Over the Wire
TAPPI
Weekly Spotlight
Verso Paper Corp., Memphis, Tenn., USA, this past week announced that it has decided to cease further discussions with NewPage Corp., Miamisburg, Ohio, or its creditors regarding a potential business combination. Verso President and CEO David Paterson said that "after careful analysis, we believe it is in the best interests of our company and its stakeholders to focus on the many other opportunities for Verso, including internal growth projects and other potential strategic alternatives."
Verso is a producer of coated papers, including coated groundwood and coated freesheet, and specialty products. Its paper products are used primarily in media and marketing applications, including magazines, catalogs, and commercial printing applications such as high-end advertising brochures, annual reports, and direct-mail advertising.
##SHARELINKS##
|
The Institute of Paper Science and Technology (IPST), Atlanta, Ga., USA, and the Institute Heritage Foundation—the alumni association for graduates of IPST, the Institute of Paper Chemistry, and the Georgia Tech Paper Science and Engineering program—will co-host an information session from 4:00 p.m. - 5:15 p.m. on October 11 at the Paper Valley Hotel in Appleton, Wis., immediately preceding the Paper Hall of Fame Induction Ceremony.
Officers Mike Friese (Encapsys—Appleton Papers) and Chris Luettgen (Kimberly-Clark Professional) are alerting all alumni and interested parties to this upcoming event and to the planned renewal of the Institute Heritage Foundation.
Alumni and interested parties are urged to send their contact information as soon as possible, whether or not they are planning to attend the event. Please include information about degrees and year conferred and, as applicable, current employment. Those who plan to attend should so indicate. Volunteers to assist with program planning are welcomed. All parties are asked to forward this notice to other alumni, to help spread the word.
More information is available online. The Foundation thanks all respondents for assistance in distributing this announcement.
##SHARELINKS##
|
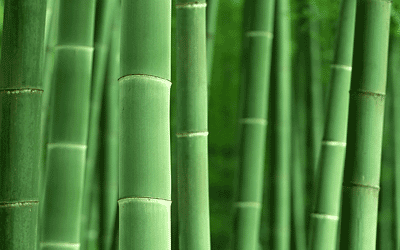 Booshoot, Mount Vernon, Wash., USA, a biotechnology company focused on bamboo forestry, agriculture, and nursery wholesale, and Kimberly-Clark (K-C), Dallas, Texas, this week announced a development agreement that will enable K-C to explore the manufacturing of tissue products containing fiber derived from Booshoot's proprietary bamboo propagation technology. The partnership marks a significant breakthrough for the tissue industry, as the companies will work together to develop high-yield fiber alternatives that can be grown domestically on a mass agricultural scale in environmentally and socially responsible ways.
According to the agreement, Booshoot will deliver tens of thousands of bamboo starts to be grown in K-C pilot projects. The trials are designed to prove the viability of several species of giant bamboos, including "Moso" (Phyllostachys edulis), as a scalable and sustainable tree fiber alternative. Where conventional northern softwood trees take 60 or more years to reach harvestable maturity, Moso grows close to 100 ft tall and is harvestable in less than a decade, producing several times the fiber of traditional timber, and capturing four times the carbon dioxide of most trees.
"We are pleased to be working with such an established global leader in the tissue industry, and to play a role helping Kimberly-Clark meet their ambitious environmental targets," said Booshoot CEO Jackie Heinricher. "Booshoot has the proven science and production capacity required to eventually produce millions of bamboo plants annually, which will play a critical part in reducing the world's dependence on native forests."
Gordon Knapp, president of North American Consumer Tissue for K-C, said that "as a leader in bamboo technology, Booshoot is well positioned to support Kimberly-Clark's objective to develop sustainable fiber alternatives and take them to commercial scale. Introducing alternatives to natural forest fiber to our supply chain is important to our goals associated with responsible fiber sourcing as well as our goals to improve management of input cost risk and variability."
In 2011 K-C used nearly 750,000 metric tons of primary wood fiber sourced from natural forests. The agreement with Booshoot is designed to help K-C meet its pledge to cut the amount of natural forest fiber in half by the year 2025, an amount equivalent to the fiber used to manufacture more than three billion rolls of toilet paper.
Booshoot's patent-pending bamboo are "true to type" species that are not genetically modified, producing more biomass on less land, in less time than other traditional forest products. In addition to providing fiber for the paper industry, bamboo from Booshoot is an ideal raw material for everything from textiles to biofuels to building materials.
##SHARELINKS##
|
SCA, a Sweden-based tissue, hygiene, and forest company with U.S. headquarters in Philadelphia, Pa., has awarded 41 children of its employees in the U.S. and Canada a total of $61,000 in scholarships for their higher education in 2012-2013. Since creating its annual scholarship program five years ago, the company has given more than $300,000 to high school seniors and college students.
"Our employees have made our business what it is today," said John O'Rourke, VP of human resources, SCA Americas. "SCA is delighted to help their children strive for success by providing education scholarships to these well-deserving students. These talented young adults have demonstrated a deep commitment to their schools and communities that we are proud to support."
The students received scholarships ranging from $500 to $2,500 for their full-time schooling at an accredited U.S. or Canadian university in 2012-2013. SCA invited all high school seniors and college students, age 24 and under, whose parents have been employed by SCA for more than one year to apply. An independent organization, Scholarship America, reviewed all the applications and selected the 41 winners, based on their academic achievements, demonstrated leadership, and participation in school and community activities, honors, work experience, statement of goals, and an outside appraisal.
SCA employs nearly 3,000 people in North America, between its headquarters in Philadelphia and 11 manufacturing sites and offices throughout the U.S. and Canada. Across the continent, SCA produces Tork® tissues, napkins, towels, specialty wipers, dispensers, and soap used in commercial settings such as restaurants, office buildings, schools, and healthcare facilities. Tork products are made from 100% recycled content and the company uses more than 750,000 tons of recycled paper a year. SCA is also the manufacturer of the TENA® line of personal care products for light, moderate, and heavy incontinence.
##SHARELINKS##
|
Sappi Fine Paper North America (SFPNA), Boston, Mass., USA, this week announced the 13 grant recipients for its 13th annual Ideas that Matter program, an industry grant program aimed at helping designers create and implement print projects for charitable causes. Since 1999, the program has awarded more than $12 million worldwide in grants to designers around the globe to support their work for nonprofit programs and organizations.
SFPNA notes that this year's winning projects reflect the on-going commitment in the design community to utilize design in combination with innovative thinking to solve social problems. Grantees submitted outstanding proposals outlining their ideas, creative execution, and their unique ability to instill positive social, cultural, or environmental change.
The selected proposals were determined by an independent judging panel of leaders from the design profession. This year's judges, all widely recognized for their forward-thinking commitment to design for social good, included Rich Hollant, principal/design director at co:lab inc., Hartford, Conn.; Sam Shelton, principal/designer, Kinetic, Washington, D.C.; Mariana Amatullo, VP, Designmatters Department, Art Center College of Design, Pasadena, Calif.; Mike Weikert, partner, Weikert Design, Baltimore, Md.; and Tracy West, creative director, 50,000feet, Chicago, Ill.
"Sappi started the Ideas that Matter program because we wanted to give back in a way that we felt could make a real and lasting impact," said Patti Groh, marketing director, SFPNA. "After 13 years, we are proud to see this legacy continue and to be able to recognize the critical role that good design plays in inspiring people to take action."
More information about the 2012 Ideas that Matter program, including a list of grant recipients, is available online.
##SHARELINKS##
|
Rayonier, Jacksonville, Fla., USA, has donated $75,000 to help the University of Florida (Gainesville, Fla.) raise $1.5 million needed to build the new Austin Cary Forest Learning Center. The donation was celebrated at a recent ceremony in the 2,040-acre Austin Cary Forest, located about six miles northeast of Gainesville.
