Over the Wire
TAPPI
Weekly Spotlight
Buckeye Technologies Inc., Memphis, Tenn., USA, will be acquired by Georgia-Pacific, Atlanta, Ga., according to an announced agreement yesterday by the two companies. G-P will acquire all of the outstanding shares of Buckeye Technologies' common stock for $37.50 per share in cash. The transaction, subject to completion, is valued at approximately $1.5 billion, including debt.
Under the terms of the agreement, which has been unanimously approved by both companies' boards of directors, stockholders of Buckeye Technologies will receive $37.50 in cash per share, representing a premium of approximately 29% based on the average closing price of Buckeye Technologies' common stock over the last week.
Georgia-Pacific expects to launch a cash tender offer for all outstanding shares of Buckeye Technologies' common stock. The tender offer is subject to the expiration or termination of any waiting period under the Hart-Scott-Rodino Antitrust Improvements Act of 1976, as amended, other regulatory approvals, and other customary closing conditions, and requires at least 75% of the outstanding shares of Buckeye Technologies' common stock to be tendered, consistent with the threshold for approval of a merger specified in Buckeye Technologies' certificate of incorporation. The transaction is not conditioned on financing. In certain circumstances, the parties have agreed to complete the transaction through a merger, subject to receipt of stockholder approval.
Buckeye Technologies is a producer and marketer of specialty fibers and nonwoven materials made from wood and cotton. The company's manufacturing assets include a specialty pulp mill at Perry, Fla., cotton cellulose mills at Memphis and Lumberton, N.C., and mills producing nonwovens at Mt. Holly, N.C., and Steinfurt, Germany. Buckeye Technologies also has global sales offices in Beijing, the U.K., France, Italy, and Switzerland. The company has approximately 1,200 employees worldwide.
"This transaction enables our stockholders to realize significant value, while also representing an important next step in the growth of Buckeye Technologies," said John Crowe, chairman and CEO of Buckeye. "We are pleased that Georgia-Pacific recognizes the significant value of our company's special and unique assets, talented employees, and research and development capabilities. Georgia-Pacific's acquisition of Buckeye will provide our company and our employees with exciting future growth opportunities. We will continue to execute on our business plan in partnership with a committed new owner that has a long history of delivering superior business performance through its dedication to operational excellence and innovation."
Jim Hannan, CEO and president, Georgia-Pacific, noted that "Buckeye Technologies' competitive assets and capabilities strongly complement Georgia-Pacific's existing cellulose business and products. The talented employees, innovation capabilities, advanced technologies, and specialty fibers and nonwovens businesses of Buckeye Technologies will provide a significant platform for continued growth and success."
##SHARELINKS##
|
As TAPPI approaches its 100th year anniversary in just two short years, it seems perfectly fitting that during this year's National Volunteer Week (April 21 – 27) we celebrate all of our members who do, and have done, so many extraordinary things through service.
From Division Chairs and Committee Secretaries to our TAPPI Journal Editorial Board and Standards and TIPs Committee, the strength of our association throughout its 98 years has always been its members. One need only look at the long list of 50 and 75-year members on our website, or those who have received awards or other recognitions for their active involvement supporting and sustaining TAPPI, to realize that our success is most decidedly your success, too.
During this special week, I encourage each of you to log on to the Member Spotlight page on TAPPI's website and read about your fellow members, many of whom credit active involvement with jumpstarting their careers and providing them with the types of personal contacts and networking opportunities that might otherwise have taken a career lifetime to build. Or those Young Professionals who credit TAPPI members serving as mentors and sage advice givers for guiding them while they make their imprint as our industries' future leaders. Better yet, why not use the Questionnaire found on the same page and send us your recommendation for the next Spotlight candidate. These members are our true heroes, volunteers who provide the energy TAPPI has always run on – for nearly 100 years.
If you're looking for ways to enhance your career, extend your network, and contribute immeasurably to our industry, become an active volunteer today. Contact Mary Beth Cornell, membership and global development director, at mcornell@tappi.org, 770.209.7210. And, for all of those who already do, during this week and every week, we say:
Thank You!
##SHARELINKS##
|
The Forest Products Association of Canada (FPAC), Ottawa, Canada, has successfully used social media to recruit deserving students to work this summer at leading forest products companies. The Green Dream internship social media contest invited students to apply for four-month paid summer jobs by submitting a video application and soliciting online votes. FPAC set up the contest to better inform students about the growing career opportunities in the dynamic forest products sector and to highlight the launch of the GreenestWorkforce.ca, a portal that helps connect students and others to career opportunities in the sector.
Dana Aljanaby of Vancouver has been chosen from the winning candidates to receive a grand prize of $5,000 based on her video application and online support.
"Under our ambitious Vision2020, we have set the goal of recruiting at least 60,000 new employees by the end of the decade," says David Lindsay, president and CEO of FPAC. "We realize the need to explore new approaches including social media to attract high quality talent as we build the forest products industry of the future."
Lindsay said that the Green Dream internship contest was a huge success with about 16,500 votes cast during the contest, close to 180,000 page views on the GreenestWorkforce.ca website and 170,299 YouTube Views of the GreenestWorkforce videos.
All of the interns have also received an IPad mini and will be required to blog about their experience in the forest sector for the Greenestworkforce.ca website.
The chosen candidates are:
- Mark Pipher from Barrie, Ontario—engineering internship for West Fraser in Slave Lake, Alb.
- Patrick Pickard from Whitecourt, Alb.—technical support for Millar Western in Whitecourt
- Kyle Waterman from Havelock, Ont.—forestry assistant for Millar Western in Whitecourt
- Dana Aljanaby from Vancouver, B.C.—timberland forester for Weyerhaeuser in Grande Prairie, Alb.
- Jordan Auzam from Pickering, Ont.—engineer for Tembec in Temiscaming, Que.
- Andre Knight Lira of Ennismore Ont.—woodlands forestry for Daishowa-Marubeni International in Peace River, Alb.
- Jeremy Woo of Vernon B.C.—human resources intern for Tolko Industries in Vernon, B.C.
FPAC provides a voice for Canada's wood, pulp, and paper producers nationally and internationally in government, trade, and environmental affairs. The $57-billion-a-year forest products industry represents 2% of Canada's GDP and is one of Canada's largest employers.
##SHARELINKS##
|
Catalyst Paper, Richmond, B.C., Canada, this week announced that president and CEO Kevin J. Clarke will step down from his position later this spring. Clarke has advised Catalyst's board of directors that, with the company's recent financial restructuring successfully completed, the time is right for a leadership transition.
"Kevin steered Catalyst through a pivotal three years and the board of directors extends its appreciation to him," said Chairman Les Lederer. "Under his leadership, the company intensified its focus on stakeholder relationships which culminated in the rapid completion of a reorganization plan that significantly improved Catalyst's balance sheet and cost structure.
"His printing and publishing industry experience was also helpful in advancing product and market development objectives," Lederer said, "and served to put Catalyst on better footing to address the ongoing challenges of the fiercely competitive paper and pulp industry."
Clarke will continue in his role for an interim period through June 2013 to assist in a smooth transition. He plans to return to his home in New York State, where his family resides. A search for his successor is underway.
Catalyst Paper produces specialty mechanical printing papers, newsprint, and pulp. Its customers include retailers, publishers, and commercial printers in North America, Latin America, the Pacific Rim, and Europe. With three mills, located in British Columbia, Catalyst has a combined annual production capacity of 1.5 million metric tons.
##SHARELINKS##
|
The City of Guntersville, Ala., USA, has received the AF&PA (Washington, D.C., USA) 2013 Community Recycling Award. The award was presented at the Earth Day Concert at Guntersville Elementary School. The program stood out from the other applications for its variety of successful outreach efforts, including close collaboration between city agencies that increased public awareness and participation, as well as partnerships with local civic groups, churches, and state and federal government agencies.
"AF&PA is proud to present the City of Guntersville with this year's AF&PA Community Recycling Award. Guntersville's recycling program is particularly intriguing thanks to the breadth and depth of the paper recovery efforts currently in place," said Steve Klarman, RockTenn Recycling director of sales, who presented the award on behalf of AF&PA.
The award-winning City of Guntersville Recycling Program began in 1994 as an initiative to control the growth of its municipal landfill, reduce solid waste expenditures, and preserve its natural beauty. Continual improvements have helped achieve the current program, which provides curbside collection to residents and 275 commercial participants. Additional drop-off receptacles are located throughout the community at the recycling center, City Hall, city parks, and numerous churches. Thanks to their success within city limits, Guntersville has now extended recycling opportunities by collaborating with the Marshall County Commission to establish drop-off centers.
AF&PA recently announced that 65.1% of all paper consumed in the U.S. was recovered for recycling in 2012. Recycling programs such as Guntersville's, combined with the recycling efforts of millions of Americans each day, will help drive the industry toward its goal to exceed 70% paper recovery for recycling by 2020.
##SHARELINKS##
|
IT'S TISSUE, The Italian Technology Experience, will be held in Lucca, Italy, June 22 -30. It will be the first venue of this international event for industry operators and all of those who have an interest in the world of tissue. A rich and diverse program of meetings, information, in-depth analysis, as well as art, music, culture, and more, will provide a natural appendage to the uniquely Italian excellence in tissue.
IT'S TISSUE is not a trade fair, not a festival, nor is it a convention. It is a special event created by the Tissue Italy Network, made up of 12 Italian equipment suppliers for the tissue industry, which every three years will bring together clients and companies and provide them with a unique insight into each of the member companies' own technological innovations. The Open House formula will allow participants to immerge themselves into the Network's world of production starting in Lucca, Italy's most important tissue capital, through the packaging Valley in Bologna and Reggio Emilia, all the way to the northern city of Lecco. To analyze fundamental business aspects and global economic trends in tissue, a plenary Forum will become a meeting and debate table among the public and some of the greatest global experts in tissue who will be joined by the voices of renown economists of the same level, opinion leaders, and international journalists.
