprint." It is also the biggest single investment on any one site that Visy has ever undertaken.
Visy's A$550 million expansion doubles production capacity at the Tumut mill and takes total investment in the project to almost A$1 billion, the biggest single investment on any one site that Visy has ever undertaken.
Pratt also announced during the opening that Visy planned to spend an initial A$100 million to build a 30 MW clean energy plant on the Tumut mill site. "I have a dream that in the not-too-distant future, Visy Tumut will spend around A$100 million to expand our clean energy generation here and take in additional waste forest wood to generate clean renewable energy and sell it into the power grid. An additional 30 MW clean energy plant here at Tumut would be another big step along the way towards my vision of making clean energy a whole new business division for Visy," Pratt said.
Pratt's plans for the clean energy plant at Tumut follow his commitment four years ago to invest A$1 billion in paper recycling and waste-to-energy infrastructure at a Clinton Global Initiative meeting in New York, N.Y., USA. The Tumut plant will be the second such plant in Australia and the Pratt family's third in the world.
Visy is building a similar plant at its Coolaroo manufacturing and recycling plant in Melbourne, Australia. Last year, Visy's U.S. associate, Pratt Industries, commissioned a $60 million (U.S. dollars) energy plant in Conyers, Ga., USA, that converts waste from its manufacturing into gas. The next Australian clean energy plant after Tumut is expected to be at Smithfield in Sydney's west. It is expected to cost between A$50 million and A$100 million.
Visy currently generates renewable energy from waste wood and other bi-products to help power the Tumut mill. Pratt noted that over the past decade, 1.2 million MW of energy had been generated from renewable sources at the mill, enough to power 160,000 homes in NSW for a year. In the 2009-10 financial year, the first to incorporate the upgrade, the mill's on-site renewable and co-generation system produced 73% of total energy and 42% of power for the plant.
The Tumut mill also generates 190,000 to 250,000 NSW greenhouse gas abatement certificates each year through renewable energy production and energy-efficient investments. "My vision for Visy Tumut is not only to keep our position as an example of world's sustainable manufacturing, but to build on it," Pratt said.
Back To Top
|
American Industrial Partners (AIP), New York, N.Y., USA, has agreed to acquire the worldwide hardwoods and industrial products business unit from Weyerhaeuser Co., Federal Way, Wash. The transaction is expected to close in August of this year. The future business will operate as Northwest Hardwoods Inc., headquartered in Tacoma, Wash., with operations in the U.S., Canada, China, Japan, and Hong Kong.
Northwest Hardwoods, with approximately 1,000 employees, manufactures hardwood lumber in North America. It sells 15 species of hardwood lumber, specializing in alder, oak, maple, cherry, walnut, ash, and hickory and operates through a network of seven primary sawmills, four concentration yards, four remanufacturing plants, and one merchandizing log yard, all in the U.S.
Back To Top
|
Weyerhaeuser Co., Federal Way, Wash., USA, this week launched Weyerhaeuser Solutions Inc. (WSI), a new subsidiary offering a full range of consulting and management services designed to help clients develop, manage, and commercialize forest assets.
WSI is a business composed of consulting experts with Weyerhaeuser operating experience and expertise. According to WSI, these experts can work with companies in industries such as energy, mining, forestry, and manufacturing that are interested in reducing their carbon footprint, sourcing bio-energy feedstocks, and managing landscapes for water supply and quality.
Ray Risco serves as president of the new subsidiary, reporting to Tom Gideon, EVP–Timberlands. Risco has more than two decades of experience operating international businesses in executive, general management, and financial roles. He has been a key player in Weyerhaeuser's international strategic development, mergers and acquisitions, partnership management, and operational leadership.
"With the ability to serve customers around the world, we can design, manage, and commercialize forest-based solutions to mitigate risk, diversify investment, and expand economic opportunity," Risco said. "We do this by taking a holistic approach to helping clients expand their portfolios to include renewable forest-based assets, and providing customized, innovative solutions, on a global scale, that enhance supply security and provide economic alternatives. Our experts can help customers to make informed choices, which we then help implement."
