 |
|
Weekly Spotlight
Miami, Fla., USA-based private equity firm H.I.G. Capital LLC this week acquired Caraustar Industries Inc., Austell, Ga., USA
Learn More...
|
Sappi Fine Paper North America (SFPNA), Boston, Mass., USA, has announced the 2013 Call for Entries for Ideas that Matter, an annual, innovative grant program that supports and transforms the creative ideas of designers into a powerful force for social good
Learn More...
|
This year, Kimberly-Clark, Dallas, Texas, USA, celebrates the 21st year of the Bright Futures program and is awarding college scholarships totaling $1.26 million to 63 children of K-C employees across 17 states and Canada
Learn More...
|
Below is the latest listing of job openings in the TAPPI Career Center
Learn More...
|
Market Roundup
U.S. Containerboard production rose 6.8% over February 2013 but fell 2.6% over the same month last year
Learn More...
|
Total U.S. kraft paper shipments were 132,600 tons in March, an increase of 11.6% compared with the prior month
Learn More...
|
Pulp & Paper
Empresas CMPC SA (CMPC), Santiago, Chile, a Latin American forestry, pulp, paper, tissue, and packaging products producer, announced this week that its board of directors has set the price for the company's forthcoming capital raise
Learn More...
|
Georgia-Pacific, Atlanta, Ga., USA, this week reported that an entity it controls, GP Cellulose Group LLC, has launched its previously announced tender offer for all of the outstanding shares of common stock of Buckeye Technologies, Memphis, Tenn., at $37.50 per share net to the holder in cash
Learn More...
|
Japanese Tissue Producer Marutomi has ordered a new Toscotec, Italy, steel yankee dryer to replace the existing 12 ft. cast iron yankee at its Fujine mill, located in Fuji, Shizuoka Prefecture
Learn More...
|
Norske Skog, Norway, after installing a Voith (Germany) EvoFlow P suction press roll on PM 4 at its Bruck mill in Styria, Austria, reports that it has been able to increase dryness by 0.5%
Learn More...
|
Schönfelder Papierfabrik, Annaberg-Buchholz, Germany, has been running its new Voith stock preparation system for several months now, and is reportedly attaining high energy efficiency
Learn More...
|
Tembec, Montreal, Que., Canada, this week reported that it supports the Guidelines for Sustainable Paper Products released April 24 by GreenBlue that "provide the common language and framework the paper products industry needs to take practical and profitable steps toward sustainability."
Learn More...
|
UPM, Helsinki, Finland, reports that it has completed the sale of assets and part of the land of the UPM Stracel paper mill site to Blue Paper SAS, the joint venture company of VPK Packaging Group NV and Klingele Papierwerke
Learn More...
|
West Fraser, Vancouver, B.C., Canada, has announced voting results from its Annual General Meeting held Tuesday, April 30, in Quesnel, B.C. Canada
Learn More...
|
United Steelworkers (USW), Philadelphia, Pa., USA, reports that its members at Wausau Paper's Rhinelander, Wis., and Mosinee, Wis., mills and the Thilmany mill in Kaukauna, Wis., have ratified a new collective bargaining agreement with KPS Capital Partners in anticipation of the private equity firm successfully creating the largest specialty paper company in North America
Learn More...
|
Containerboard/Packaging
To satisfy one of the conditions set by the EU Commission for approval of the combination between Billerud and Korsnäs (Sweden), an agreement has been signed with SwedPaper AB concerning divestment of a paper machine (PM 2) at the BillerudKorsnäs Gävle mill in Sweden
Learn More...
|
Boise Inc., Boise, Idaho, USA, reports that it will invest $110-$120 million to convert an idled paper machine at its Deridder, La., mill to produce packaging grades and will close two paper machines at its International Falls, Minn., mill no later than the fourth quarter of this year
Learn More...
|
Smurfit Kappa, Ireland, has moved up its earlier announced plans to close two existing containerboard machines at its papermaking facility at Townsend Hook in Kent, U.K. and replace them with a single, more modern machine
Learn More...
|
Nonwovens
The Journal of Industrial Textiles has published the results of a study conducted by Texas Tech University and Enercon Industries, Menomonee Falls, Wis., USA, that determined when spunbond polypropylene nonwoven fabrics are pre-treated with atmospheric plasma it increases the breathability of the fabric
Learn More...