To make the event even more captivating and dynamic, IT's Tissue will offer cultural experiences to be held in the enchanting, historical center of Lucca, specifically organized for participants beginning with an exhibit of one of the greatest photographers of the Twentieth Century, Henri Cartier-Bresson, followed by the concert of a world famous pop star. Every night, in the Piazza Anfiteatro, international jazz artists will perform live. And what event would it be in the city of Puccini, without concerts dedicated to this grand composer: every day in the Basilica di San Giovanni participants will be able to attend recitals, a selection of operas, and special concerts.
This artistic experience will be completed with visits to the Paper Museum in Pescia as well as other museums in the province of Lucca, including those in the heart of the marble caves of Carrara to discover the secrets of Michelangelo and in the historical foundries of Pietrasanta where the world's greatest sculptors have worked and continue to work till this day. Itineraries will be dedicated to physical and internal wellness with the "white nights" at Spas, shopping at the outlets of the most well-known brands in Italian fashion, and wine and oil tastings in wineries and agriculture companies in the area.
IT's Tissue presents itself to the world as an opportunity that cannot be missed. The chance to surround oneself completely with Italian excellence in a location full of history where tradition and innovation are joined to become an ideal manuscript of synergy, unlike any other in its sector, organized by the Tissue Italy Network.
Tissue Italy Network member companies (in alphabetical order) are: A. Celli Paper S.p.A., Lucca; Elettric 80 S.p.A., Reggio Emilia; Fabio Perini S.p.A., Lucca; Futura S.p.A., Lucca; Gambini S.p.A., Lucca; MTC - Macchine Trasformazione Carta S.r.l., Lucca; Omet S.r.l., Lecco; PCMC S.p.A., Lucca; Pulsar S.r.l., Bologna; Recard S.p.A., Lucca; TMC – Tissue Machinery Company S.p.A., Bologna; and Toscotec S.p.A., Lucca.
##SHARELINKS##
|
Beginning this weekend, more than 1,500 paper and allied industry professionals will be in Atlanta, Ga., USA, for PaperCon 2013 to take advantage of a highly diverse program, networking events, sold-out exhibit, and educational opportunities that this special event has to offer. The preliminary attendee list is available online, and there is still time to register online.
The PaperCon Papermakers program provides everything needed to conduct paper machine performance evaluations, run mill trials, and acquire product certification. Other sessions focus on energy conservation, low consistency refining, and tutorials on pressing and drying.
Eight peer-reviewed TAPPI Coating sessions focus on scientific developments and practical tips. Highlights include opacity enhancement with titanium dioxide, and advancements in barrier coating. In addition, PaperCon is offering an Introduction to Traditional and Emerging Printing Technology Course just prior to the conference.
PIMA Management sessions at PaperCon provide excellent insight for mill mangers, production managers, and executives. This year's sessions will help attendees develop effective labor/management relationships and show them how to motivate today's employees.
The Tissue360° Forum provides a technical and markets overview program that, combined, provides exceptional insight into the global tissue and hygienic products arena unavailable anywhere else. The program focuses on fiber, water, and energy saving, the latest softness and strength additives, forming concepts, and unfolding developments in the worldwide marketplace. In addition, TAPPI is offering the Tissue Properties and Manufacturing Course, with an introductory-to-intermediate level curriculum.
The OpEx Reliability Workshop, being held for the third consecutive PaperCon event, explores the latest thinking and successes and failures in asset management strategies, operator driven reliability programs, alignment technologies, MRO inventorying and storeroom management, sealing solutions, and best practices in maintenance and reliability education and training approaches. This special one-day program also gives you full access to the PaperCon exhibit area.
The Young Professionals (YP) Program offers those new to the industry an excellent opportunity to gain basic industry knowledge and meet experienced industry leaders, while moving up the learning curve and expanding networks. CEUs are available for several sessions.
The RPTA P-T Seminar has in-depth information for attendees using recycled fiber and paperboard producers using cylinder machine technology. It also covers the latest on OCC supply and quality. This seminar is open to all PaperCon registrants, and RPTA members may register at the TAPPI member rate.
Co-located with PaperCon, the NETInc (Innovative Nonwovens Conference) is the only nonwovens conference developed by engineers and technologists to help bridge the gap between nonwovens science and commercial applications. It provides great synergies with the Tissue360° Forum, and is open to all full PaperCon registrants.
##SHARELINKS##
|
The TAPPI Yankee Dryer Safety and Reliability (YDS&R) Committee will hold its Spring Meeting May 1-2 at the Hyatt Regency in Downtown Atlanta, Ga., USA, during PaperCon 2013. Members and friends are cordially invited to attend this meeting, which is scheduled as follows:
- Work Group Meetings, Wednesday, May 1, Noon – 4:00 p.m.
- Full Committee Meeting, Thursday, May 2, 8:00 a.m. – Noon.
Attendees are asked to register online for these meetings so that we may get an accurate headcount. You may attend one time as a visitor, and thereafter, you must join TAPPI to participate in the committee. If your membership has lapsed, you may renew using the online registration link as well.
More information about the YDS&R committee also is available online, as is Hotel information.
Please email Scott Springmier with any questions, or contact him by phone at +1 404-375-0464.
We look forward to seeing you in Atlanta
##SHARELINKS##
|
The joint OpEx-RPTA session at PaperCon in Atlanta, Ga., USA, on April 30, is focused on two of the industry's latest approaches in the maintenance and reliability area—Operator Driver Reliability (ODR) and MRO storeroom inventory best practices. Beginning the session, Christer Idhammar with IDCON examines what has been tried with ODR, who's succeeded, what's failed, and why—all based on mill case study results. SKF's Dave Staples follows with a functional analysis of "Operator Driven Reliability: What Does Good Look Like and How Close Are You?"
Staples' presentation starts by visualizing the ideal ODR program based on best practices benchmarked globally. "Participants will learn how to perform a self assessment on an ODR program," he says. "Assessments are designed to identify gaps compared with best practices and make recommendations on how to close these gaps. Training will also offer realistic targets for an ODR program based on industry standard performance targets, corporate infrastructure, and maintenance sophistication."
In the session's third presentation, Jim Davis of PCA will examine the latest approaches to efficient storeroom management. His presentation on "Building the Perfect Storeroom" provides a close-up look at today's MRO inventory best practices.
More information about the OpEx Workshop program is available online.
##SHARELINKS##
|
Below is the latest listing of job openings in the TAPPI Career Center. The current listing includes job openings for a variety of positions including chief engineer, mill manager, production manager, piping designer, process engineer, basepaper project leader, pulp mill process engineer, and strategic capital and energy manager. Specific job openings at companies and locations in the TAPPI Career Center include:
Employer |
Title |
Location |
Albemarle Corp. |
Sr. Specialist/Advisor-Corrosion & Materials |
Baton Rouge, La. |
Boise Inc./Tharco |
Sales Representative |
Salt Lake City, Utah |
Canfor Pulp |
Manager, Strategic Capital and Energy |
Prince George, B.C. |
Crane |
Process Engineer |
Dalton, Mass. |
Cranston Machinery Co. |
Regional Sales Manager - Sales Engineer |
USA |
Fajar Paper |
Mill Manager |
Cikarang, Indonesia |
Fajar Paper |
Production Manager |
Cikarang, Indonesia |
Fajar Paper |
Chief Engineer |
Cikarang, Indonesia |
Robins & Morton |
Senior Pulp Mill Process Engineer |
Birmingham, Ala. |
Robins & Morton |
Senior Paper Machine Process Engineer |
Birmingham, Ala. |
Robins & Morton |
Piping Designer |
Morrisville, N.C. |
Sappi Fine Paper |
Basepaper Project Leader |
Westbrook, Maine |
More information about these jobs is available online
##SHARELINKS##
|
Market Roundup
U.S. sales of corrugated packaging board picked up in the first quarter of 2013 but are growing slowly, reflecting moderate and inconsistent demand for the consumer products that they contain, industry executives said in a report by MNI, New York, N.Y., USA. Corrugated producers in Texas, Wisconsin, and Philadelphia, Pa., in the MNI report said that orders are growing steadily, particularly from the food and beverage and pharmaceuticals industries, and that demand appears to be stronger than it was in the fourth quarter of 2012.
But one production measure of containerboard—the grades used for making corrugated—suggested volatile demand and uncertainty about the strength of the economic recovery, MNI pointed out.
"I would not say that we are seeing a strong upturn in orders," Jana Harris, president of Harris Packaging Corp., a maker of corrugated and folding-carton packaging in Fort Worth, Texas, was quoted in the MNI report. "We are not convinced that the economic recovery is well established. It is improving but not at a rate that would make us feel comfortable enough to say that it has turned around."
By early April, orders year-to-date were 4% greater than a year earlier, while the dollar value of sales was higher because of a recent price increase, Harris added. The company's biggest orders have come from the food and pharmaceutical industries while there has been a loss from manufacturers of durable goods such as technology and furniture, who have moved their operations overseas.
Most of the company's growth has come from acquiring new "brown box" customers and from more opportunities in retail display, rather than from existing customers, Harris noted. Meanwhile, the 100-employee company is losing some existing customers to lower-priced competitors. "Accounts that we have provided quality product and service and built a strong relationship with over many years are now going out for national bids," Harris said.
According to Scoring Boxes, a newsletter for the packaging industry, shipments of corrugated boxes rose an annual 0.7% in February, the latest month for which data are available. Year-to-date, MNI reported, shipments rose 0.4%, a rate that the publication said reflects moderate growth in the non-durable goods sector. "This steady growth rate is consistent with the slow growth in output of the nation's nondurable goods manufacturing operations which have increased output by 1.2% during the first two months of 2013," the report said.
But there are signs of volatility in demand for packaging, according to the report. It said the amount of containerboard that is not consumed by U.S. corrugators, exported, or held in inventories, was 95% higher in February than the seven-year average for that month. That followed volatile output in the "unidentified" containerboard production in January and December, suggesting customers still lack the confidence to place large orders on a sustained basis, the report said.