Services WSI provides include:
- Natural Resource Management. Site evaluation, land appraisal, financial analysis, active forest management, watershed and water-use strategies, and supply chain services for sustainable forest products
- Climate Change Strategy. Innovative carbon sequestration solutions
- Renewable Resources for Energy. Ecosystem services to remediate current operations and assistance in transitioning to renewable energy supplies.
Back To Top
|
Containerboard/Packaging
Ahlström Capital, Helsinki, Finland, and the Accent Equity, Stockholm, Sweden, investment fund are combining their operations in the packaging industry to form a new group to be known as Arch Packaging Group AB. The merger strengthens the competitiveness of the constituent companies, A&R Carton, a key European folding carton packaging company, and Flextrus, a leading flexible packaging provider in northern Europe, which will continue to operate in the market as separate companies and brands. The change is a step in the direction of a possible future IPO.
Arch Packaging will have an annual turnover of about EUR 500 million and 2,000 employees at 18 factories in 8 countries in Europe. The Group will be headquartered in Malmo, Sweden. A&R Carton's President and CEO Per Lundeen will be CEO, and Flextrus's CEO Per Nystrom will be deputy CEO.
Back To Top
|
Cartones America, Cali, Colombia, a privately-owned, Andean Region producer of containerboard, corrugated boxes, clay-coated paperboard, spiral tube board, and specialty board packaging products, has successfully started up PM 3 at its Cali mill following a major rebuild by the Italian company Toscotec. PM 3 produces test liner using recycled paper.
The goal of the rebuild was to reduce energy costs and improve paper machine efficiency, enabling it to increase production. This was accomplished by significantly increasing dryness of the web after the press section. This part of the machine can now reach a new maximum operating speed of 900 m/min.
Toscotec's scope of supply consisted of a new press section and the dryer section modification. The press design features an advanced Combi-press in first position, with a compact two nip solution, and a state of the art "TT Shoe-press" in second position. The existing drying section, containing 35 TT SD (Toscotec's steel dryer cylinders), is equipped with a new stabilizing system for improving machine runnability.
Cartones America traces its roots back to the 1950s in Cali. In recent years, the company has grown steadily, investing in operations in Venezuela (1993), Ecuador (1998), Peru (2000) and Chile (2006).
Back To Top
|
International Paper Co., Memphis, Tenn., USA, this week said it will indefinitely shutdown the No. 3 paper machine at its Valliant Mill in Oklahoma on November 1. This machine produces approximately 430,000 tpy of containerboard used to make corrugated packaging.
"The decision to shutdown this machine will enable us to match our production to our customer needs and limit our exposure to high fiber and other input costs in the area," said Carol Roberts, SVP of IP's Industrial Packaging business. "Nevertheless, this decision will impact very good, hardworking people, and we are taking steps to support them."
Approximately 60 jobs will be impacted at the mill as a result of the machine shutdown. The company will provide severance and outplacement assistance to affected employees.
Key grades produced on the No. 3 machine will be transitioned to other mills to meet customers' needs. Prior to the shutdown of Valliant PM 3, IP's North American containerboard production is about 11.5 million tpy.
Back To Top
|
Sonoco Recycling Inc., a wholly owned subsidiary of Sonoco, Hartsville, S.C., USA, and Shoosmith Brothers Inc., this past week opened The Recycling Center, a landfill diversion facility that will be operated by Sonoco Recycling at the Shoosmith Brothers landfill in Chester, Va. The center will handle mixed material loads for recycling.
With the new recycling facility, commercial and industrial customers will now be able to recycle unsorted and mixed loads that previously would have gone to landfills. The facility will sort and process items such as mixed paper, metal, and plastics. Reclaimed materials will be linked to other end users. Recovered paper, for instance, will go to Sonoco's Richmond paper mill only 12 miles away.