|
Miller Weldmaster, Navarre, Ohio, USA, showcased its T300 Filter Line at the recent IDEA show in Miami, Fla., and demonstrated how the company can meet the production needs of nonwovens manufacturers
Learn More...
|
|
New Products
The uprooter is a boom-mounted device fitted to a harvester. It uproots seedlings from the ground
Learn More...
|
Smurfit Kappa Bag-in-Box, Ireland, will showcase its complete range of new and modern flexible packaging, the Pouch-Up®, at the London International Wine Fair (LIWF) & Distil on May 20 – 22
Learn More...
|
Published Pricing
Ahlstrom, Finland, this week announced price increase on its specialty paper materials produced by the Label and Processing business
Learn More...
|
Metsä Fibre, Finland, announced this week that it will increase the price of Botnia Nordic Pine NBSK (northern bleached softwood kraft) pulp in Europe, effective immediately
Learn More...
|
Energy
California, USA-based Advanced Biofuels Corp., has bought a legacy 7 million gal/yr ethanol plant in Moses Lake, Wash., with plans to retrofit existing systems and install new pretreatment process equipment, converting the facility into a 6 million gal/yr advanced ethanol facility
Learn More...
|
People
Melissa Stevens was promoted to VP, Sales, Michelle Carpenter was promoted to VP, Environmental and Energy Stewardship, and Beth Reardon was promoted to regional sales manager, Midwest
Learn More...
|
TAPPI News
What are cellulose nanomaterials? What potential do they offer our industry? Register for a free webinar to be conducted tomorrow, Friday, May 10, at 11:00 a.m., EST to learn about these new materials and their applications.
Learn More...
|
The popular Paper Machine Operations Course, returning to the TAPPI Training Facility on May 21-23, has proven to be one of the best ways to get a good overview of paper mill operations.
Learn More...
|
Register by May 11 to save for one of the 25 seats in this popular course. Learn the principals and foundations of innovative wet end chemistry.
Learn More...
|
The CBU Student Chapter has elected new officers for the 2013 -14 academic year.
Learn More...
|
Conference takes place May 30-31 in Shanghai, China.
Learn More...
|
Don't miss your chance to attend this popular course June 25-27, which sold out last year. Register by May 27 and save up to $200.
Learn More...
|
This course is ideal for engineers and other technical people who need a better understanding of wet end chemistry. The course is designed for anyone that is involved with wet end operations as well as anyone training staff working in this area.
Learn More...
|
Learn how to enhance your Operator Training Program from some of the leading experts in the Industry.
Learn More...
|
Nominations for the major TAPPI 2014 awards are due by August 1, 2013.
Learn More...
|
Popular Paper Recycling Conference series hits Asia for its launch this month, taking place in Shanghai, China, with a full program featuring Deloitte China, Smurfit Kappa, and Ekman Recycling.
Learn More...
|
This once-in-a-lifetime event will expand public awareness, foster further connection, and provide outstanding opportunities for collaboration, growth, and investment in our future for all of those involved.
Learn More...
|
The TAPPI Centennial Celebration beginning in 2015 will be a multi-year series of outreach events and educational offerings showcasing the proud history and promising future of the global pulp, paper, packaging and related industries. BUCKMAN is the first company to support the Centennial Celebration at the $100,000 level.
Learn More...
|
As TAPPI's 100th year approaches, we are looking for donations to the TAPPI Library.
Learn More...
|
Patrice Mangin has been named winner of the 2013 TAPPI Research & Development Technical Award and the William H. Aiken Prize.
Learn More...
|
TAPPI's 2013 International Conference on Nanotechnology for Renewable Materials, June 24-27 in Stockholm, Sweden, features the largest program to date, with more than 80 technical presentations.
Learn More...
|
PPSA will host its 70th Annual Safety and Health Conference - "The Human Element of Safety," June 9-12, 2013, in Williamsburg, Va., USA.
Learn More...
|
PPMA has launched its first ever Best Place to Work Award, which is open to all companies in the forest products industry and will look not only at corporate life but also at how employees feel about their work environments. .
Learn More...
|
The 8th Annual International Conference on Nanotechnology for Renewable Materials is scheduled for June 24-27, 2013, in Stockholm, Sweden, at the KTH Royal Institute of Stockholm.