Mill inventories of containerboard reflect the same erratic pattern, increasing by 25% in February after declining by a similar margin in January.
At MarquipWardUnited, a Phillips, Wis.-based maker of machinery for the corrugated and folding carton industries, requests for quotes from packaging manufacturers rose 39% in March from February, according to Trish Kempkes, the company's director of global communications. Kempkes said the requests for quotes are likely a response to two new products that are being offered to meet manufacturers' demand for higher energy-efficiency.
In Fort Atkinson, Wis., overall sales at Wisconsin Packaging Corp. are flat so far this year despite increases of up to 12% to the food industry and around 5% to the furniture industry, said President Fred Negus. Orders from the manufacturing industry are strengthening modestly, he said. Still, that's an improvement from the fourth quarter of last year for the company that employs around 65 people and produced some 200 million square feet of packaging material in 2012, he said.
In Hatboro, Pa., a suburb of Philadelphia, Acme Corrugated Box Co. is seeing good growth in orders, continuing the trend of the last six or seven months, said President Bob Cohen in the MNI report.
##SHARELINKS##
|
Pulp & Paper
BillerudKorsnäs CEO Per Lindberg this week noted that at the end of the first quarter 2013, the integration of the two Sweden-based companies (Billerud and Korsnäs) is proceeding as planned. "The first full quarter as the new has come to an end and the integration of the two companies is progressing very well. We have therefore increased the target with SEK 200 million for our integration program to approximately SEK 530 million in synergies, savings, and increased efficiency.
"Non-recurring costs for realizing the synergies and savings will increase to approximately SEK 200 million, but are clearly justified given the expected savings. The sales process of PM 2 in Gävle is also progressing according to plan and we expect to be able to fulfill the requirements from EU concerning our acquisition of Korsnäs," Lindberg said.
The company's adjusted operating profit for the quarter of SEK 432 million is in line with expectations given the current environment, according to Lindberg. "The currency situation with a very strong Swedish krona is putting high pressure on our operating profit and the negative impact quarter on quarter is SEK 68 million. Given the strong krona, it is pleasing to see that the integration generates positive savings effects beyond our initial expectations."
The trading situation in the first quarter was somewhat slow but stable, Lindberg noted, pointing out that the market situation varied between the company's business areas, and while Packaging Paper faced a slightly slower than normal market, Consumer Board experienced a more satisfactory and normal market and the Containerboard's market was rebounding and strong. "Overall, we are still waiting for a European pick-up, and as a consequence increasing our sales efforts in emerging markets," Lindberg concluded.
BillerudKorsnäs is a fiber-based packaging paper producer. It has annual sales of some SEK 20 billion.
##SHARELINKS##
|
Unisource Worldwide, Norcross, Ga., USA, this week announced that it is engaged in exclusive talks with International Paper, Memphis, Tenn., regarding a proposed transaction in which its xpedx distribution business would be combined with Unisource. Unisource and xpedx are complementary business-to-business distributors of printing paper, packaging, and facility supplies.
The discussions were initiated after Unisource approached IP about the potential business combination, and on April 19 the parties entered into a non-binding letter of intent to explore a possible transaction. Unisource will continue doing business as usual until a proposed deal is closed. If no transaction is completed, Unisource will remain a private company. Combining the two businesses would enable an expanded geographic reach to important regions of the world, and further optimize and strengthen the supply chain, resulting in better customer service
Seth Meisel, a member of the Unisource Board of Directors and a managing director at Bain Capital, the majority owner of the company, said that "Unisource and xpedx serve their markets and customers well. A new company that unites their capabilities can create even more opportunities to deliver value and growth."
##SHARELINKS##
|
Packaging Dynamics Corp., Chicago, Ill., USA, a producer of flexible packaging and specialty papers, this week announced the signing of a definitive agreement to sell its Thilmany Papers business unit to a new company to be formed and controlled by investment funds sponsored by KPS Capital Partners.
Wausau Paper previously announced that it had signed a non-binding Letter of Intent to sell its Specialty Paper business to this new company being formed by KPS.
Following the closing of these transactions, the new company will include Thilmany Papers' Nicolet and Kaukauna mills and Wausau Paper's Mosinee and Rhinelander mills, all of which are located in Wisconsin, as well as the output of Verso Paper's number five paper machine in Jay, Maine.
Roger Prevot, CEO of Packaging Dynamics, said that "this is truly an extraordinary opportunity to contribute our Thilmany Papers business to form a larger specialty papers company that will deliver lasting value to customers, employees, and to the communities in which it operates, and for us to focus exclusively on our attractive downstream packaging and converting businesses."
Seth Hollander, a partner at Kohlberg & Company, said that "we are pleased that our efforts to transform Thilmany's mill operations and to build a world-class organization have positioned the paper business to make this next step in its evolution." Kohlberg & Company acquired Thilmany from International Paper and subsequently combined it with Packaging Dynamics. Hollander added that "we look forward to operating Packaging Dynamics as a focused leader in its food packaging and specialty laminations end markets and continuing to grow those businesses organically and through additional acquisitions."
Russ Wanke, VP and GM of Thilmany Papers, noted that "our team here at Thilmany is proud to be playing a critical role in the creation of a major new Wisconsin-based company. By combining Thilmany and Wausau's Specialty Paper Business, we and KPS are establishing one of the leading specialty paper companies in North America. We believe the combination will result in a company with the product breadth and customer reach to capitalize on the growing worldwide demand for specialty papers."
Closing of the Thilmany Papers transaction is conditioned upon the completion of the Wausau transaction, ratification of a new collective bargaining agreement between the new company and the United Steel Workers, required regulatory clearances, and certain other customary closing conditions. Packaging Dynamics expects to finalize the transaction in mid-year.
##SHARELINKS##
|
Papyrus, Gothenburg, Sweden, reports that it has finalized the divestment of its envelope production unit in Germany to the Mayer-Kuvert-network, as announced last month. With the divestment, Papyrus continues to pursue its strategic business decision to separate itself from envelope manufacturing and focus fully on its core business and the reinforcement of the company's position as a key paper merchant in Continental Europe.
Papyrus, with net sales of EUR 1,726 million in 2012, currently has operations in 22 countries across Europe and employs some 2,300 people.
##SHARELINKS##
|
SCA, Stockholm, Sweden, reports that in conjunction with its acquisition of Georgia-Pacific's (Atlanta, Ga., USA) European tissue operations during the summer of 2012, the EU Commission imposed requirements concerning the divestment of certain units within consumer tissue. The EU Commission has now approved the divestments.
Requirements imposed by the EU Commission included the sale of parts of G-P's former operations in the U.K., Ireland, and the Benelux countries, and certain operations in the Scandinavian region.
The branded business in the U.K., Ireland, and the Benelux countries is being sold to Sofidel. The production facility in Horwich, U.K., is included in this transaction. The retailer brand businesses in the U.K. and Ireland are being sold to Northwood and Wepa. The production facility in Bridgend, U.K., is included in this transaction.
Parts of the Nordic retailer brand business have been sold to Vajda Papir. The production facility in Drammen, Norway, is included in the transaction, together with a conversion line from the facility in Nokia, Finland.
These operations together represent total sales of about EUR 200 million and the combined purchase consideration is approximately EUR 100 million.
SCA produces personal care, tissue, and forest products. Sales are conducted in about 100 countries, and the company has some 36,000 employees.
##SHARELINKS##
|
Shandong Sun Paper, China, has ordered from Andritz, Graz, Austria, two tissue machines with steel yankees for the production of high quality facial and toilet paper. The machines will be installed at the Yanzhou mill, Shandong province.
The first ANDRITZ machine is scheduled to start up in May 2014 and the second at the beginning of 2015. With these orders, Shandong Sun Paper is entering the tissue business.
The new PrimeLineTM W8 tissue machines are designed for speeds of 2,000 m/min, with a paper width of 5.62 meters. Each machine will be equipped with a PrimeFlow two-layer headbox including dilution control, a PrimeDry Steel Yankee with a diameter of 18 ft., and a PrimeDry ReEvaporation HeatRecovery system. The scope of supply also includes a stock preparation plant and the automation system with DCS (distributed control system) and QCS (quality control system).
According to Ying Guangdong, VP and chief engineer of Shandong Sun Paper, this investment is part of an expansion program to become one of the five largest tissue producers in China within the next 10 years.
##SHARELINKS##
|
Stora Enso, Helsinki, Finland, this week reported that it plans to launch a streamlining and structure simplification project to achieve annual fixed cost savings of EUR 200 million, including the earlier announced EUR 30 million in the Building and Living Business Area, with the full impact starting from the second quarter of 2014. The project will include all business areas and corporate functions. In addition to reducing costs, the planned project would reduce interdependencies between businesses and enable a stronger focus on growth in value creating businesses.
"We plan to clearly and decisively further reduce our fixed costs to revenue ratio not only to adjust to the decline in market demand, but also to clearly add resilience against the cyclical and structural changes in our revenue. The reality is that our European driven printed media markets have shrunk more than 20% since 2008, and there is no reason to believe that the structural change of the past five years in Europe will slow down or change direction in the foreseeable future," said Stora Enso CEO Jouko Karvinen.
The company plans to change from four business areas to three divisions by integrating the current Building and Living Business Area with the Printing and Reading Business Area in a new division mainly focusing on mature businesses and geographies. The other two divisions would be the existing Renewable Packaging and Biomaterials Business Areas, which would remain as they are and concentrate on growth markets and businesses, as well as innovation.
The divisions and corporate functions would undergo organizational streamlining. Further outsourcing alternatives in group shared services and sale of non-core assets will be considered. As far as possible, the company plans to centralize functions in one location instead of several.
"The planned project is vitally important in supporting our transformation towards a value-creating renewable materials company focusing on growth markets. We start the plans from a position of relative strength and with a solid balance sheet and liquidity, thanks to our earlier actions. These plans, combined with our financial strength, will give us flexibility and agility to make future choices and achieve our strategy," Karvinen said.