The funds will support a 7,800-sq ft building that includes a spacious conference room, a classroom, library, kitchen, gallery, and large wrap-around porch. It also will include an elevated deck built out over the surface of Lake Mize. With high ceilings, clean lines, and large timbers, the building is designed to complement its natural surroundings.
Rayonier explains that the learning center is needed to replace the Austin Cary Forest Conference Center that opened in 1986, remembered by thousands of current and former Alachua County residents as a place where UF classes met and special events were held. That building was destroyed by fire in July 2011.
News of the disaster inspired Rayonier executives to reach out to UF's School of Forest Resources and Conservation, said Paul Boynton, president and CEO of the company. "Rayonier has a long connection to the University of Florida, particularly IFAS and the School of Forest Resources and Conservation," Boynton said. "We consider them great partners in the success of our company, and we're proud to provide assistance to this effort."
Boynton noted that many graduates of the UF forest resources school are hired by Rayonier's forest resources operation, one of the company's three primary businesses. The others are real estate and production of high-performance fibers.
Jack Payne, UF SVP for agriculture and natural resources, said the new center will help UF/IFAS programs keep pace with the ever-evolving needs of forest landowners. "Rayonier has come to expect the best from us, in terms of producing students who know the latest production technologies and challenges," Payne said. "Their generous contribution helps ensure that our students continue to receive top-flight instruction and practical know-how through programs at Austin Cary."
Fund-raising efforts have so far produced more than half the $1.5 million goal, said Tim White, director of the UF forest resources school. If fund-raising continues at its current pace, he added, the full amount needed may be raised by the end of the year. Groundbreaking for the project could happen as early as March 2013.
Administrators have set a goal of drawing 25,000 visitors to the learning center annually, for classes, outdoor youth programs, professional meetings, and social events.
##SHARELINKS##
|
Neenah, Wis., USA, will again be the location for the TAPPI Yankee Dryer Safety and Reliability Committee (YDSRC) meeting, scheduled for November 6. Miron Construction has agreed to host the gathering.
The meeting will feature technical presentations on yankee doctor setup and profiling and considerations for metalizing Yankees. The meeting will be co-located with the Lake States TAPPI Energy Forum. More details are available online. The TAPPI Tissue Runnability Course will follow the YDSRC meeting on November 7-9, also in Neenah.
YDSRC is an active group of Yankee dryer owner/users and service providers who meet twice annually to reduce delay that causes low productivity and negatively impacts dryer safety and overall business results. The committee's goal is to develop standard practices and standards for problems that cause drying system delay and compromise safety across the tissue industry. More information is available online.
##SHARELINKS##
|
Below is the latest listing of job openings in the TAPPI Career Center. The current listing includes job openings for a variety of pulp and paper manufacturing positions, product marketing manager, shift supervisor, stock prep manager, chemist, sales engineer, director of production planning, and customer service representative. Current, specific job openings at companies and locations in the TAPPI Career Center include:
Employer |
Title |
Location |
AIRTHERM Corp. |
Sales Engineer |
Longview, Wash. |
Albarrie Environ. Serv. |
Product Mktg. Mgr. (Liquid Filt. Media) |
Canada |
Armstrong World Ind. |
Maintenance Mgr. |
Pennsylvania |
Boise Inc. |
Sr. Scientist-Fiber |
Wallula, Wash. |
Celanese |
Chemist II-Paper Lab |
Florence, Ky. |
Confidential |
Pulp & Paper Manufacturing Openings |
Fernandina Beach |
Confidential |
Pulp & Paper Manufacturing Openings |
Hopewell, Va. |
Confidential |
Pulp & Paper Manufacturing Openings |
West Point, Va. |
Confidential |
Pulp & Paper Manufacturing Openings |
Florence, S.C. |
Confidential |
Technical Services Manager |
Columbus, Ohio |
Confidential |
Coatings Scientist |
Columbus, Ohio |
First Quality Enterprises |
Director of Operations |
Lock Haven, Pa. |
Georgia-Pacific |
Mgr.-Process Safety |
Atlanta, Ga. |
GL&V USA |
Sr. Process Engineer- Fiberline Specialist |
Nashua, N.H. |
Longview Fibre |
Dir. Production Planning/Order Fulfillment |
Longview, Wash. |
New-Indy Containerboard |
Shift Supervisor |
Ontario, Calif. |
New-Indy Containerboard |
Stock Prep Mgr. |
Ontario, Calif. |
UPM Kymmene |
Customer Service Representative |
Westmont, Ill. |
More information about these jobs is available online
##SHARELINKS##
|
Market Roundup
In the North American coated paper sector, Mark Wilde of Deutsche Bank reports that the LWC (lightweight coated) paper market is showing signs of some strength. Estimated prices on No. 5, 40-lb offset rolls were up $15/ton to $850 - $890/ton in August. Producers had announced a $40-60/ton price hike for May/June.
The key driver behind the positive price gains, Wide notes, is improved demand/supply balance from ˜12% reduction in capacity (Verso's 180,000 tpy Sartell PM 3 and Resolute's 150,000 supercalendered machine No.1 at Catawba.) July shipments were +0.3% y/y (YTD -2.8%).
August No. 3 60-lb CFS (coated free sheet) prices were flat m/m at $965 - $985/ton. Producers failed to implement the $30/ton May price increase. July shipments improved modestly, down -0.9%, Wilde reports.
##SHARELINKS##
|
Uncoated free sheet (UFS) prices were flat in August, Mark Wilde of Deutsche Bank continues. Prices for 20 lb repro-bond were stable at $1,035 - $1,085/ton. Prices for 50 lb offset was flat m/m at $910 - $930/ton. A $40/ton cut-size price hike for late-May/early-June and a $60/ton increase on offset grades have both failed. Trade reports suggest some spot deals on cut-size papers.
UFS demand remains sluggish. July shipments were -2.7% y/y (YTD -3.0%), Wilde reports. Additional supply from the restart of the Grays Harbor mill (+135,000 tpy) will be offset by Domtar's conversion of its 270,000 tpy Marlboro mill to specialty grades, he adds.
Uncoated groundwood estimated prices were flat in August, according to Wilde, with 22-lb directory at $790 - $810/ton, 35-lb offset at $650 - $700/ton, and SC-A at $820 - $860/ton. Demand remains anemic. July shipments were down 18.7% y/y, while Q2 shipments were -15.7% y/y. Potential restart of a 360,000 tpy supercalendered paper machine at Pt Hawkesbury, Nova Scotia, by late-September could increase supply in the market and pressure prices. Verso's Sartell mill shutdown will reduce supercalendered capacity by a very modest 35,000 tpy, Wilde says.
##SHARELINKS##
|
Pulp & Paper
Fortress Paper Ltd., Vancouver, B.C., USA, this week updated the status of projects and operations at four of its global facilities—the Fortress Specialty Cellulose Mill and the Fortress Global Cellulose Mill in Canada, the Dresden, Germany, mill, and the Landqart Mill in Switzerland. Fortress Paper operates internationally in three business segments—dissolving pulp, specialty papers, and security paper products.
Fortress operates its dissolving pulp business at the Fortress Specialty Cellulose Mill, which is also in the process of expanding into the renewable energy generation sector with the construction of a cogeneration facility, which, it says, is proceeding generally as planned with some minor delays due to delivery impediments of major equipment. The turbine and generator are on site and installed with delivery of the final critical path item expected late this month. The cogeneration facility is expected to be delivering power in January. The company recently acquired the Fortress Global Cellulose Mill located at Lebel-sur-Quévillon, Qué., Canada, which it intends to convert into a dissolving pulp mill.
The Fortress Specialty Cellulose Mill has confirmed that the annual maintenance shutdown will be taken the last week of this month. During this outage, critical electrical work will also be completed to allow connection of the new power generating facility to the grid. This is the first scheduled maintenance shutdown since the mill commenced producing dissolving pulp, and it is anticipated that the next annual maintenance cycle may also require a higher level of planned maintenance downtime.