Learn More...
|
Members receive a special discount on these best selling publications from 2012.
Learn More...
|
Register now for the class where you will learn to understand OSHA, avoiding citations that could cost millions of dollars. Teach your company how to lower fatalities and near-misses.
Learn More...
|
|
Find us on Facebook
Network with us on LinkedIn
Follow us on Twitter
|
Weekly Spotlight
Miami, Fla., USA-based private equity firm H.I.G. Capital LLC this week acquired Caraustar Industries Inc., Austell, Ga., USA. Caraustar was majority owned by private investment funds managed by Wayzata Investment Partners, Wayzata, Minn.
Caraustar is one of North America's largest integrated manufacturers and converters of 100% recycled paperboard and converted paperboard products. It serves end-use markets in tube and core, folding carton, gypsum facing paper, and specialty paperboard products. The company services its diversified customer base through a large network of facilities across North America.
In 2009, Wayzata led a group of bondholders in a pre-packaged chapter 11 process in which Wayzata-managed funds acquired a majority ownership stake in Caraustar. The Wayzata led restructuring significantly reduced Caraustar's debt burden and dramatically improved Caraustar's balance sheet. Since exiting bankruptcy, Caraustar has used its stronger balance sheet to drive operational improvement and to increase profitability.
Mike Patton, CEO of Caraustar, said that "we believe this is an exciting time in our industry, and I am pleased to have H.I.G.'s support to help us achieve our growth plan. We look forward to working with H.I.G. to build upon our reputation as a customer-oriented market leader."
Tenno Tsai, a principal of H.I.G., noted that "we are very excited about the Caraustar opportunity. Caraustar is a market leader with a blue chip customer base, broad geographic footprint, and an efficient, high quality manufacturing base. We believe there are numerous market opportunities going forward and we look forward to supporting Mike and his team in achieving continued growth."
Back To Top
|
Sappi Fine Paper North America (SFPNA), Boston, Mass., USA, has announced the 2013 Call for Entries for Ideas that Matter, an annual, innovative grant program that supports and transforms the creative ideas of designers into a powerful force for social good. Fourteen years ago, Sappi established the Ideas that Matter grant program to recognize and support designers who use their skills and expertise to solve communications problems for a wide range of charitable activities.
Sappi says that it has witnessed this "world-changing work" first hand and remains committed to the belief that "good ideas inspire people to take action, great ideas change the world."
Ideas that Matter remains the only grant program of its kind in the industry, the company notes. Since 1999, Sappi has funded more than 500 nonprofit projects, contributing more than $12 million worldwide to causes that enhance people's lives, communities, and the planet as a whole. Since the program's inception, Ideas that Matter funded projects have addressed societal issues from diversity and human rights campaigns to projects that focus on health and youth development. In tracking the program's long-term success, Sappi estimates that these projects have directly impacted the lives and environments of people and communities across 24 states and 15 countries.
Each project concept and design entry to Ideas that Matter is evaluated on creativity, potential effectiveness, and practicality of the implementation plan by an annually selected, independent panel of judges comprised of leaders and influencers in the design industry.
Individual designers, design firms, agencies, in-house corporate design departments, design instructors, individual design students, and design student groups can apply for an Ideas that Matter grant. The designer or the nonprofit must be based in North America. Grant awards range from $5,000 to $50,000 per project. At least a portion of the project must be printed, though additional elements may include a variety of communication mediums. And, for the first time in 2013, proposals may include up to 10% of the total budget as an honorarium for the applying designer or design firm.
An entry form and more information about Ideas that Matter can be obtained online, or by calling 800-882-4332. Applications for proposals must be postmarked by July 19. The winners will be announced in September.
Back To Top
|
This year, Kimberly-Clark, Dallas, Texas, USA, celebrates the 21st year of the Bright Futures program and is awarding college scholarships totaling $1.26 million to 63 children of K-C employees across 17 states and Canada. Bright Futures scholarship grants are worth up to $20,000, or $5,000 per school year, for full-time students attending accredited colleges and universities. Since its inception, the program has awarded more than $35 million in scholarships to more than 1,800 students.
Recipients were chosen based on academic achievement, leadership, work experience, and involvement in extracurricular activities.