The planned new division combining the current Building and Living Business Area with the Printing and Reading Business Area would be led by Karl-Henrik Sundström, currently CFO of Stora Enso. The company will immediately begin the process of recruiting a new CFO. The leadership of the two other divisions will remain as it is today, with Mats Nordlander heading Renewable Packaging and Juan Bueno heading Biomaterials.
The division structure plans become effective July 1, subject to the outcome of co-determination negotiations.
##SHARELINKS##
|
Yuen Foong Yu (YFY), China, has announced massive expansion plans for the next several years, investing more than $260 million in Taiwan and China. The company is planning to increase its paper machine fleet to double its current production capacity, reaching a total of 420,000 metric tpy.
PMP Group, Italy, has been selected a strategic partner for the project, having supported YFY's development with previous deliveries of three tissue machines for its YFY Beijng and Yangzhou mills. This time PMP will supply four new, complete Intelli-Tissue 1500 lines, providing 108,000 metric tpy of total capacity. Fa Tang, YFY's VP of Tissue, said that "we have decided to continue contracting with PMP Group because they have good skills and experience in tissue machine manufacturing."
Crescent former tissue machines, each with a 2.8 m width, an operating speed of 1,600 m/min, and a daily capacity of 75 metric tons, will be delivered to the mills located in China (Yangzhou and Dingfung). The machines will produce virgin fiber-based tissue in the basis weight range at the reel for 13-3 conversion into facial tissue, toilet rolls, and kitchen towels. The scope of supply includes stock preparation, the entire tissue machine (Intelli-Jet V headbox, Intelli-Former crescent former, a 16-ft. yankee dryer with a high efficiency steam hood, and an Intelli-Reel). It also includes auxiliary systems such as drives, lubrication system, steam and condensate, dust removal system, and controls and services. The machines will be launched one per quarter beginning in June 2014.
The main technological goals of the installations are focused on energy savings (low steam consumption), quality of the final product (due to application of special solutions in stock preparation, double lay, etc.), and production flexibility. For better financial effectiveness of the project, the deliveries are sourced from PMP Group facilities in Poland and guarantee Optimum Cost Solutions.
Currently, Yuen Foong Yu Paper brands, including Mayflower, Tender, and Delight, play a significant role in the premium tissue sector in China and Taiwan. Through production expansion, public relations efforts, and strengthening the branded products, YFY's goal is to be ranked in the top five producers in China.
##SHARELINKS##
|
Containerboard/Packaging
Metsä Board, Finland, has installed Tieto Corp.'s factory systems at five of its paperboard mills in Finland. The solution is based on Tieto's (Helsinki, Finland) TIPS (Tieto Integrated Paper Solution) system and covers production optimization and management, inventory management and interfaces with subcontractors, the sales system, and automation. The system also includes an interface with SAP Business Warehouse reporting. A similar delivery is currently in progress at the Metsä Board Zanders Gohrsmühle mill in Germany.
Metsä Board had already used TIPS products, but now the version has been updated and deployed at all five factories. In the future, the system will be updated with new versions every one to two years, which will extend its life cycle. The mills use one application, which results in savings and standardized operating models.
"We have built a system that enables us to develop shared best practices and facilitates goal setting and monitoring at the five mills. System maintenance and further development have become more efficient. A significant number of our personnel were involved in the project and many of our wishes became reality in the development of the application. The collaboration between our companies went well from my perspective: we stayed on schedule and within the budget, even though there were substantial changes in the project along the way," says Metsä Board's Matti Ketonen, VP, Supply Chain.
"TIPS is a comprehensive production control system for the pulp, paper, paperboard, and soft tissue industries. It uses modern information technology and advanced functionality to improve the efficiency and profitability of pulp and paper companies.
##SHARELINKS##
|
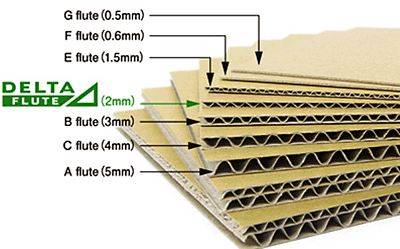 Rengo Co., Japan, this week announced that it has developed and will begin selling Delta Flute, "a new standard for corrugated board." The company notes that corrugated board is a type of architecture unto itself, adding that it has successfully created a product that is the further evolution of "less weight/less carbon" through the trinity of functionality, strong construction, and attractiveness—"the architectural design concepts that have been prized since the time of ancient Rome."
Based on the concept of "less is more," Delta Flute is a new innovation in corrugated board that creates great value with few resources, Rengo explains, pointing out that Delta Flute is a type of corrugated board with a thickness midway between B-flute, which has a thickness of approximately 3 mm and is used for purposes such as canned beer packaging, and E-flute, which has a thickness of approximately 1.5 mm and is used for purposes such as gift boxes. "This original product is a brand new standard that has never existed. Rengo will approach its users regarding conversion to this product as one effort to realize the widespread use of corrugated packaging that is more lightweight and more functional in order to further reduce impact on the environment," the company said.
Overview of Delta Flute corrugated board:
- Thickness = approximately 2 mm
- Number of flutes per 30 cm = 60 plus-or-minus 2
- Offers greater transportation and storage efficiency than B-flute, accomplishing the further optimization and streamlining of packaging
- Carbon dioxide emissions are reduced and impact on the environment is mitigated through further reduction of corrugated board weight
- Has greater flat crush strength than B-flute
- Because Delta Flute is stronger than E-flute, it can be used as outer corrugated packaging with the functions of inner boxes.
Production is scheduled to begin at all of Rengo's corrugated plants in Japan this spring.
##SHARELINKS##
|
Siam Kraft Industry Co. (former Thai Union Paper Industry Co.) has selected UMV as the supplier of a major coating section upgrade in their Wangsala mill PM9, located in Thailand. The 2.8 meter wide machine produces Coated Duplex board at a basis weight of 230 - 500 gsm.
The project is expected to improve production capacity and quality by replacing the Air knife in the pre-coating position with an INVO® Coater, utilizing the INVO Tip metering technology. The top coater will likewise be equipped with the INVO Tip technology. Other parts of the coating section will also be modernized..
With the startup of this project, planned for the fourth quarter of this year, UMV will have its first INVO Coater in Asia.
##SHARELINKS##
|
Sonoco, Hartsville, S.C., USA, reports that it has been awarded the primary packaging, retail display assembly, and fulfillment of a segment of battery products for Energizer brands, St. Louis, Mo. As part of a companywide plan to improve operations, Energizer and Sonoco will develop processes to streamline Energizer's Asheboro, N.C., battery packaging facility.
To achieve its productivity goals, Energizer awarded a portion of the primary and display packaging to Sonoco for battery stock keeping units (SKUs), defined as types that run on more manual, hand-packed lines. As part of its total solution approach, Sonoco will also manage the fulfillment process for Energizer on these specific SKUs.
"After a great deal of research and analysis, we found the most effective way to accomplish our packaging objectives was to work with Sonoco on a total solutions approach," said Chuck Marckwardt of Energizer. "We'll relocate the equipment to a Sonoco facility where they will manage a turnkey operation—handling the design, material procurement, packaging production, and distribution of all multiple SKUs. We felt that Sonoco could best provide this kind of support."
Jeffrey Tomaszewski, division VP and GM of Sonoco Display and Packaging, noted that "this turnkey service, provided at our Rural Hall, N.C., Display and Packaging facility, includes the design and sourcing of materials and packaging, the actual packaging of the batteries, and the deployment of finished goods to designated distribution centers and/or direct to customers on behalf of Energizer."
The scope of service includes providing a total solutions approach for more than 30 million primary packs covering more than 150 SKUs in packaging configurations, including blister cards, shrink wrapped trays, and carton products. In addition, Sonoco Display and Packaging will design, source, manufacture, pack, and ship thousands of retail displays annually. The first shipment was delivered in March, with complete ramp up of operations expected to occur through the second quarter.
##SHARELINKS##
|
New Products
When consumers need paper for a specific purpose like business reports, copies, or daily home printing, they can encounter a range of product specifications. To simplify the paper purchasing experience, Georgia-Pacific, Atlanta, Ga., USA, is re-launching its communication papers in three intuitive product categories—standard, premium, and super premium—with streamlined packaging that places the most important product information front and center and a simple color system for easy identification.
"Our research showed that consumers want their paper purchases to be quick and easy, but not at the sacrifice of high quality and good value," said Bob Hieronymus, senior category director, G-P Communication Papers. "To make the paper decision less complicated, we grouped our papers into three tiers that easily communicate product quality. We also created a new packaging design in vivid colors, with streamlined product information that consumers cite as most important in making a purchase decision."
G-P based the three product categories on a paper's weight, which consumers most readily equated with quality in the company's research. Within the three tiers, other quality and purpose refining options are available:
- Standard – Offered at a basic weight for one-sided documents like copies, drafts, and other daily needs, this multipurpose paper also comes in a bright option and a 30% recycled content option
- Premium –This inkjet and laser paper's extra thickness helps reports, flyers, and important documents look appealing and feel durable (a bright option also is available in this category)
- Super Premium – New to the G-P paper offering, this ink jet and laser paper is the thickest, brightest, and smoothest of the three paper categories for important presentations, resumes, and brochures.
For photographs, scrapbooking, invitations and other paper needs, the G-P portfolio has a line of specialty papers that also is offered in the new packaging. This category features standard and premium options for inkjet printed photos that include glossy, matte, and high gloss finished papers, as well as a card stock option.
More information is available online.