"This new recycling facility is one of the first to be constructed at a landfill with the primary mission of diverting waste destined for land disposal," said Jim Brown, VP, Sonoco Recycling. "We are capturing materials that previously held no value for customers and returning them to the manufacturing stream to make products that consumers use every day."
"Few facilities exist to accept unsorted industrial and commercial waste destined for landfills," said Fletcher Kelly, VP of Shoosmith Brothers. "By recovering and repurposing this waste to alternative end uses, we're not only generating additional revenue, but lengthening the life of our landfills."
The recycling facility, operated by Sonoco Recycling on behalf of Shoosmith Brothers, will serve commercial and industrial customers in the Greater Richmond area as well as regionally. As diversion efforts expand, the economic impact of the facility will be visible in various ways, including the ultimate creation of up to a 20% increase in new jobs.
Sonoco Recycling annually collects more than 3 million tons of old corrugated containers, various grades of paper, metals, and plastics. Currently, Sonoco Recycling operates three material recovery facilities (MRFs) serving more than 125 communities in which curbside-collected residential and commercial materials are processed.
Back To Top
|
Nonwovens
Buckeye Technologies Inc., Memphis, Tenn., USA, this week announced plans to close its Delta, B.C., Canada, airlaid nonwovens facility by the end of calendar 2012. The company says it will work closely with its customers to continue to meet their needs by sourcing products currently produced at Delta from its facilities in Gaston County, N.C., and Steinfurt, Germany.
Buckeye Chairman John B. Crowe said that "this closure has become necessary due to several factors including unfavorable site location relative to customers and raw material suppliers, a strong Canadian dollar, and low capacity utilization. It is unfortunate that this closure will result in the eventual termination of employment for approximately 95 dedicated employees. We have owned and operated the Delta facility since 1997 and we value and appreciate the many contributions of the organization over the past 14 years. In the fall of 2010, we consolidated our production from a two machine operation to one airlaid machine in an attempt to improve the profitability of the site. Even after this consolidation, which did improve margins, the plant's forecasted financial performance remains at an unacceptable level.
"We are making this announcement now to allow adequate time to address employee and customer needs. This 18-month period will allow us time to implement changes that may be needed at Gaston and Steinfurt to meet the needs of our current Delta customers. This closure and consolidation of business will improve capacity utilization, profitability and return on invested capital for our Nonwovens business. We expect to incur a non-cash asset impairment charge of about $15 million and $5 million in restructuring expenses between now and Dec. 31, 2012. The closure is expected to generate about $30 million in cash over the next 18 months, primarily through the sale of land and buildings and a net reduction in working capital. From now until the end of 2012, we will focus on meeting the needs of our customers and on maximizing cash flow generation at the site."
Back To Top
|
Published Pricing
DuPont Titanium Technologies. Wilmington, Del., USA, has announced a price increase of $0.25 per pound, or as permitted by contract, for all DuPont™ TiPure® titanium dioxide (TiO2) grades sold in North America (U.S. and Canada). The price increase becomes effective July 1.
DuPont Titanium Technologies operates plants at DeLisle, Miss.; New Johnsonville, Tenn.; Edge Moor, Del.; Altamira, Mexico; and Kuan Yin, Taiwan, all of which use the chloride manufacturing process. The company also operates a mine in Starke, Fla.
Back To Top
|
Energy
The Nature Conservancy (TNC), Arlington, Va., USA, and the Sustainable Forestry Initiative (SFI, Washington, D.C., this week launched a pilot project to help bioenergy companies in the U.S. support responsible forest management through their procurement of woody biomass. The joint effort reflects the recognition by both organizations that the bioenergy industry provides new market opportunities for forest landowners and managers, but that appropriate steps should be in place for the procurement of forest fiber in order to maintain the health of the forest resource.