During August, the specialty cellulose mill operated at an average monthly rate of 83% of planned production capacity, with steady progress being made on de-bottlenecking activities. Production of dissolving pulp was recently curtailed for an equivalent of four days of pulp production as a result of a premature tube failure in the mill's No. 2 recovery boiler. The boiler and full mill were shut down safely to complete repairs and are now operating normally. The curtailment and subsequent ramp-up reduced the mill's overall production efficiency for the month.
Initial work has commenced at the Fortress Global Cellulose Mill following the close of the acquisition this past June, including building and equipment repair and the reactivation of services and utilities in a planned sequence. Water supply and fire protection services are operational and the high voltage distribution network is in the process of being reactivated. Critical equipment assessment is ongoing and the company is finalizing refurbishment plans for the key process areas. Various cost saving and asset preservation plans are being developed ahead of the coming winter season. To date, pulp mill repairs and re-commissioning activities are proceeding materially as planned.
The Fortress Global Cellulose Mill has also received an official authorization permit from the Québec Ministère du Développement durable, de l'Environnement et des Parcs. This permit is required to proceed with the construction of the new dissolving pulp plant.
Following the filing of its application with Hydro-Québec Distribution, the Fortress Global Cellulose Mill has received approval for its cogeneration project at Lebel-sur-Quévillon and is working with Hydro-Québec toward the conclusion of the power purchase agreement, expected to be completed shortly.
At the Dresden mill, continued growth of the worldwide market for non-woven wallpaper base has exceeded management's expectations and the mill is maintaining its position as a leader in this market, the company notes. During the general maintenance shutdown of the mill in the first 10 days of August, the company completed the main portion of its 2012 capital expenditures program. To date in 2012, the company has spent approximately EUR 3.7 million in Capex with the goal of increasing production speed from 450 m/min to approximately 475-500 m/min, depending on the product mix, and thereby increasing its theoretical annual production capacity from approximately 56,000 metric tpy to approximately 60,000 metric tpy. This increase in production capacity would enable Dresden to maintain its market share of approximately 50% of the world-wide non-woven wallpaper base market.
Although the Landqart Mill had another challenging month in July, results in August show a marked improvement with product shipments commencing for the large re-instated banknote substrate order, Fortress reports. Although waste rates remained relatively high during this period, they are decreasing and are coming in-line with expectations.
##SHARELINKS##
|
Ilim Group, Russia, this week reported that it will invest more than $580 million this year to complete modernization and expansion projects at its mills. Group CEO Paul Herbert made the announcement at a media briefing held at the APEC CEO Summit in Vladivostok, Russia.
"By the fifth anniversary of our joint venture with International Paper this October, we will have fulfilled the investment plans that were given at the time of our JV launch in 2007. Including the 2012 amounts, the total investment we have made since 2007 will exceed $1.8 billion, which is even larger than we announced five years ago," Herbert said.
The company is currently completing construction of a new world's-largest softwood pulp line in Bratsk, Siberia (investment of approximately $800 million), and is building a new paper production line in Koryazhma at a cost of $270 million. Both projects will be completed by the end of 2012 and production will start flowing into markets during the first quarter of 2013.
Other major investment projects already completed by the company include a $250 million investment in latest technology forest equipment that improved efficiency of harvesting, transportation, and reforestation operations by 40%, and the construction of a $50 million new semichemical pulping process that dramatically improved the quality, effectiveness, and ecological friendliness of the company containerboard production at Koryazhma.
"Ilim Group continues to demonstrate that it is the Russian forest industry leader and the largest investor in the Russian pulp, packaging, and paper industry. Currently, our main focus is to successfully complete and startup our big projects. After that, we will start development of our next growth steps, which will include investments focused on building capacity for high quality consumer packaging products for the domestic market, and a second major expansion of our softwood pulping capacity in Siberia to satisfy the growing Chinese and SE Asian demand," Herbert added.
##SHARELINKS##
|
Metsä Tissue Oyj, Finland, part of Metsä Group, a European tissue and cooking paper products supplier, has signed a credit agreement with the European Bank for Reconstruction and Development (EBRD). The EUR 35 million, 8.5-year loan will finance further operational improvements in Poland and Russia.
The ongoing investments at the company's Krapkowice mill in Poland are part of a three-year development program aiming to strengthen the company's market position in Continental Europe, improve its production capacity, and enhance its brand and service offering. Productivity will additionally be improved by consolidating Polish tissue base paper production at one mill and by further standardizing technology.
Two new Voith tissue machines are included in the Krapkowice mill expansion. PM 7, currently starting up, will have a production capacity of 35,000 metric tpy. The second 35,000 metric tpy machine, PM 8, will be installed next year. The program also includes the rebuild of PM 6 at Krapkowice, which has a capacity of 17,000 metric tpy. PM 5 has been permanently shut down, as has PM 11 in Konstancin-Jeziorna, near Warsaw.
After the project has been completed, the Krapkowice mill will have a capacity of approximately 90,000 metric tpy. A new converting line also will be installed at Krapkowice.
In addition to boosting productivity and energy efficiency, the program will also yield significant environmental benefits such as lower energy consumption and carbon dioxide and sulfur dioxide emissions.
Finally, part of the EBRD loan will be used for a new converting plant in Russia. The company will relocate its converting operations to a new converting and distribution facility in Vorsino, about 55 km away from its existing converting plant in Naro-Fominsk, which will be closed.
##SHARELINKS##
|
Metso, Finland, reports that it has received several measurement orders from Chinese paper mills. The orders were from Jiangsu Jinhuang Paper Co., Hebei Changtai Paper Industry Co., Anhui Huatai Forest Pulp & Paper Co., Guangdong Huatai Paper Co., and Wuhan Jin Feng Huang Paper Industry Co.
Metso will deliver to Anhui Huatai a dozen consistency transmitters, one of them being a Metso OC, an optical consistency transmitter. The upcoming delivery for the rebuilding of a pulp factory also includes several Metso SP (blade) and Metso Rotary transmitters, as well as equipment for cooking liquor measurement, among other things.
The Jiangsu Jinhuang order is for several Metso SP (blade) transmitters for a greenfield factory. Another greenfield project customer is the Hebei Changtai Paper Industry, which will be installing a linerboard project as well as a plasterboard paper machine. The Wuhan Jin Feng Huang mill is also among the company's recent major customers, ordering two new board machines (PM 3 and PM 5), as well as 16 Metso SP consistency transmitters. All of the orders from the Chinese papermaking companies are due to be delivered this fall.
The Metso optical consistency transmitter is a new member in the family that uses state of the art technology with a new design, offering reliable measurement at all times, the company explains. In mechanical pulping (e.g. TMP, GW, and CTMP), typical applications are grinders, cyclone cleaners, latency removal, screening, and low consistency refining. In chemical pulping, the new transmitter can be used for screening, washing, refining, and drying machine applications.
##SHARELINKS##
|
Norske Skog, Norway, reports that it will convert a machine at its Boyer mill in Australia to the production of coated grades, and close one newsprint machine at the Tasman mill in New Zealand. The machine conversion project at the Boyer Mill in Tasmania will involve an AUD 84 million investment over the next two years to allow the production of coated papers suitable for catalogs. The Australian Federal Government will contribute AUD 28 million in grants to help fund the project, and the Tasmanian State Government is providing an AUD 13 million loan. Completion is targeted for the first quarter of 2014.
"We are committed to the future in Australia, and are therefore investing AUD 84 million there. With substantial funding support from the Australian government, we are strengthening the operations at Boyer. This will create future growth opportunities for the Norske Skog group," said Norske Skog President and CEO Sven Ombudstvedt.
"The permanent closure of 150,000 metric tpy of capacity at the Tasman mill in New Zealand is required to create a better balance between demand and supply for newsprint in the region. Currently there is considerable surplus capacity of newsprint in the region. Despite years of great efforts of the staff, the decision is unfortunately unavoidable. The implementation arrangements and timeframes will be subject to consultation with employees and other stakeholders," Ombudstvedt added.