##SHARELINKS##
|
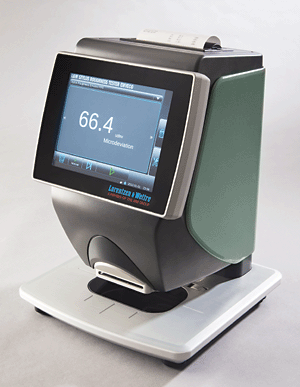 Lorentzen & Wettre, Stockholm, Sweden, a member of the ABB Group, has announced the L&W Stylus Roughness Tester Emveco—a paper laboratory instrument that measures the micro-surface roughness of paperboard and linerboard. The evaluated property is called microdeviation, which is a measure of the topography of the paper or board surface, and a characteristic that correlates well to how a paper or board will print.
This new product is a replacement of the Emveco Stylus Roughness Profiler System 210-R, used in the industry for many years.
All measurement and analysis is done inside the instrument, no extra software or computer is needed. The testing procedure is fully automated. A photocell detects the presence of sample. The reference head is automatically lowered against the sample to rest against the paper sample. The reference head moves at a constant speed relative to the sample and the stylus follows the contours of the surface. After a defined measuring distance, the reference head is lifted and moved back to the start position. The sample is then fed to next measuring position by the sample feeder. Each measurement takes less than 10 seconds.
The instrument is designed with attention to ergonomics and efficiency; easy to use color-touch screen with intuitive menus, and large easily accessible buttons, quick response, and high resolution. An integrated strip feeder facilitates extensive measurements, since each position can be measured at a fixed distance and continued until the strip ends. To speed up the strip measurement, the strip feeder can be set to measure more frequent at certain positions and less on others.
##SHARELINKS##
|
SCA, Philadelphia, Pa., USA, has introduced a new product portfolio making it easy for women to identify the best product for their needs based on their everyday activities. The new TENA lifestyle portfolio features new brand packaging and personal care pantiliners, pads, and underwear to fit the way women live. It offers ultra-thin protection from the unexpected leak in the following categories–Stylish, Active, and Anywhere. The products were selected and designed to offer high quality global incontinence care to women in North America, while making it easy for them to identify the best product for their needs based on their everyday activities.
"At SCA, we've spent years studying the needs of women in all stages of life who are experiencing light bladder leakage or what we refer to as the unexpected leak," said Robert W. Wilson, VP of consumer sales for SCA's Personal Care, North America. "One of our key findings was that the technological language used on incontinence product packaging, such as absorbency, is not as differentiating for consumers as it once was. Consumers are seeking a more intuitive approach to finding the products that will work for the occasions they face throughout the day."
Lizelle Valdecanas, brand director TENA, Personal Care-North America, noted that "TENA is innovating the way we talk to women who experience the unexpected leak. Through our new lifestyle portfolio and advertising campaign, we're helping to give women dealing with issues around incontinence the opportunity to live with a greater peace of mind and we're very proud of this."
The lifestyle portfolio, which includes two pantiliners and four pads that consumers can mix and match to suit their needs, consists of:
- Stylish pads that offer a sleek cotton design to provide protection without detection – whether sporting favorite jeans or a little black dress
- Active liners and pads that are created with an unsurpassed level of protection no matter what a consumer is doing. Its flexible cotton design is meant to move with the body–whether they're twisting to the tango or sprinting to a meeting
- Anywhere pads are created for day-to-day life; the soft cotton design fits any body and any lifestyle, whether stuck in traffic or stuck at the office.
"Over half of women experiencing the unexpected leak are not using proper protection, relying on feminine care rather than incontinence care products," said Wilson. "By creating the lifestyle portfolio, we are giving women a sense of liberation because TENA lifestyle products not only fit their lifestyles but also their unique needs. And once they give TENA personal care products a try, they love them.
More information is available online.
##SHARELINKS##
|
Brooks Instrument, Hatfiel, Pa., USA, a provider of advanced flow, pressure, vacuum, level, and vapor delivery solutions, has launched the MT3809 armored variable area (VA) flow meter, an instrument designed to perform effectively in extreme conditions in chemicals, petrochemicals, oil and gas, and LP gas applications.
The MT3809 provides flexibility to use a single flow meter regardless of application, process configuration, or flow rate. It works accurately across a vast range of operating temperatures, from 196ºC to 420ºC (-320ºF to 780ºF), and at pressures to 1,380 bar (20K psi). Even in demanding applications measuring gases, liquids, and steam, the MT3809 delivers 2% full-scale/1.6 VDI accuracy. The explosion-proof housing meets the most stringent hazardous-area classifications worldwide, and a flameproof option is available for IIC/Class 1 Division 1 locations.
More information about the new MT3809 is available online.
##SHARELINKS##
|
People
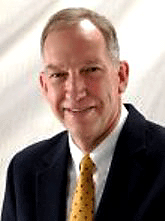 Port Townsend Paper Corp., Port Townsend, Wash., USA, has named Roger P. Hagan, long time member of PIMA and current PIMA executive council chair, its new president, effective May 1. Hagan, a 35-year veteran of the paper and packaging industry, will assume all financial, operational, and external communications responsibilities, according to Dale Stahl, the company's executive chairman to whom Hagan will report.
Roger Loney, who served as president since 2008, announced his resignation as president last month to return to the East Coast, and is remaining in Port Townsend to help Hagan with a "quick and seamless transition of company leadership," Stahl said.
Hagan has been working as VP, operations at Zilkha Biomass Energy/Fuels in Houston, Texas, for the past year. He has managed six different mills during his 35-year career, including RockTenn's Solvay mill in New York, the Hodge mill in Louisiana, and the Stevenson Mill in Alabama. He holds a B.S. degree in pulp and paper technology from the University of Washington, and a M.S. degree from the Institute of Paper Science and Technology in Atlanta, Ga.
Port Townsend Paper is owned by Port Townsend Holdings, which is owned and operated by GoldenTree Asset Management, a New York–based equity investment firm.
##SHARELINKS##
|
Women's Foodservice Forum (WFF), Orlando, Fla., USA, presented Georgia-Pacific EVP of Consumer Products Kathy Walters with its 2013 Leadership Award at the group's annual meeting this past week. As a senior executive leading the G-P Consumer Products Group, Walters oversees the largest retail and commercial tissue and tabletop businesses in North America spanning more than 70 locations and 13,000 employees.
Walters advances the culture of her organization through the company's Market Based Management Guiding Principles, appreciating the value of diversity and encouraging and practicing teamwork. She is actively involved in succession planning across each of the businesses under her leadership and ensures women and minorities are provided opportunities across Georgia-Pacific.
Each year the WFF Leadership Award is given to a female executive in the foodservice industry who shows exceptional leadership qualities within her company and the industry at large and whose professional growth and achievements are recognized through career advancement.
##SHARELINKS##
|
TAPPI News
In 2015, TAPPI will celebrate its one hundredth year. The TAPPI Centennial Celebration will be a multi-year series of outreach events and educational offerings showcasing the proud history and promising future of the global pulp, paper, packaging, and related industries. This once-in-a-lifetime event will expand public awareness, foster further connection, and provide outstanding opportunities for collaboration, growth, and investment in our future for all of those involved.
BUCKMAN has become the first company to support the Centennial Celebration at the $100,000 level. Kathy Buckman Gibson, chairman of the board, noted that "Buckman is delighted to celebrate TAPPI's 100th anniversary by being a Centurion Sponsor. Like so many others, we have benefitted from the many ways TAPPI has been an advocate for knowledge-sharing, innovation, and growth in the paper industry. We appreciate the opportunity to take a leadership position in encouraging others within the industry to support the Centennial, share our industry's story of sustainability, and forge the future of innovation."
Goals for the TAPPI Centennial Celebration are:
- To honor TAPPI's 100 years of connection, education, and advancement as a foundation for the sustainable success of our members, our industries, and the world we share
- To recognize the achievements of those who built our industry, and to inspire those who seek to build its future
- To celebrate the contributions and innovations of the global pulp, paper, and packaging industries to human culture, commerce, health, and social advancement
- To sustain the industry and support its growth, vitality and future through the TAPPI Foundation.
Lela Simpson Gerald, director of Global Marketing Communications, added that "the value we get from TAPPI has continued to grow over the course of our decades of working together. Leading the sponsorship campaign for TAPPI's 100th anniversary is our way of thanking them for all they've done in the past and to proactively help the world understand the role paper products will play in the future."
We invite you to be a part of this momentous event. The sooner you join us, the more opportunities there are for recognition of your company, its products, and key innovations. Keep in mind, an early commitment allows you to spread your investment over multiple years' budgets. For more information on the Centennial Celebration and sponsorship opportunities please visit our website or contact David Bell at dbell@tappi.org; 770-209-7209.
##SHARELINKS##
|
Space is still available for anyone interested in 18 holes before PaperCon festivities start in Atlanta, Ga.. This event will take place Sunday, April 28, 8:00 a.m. - 3:30 p.m. at the Bobby Jones Golf Course in Atlanta.
More information is available online.
##SHARELINKS##
|
Patrice Mangin, Professor at the University of Québec à Trois-Rivières, Department of Chemical Engineering's Chemical Research Centre on Lignocellulosic Materials (CRML), has been named winner of the 2013 TAPPI Research & Development Technical Award and the William H. Aiken Prize. The award recognizes outstanding accomplishments or contributions that have advanced the technology of the paper and related industries in the field of research and development.
"Dr. Mangin has had an outstanding career as general manager of international research and development institutes at CTP in France and CIPP in Canada," notes Dr. Dominique Lachenal, professor at Grenoble INP-Pagora, who nominated Dr. Mangin. "Despite his heavy responsibilities, Dr. Mangin continuously made extremely valuable contribution to science and technology through the supervision of graduate students, the presentation of conferences, and the writing of scientific papers."
Mangin, a TAPPI member since 1980, received his Ph.D. from the Institute National Polytechnique of Grenoble (INPG) in 1988. He is chairman ex-officio of PAPTAC, and a member of the AGENDA 2020 CTO Committee. Patrice coordinates the wood valuation and job creation program of his regional (Mauricie) forest products industries. In his 40-year career, he built the Integrated Pulp and Paper Centre of which he was general director until 2012. He was CEO of the French Centre Technique du Papier, scientific director of the Swedish Print Research program, held industry chairs both at UQTR and KTH (Stockholm), and worked 17 years at PAPRICAN.