"Kimberly-Clark is pleased to be able to offer a program like Bright Futures Scholars to the children of our employees," said Tom Falk, chairman and CEO of Kimberly-Clark. "There is no more important investment we can make than in our next generation of leaders. We wish them all the best with their college experience and beyond."
The average GPA for this year's scholarship class is 3.94, and awardees will attend such top colleges and universities as Harvard, Duke, Columbia, Cornell, and Stanford. Past scholarship recipients have gone on to pursue successful careers in medicine, education, the armed forces, and engineering.
More information about this year's award recipients is available online.
Back To Top
|
Below is the latest listing of job openings in the TAPPI Career Center. The current listing includes job openings for a variety of positions including senior specialist/advisor in corrosion and materials, paper materials engineer, paper coating specialist, sales manager, piping designer, and strategic accounts manager. Specific job openings at companies and locations in the TAPPI Career Center include:
Employer |
Title |
Location |
Albemarle Corp. |
Sr. Specialist/Advisor |
Baton Rouge, La. |
Dart Container |
Paper Materials Engineer |
Chicago, Ill. |
EcoSynthetix |
Sales Director (S/E U.S.) |
Lansing, Mich. |
EcoSynthetix |
Paper Coating Specialist |
Burlington, Ont., Canada |
EcoSynthetix |
Sales Manager (Europe) |
|
Minerals Technologies Inc. |
Strategic Account Manager |
|
Robins & Morton |
Piping Designer |
Morrisville, N.C. |
Sappi Fine Paper |
Basepaper Project Leader |
Westbrook, Maine |
More information about these jobs is available online.
Back To Top
|
Market Roundup
U.S. Containerboard production rose 6.8% over February 2013 but fell 2.6% over the same month last year, according to the AF&PA (Washington, D.C., USA) March 2013 U.S. Containerboard Statistics Report released this past week. The month-over-month average daily production decreased 3.5%.
The containerboard operating rate for March 2013 lost 3.4 points from February 2013, from 96.2% to 92.8%.
Back To Top
|
Total U.S. kraft paper shipments were 132,600 tons in March, an increase of 11.6% compared with the prior month, according to the AF&PA (Washington, D.C., USA) March 2013 Kraft Paper Report published this week. Bleached kraft paper shipments decreased year-over-year 1.3%, and the 7.2% year-over-year decline in unbleached kraft paper shipments were enough to bring overall kraft paper shipments down 6.5% year-over-year.
Total month-end inventory increased 0.4% to 71,600 tons in March compared with February 2013 month-end inventories.
Back To Top
|
Pulp & Paper
Empresas CMPC SA (CMPC), Santiago, Chile, a Latin American forestry, pulp, paper, tissue, and packaging products producer, announced this week that its board of directors has set the price for the company's forthcoming capital raise. The capital raise of up to 155,602,948 shares will be priced at CLP 1,480 ($3.1237) per share during the preferential rights period, when shareholders of record as of May 3 may subscribe to the offering in a fixed proportion to their holdings.
The preferential rights period will begin on May 9 and conclude on June 8. The Matte Group, CMPC's controlling shareholder, has stated its intention to subscribe to the offering in proportion to its holdings.
The capital raise marks the first steps of the previously announced financing package for CMPC's planned expansion of the Guaiba pulp facility in the state of Rio Grande do Sul, Brazil. Additional steps in the financing package may include a bond offering, the sale of non-core assets including the company's 7.7% stake in Bicecorp S.A., together with some real estate assets, the use of a BRL $2,510 million (approximately $1.2 billion) credit facility with Brazilian development bank BNDES and, if it is deemed necessary, a potential second capital raise of up to $250 million.
The expansion of the Guaiba mill will increase CMPC's pulp production capacity by approximately 1.3 million metric tpy to 4.1 million metric tpy, helping the company double its share of the global pulp market. Total investment in the project will be approximately $2.1 billion.
Shareholders approved the capital increase at an extraordinary shareholders meeting on January 24. The pricing of the transaction was fixed at a meeting of the board of directors on April 19.
Back To Top
|
Georgia-Pacific, Atlanta, Ga., USA, this week reported that an entity it controls, GP Cellulose Group LLC, has launched its previously announced tender offer for all of the outstanding shares of common stock of Buckeye Technologies, Memphis, Tenn., at $37.50 per share net to the holder in cash. G-P had announced the merger agreement on April 24. Buckeye's board unanimously approved the terms of the merger agreement, including the tender offer, and recommended that stockholders tender their shares.