The final costs of the restructuring will be determined once the consultation process at the Tasman mill is completed.
##SHARELINKS##
|
Resolute Forest Products Inc., Montréal, Qué., Canada, this week reported that it will take advantage of its strong liquidity position to redeem an additional $85 million of its 10.25% senior secured notes due 2018. The company also announced that it has now repurchased 3.7 million shares of its common stock under the existing $100 million share repurchase program.
"I'm pleased to say that we have now repurchased more shares than we issued to acquire Fibrek," said Richard Garneau, president and CEO. "Today's announcements demonstrate our commitment to disciplined capital management—we are using our strong financial position to reduce debt, while also returning cash to shareholders. We will continue to manage capital with the utmost discipline, carefully balancing initiatives to return cash to shareholders with other considerations, such as pursuing sound capital investments and opportunities to further increase Resolute's earnings power."
The company will use available cash for the redemption of $85 million in principal amount of the notes, plus accrued and unpaid interest. The redemption is scheduled to occur on October 10, at a redemption price of 103%. Following the redemption, the aggregate face amount of the notes will be approximately $500 million.
Resolute owns or operates 21 pulp and paper mills and 22 wood products facilities in the U.S., Canada, and South Korea.
##SHARELINKS##
|
Sofidel, Italy, producer of Regina paper towels, has closed its acquisition of U.S.-based Cellynne Holdings Inc. Founded in 1988, with headquarters in Haines City, Fla., Cellynne is a producer of tissue paper (for hygienic and domestic use) in the away-from-home (AFH) and at-home (AH) consumer sector. It has more than 300 employees and three production sites, strategically located in the U.S., with two additional converting sites in Green Bay, Wis., and Henderson, Nev. It has an overall production capacity of 70,000 metric tpy.
With this acquisition, Sofidel, Europe's second biggest paper tissue producer, now has access both to a new continent and the particularly challenging U.S. market. The decision is consistent with its policy aiming at international growth and innovation, a strategy that began at the end of the 1990s.
"This is an important step in the group's international growth strategy," said Sofidel CEO Luigi Lazzareschi. "It raises the group's overall production capacity to more than 1,000,000 metric tpy and marks its entry into the U.S. market."
"Cellynne is a great company. We have full confidence in the expertise and professionalism of its staff and in the efficiency of the factories acquired, Lazzareschi added. "This is a strategic investment that we hope will further strengthen our competitiveness and growth, by entering such a market that is full of opportunities."
##SHARELINKS##
|
Containerboard/Packaging
KapStone Paper and Packaging Corp., Northbrook, Ill., USA, has approved a $29 million investment in the company's North Charleston, S.C., paper mill. The investment is expected to improve the capability and efficiency of No. 3 paper machine in producing ultra high performance (UPL) lightweight linerboard grades by replacing the press section. The new press section will be supplied by PMT Italia. The investment also includes projects in the fiber and utilities areas to support production of these strategically important grades.
Engineering and construction phases of the project are expected to occur over the next 18 months, targeting installation of the press section during the first quarter of 2014.
KapStone Paper and Packaging is a producer of unbleached kraft paper and corrugated products. It is the parent company of KapStone Kraft Paper Corp. and KapStone Container Corp., which includes three paper mills and 14 converting plants across the eastern and mid-western U.S. The business employs approximately 2,700 people.
##SHARELINKS##
|
Cascades Inc., Kingsey Falls, Qué., Canada, a producer of packaging and tissue products, reports that it is making major investments in several folding carton and microlithography plants of its Norampac Division. A total investment of $22 million will be used to install new equipment to optimize production and efficiency at the Viau (Montréal, Qué.), Mississauga (Ontartio), Winnipeg (Manitoba), and Cobourg (Ontario) plants.
With this investment program, the Lachute (Québec) folding carton plant will be closed at the latest by the end of the first quarter of 2013, and its customers will be progressively transferred to other Norampac facilities. Nearly 155 employees will be affected by the closure of the Lachute plant. However, approximately 40% of them will have the opportunity to be relocated in other Norampac and Cascades units in Québec.
Cascades notes that the installation of modern and versatile equipment in these plants will lead to an enhanced synergy between the microlithography and folding cartons sectors, which will allow Norampac to increase its productivity and efficiency. Two state of the art printing presses will be installed in the Viau and Mississauga plants. These presses, one which has a printing capability of up to seven colors and an ultraviolet drying process, were designed with the latest technology and are among the best in the industry. The optimization project also includes new equipment in the group's other folding carton plants, including a new gluer in Winnipeg and forming equipment in Cobourg.
"These investments are in line with Cascades' strategy that aims to modernize and improve the profitability of our packaging assets," explained Marc-André Dépin, president and CEO of Norampac. "This is our group's most important investment in the folding cartons sector in several years."
Dépin added that "the folding carton market in Canada continues to be key to our strategy in the packaging sector. This market benefits from stable growth that closely matches that of the consumer market for food products sheltering it from the negative cycles that affect industrial products. Cascades occupies an enviable position in the folding carton market in Canada, and these investments will allow us to consolidate and improve upon this position in the coming years."
##SHARELINKS##
|
Chesapeake, U.K., a global packaging manufacturer, reports that it will install a new GIDUE M5 digital flexo label press in one of its U.K. plants later this year. CEO Mike Cheetham noted that "the new GIDUE press will support our ambitious growth plans. The capabilities of this press will help to extend the range of labels we produce, particularly complex designs requiring a high number of colors, three or even five ply formats as well as using multiple substrates for the same label. The GIDUE press is also equipped with many quality control features that will help us strengthen the quality and service levels we deliver to our customers."
The M5 digital flexo press is equipped with 10 UV flexo print units and incorporates advanced HD camera technology (Print Tutor™) on each print unit. This checks each printed label for color consistency and "self-adjusts" print pressure, density, and print register through the use of seven servo driven motors on each unit. Machine setup is fully automated and print quality is monitored and adjusted at any manufacturing speed across a full range of substrates.
Federico d'Annunzio, MD of Nuova GIDUE S.r.l., explained that "Chesapeake is a large business with a global vision of the label and packaging industry. A dedicated GIDUE support team worked together with its management team to target the highest possible quality levels. Chesapeake is an ideal partner to develop innovative quality solutions that will offer its customers' even greater product reassurance."
##SHARELINKS##
|
New Products
Cristini Diagnostic Systems, Italy, has introduced PermFlowDUO™ as the world's first portable instrument to integrate (in the same unit) a sophisticated microwave meter, a water permeability meter, and a temperature sensor. The unit is designed to monitor paper machine press section clothing performance.
Cristini notes that monitoring press section clothing is essential to ensure that the paper machine runs at the best efficiency and quality, with the lowest emissions. Until now, it adds, the only way to monitor moisture and water permeability in press fabrics was by using two separate instruments.
For the operator, this required twice the number of accesses to paper machine positions (impacting safety) and twice the time for scans. It also reduced reliability of the measurements, since the scan of moisture and water permeability were not conducted in the same position at the same time.
With the PermFlowDUO, the company explains, the simultaneous scan of moisture, permeability, and temperature greatly improves safety and accuracy, while reducing the time for scans, stress on the operator, and, last but not least, investment, maintenance, and transportation costs.
The simultaneous reading at a high sampling rate allows the production of unique and accurate on-board 3D maps of the felt moisture and permeability. The 3D map felt scan does not require any sensor positioning device, and can be sampled during the normal cross-machine-direction scans by the on-board processor. A full 3D felt scan with good resolution normally requires only two minutes.
The instrument is provided with a full color range trigger (more precise and sensitive than the standard infrared triggers), to synchronize the scans with the felt revolutions. The sampling rate up to 2.5 times faster than standard meters allows not only better accuracy, but also a reliable, high resolution, on-board FFT analysis to predict possible press roll vibrations. The instrument's calibration curves allow accurate alignment of both readings with previous instruments and existing meters. An algorithm highlights, on the instrument screen, felt areas that are clogged or worn out, to help the papermaker better plan felt changes and felt cleaning intervals, according to Cristini.