Patrice participated in many research and development strategic planning sessions in Canada (Canadian Forest Innovation Council, Conseil de l'Industrie Forestière du Québec, and Senate Commissions), in the U.S. (Agenda 2020) and Europe (CEPI). As CEPI Research Group chairman, he coordinated the European forest products industry proposals to the 6th EU Research Framework Program. Author of more than 300 articles, he published in 2011 UNO year of the forest, the book "Once Upon a Forest" to celebrate forest as humanity's best hope for the future.
He is a TAPPI Fellow (2010) and received TAGA highest Award (M.H. Bruno) in 2009. The award is given for outstanding accomplishments or contributions that have advanced the technology of the paper and related industries in the field of research and development. The prize is funded by an endowment from the estate of William H. Aiken, TAPPI president in 1967-1968, and VP of technology for the former Union Camp Corp.
##SHARELINKS##
|
The only conference that focuses exclusively on renewable and sustainable nanomaterials, showcasing the latest applications and discoveries using cellulose, chitosan-derived, and other nanomaterials....
In its eighth year, TAPPI's 2013 International Conference on Nanotechnology for Renewable Materials to be held June 24-27 in Stockholm, Sweden, features the largest program to date, with more than 80 technical presentations.
KTH Royal Institute of Technology Campus - Stockholm, Sweden
Register by Monday, April 29, to receive the early bird rate. Reserve your hotel room by Monday, April 29, as well to receive the discounted room rate at the Elite Hotel Arcadia, the preferred conference hotel.
Your conference registration also includes a tour of either Innventia AB or the Wallenberg Wood Science Center beginning at 16:00 on Monday, June 24. Space is limited on both tours. Both will end by 18:30 so that you can attend the welcome reception. More details will be available soon, but allow for an early arrival time so you don't miss out.
This conference is your opportunity to learn about composite foams made with modified nanofibrillated cellulose from pulp mill waste streams, eco-friendly membranes, and high-strength, thin, and flexible films made from cellulose nanomaterials. Presentations also address material characterization, self-assembly behavior, rheology and processing of nanomaterials, novel medical applications, characterization techniques, and health and safety issues. A Standards Workshop is also scheduled to help advance the development of standards for cellulose nanomaterials.
With the two pre-conference tours, five keynote presentations, a poster session plus Student Poster Competition, it will be a packed three days in Stockholm. Register today, and see what solutions are available to support tomorrow's bioeconomy.
The 8th Annual International Conference on Nanotechnology for Renewable Materials is hosted by TAPPI's International Nanotechnology Division, which strives to collectively advance the responsible and sustainable production and use of renewable nanomaterials.
Learn more about the Nanotechnology Division.
##SHARELINKS##
|
TAPPI's 2013 Introduction to Wet End Chemistry Course provides in-depth training on paper machine wet end chemistry that will bring both mill technicians and suppliers up to speed on this key area of papermaking. The three-day course, to be held June 11-13, 2013 in Peachtree Corners (Metro Atlanta), Georgia, is the only course of its kind in the world.
"This course is ideal for engineers and other technical people who need a better understanding of wet end chemistry," notes Scott Springmier, Manager, Pulp and Paper for TAPPI. "The course not only covers the key technologies, chemical additives and terminology but it also delves into the use of papermaking additives to change paper properties, improve runnability and reduce costs."
The course is designed for anyone that is involved with wet end operations as well as anyone training staff working in this area. New engineers with a strong technical background but lacking papermaking process knowledge would also benefit. Instructors focus this 3-day interactive training on innovative wet end chemistry principals and the use of additives to change or create new paper products. Through case studies, break-out sessions and networking with others in the course, attendees will learn how to implement new technology to improve efficiency and product quality, reduce machine downtime and off-specification production, select and use of papermaking chemicals, and troubleshoot problems.
Topics covered include: basic water chemistry, fibers and fines, starch, dry and wet strength agents, alum chemistry, rosin sizing, synthetic sizes, dyes, fillers, retention systems and deposit and pitch control. The impact of recent regulatory developments and how changes in fiber quality are impacting wet end operations are also reviewed.
The three course instructors are respected experts in wet end chemistry. Martin A. Hubbe, Ph.D., is Professor, Department of Forest Biomaterials, North Carolina State University. He began his career with American Cyanamid before joining International Paper Company as a research associate and later principal scientist. Larry Anker, Ph.D., is Sizing and Wet Strength Applications Group Leader for Ashland Hercules Water Technologies. He earned a B.S. in Chemistry, Mathematics and Physics from Washington and Lee University and Ph.D. in Chemistry at Penn State University. Przem Pruszynski, Ph.D., is Global Technical Specialist for Nalco. He holds an M.S. in Analytical Chemistry and Ph.D. in Physical Organic Chemistry from University of Poznan, Poland, where he taught for 12 years. He's authored nearly 100 papers, holds several patents and has taught numerous technical courses.
##SHARELINKS##
|
2013 NCSU Alumni and Friends Golf Tournament
Register Today!
Date: Friday, April 26, 2013
Location: NC State's Lonnie Poole Golf Course
Format: Four Person Superball
Cost: $100 per player
(Fee includes golf cart, range balls, lunch, refreshments, tee gift and a PGA Golf Management student as a personal forecaddie for your group)
AM Round Times
Check-in - 7am; Shotgun Start - 8 a.m
.PM Round Times
Check-in - 12pm; Shotgun Start - 1:30 p.m.
Proceeds support scholarships and other enrichment activities for students.
Sponsored by NC State Natural Resources Foundation Inc.
##SHARELINKS##
|
Fact: the current economy has affected many schools' endowment funds, resulting in decreased support of student scholarships.
But here's the good news: TAPPI has a scholarship to offer. You have a chance to apply for some green (funds to pay tuition, etc.) to fund a satisfying green career. The Cullison scholarship is available for graduate and undergraduate students with an interest in the pulp, paper, converting, and packaging industries.
William L. Cullison Memorial Scholarship.
What this message means to you:
- If you're a student, here is a great way to apply for financial assistance for the 2013-2014 school year.
- The deadline for the Cullison scholarship is May 1, 2013. Mark your calendar now to allow yourself time to create an application that reflects the hard work you've been investing in your career.
- If you are affiliated with a college or university, share this with your students or other staffers who work with students. They will be glad you did!
- If you're in the industry, perhaps you know of students worthy of scholarship assistance with their education, please pass this information along.
##SHARELINKS##
|
It's time to tighten up plans to attend the Total Pump Training course being held at the TAPPI Training Facility in metro Atlanta, Ga., USA, for three days, May 1-3, 2013. This is an invaluable course for anyone in the pump and piping system industries.
The Total Pump Training course offers a comprehensive look at common pump applications and is taught by a recognized industry expert who can answer any questions about how system changes can alter pump operation and the best way to respond to system modifications.
Learn the important fundamentals of pumps, about positive displacement pumps, hydraulics selection and curves, advanced hydraulics considerations, sealing systems, installation, troubleshooting, repair, and more.
Earn 2.0 CEUs or 20 Professional Development hours, and carry back with you two indispensable manuals and even greater confidence.
Register online before seats fill.
##SHARELINKS##
|
Early Bird Registration rates for this course have been extended to May 1. Register today to save over $650 off the normal registration rate. Don't miss the best educational and learning opportunity of the year - the 2013 TAPPI Corrugated Press Hands-on Maintenance Workshop, May 7-8, at the Global Equipment USA Warehouse in Skokie, Ill., USA.
This unique course offers both classroom and indispensable hands-on maintenance training for corrugated industry plant managers and supervisors, engineers, maintenance teams, and machine operators.
Over the course of two days, you will learn from our team of instructors led by course chair Tom Pearce, Pearce Corrugated Consulting, and actively participate in more than eight hours of hands-on training.
Students will acquire practical knowledge and experience while conducting maintenance procedures on the facility floor, and interact with real-world machinery. You will be able to view first-hand the solutions to common problems and techniques to improve quality, efficiency, and reduce future downtime at your plant.
Because the attendance will be limited to the first 18 people that register, you will have ample time to have your individual and specific questions answered by our instructors. You could pour over all of the how-to manuals available and still not retain this level and quality of working knowledge.
After successfully completing this course, participants should be able to:
- Learn to use the basic tools to mechanically audit and troubleshoot a press
- Learn press audit procedures for process centering, better quality products, and increased productivity
- Attendees will understand presentation anilox roll selection, Press "fingerprinting", inks & substrates, quality defects & cause(s).
To learn more about this course and why you should attend, go the course website.
##SHARELINKS##
|
The popular Paper Machine Operations Course is returning to the TAPPI Training Facility on May 21-23, 2013. This course has proven to be one of the best ways to get a good overview of paper mill operations.
Led by Jim Atkins and a team of instructors, this course will provide participants with an improved understanding of the overall paper machine operation. Fundamental understanding of fiber properties and the way the mechanical components function on the paper machine will give the participant the tools needed to more quickly troubleshoot operational problems and improve paper machine operations and product quality.
Go to the course website to learn more and to reserve your space in this upcoming course.
This course in NOT intended for employees of tissue companies. Those interested in learning about tissue may be more interested in the TAPPI Tissue Runnability Course.
##SHARELINKS##
|
To provide additional value for TAPPI members, the Nanotechnology Division has launched a Webinar Series. This series will feature webinars from experts in nanocellulose and nanomaterials from around the world.
Join us on May 10 at 11:00 AM EST for a broad overview on cellulose nanomaterials. Nanotechnology Division Chair Sean Ireland, Manager, New Technologies and Market Ventures for Verso Paper Corp. will give a webinar titled "Cellulose Nanomaterials - A Transformative Opportunity for the Forest Products Industry." There is no charge to join the webinar.
Register today.