The project will assist facilities that produce renewable energy or transportation fuels from woody biomass to establish a responsible procurement system. SFI's Fiber Sourcing requirements will be applied for the procurement system, and analysis will be conducted to identify gaps between existing procurement and SFI Fiber Sourcing requirements.
"Woody biomass can be a great source of renewable energy and offers an excellent incentive so landowners can maintain their forests as forest—as long as the forest is managed responsibly," said Glenn Prickett, chief external affairs officer for The Nature Conservancy. "TNC is interested in this project with SFI to explore how the SFI Standard's unique Fiber Sourcing requirements can address the need of responsible procurement of woody biomass for bioenergy facilities while managing for important forest values."
Through the SFI program's fiber sourcing requirements, all SFI program participants—whether they own or manage lands or buy fiber—must take measures to ensure the raw material in their supply chain is from responsible sources. Next steps for this project entail the identification of bioenergy facilities that can be project participants and will form the basis of our shared learning.
"Working with The Nature Conservancy and project partners will be a constructive undertaking to share and learn from our collective knowledge as it relates to responsible procurement. This initiative has the potential to demonstrate to policymakers that voluntary certification has an important role to play in demonstrating the viability of voluntary measures to address emerging issues related to a growing bioenergy market," said SFI President and CEO Kathy Abusow.
Back To Top
|
People
Boise Inc., Boise, Idaho, USA, announced that Jeff Lane resigned his position as SVP of the company's packaging operations effective yesterday (June 22). Lane is leaving the company to pursue an employment opportunity outside of the packaging industry. Robert A. Warren, COO for Boise, will assume responsibility for Boise's Packaging business effective immediately.
"We appreciate Jeff's leadership of our Packaging and Specialty businesses, and all of our businesses have benefited greatly from his leadership in the commercial arena," said Alexander Toeldte, CEO. "Most recently, he led the acquisition and integration of Tharco Packaging. I thank Jeff for all the contributions he made to Boise Inc. and wish him well in his future career."
Back To Top
|
KiOR Inc., Pasadena, Texas, USA, a cellulosic fuels producer, reports that former Secretary of State Condoleezza Rice has agreed to join its board of directors, starting in July.
Secretary Rice has a distinguished career in the public, private, and academic sectors. She served as U.S. Secretary of State from January 2005 to 2009 after serving as the Chief National Security Advisor to the President beginning in 2001. She is currently professor of political economy in the Stanford Graduate School of Business, senior fellow of public policy at the Hoover Institution, and professor of political science at Stanford University.
Secretary Rice also has served on the board of directors for the Chevron Corp., the Charles Schwab Corp., the Transamerica Corp., and the International Advisory Council of J.P. Morgan. She is currently on the board of Makena Capital, a private endowment firm, and C3, an energy software company.
Back To Top
|
Panther Systems, Vancouver, Wash., USA, has named Phil Farmer as its new CEO. Farmer joins Panther with 25 years of experience in the paper industry. He has held key leadership positions as GM and division VP at Caraustar, Atlanta, Ga., GM at RockTenn, Norcross, Ga., and most recently GM at Graphic Packaging International, Marietta, Ga.
Panther Systems provides quality control and automation systems and production management software for the global pulp, paper, and tissue industries.
Back To Top
|
TAPPI News
Nominations for the major TAPPI 2012 awards are due by August 1, 2011. The awards that may be presented in the upcoming year are:
- Gunnar Nicholson Gold Medal Award - The Association's highest technical honor may be presented annually to recognize an individual or individuals for preeminent scientific and engineering achievements of proven commercial benefit to the world's pulp, paper, board, and forest products industries and the other industries that TAPPI serves.
- Herman L. Joachim Distinguished Service Award - The Association's highest award for service, may be presented annually to recognize leadership and service which have significantly and demonstrably contributed to the advancement of the Association.