The instrument does not require a PC to export data. Instead, data are downloaded on common USB mass storage devices in .txt, xls, and custom formats, compatible with the most commonly used data analysis and reporting PC software. All of the on-board functions are duplicated on the supplied PC database/analysis software.
More information is available online.
##SHARELINKS##
|
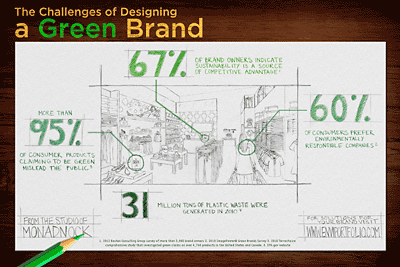 Monadnock Paper Mills Inc., Bennington, N.H., USA, the oldest continuously operating paper mill in the U.S., has officially launched the Envi Portfolio, a full complement of fiber-based solutions designed to provide eco-savvy brand owners with high-quality alternatives to plastics across a broad range of applications and end-uses. Gap stores and other global brands, Monadnock says, are already rolling out highly engineered solutions from the Envi Portfolio.
"Gap Inc. is committed to making sustainable choices that work for our customers and for the environment," said Jorge Perez-Olmo, senior marketing manager, Gap. "Monadnock's Envi Portfolio of environmentally-friendly, recycled paper and gift card products allow us to bring this effort to our stores."
Brand Design Manager Julie Colon of Burt's Bees adds that "Monadnock helps brands like ours continue to make more sustainable packaging choices without sacrificing performance, beauty, or budget."
The Envi Portfolio includes the following primary solutions for brands committed to environmental stewardship.
- Envi Card Stock —100% renewable and recyclable wood fiber alternative to PVC and PLA often used in gift, loyalty, promotional, and membership cards
- Envi Wet Strength Label —100% post-consumer recycled fiber (PCW) labels that withstand the rigors from high-speed application lines straight through to the ice bucket
- Envi Tag/Ticket— 100% PCW fiber offerings designed to effectively meet the marketplace need for environmentally friendly tags, tickets, and on-garment identification
- Envi Durable Tag— made with renewable and PCW fiber, ideal for high-moisture, weather-resistant applications such as horticultural tags and exterior POP signage
- Envi Folding Box— up to 100% PCW, bright white, high-caliper folding boxboard crafted to meet the marketplace need for environmentally friendly packaging
- Envi Shopping Bag— up to 100% PCW stocks that effectively address growing state and local directives legislating the use of plastic shopping/carrier bags
- Envi Wallgraphics — made with renewable and PCW fiber, these substrates are engineered to replace vinyl graphics for walls, windows, and other rigid surfaces in the home and in commercial environments.
The Envi Portfolio can be customized to meet brand owners' aesthetic, performance, and security requirements.
##SHARELINKS##
|
Metso, Finland, and the Swedish seal manufacturer Huhnseal, part of the Italian Meccanotecnica Umbra Group, have signed an agreement regarding mechanical seals for the global pulp and paper industry. The seals will be sold under the Metso brand with the product name SealMax. The agreement includes mechanical seals both for Metso equipment and for all standard applications.
Introducing SealMax is in line with Metso's ambition to expand its scope of supply. The two companies have initiated the development of tailor-made mechanical seals for Metso equipment, such as MC pumps, mixers, agitators, pulpers, screens, and LC refiners. These sealing solutions will be available for new projects and also as upgrades for existing equipment. Huhnseal already has solutions for most standard applications in the pulp and paper industry. These solutions will now be sold and marketed globally through Metso.
Mechanical seals are critical components in many types of rotating equipment and are therefore often given a high priority in the maintenance strategy. "Adding SealMax seals to our offering gives us in Metso the opportunity to work even closer with our customers. By combining the product and application know-how of Metso and Huhnseal, we can offer solutions with improved overall performance and thus save money for our customers," Björn Kempe, business manager, Service Agreements, Metso, said.
"Huhnseal and Metso have cooperated for more than 10 years. Huhnseal has a vast experience of supplying Metso with standard and special sealing solutions for its heavy-duty applications," said Per Hellman, CEO of Huhnseal. "This partnership is in line with our strategy to grow on a global scale. Huhnseal will provide product and service support to Metso via both our central as well as local resources around the world and continue with our ambition to supply the optimal sealing solution for each application."
##SHARELINKS##
|
Neenah Paper, Neenah, Wis., USA, has launched its Royal Sundance™ paper collection, bringing together two popular brands "to make paper selection a simple and affordable process." These economically priced papers are available in a variety of colors, textures, weights, and envelopes, the company notes.
The new collection consists of five finishes—felt, fiber, smooth, linen, and laid – each with its own color palette that includes a range of whites and its most popular business colors. There are also five common colors across the felt, smooth, linen, and laid finishes—brilliant white, ultra white, 100 PC white, natural, and Eclipse Black™.
After purchasing Wausau Paper's premium brands earlier this year, Neenah found that Wausau's Royal Papers were a natural fit with its own Sundance collection. Royal Fiber and Royal Linen Papers were the industry-leading choices for fiber-added and linen-patterned papers, while the felt and smooth finishes had been the hallmark of Neenah's Sundance Papers. The new collection brings these papers together as well as the Royal Resource and Royal Laid Papers.
"Royal and Sundance Papers were both very well-respected and well-known brands in the market," said Kathy Kemps, senior brand manager for Neenah Paper. "These two popular brands perfectly complemented each other, so the decision to take the best of both and create the distinctive Royal Sundance collection was ‘real simple.'"
The new offerings include a wide range of basis weights to mix and match finishes and colors, along with matching envelopes. Neenah Paper's Universal Digital Finish has also been added to the digital offerings in the collection, making Royal Sundance Digital Papers compatible with all digital presses.
More information (including instructions for placing an order) is available online.
##SHARELINKS##
|
To bring safety to the conduct of press fabric measurements, Voith (Germany) has developed ProTect. This new tool allows essential measurements to be carried out but eliminates risks to the operator from working close to rotating parts or walking on slippery surfaces.
ProTect was designed to safeguard operating personnel while giving reliable press fabric measurements at various positions in the press section of the paper machine. The tool is very easy to operate and adapts flexibly to different measuring equipment items. ProTect is a safe solution, giving exact and repeatable measurements of the press fabric, Voith notes.
Press fabric measurements are very important to ensure efficient paper production, Voith explains. Measurements, it points out, need to be taken while the paper machine is running, exposing operators to a number of safety risks. ProTect eliminates these risks. It consists of a self-propelled carriage, fixture, and any number of traverse beams. It can be used with all common manual measurement devices. The moving parts of ProTect are predominantly located outside of the machine, so wear and additional maintenance outlay are minimized.
##SHARELINKS##
|
Published Pricing
Södra, Sweden, will raise the price of its softwood pulp in Europe to $790.00 per metric ton, effective October 1. The company notes that the price increase is due to an improving market outlook, following a downward trend during early summer. The price will be unchanged in September.
Södra's four business areas produce sawn and planed timber goods, interior products, paper pulp, and biofuel. In recent years the company has also become such a large producer of electricity that it now produces more electricity than it uses. It employs some 4,000 people in areas that range from forestry management and environmental conservation to accounting, sales, and product development.
##SHARELINKS##
|
Energy
Millar Western Forest Products Ltd., Canada, reports that it will construct a $42 million bioenergy facility at its bleached chemi-thermomechanical pulp (BCTMP) mill in Whitecourt, Alberta, Canada. The project will involve integration of anaerobic hybrid digesters (AHDs) into the BCTMP mill's existing aerobic effluent treatment system.
The AHD units will recover organic material from the pulp mill's effluent stream and convert it to a biogas. After conditioning, the biogas will be used to fuel reciprocating engines, to generate 5.2 MW of renewable energy for use by the company's pulp operations.