##SHARELINKS##
|
The 14th TAPPI European PLACE Conference, May 6-8 in Dresden, Germany, is your opportunity to connect with the global flexible packaging industry. This is your opportunity to interact with others looking to embrace raw material and hardware suppliers, regulatory experts, and trend setting technology leaders from the converting industry, universities, and end-users.
In addition to its robust technical program, the European PLACE Conference includes numerous networking opportunities including coffee breaks and lunches, a Table Top Walk, and an evening event at the famous Watzke Ball & Brauhaus.
Download the Brochure.
##SHARELINKS##
|
Register by May 11 to save for one of the 25 seats in the popular TAPPI Introduction to Wet End Chemistry course.
Three industry-known instructors are focusing the three-day curriculum, June 11-13, 2013, on innovative wet end chemistry principals and foundations designed to help you reach higher yield, improve confidence in the use of papermaking chemicals, and to better troubleshoot.
View the Workshop Schedule to see the specific topics covered.
This introductory- to intermediate-level course is designed for those in pulp and paper manufacturing facilities with job responsibilities, such as chemical and process engineers, mill superintendents, research and development engineers, technology and chief chemists, R&D vice presidents, process and quality control technicians, and suppliers involved with the wet end processes.
##SHARELINKS##
|
The launch of this successful conference series, produced by the Recycling Today and Smithers Pira, in co-operation with China TAPI, into Asia provides a unique opportunity for companies in North America, Europe, and the rest of the world to meet buyers in the Asian market.
The full program for Paper Recycling Conference Asia launching on May 30-31, 2013, has been announced. Highlights include the opening keynote address - The role of recyclables in China's Economic Resurgence, presented by Professor Wang, Ministry of Environmental Protection, China; An Overview of Macro-Economic Trends Impacting Asia's Recovered Paper Industry from Sally Sun, Deloitte China, and an exclusive One-on-One Interview with Ross Li, Lee & Man.
Save 20% on a ticket to attend by using the code CD20TAP!
Attendees will hear from other key speakers on the agenda, including; Randy Kim, Ekman Recycling; Henri Vermeulen, Smurfit Kappa Group; Niu Qingmin, Jiangsu Paper Association; Yoshimitsu Tanaka, Kaneko, and more, on recovered paper supply, infrastructure, and quality issues and challenges.
"We're excited about launching a Paper Recycling Conference in Asia, particularly as Asian demand continues to represent the major growth area for recovered paper. Since this inaugural event replicates the design of our existing events' list to attract merchants, brokers, suppliers of recovered fiber, and mills from around the globe, it's sure to represent a unique and powerful opportunity for the world's suppliers and consumers of recovered paper to meet," Jim Keefe, EVP and group publisher, Recycling Today, said.
More information about the inaugural Paper Recycling Conference is available online.
##SHARELINKS##
|
Nominations for the major TAPPI 2014 awards are due by August 1, 2013. The awards that may be presented in the upcoming year are:
Gunnar Nicholson Gold Medal Award - The Association's highest technical honor may be presented annually to recognize an individual or individuals for preeminent scientific and engineering achievements of proven commercial benefit to the world's pulp, paper, board, and forest products industries and the other industries that TAPPI serves.
Herman L. Joachim Distinguished Service Award - The Association's highest award for service may be presented annually to recognize leadership and service that have significantly and demonstrably contributed to the advancement of the Association.
Paul W. Magnabosco Outstanding Local Section Member Award - The highest honor for Local Sections may be presented annually to recognize an individual for outstanding leadership and exceptional service to one or more Local Sections, which have resulted in significant and demonstrable benefits to the Local Section members.
TAPPI Fellow - TAPPI Fellows are individuals who have been members of TAPPI for not less than 10 years prior to the nomination, and who have contributed meritorious service to the Association and/or the paper and related industries. Retiring members of the TAPPI Board of Directors become Fellows automatically at the end of their term.
The TAPPI Awards and Honors page has links to these awards that will show the qualifications required and links to the nomination forms that must be completed. You may submit all nomination forms by email to standards@tappi.org, or you may fax them to the attention of the awards department at +1-770-446-6947, or send them by mail to TAPPI, Awards Department, 15 Technology Parkway South, Peachtree Corners, GA 30092, USA.
##SHARELINKS##
|
The TAPPI Centennial Celebration will be a multi-year long series of outreach events and educational offerings showcasing the proud history and promising future of the global pulp, paper, packaging, and related industries. This once-in-a-lifetime event will expand public awareness, foster further connection, and provide outstanding opportunities for collaboration, growth, and investment in our future for all of those involved. Goals for the TAPPI Centennial Celebration are:
- To honor TAPPI's 100 years of connection, education, and advancement as a foundation for the sustainable success of our members, our industries, and the world we share
- To recognize the achievements of those who built our industry and to inspire those who seek to build its future
- To celebrate the contributions and innovations of the global pulp, paper, and packaging industries to human culture, commerce, health, and social advancement
- To sustain the industry and support its growth, vitality, and future through the TAPPI Foundation.
We invite you to be a part of this momentous event. The sooner you join us the more opportunities there are for recognition of your company, its products, and key innovations. Keep in mind that an early commitment allows you to spread your investment over multiple years' budgets.
For more information on sponsorship and volunteer opportunities please contact dbell@tappi.org.
The sponsorship prospectus can be downloaded online.
##SHARELINKS##
|
Member Mike Haas is a strong proponent of education and considers his long association with TAPPI to be a key ingredient in a successful career. He says that TAPPI has always served as a "fantastic learning resource" that has consistently offered him opportunities to hone leadership skills.
But it is not just the opportunity to engage in scientific and scholarly pursuits through TAPPI that Mike says brings great personal and professional rewards. It is the chance to mentor and serve as an advocate for future leaders in the industry, and it is for this reason that he urges fellow professionals to support the pulp and paper schools in their areas. "Get involved, serve as a mentor, create excitement about careers in our industry," he says.
Mike knows personally of what he speaks. As a young student at Miami University, he says he learned first-hand "how rewarding and fun TAPPI membership could be." It was the encouragement of TAPPI members like Fellow Dick Elliott that convinced him joining TAPPI was an important cog in the wheel of professional success. He presented his first TAPPI paper at a pulping conference in Toronto and there was no looking back.
Find out more by reading this month's Member Spotlight.
Spotlight participants are recommended by fellow members and staff. If you would like to nominate a member, just send his or her name (or names) to MemberSpotlight@tappi.org. We will forward a Spotlight Questionnaire to fill out and return.
We look forward to seeing you in the Spotlight!
##SHARELINKS##
|
The packaging industry continually seeks innovative solutions to make their products more sustainable and, at the same time, cost-effective. Further, the Consumer Packaged Goods companies seek to deliver enhanced consumer experience through improved package performance, which may be achieved through improved material properties. Cellulose nanofibers, cast as composite films, provide excellent barrier to oxygen and water vapor.
At TAPPI's upcoming International Conference on Nanotechnology for Renewable Materials this June, researchers from around the world will share their latest findings on the use of cellulose-derived nanomaterials to improve functional properties, targeted for packaging applications. Dr. Tamal Ghosh of PepsiCo's Corporate Research (Beverage Packaging), USA, will host a packaging-focused session on Wednesday, June 26.
The Packaging Session showcases three presentations focused on food and beverage packaging applications. A team of researchers from Switzerland will present their work on composite films with layered silicates and nanofibrillated cellulose. Their results will show a 30-fold lower water vapor permeability and 5-fold higher E-modulus compared with commercial base paper. Researchers from Hungary will discuss their work on improved barrier properties of a poly lactic acid (PLA) bottle coated with an invisible layer of cellulose nanocrystalline-chitosan material. An international team of researchers will discuss the promise of fungal chitin as a nanomaterial for the future.
The 8th Annual International Conference on Nanotechnology for Renewable Materials is scheduled for June 24 -27, 2013, in Stockholm, Sweden, at KTH Royal Institute of Stockholm. New reports will present some exciting advances for both within the pulp and paper industry and beyond. The technical program features cellulose nanomaterials in a variety of applications, including:
- Unique and Thin-Film Composites
- Filler and Coating Applications for Different Paper Grades
- Improved Barrier Properties for Packaging Applications
- Cellulose Nanomaterials as Films and Carriers in Medical Applications
- Nanopaper and Iridescent Colored Cellulose Films.
With more than 80 technical presentations, five keynote presentations, and 50 poster presentations, this year's conference is packed with the latest applications of renewable nanomaterials. Watch for additional updates from TAPPI on how nanotechnology, and cellulose nanomaterials, in particular, can be a transformative technology for the pulp and paper industry.
The 8th Annual International Conference on Nanotechnology for Renewable Materials is hosted by TAPPI's International Nanotechnology Division, which strives to collectively advance the responsible and sustainable production and use of renewable nanomaterials.
More information is available online.
##SHARELINKS##
|
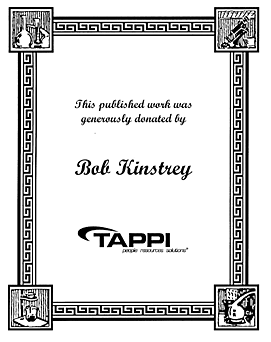
Do you have a history book gathering dust on your shelf? TAPPI's 100th year is coming soon and we are looking for donations to the TAPPI Library. Specifically, we are interested in histories of companies and mills in the paper and packaging industry (both producers and suppliers). Each donated book will have a bookplate in the front cover recognizing the donor. For more information please contact David Bell.
Please send books to:
c\o David Bell
TAPPI
15 Technology Parkway, South
Suite 115
Peachtree Corners, Georgia 30092
##SHARELINKS##
|
The existence of cellulose nanocrystals and cellulose nanofibrils has been known for several decades, yet recent advances in science, particularly in the field of nanotechnology, have revealed that these materials contain unique physical properties, particularly high strength properties. Researchers have been studying how these materials can improve paper properties and will present their latest finding this June 24-27, 2013, in Stockholm, Sweden, at TAPPI's 8th Annual International Conference on Nanotechnology for Renewable Materials at the KTH Royal Institute of Stockholm.