- Paul W. Magnabosco Outstanding Local Section Member Award – The highest honor for Local Sections may be presented annually to recognize an individual for outstanding leadership and exceptional service to one or more Local Sections, which have resulted in significant and demonstrable benefits to the Local Section members.
- TAPPI Fellow - TAPPI Fellows are Individuals who have been members of TAPPI for not less than 10 years prior to the nomination, and who have contributed meritorious service to the Association and/or the paper and related industries. Retiring members of the TAPPI Board of Directors become Fellows automatically at the end of their term.
TAPPI Awards and Honors shows the qualifications required and links to the nomination forms that must be completed. You may submit all nomination forms by email to standards@tappi.org, or you may fax them to the attention of the awards department at +1-770-446-6947, or send by mail to TAPPI, Awards Department, 15 Technology Parkway South, Norcross, GA 30092, USA.
Back To Top
|
The Lake States TAPPI North Central PIMA - Kick-Off Meeting will be held on Tuesday, August 23, 2011, at the Bull's Eye Country Club, 3320 Timber Valley Drive, Wisconsin Rapids, WI.
A morning shotgun, scramble golf outing is planned with dinner to follow. Prizes will be awarded and individual pin events will be held. Those submitting their registration with their fee, postmarked by August 9th, will be assigned holes on a 1st come, 1st serve basis. Later registrations will be assigned as space is available.
Foursome sponsors and all singles will be notified of their hole assignment via phone, fax or email. The scramble will have prizes and individual pin events. Check-in registration will be at the main entrance of the golf course club house. Golf clubs will be unloaded, tagged, and placed on golf carts for your assigned hole. Beverage carts will also be available throughout the day on a cash basis. Lunch will be provided at the turn, with the standard fine cuisine of brats, hamburgers, and beverage.
For registration details and complete details about this event
Back To Top
|
TAPPI is still accepting applications for the William L Cullison Scholarship . Scholarship funds are currently awarded in increments up to $4,000 per academic year for the last two years of a student's undergraduate program. The deadline has been extended to August 1, 2011. All candidates will be notified of their application status by September 1, 2011.
Potential candidates must meet all of the following eligibility criteria to be considered. It is important to note that financial need is not a requirement to be eligible.
• Major in a pulp and paper science course of study at a college or university. Many of these colleges and universities sponsor a TAPPI Student Chapter.
• Maintain a 3.5 grade point average or better (on a 4.0 scale) through the first two years in a four-year program, or first three years in a five-year program.
• Demonstrate outstanding leadership abilities.
• Demonstrate significant interest in the pulp and paper industry.
TAPPI's selection committee has created a new, expedited process for applicants to submit their application. It recognizes that while students are seeking additional ways to cover the cost of their education, they also appreciate electronic solutions to facilitate application submission. The committee is happy to oblige and the online process is fairly straightforward.
For further information and to apply go to Scholarship Information
Back To Top
|
Organised by Recycling Today Media and Pira International, Paper Recycling Conference Europe 2011 (PRCE) is designed to bring the supply and consuming sides of the industry together to create an active dialogue and generate trading opportunities. The conference will feature sessions touching upon trading/commercial activities, collection methods and recycling plant operations.
The programme will include:
- EU end-of-waste criteria for recovered paper: expected impact and the new opportunities
- trading views from all sides of the trading triangle
- challenges of decreasing fibre quality
- implications of generators' move to market their recovered paper directly
- a new Q& A session with a leading industry expert
The 2 day conference will be complemented by an exhibition and extensive networking opportunities with over 250 attendees. Find out more at www.paperrecyclingeurope.com
TAPPI Members are entitled for 20% discount. To claim, book online and use promo code: TM20D
Back To Top
|
William J. Whitsitt, a world expert on corrugated containers and corrugator runnability, passed away on May 28, 2011, at age 84. A Minnesota native, Bill joined the Institute of Paper Chemistry (IPC) in Appleton, WI, in 1948, upon receiving his BChE from the University of Minnesota that year. His over 40 year tenure at IPC was spent in all aspects of container research including boxboard and multiwall sack but with a major emphasis on corrugated containers. The latter included studies of material (liner and medium) and combined board properties and performance, as well as combined board and box manufacturing processes, in order to learn how material properties and manufacturing processes impacted box performance. Bill was internationally known for his work through his many publications, but he also conducted numerous confidential research projects for member companies.