All required regulatory approvals are now in place, allowing the project to proceed immediately. Construction will begin this month, with startup slated for late 2013. The project will not disrupt pulp or lumber production at the company's Whitecourt facilities.
##SHARELINKS##
|
People
Ahlstrom Corp., Finland, reports that Nathalie Ahlström has resigned as a member of Ahlstrom's Board of Directors due to a conflict of interest caused by her taking up a new executive position. The resignation was effective September 1.
Ahlstrom noted that the company and its board of directors "wish to warmly thank Ms. Ahlström for her valuable contributions and wish her all the success in her future endeavors."
The board will continue with six members until the next annual general meeting in 2013: Peter Seligson (chairman), Pertti Korhonen (vice chairman), Sebastian Bondestam, Lori J. Cross, Esa Ikäheimonen, and Anders Moberg.
##SHARELINKS##
|
TAPPI News
SuperCorrExpo, Oct.1-4, 2012, in Atlanta, Ga., USA, is your one-stop shop for all things corrugated. In addition to the nearly 300 exhibitors on the show floor, you can also take advantage of the pre-conference workshops, the joint TAPPI/AICC conference program featuring six keynote presentations and eight multi-track workshops, as well as countless networking opportunities like the Welcome Reception at 200 Peachtree on Sunday, September 30.
And, just added to the jam-packed program, there is now a Folding Carton Workshop sponsored by PIRA. Join Strategic Consultant Dr. Graham Moore on Thursday, October 4, as he provides an overview of the carton board sector and insight into the value added innovations that are attracting attention in the carton board market and increasing the functionality of the products. A separate registration is required for this workshop.
See for yourself why SuperCorrExpo is One Week. One Conference. One Can't Miss Event!
Register today!
##SHARELINKS##
|
Discounted Registration for PEERS and IBBC ends on September 14. In addition, discounted hotel rooms at the host hotel are available on a first-come, first-serve basis through September 21.
The Pulping Program will focus on new methods to improve kraft pulping to afford pulps that are more uniform in quality and to afford higher pulp yields. Also of interest is the one-day, pre-conference Intro to Kraft Pulping Workshop, designed for professionals that need to interact more knowledgeably with experienced process engineers and operators.
The Engineering Program will feature a Boiler Mact Panel Discussion (with panelists from URS Corp., Jansen Combustion and Boiler Technologies Inc., TRC Environmental Corp., A.H. Lundberg Associates, and Sage Enviornmental, and a one day Track on OpEx Maintenance and Reliability.
This year the Environmental Track will take a serious look at the current environmental landscape of the industry - from air and emission control to water reuse and waste.
Recycling experts from around the world will present new technological breakthroughs related to fractional pulping, absorption deinking, and electrostatic deinking for paper recycling in the Recycling Program.
The State of the Industry Session, part of the Sustainability Program, will feature "Fiber Supply and Demand" with Rod Fisher from Fisher International.
PEERS is co-located with IBBC, the only conference dedicated to examining applications of biorefineries in the pulp and paper industry - offering you a deeper analysis of technology and economics in commercializing biorefineries. See the Full Program.
##SHARELINKS##
|
The Corrugated Containers Manufacturing Process
Authors: Jody A. Brittain, Stephen R. Perkins, and Philip G. Schnell
This comprehensive textbook describes the entire process of manufacturing corrugated containers. In addition to detailed explanations, the book also features practical troubleshooting tips and a discussion of common problems and solutions within each major section. Seven detailed chapters cover the following topics:
- Paper and the Papermaking Process
- Steam
- Corrugating Adhesives
- Singleface Operations
- Doublebacker Process
- Combined Board
- Converting.
This textbook is designed to provide in-depth explanations and information for professionals working in all areas of the corrugated containers industry.
Product Code: 0101R281
Member Price: $37.00
Non-Member Price: $185.00
##SHARELINKS##
|
If you've ever wanted to feel more confident in working with important financial information at your mill, understanding the costs of running operations, or perhaps in putting the financial structure behind an idea, this course is for you.
The Financial and Strategic Analysis Workshop for Pulp & Paper and Related Industries is taught by instructors with decades of leadership in the business operations of the pulp and paper industry.
North Carolina State University and TAPPI have partnered to offer this exceptional course scheduled for October 3-5, 2012, in Raleigh, N.C., USA.
You'll learn both basic and sophisticated tools to help you analyze and manage important financial information with more confidence.
Understand the critical role of reinvesting in pulp and paper mill assets to ensure long-term survival and prosperity
- Study basics of capital budgeting, cost of capital (cost of debt and cost of equity), and financial indicators to allow you to use these tools to build financial analyses and sell your ideas, products, and services
- Appreciate the importance of cost structure and how you can increase your competitive advantage by managing your costs
- Explain in financial terms the impact of your operation, research, new technique, or new product
- Build an entire financial analysis from the ground up
- Learn the basics for strategic planning and decision making.
Learn more about the instructors and curriculum with this printable schedule.
##SHARELINKS##
|
 Member Jay Kaplan has been associated with TAPPI since 1994 when he was living in the Chicago area working for Stone Container. But it wasn't until years later that he finally took full personal advantage of all the benefits inherent in TAPPI membership, "the industry's best resource for technical support and information on emerging technologies and cutting edge science."
Having been mentored early in his career by serveral long-time TAPPI members, Jay says their influence set the groundwork for his future involvement. Through the years he has practiced in numerous meetings and shows at both the local and national level, and is now very involved in SuperCorrExpo, the largest tradeshow in the western hemisphere catering to the corrugated industry. "It's through events like these that you form and nurture professional relationships that help drive sustainable business improvements that may not have been achieved as quickly or at all without the common ground and opportunity that TAPPI provides."
Jay also believes this exposure to emerging technologies, technical expertise, and experts from outside his own company have played an integral role in his professional growth. Now serving as the Manager for Learning an Organizational Development for Corrugated Packaging at RockTenn, he says that use of TAPPI's website, the eLibrary, technical support, and industry news are all important elements to stay on the cutting edge of your career. And, furthermore, Jay puts his actions where his words are. Not content to just tell his peers and fellow employees about the benefits of membership, he recently brought a new group of new and future production managers to TAPPI's headquarters in Norcross, Ga., USA, for a tour and afternoon of learning. "I believe they left feeling a lot more informed about what our industry has to offer," he said.
To read more about Jay's professional accomplishments and personal interests, be sure to visit this month's Member Spotlight page.
##SHARELINKS##
|
Lake States TAPPI/North Central PIMA will host the 13th Annual "Guns of Navarino" on Tuesday, September 25, at J&H Game Farm in Navarino, Wis., USA. This event is designed to help relieve work related stress through a series of team building activities culminating in an evening of social interaction. Sounds good, doesn't it? Just ask anyone who has been to one of our past outings.
This event will begin at 11:30 a.m. on September 25, and the actual tournament gets underway as soon as teams assemble, at approximately 12:30 p.m. The format will be five-person teams. Individual shooters and teams of less than five are also welcome. We will make every effort to have complete teams of five for the competition. Registration is limited to the first 30 teams (150 shooters). The cost for the event will be $120.00 per person ($600.00 per team). Registration includes the following:
- Sporting clays, five-stand, wobble events
- Ammunition for both shooting events
- Dinner (picnic/tailgate style)
- Cash prizes for top team and Individual
- Raffle prizes
- Shotgun Raffle.
Lunch will be provided before the shoot, starting at 11:30 a.m. There will be a cash bar available after the shooting portion of the program concludes. No alcohol will be served until you have completed the shooting portion of the outing. Prizes will be awarded following the completion of the day's shoot.
Don't Delay. Assemble your Teams Today!
Event information is available here.
Registration Information is available here.
##SHARELINKS##
|
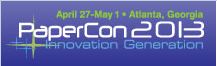
A Call for Papers has been issued for PaperCon 2013. Theme is "Innovation Generation."