The program for this year's event has been released, and one session will focus on using cellulose nanofibers for improving retention and increasing strength in paper. Researchers from Aalto University in Finland will report on improved flocculation of both precipitated calcium carbonate (PCC) and kaolin with the addition of certain cellulose nanomaterials. Researchers from Papiertechnische Stiftung (PTS) in Heidenau, Germany, will report on the importance of adding fillers, celluloses, and compounding agents in the right order to achieve the best results. Researchers from VTT in Finland will report on ways to increase the strength of paper by using filler particles coated with nanoscale calcium silicate hydrate (CS) structures.
New reports at the conference will present some exciting advances for both within the pulp and paper industry and beyond. The technical program features cellulose nanomaterials in a variety of applications, including:
- Unique and Thin-Film Composites
- Filler and Coating Applications for Different Paper Grades
- Improved Barrier Properties for Packaging Applications
- Cellulose Nanomaterials as Films and Carriers in Medical Applications
- Nanopaper and Iridescent Colored Cellulose Films.
With more than 80 technical presentations, five keynote presentations, and 50 poster presentations, this year's conference is packed with the latest applications of renewable nanomaterials.
Watch for additional updates from TAPPI on how nanotechnology, and cellulose nanomaterials in particular, can be a transformative technology for the pulp and paper industry.
The 8th Annual International Conference on Nanotechnolgy for Renewable Materials is hosted by TAPPI's International Nanotechnology Division, which strives to collectively advance the responsible and sustainable production and use of renewable nanomaterials. More information is available online.
##SHARELINKS##
|
The Bleaching of Pulp, Fifth Edition
By Alan W. Rudie and Peter Hart
Previous editions of The Bleaching of Pulp have provided comprehensive information on the technology used to bleach wood pulps. The 5th edition will continue this tradition as the premiere industry text on bleaching technologies but will be more focused on the modern industrial processes with less emphasis on fundamental science. New or more comprehensive sections are included on elemental chlorine free bleaching, enzymes, acid treatments for hexeneuronic acids, control of mineral scale, and multi-stage modeling as used to optimize bleaching among multiple stages.
Item Number: 0101R331 • List Price: $232 • Member Price: $155
Handbook for Pulp and Paper Technologists
(The Smook Book) Third Edition
By: Gary A. Smook
This best-selling text provides an introduction to the entire technology of pulp and paper manufacture. The book features 27 chapters covering all aspects of pulping and papermaking. Hundreds of illustrations, charts, and tables help the reader grasp the concepts being presented. The third edition features additional material on secondary fiber recovery and utilization, mechanical pulping, kraft pulping and bleaching, and papermaking. 2002. 425 pages, hard cover.
Item Number: 0202SMOOK • List Price : $75 • Member Price: $56
Troubleshooting the Papermaking Process
By: By Jerome M. Gess and Paul H. Wilson
This book takes the reader through the process of making paper, pointing out where interruptions can occur and where elements that are added to the system can cause problems in that part or subsequent parts of the papermaking process. The aim of this book is to give papermakers and those involved in the papermaking process the information required to allow them to understand how to track down and solve problems at their source rather than where the problems surface.
Item Number: 0101R298 •List Price: $161• Member Price: $106
Paper Machine Quality Control Systems - Vol. 1: Measurement Systems and Product Variability
By: Quality Control Systems Education Common Interest Group of the Process Control Division
This book describes in detail the measurement technology used in Quality Controls Systems (QCS). Individual chapters are devoted to the five most prevalent QCS measurements (basis weight, moisture, caliper, ash, and color) in the paper industry. Each of these chapters covers the physical principles involved in each measurement, sensor designs, various methods of implementation, and influence factors. A somewhat lighter coverage is given to 10 other QCS measurements that do not have such a broad installation base. Common issues that impact all sensors are explained, including how sensor performance is measured and reported, the impact of scanning process, filtering, scanner designs and construction, and sensor calibration and correlation. Statistical methods are covered in depth from discrete one-dimensional variability to multi-dimensional variability. Guidance is provided for using these statistical methods to locate the sources of variability in the paper process.
Item Number: 0101R328•List Price: $205• Member Price: $135
The Corrugated Containers Manufacturing Process
By: Jody A. Brittain, Stephen R. Perkins, and Philip G. Schnell
This comprehensive textbook describes the entire process of manufacturing corrugated containers. In addition to detailed explanations, the book also features practical troubleshooting tips, and a discussion of common problems and solutions within each major section. Seven detailed chapters cover the following topics:
- Paper and the Papermaking Process
- Steam
- Corrugating Adhesives
- Singleface Operations
- Doublebacker Process
- Combined Board
- Converting.
This textbook is designed to provide in-depth explanations and information for professionals working in all areas of the corrugated containers industry.
Item Number: 0101R281•List Price: $185•Member Price: $37
##SHARELINKS##
|
The Pulp and Paper Manufacturers Association (PPMA) has launched its first-ever Best Place to Work Award. The award is open to all companies in the forest products industry and will look not only at corporate life but also look at how employees feel about their work environments.
In conjunction with Majority Opinion Research Group, PPMA has started taking nominations for this award and will continue to accept nominations through July 1, 2013.
"This award is an exciting opportunity for PPMA to honor great companies. As an association that serves HR professionals, we know the value of the making your company a great place to work," said PPMA President Joe Thibaudeau, employee relations manager - Procter & Gamble - Green Bay, Wis., USA.
The award will be presented to the winner at the annual PPMA conference on October 23-25, 2013, in Milwaukee, Wis., USA. The winner will have the chance to speak with conference attendees about what makes his or her company the "Best Place to Work."
PPMA is a nonprofit association built around a community comprised of executives, managers, and human resource professionals from the pulp and paper industry. For its members, PPMA serves as a primary source of information on labor settlements and current human resource issues, governmenta,l and related operational issues.
To nominate your company for the Best Place to Work Award, use the online form.
##SHARELINKS##
|
The Pulp and Paper Safety Association (PPSA) will host its 70th Annual Safety and Health Conference - "The Human Element of Safety," June 9-12, 2013 in Williamsburg, Va., USA.
At the conference, presenters will address how human behavior will proactively help prevent, detect, and control events before they occur. Professionals from across the country know the importance of safety and attendees will hear from 18 speakers who will show the impact of addressing the human impact on safety. The conference will feature updates from OSHA, member company case studies, and PPSA's popular legal update.
Among the confirmed speakers are representatives from MeadWestvaco, Weyerhaeuser Co., Domtar, Safe Start, International Paper, REM Safety Consulting, Michael Best & Friedrich Law Firm, Training Logic, Change Management Consulting, and BushCo.
PPSA is a non-profit, non-political, international organization, devoted to the countinuous improvement of safety throughout all aspects of the paper industry. From forest products to paper mills, to converting plants, to recycle collections centers, our membership is grouped by category to ensure a fair and appropriate basis for comparison.
Registration is currently open for this event. More information is available online.
##SHARELINKS##
|
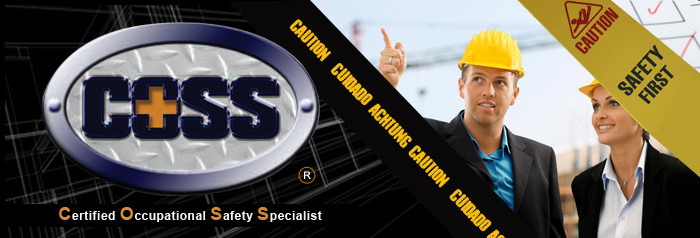
Are you ready to go further, faster in your safety career? The Certified Occupational Safety Specialist (COSS) class can take you there.
The COSS Class is Unique
Not only will you learn how to read and understand the OSHA 1910 and 1926 CFRs and help your company avoid OSHA citations that cost millions of dollars, but more importantly, by learning how to work safely on a job site, you can teach your company how to lower fatalities and near misses. Almost 47% of COSS graduates responding to our survey indicate that, since taking COSS, their company's injury rate and/or OSHA recordables have decreased by as much as 25% and others attest to as much as a 100% decrease!
Request a Course Outline & Syllabus for more information.
The class also addresses the psychology of safety, the true cost of an accident, hazard recognition, how to start up a health and safety program, behavior based safety, system safety, and much more!
What Will You Receive?
Upon successfully completing the class, you will obtain your national Certified Occupational Safety Specialist (COSS) designation, your OSHA 10-hr. card of completion in construction, and your OSHA 10-hr. card of completion in general industry.
National Program Recognitions
COSS is currently one of only 37 programs in the world recongnized and accredited by the American Petroleum Institute (API). In addition, the certifying body for construction education for colleges, universties and technical/trade schools, American Council for Construction Education (ACCE), has also recongnized our program. COSS is the only non-degree program to receive this national endorsement. Lastly, COSS has been established as a mandatory course for students in the Construction Management Program at Louisiana State University.
Program Content
The program consists of 40 hr. of hands on, face-to-face learning, which is delivered by an Authorized OSHA outreach trainer in both construction and general industry. Case studies and workshops are used extensively to bring learning objectives into focus. Guest speaker from areas such as OSHA and other governmental agencies are used to enhance the learning experience. Student presentations, daily quizzes, practical reviews, and a comprehensive final exam will allow you to demonstrate your competency.
Prerequisites
The only prerequisite for the COSS class is you must have a high school diploma or equivalent. In each class, we tend to have a mix of non-experienced, first time safety persons, as well as safety professionals who have been in the safety field for 20+ years. But, we have learned that regardless of the numbers of years of experience you have in safety, everyone leaves the COSS class with a wealth of knowledge!
Visit the COSS website for FAQs, testimonials and a list of clients that have taken COSS.
Register now.
If you would like more information on the COSS program, contact Beth Gordon at 877-610-2677
##SHARELINKS##
|
|
|