An effective educator, he made frequent presentations at TAPPI Corrugated Container Conferences, taught a Corrugating Short Course at IPC and a course in Containers offered to IPC students. His friendly easy going manner coupled with his vast knowledge also made him a popular instructor in a number of other courses. He was always willing to share his knowledge with others. Bill joined Menasha Corporation in 1989 when IPC moved to Atlanta.
A TAPPI member since 1964, Bill was an active member of the Test Methods Review Board, and was named a TAPPI Fellow in 1991. He will be missed by his family and friends and the international corrugating community. A scientist to the end, Bill donated his body to science.
Back To Top
|
Mike Kocurek, Professor of Paper Science & Engineering at North Carolina University, will be again leading one of TAPPI"s more popular courses in Norcross (Atlanta), Georgia on August 8-9.
Past attendees of this course have agreed that the course format provides an excellent introduction to kraft pulp mill operations, and allows them to provide stronger input on operations after returning from the course.
After successfull completion of the course, participants should be able to:
- Describe and define kraft pulp mill processes, equipment, operating variables, and terminology, in order to increase ability to improve operations and pulp quality.
- Recognize how one part of the process affects other operations, in order to increase awareness of thinking on a mill wide scale.
- Interpret how the process variables affect pulp quality, in order to improve pulp quality and troubleshoot variations in quality.
- Extend awareness of the complex environmental challenges associated with kraft pulp production.
In addition, 13.3 continuing education credits are awarded upon completion of the course.
Learn more and register to attend
Back To Top
|
The TAPPI Tissue Properties & Manufacturing Course will be held in Atlanta on August 10-11.
The overall objective of this course, led by Mike Kocurek, Professor Emeritus of North Carolina State University, is to increase understanding of tissue performance properties and manufacturing. It is designed for participants who desire an intermediate level, comprehensive, and structured course on tissue properties, and the effect of manufacturing processes on product performance properties.
Completion of this course earns participants 14 CEU's.
To learn more and to register
Course topics will cover:
- Tissue properties & tests and how these relate to sheet structure
- Performance effects of fiber raw materials, pulp mill and recycling operations
- Stock prep refining for tissue
- Chemicals for tissue
- Tissue machine wet end operations & effects on sheet structure & properties
- multilayer headboxes, formation, fiber orientation, dewatering, and fabrics for sheet forming and sheet structure
- TAD and Yankee drying & effects on properties
- wet felts for obtaining desired sheet structure
- Creping, calendering, embossing
Back To Top
|
Lake States TAPPI/North Central PIMA held the Triple J Wing & Clay Spring Outing on April 5, 2011, at Triple J Sporting Clays. There were 72 shooters, the largest turnout ever for this event, and all had a great time. In addition to enjoying the shoot and network with other industry members the event raised over $4000.00 for our scholarship program.
The fall clay shoot is tentatively scheduled for Tuesday, September 20, 2011, at Triple J Sporting Clays. Be sure to mark your calendars as this is an excellent opportunity to meet with industry folks.
The Lake states TAPPI/ North Central PIMA Golf Outing will be held at Bull's Eye Country Club in Wisconsin Rapids on Tuesday, August 23, 2011. It will be a scramble event so put together your foursomes and join us for a great day of golf and help our scholarship program.
Back To Top
|
|
|
TAPPI Over the Wire | 15 Technology Pkwy. S. | Norcross, GA 30092 USA | Voice: 770.446.1400 | Fax: 770.446.6947
|
 |