After record attendance in 2012, PaperCon will again bring together CEOs, mill managers, superintendents, scientists, process engineers, and suppliers for the largest pulp and paper technical program in the world. The event will take place April 27 to May 1 in Atlanta, Ga., USA. Learn more about PaperCon 2013.
For 2013, PaperCon is pleased to welcome the Tissue360 Forum, NETInc (Innovative Nonwovens Conference), RPTA (Recycled Paperboard Technical Association) P-T Seminar and the OpEx Reliability Workshop. Each of these events is open to full PaperCon registrants and papers in these areas are welcome.
Calls for Papers and Posters have been issued. The conference theme is Innovation Generation, and authors are encouraged to include this within their papers. Topics under consideration include mill management, papermaking, coating, tissue, nonwovens, and recycled paperboard. Paper company personnel, suppliers, academics, and students are strongly encouraged to submit their ideas for papers, posters, or roundtable discussions.
Papermakers Program:
The Papermakers Program encourages topics on paper machine performance evaluations, papermaking fundamentals, product/process optimization, recycled paperboard, tissue making (Tissue360 Forum), and the RPTA P-T Seminar. The deadline for submission of abstracts is November 20, 2012. Abstracts for panel discussions and roundtables are welcome. See Papermakers Program Call for Papers.
Coating and Graphic Arts Program:
The Coating and Graphic Arts Program will focus on The Future of Print and its Demands on Paper and Coatings. The deadline for extended abstracts for this program is Oct. 16, 2012. See the Coating and Graphic Arts Program Call for Papers.
All abstracts must be submitted using TAPPI's Speaker Management System for consideration by the TAPPI and RPTA program committees.
##SHARELINKS##
|
You're invited to the 7th Annual Pacific Section Golf Tournament! This event will be held on September 28, 2012 (Friday). Start time is 1:00 p.m. at the Lewis River Golf Course.
The tournament format is a Modified Shotgun Start, four-person scramble with 144 spots open - First Come/First Serve. The entry fee is $125/person, which includes green fees, cart, two beverage tickets, prizes, a meal afterwards, and most of all... lots of fun!
Awards: 1st Place Team, 2nd Place Team, 3rd Place Team, M/W Longest Drive, KP, Longest Putt. Also enjoy door prizes and a raffle!
Proceeds go to the Pacific Section TAPPI scholarship fund!
Questions? Contact Vince Hochanadel via phone (360) 901-1680 or via email: vince.hochanadel@gmail.com.
Additional details and the registration form can be found here on the TAPPI website.
##SHARELINKS##
|
On Nov. 7-9, 2012, TAPPI will conduct its Tissue Runnability Course in Neenah, Wi., USA.
This special course is being taught by technical experts in each area of the machine from wet end operations through creping and process control. The experienced, highly qualified faculty for this course will provide a thorough understanding of the entire tissue making process and current best practices in each area.
Wednesday's (November 7) classes will focus on stock preparation and wet end operations, while Tuesday's (November 8) classes cover pressing, drying, and doctoring. Wednesday (November 9) classes examine technologies and latest developments in hoods, TAD (through-air drying), and other dynamics of the tissue machine dry end,
The 2012 TAPPI Tissue Runnability Course is designed for process engineers, machine supervisors, and reliability professionals who have to maximize uptime and saleable production. It is also an excellent tutorial for suppliers who support tissue making customers. It will help attendees:
- Improve tissue quality and consistency
- Understand contributors to waste and downtime
- Learn reliability and maintenance best practices
- Diagnose and troubleshoot problems quickly.
After successfully completing this course, attendees will specifically be able to:
- Diagnose the impact of recycled furnishes on tissue properties
- Make changes to wet-end chemistry to improve machine operations
- Improve cleaning and conditioning of fabrics
- Troubleshoot runnability problems in the press, Yankee, and creping systems
- Identify improvement opportunities on the dry end
- Pinpoint productivity opportunities in Yankee steam, coating, and hood systems.
TAPPI will award CEU credits to participants who attend at least 80% of the educational sessions and complete a final program evaluation.
The 2012 Tissue Runnabilitry Course includes advanced process instruction. If you are looking for an introductory-intermediate tissue course, consider the upcoming 2012 Tissue Properties and Manufacturing Course at TAPPI Headquarters in Norcross, Ga., USA, on August 15-16.
Attendance for the 2012 TAPPI Tissue Runnability Course is limited, so please register today at the course website.
##SHARELINKS##
|
TAPPI's International Bioenergy and BioProducts Conference, October 17-19, 2012 in Savannah, Ga., USA will focus on advancements and commercialization of bioconversions that leverage the forest products manufacturing infrastructure, providing you with a deeper analysis of the technology and economics involved in commercializing biorefineries. Click here to learn more about the IBBC full technical program.
Keynote Speakers:
- Paul Spindler, VP of Technology at Catchlight
- John B. Crowe, Chairman and CEO, Buckeye Technologies, Inc.
In addition, IBBC will include technical presentations, expert panels, case studies, and reports from projects that address:
- Feedstock and harvesting improvements to increase yield and quality of biomass
- Bioconversion technologies for wood and biomass
- Production of chemicals and transportation fuels from wood and biomass
- Commercial bioenergy products using woody biomass
- Tools for evaluating bioenergy projects.
IBBC will be co-located with the TAPPI PEERS Conference, creating a value-added opportunity for participants to expand their learning, networking, and resources by attending both events.
Exhibit and Sponsorship opportunities are available. Contact Shane Holt via e-mail or at 800.369.6220, ext. 3345 for more information.
##SHARELINKS##
|
Operating Excellence (OpEx) Maintenance and Reliability Seminar at PEERS
This is a first-time program for the 2012 TAPPI PEERS Conference.
Maintenance and reliability continue to be critical to the efficient operation of pulp and paper mills worldwide, just behind fiber and labor as top production cost factors.
This one-day seminar explores the latest reliability strategies today's mills are implementing to stay in-tune and competitive under progressively lean operating conditions.
The OpEx Maintenance and Reliability Track, included in your PEERS registration at no extra cost, is part of the Engineering Program.
If you are only interested in attending the OpEx Track, select the Single Day PEERS Registration for Thursday, October 18. This year's PEERS Conference includes a full program of educational opportunities for maintenance and reliability personnel, including:
- Sunday, Oct. 14: Fixed Equipment Maintenance Optimization System Course (Additional Fee)
- Monday, Oct. 15 - Wednesday, Oct. 17: Corrosion & Materials Engineering Track
- Thursday, Oct. 18: OpEx Maintenance and Reliability Track.
In addition, 2012 TAPPI PEERS Conference, October 14-17 in Savannah, Ga., features a detailed technical program. Five programming tracks of peer-reviewed sessions, Pulping, Engineering, Environmental, Recycling and Sustainability, will answer the most pressing business and technical questions faced by pulp and paper companies as they manage raw materials, assets, regulatory requirements and production assets.
Register now and save.
The 2012 TAPPI PEERS Conference will be co-located with the 2012 International Bioenergy and Bioproducts Conference, creating a value-added opportunity for you to expand your learning, networking, and resources by attending both events.
See you in Savannah!
##SHARELINKS##
|
Attend the Fixed Equipment Maintenance Optimization System Workshop (FEMOS)
Sunday, October 14, 2012; 8:00 a.m. - 5:00 p.m.
Mills annually spend millions of dollars inspecting, repairing, and recovering from unexpected leaks in boiler tubes, tanks, pressure vessels, exposed and buried pipes, stacks, bleach towers, etc. – learn how to substantially reduce those costs! Corrosion Probe Inc.'s FEMOS Workshop training shows maintenance staff how to rationally manage the mechanical (containment) integrity of all types of fixed equipment with a simple, rigorous system utilizing comparable disciplines and procedures promoted by vendors specializing in maintenance of rotating equipment.
What will you learn?
The workshop teaches attendees how to implement a mill-specific program by using a transparent and disciplined process to systematically design the right inspection plan for each major piece of fixed equipment based on its materials of construction, present condition and service conditions. The basic concept employs proven, high-value practices from refining and petrochemical industries for risk-based inspection, customizing inspection plans to possible damage mechanisms and using fitness-for-service engineering assessments to define damage limits.
Who is leading the workshop?
Corrosion Probe Inc.'s experienced and renowned TAPPI participants Dave Bennett, David Crowe, and Doug Sherman, will train up to 20 people in a one-day (6-hour) workshop. Training is presented so attendees can use their new knowledge to immediately implement FEMOS at their mill. Many working examples are provided and students are invited to bring their mill's costliest fixed equipment inspection/ maintenance concern for case analysis.
The workshop takes place just before the TAPPI PEERS and IBBC conferences so those attending the FEMOS workshop can also attend these important events.
Learn more about PEERS 2012...
##SHARELINKS##
|
Gain a better understanding of kraft pulping operations and the effect of process on quality.
An encore, one-day presentation of the popular Intro to Kraft Pulping Workshop will be held in conjunction with the 2012 TAPPI PEERS Conference, October 14-17 in Savannah, Ga., USA. This workshop, held on Saturday, October 13, will be lead by Dr. Michael J. Kocurek, Professor Emeritus of Paper Science and Engineering at North Carolina State University.
The Intro to Kraft Pulping Workshop is a condensed version of the pulping portion of the full course. The overall course objective is to give participants increased understanding of kraft pulping operations, awareness of how one part of the process affects other operations, and the effect of processes on kraft pulp quality.
Learn more about this workshop.
Pulp and Paper Companies Get Discounted Registration!
TAPPI offers a discounted registration to pulp and paper mills and their corporate offices to attend the PEERS Conference. Bring an unlimited number from your mill or office to visit for one day, one hour, or just to drop in and see the Trade Fair! Learn more.
Register Now for PEERS and Save!
The 2012 TAPPI PEERS Conference will be co-located with the International Bioenergy and Bioproducts Conference, creating a value-added opportunity for you to expand your learning, networking and resources by attending both events.
See you in Savannah!
##SHARELINKS##
|
Are you someone who could benefit from an overview of the entire pulping and paper-making process?
If so, The 2012 TAPPI Hands-On Workshop for Pulp and Paper Basics might be the perfect course for you to learn about the fundamental processes and operations of the pulping and paper-making industry. This year's workshop runs from October 1-5 at North Carolina State University in Raleigh, North Carolina, USA. Reserve your place now so that you can:
- Find out how different processes affect paper properties
- Perform hands-on laboratory experiments to support your understanding of the process
- Run a pilot plant paper machine
- Solidify your knowledge from close interaction with professors in small, interactive groups
Be among the first 32 people to register for this five-day workshop, and you will gain an invaluable overview of pulping, bleaching, chemical recovery, recycling, paper-making and converting. You'll receive course notes, an accompanying CD-ROM, and your own polo shirt. You will also have the opportunity to earn 3.7 CEUs.
This workshop is ideal for new process engineers, manufacturing operators and technicians, sales and service personnel, machine operators, and maintenance personnel. Everyone who wants a better understanding of the basic operation of the pulp and paper business will benefit from this course.
This course typically fills quickly, so don't wait long.
We look forward to seeing you in Raleigh this October!
##SHARELINKS##
|
Frank Romano to Keynote at PaperCon 2013
Frank Romano, Professor Emeritus, Rochester Institute of Technology, will Keynote at Papercon 2013 on Sunday, April 21. Focusing on "Innovation and the Future of Print," Romano will kick-off PaperCon's Coating and Graphic Arts Program.
Romano's career has spanned an impressive 53 years in the printing and publishing industries. Many know him as the editor of the International Paper "Pocket Pal" for 30 years, or have read one of the thousands of articles he has written. He is the author of 52 books, including the 10,000-term Encyclopedia of Graphic Communications (with Richard Romano), the standard reference in the field.
Learn more about Romano.
PaperCon 2013 will take place April 27 through May 1 in Atlanta, Ga., USA. Designed by industry professionals, PaperCon brings together CEOs, mill managers, superintendents, scientists, process engineers and suppliers for the largest pulp and paper technical program in the world. No other event provides such a comprehensive program, networking opportunities, and trade fair among such a distinguished group of industry leaders.
Learn more about PaperCon 2013.
Registration information, including special mill reservation deals, are now available at the PaperCon website.
##SHARELINKS##
|
The 20 volumes of Papermaking Science and Technology bookseries cover the entire paper manufacturing process from wood raw material to end product, providing a basis for university-level education, for updating training courses, and as handbooks for the industry. The bookseries has been updated and second editions are now available. TAPPI members can place an order by contacting The Finnish Paper Engineers' Association. Please contact Mary Anne Cauthen, Member Group Coordinator, at +1.770.209.7352 or by e-mail at MCauthen@TAPPI.org
These books can be purchased individually or as a set.
This 20 volume set includes:
- Volume 1 - Economics of the Pulp and Paper Industry
- Volume 2 - Forest Resources and Sustainable Management
- Volume 3 - Forest Products Chemistry
- Volume 4 - Papermaking Chemistry
- Volume 5 - Mechanical Pulping
- Volume 6, part 1 - Chemical Pulping Part 1, Fiber Chemistry and Technology
- Volume 6, part 2 - Chemical Pulping Part 2, Recovery of Chemicals and Energy
- Volume 7 - Recycled Fiber and Deinking
- Volume 8 - Papermaking Part 1, Stock Preparation and Wet End
- Volume 9 - Papermaking Part 2, Drying
- Volume 10 - Papermaking Part 3, Finishing
- Volume 11 - Pigment Coating and Surface Sizing of Paper
- Volume 12 - Paper and Paperboard Converting
- Volume 13 - Print Media - Principles, Processes, and Quality
- Volume 14 - Process and Maintenance Management
- Volume 15 - Materials, Corrosion Prevention and Maintenance
- Volume 16 - Paper Physics
- Volume 17 - Pulp and Paper Testing
- Volume 18 - Paper and Board Grades
- Volume 19 - Environmental Management and Control
- Volume 20 - Biorefining of Forest Resources
##SHARELINKS##
|
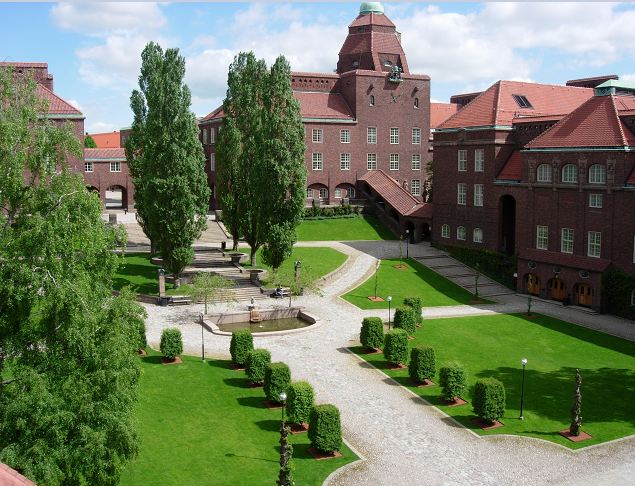 The 2013 TAPPI International Conference on Nanotechnology for Renewable Materials will be held July 24-27, 2013, on the KTH Royal Institute of Technology campus in Stockholm, Sweden. Industry experts, scientists, health and safety specialists, legal and government policy makers, as well as the field's leading researchers will discuss the latest in nanotechnology research and development.
The 2013 Technical Program Committee has issued a Call for Papers inviting contributions from participants working in research, development, and deployment of renewable nanomaterials.
Abstracts are due by December 3, 2012.
##SHARELINKS##
|
Make your plans now to join a host of professionals from industry, universities and research institutes at the 14th TAPPI European PLACE Conference, which will be held May 6-8, 2013, at the Swissotel in Dresden, Germany.
The Call for Papers is now officially open. Submit your abstract and take an active role in this not-to-miss event!
##SHARELINKS##
|
|
|