Under terms of the merger agreement, after the completion of the tender offer and the satisfaction or waiver of all conditions, Buckeye will merge into G-P's GP Cellulose Group, and all outstanding shares of Buckeye Technologies' common stock, other than shares held by G-P, GP Cellulose Group, or Buckeye, or Buckeye share holders who have and validly exercise appraisal rights under Delaware law, will be cancelled and converted into the right to receive $37.50 per share, net to the holder in cash.
The completion of the tender offer is subject to, among other things, the expiration or termination of any waiting period under the Hart-Scott-Rodino Antitrust Improvements Act, the receipt of other required regulatory approvals, and other customary closing conditions, and requires at least 75% of the outstanding shares of Buckeye common stock on a fully-diluted basis to be tendered, consistent with the threshold for approval of a merger specified in Buckeye's certificate of incorporation. The transaction is not conditioned on financing.
The tender offer and withdrawal rights are scheduled to expire at midnight New York City (EDT) time on June 4, unless extended or earlier terminated. Buckeye' directors and executive officers, who collectively held 3.6% of the outstanding shares of common stock of the company as of April 24, have agreed to tender their shares in the offer.
Back To Top
|
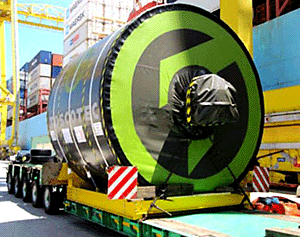 Japanese Tissue Producer Marutomi has ordered a new Toscotec, Italy, steel yankee dryer to replace the existing 12 ft. cast iron yankee at its Fujine mill, located in Fuji, Shizuoka Prefecture. The PM 1 tissue machine features a crescent former configuration with a sheet width at the pope reel of 3,140 mm.
The new Toscotec TT SYD-12FT will be installed by the end of 2013. The installation will allow the mill to increase its machine operating speed as well as achieve considerable energy savings. The new dryer will be supplied in accordance with local regulations and to the JIS (Japanese Boiler Association) standards. Related services also will be included in the scope of supply.
Founded in 1955 as a small mill with one 1.2-m wide tissue machine and nine employees, Marutomi now has a total of 13 tissue machines and, focusing mainly on bath tissue from recycled paper, has grown into one of Japan's largest producers of toilet rolls with a market share that it estimates to be around 14%. The mill uses only 100% recycled fiber with about 95% of its production being toilet tissue and the remaining 5% facial tissue.
Back To Top
|
Norske Skog, Norway, after installing a Voith (Germany) EvoFlow P suction press roll on PM 4 at its Bruck mill in Styria, Austria, reports that it has been able to increase dryness by 0.5%. Additionally, web draw after the third press as well as startup behavior of the felts were considerably enhanced and overall runnability has improved significantly. The Bruck mill, which Norske Skog acquired in January 1996, produces both lightweight coated (LWC) papers and newsprint.
The project began after Norse Skog Bruck commissioned Voith to examine whether dryness could be increased on its PM 4 by at least 0.5% after the fourth press. A stock analysis performed by Voith revealed that this could be achieved by increasing the line load in the first and second press. Since specifications of the existing suction press roll did not meet new requirements resulting from the increased line load, Norske Skog Bruck ordered the installation of a new EvoFlow P suction press roll with a SolarFlow high-capacity roll cover from Voith. This polyurethane roll cover features a modified groove dimension, helping to increase drainage significantly.
The new roll dimensions were designed for a nip load of 120 kN/m. The existing bearing housings were re-used. In addition, a mechanical deckle adjusting unit was installed in the low-vacuum zone.
PM 4 produces 275,000 metric tpy of LWC paper in a basis weight range of 34 to 54 gsm, with an operating speed of 1,400 m/min.
Back To Top
|
Schönfelder Papierfabrik, Annaberg-Buchholz, Germany, has been running its new Voith stock preparation system for several months now, and is reportedly attaining high energy efficiency. The new system is equipped with Voith LowEnergyFlotation (LEF), the latest generation of deinking flotation for removing ink and hydrophobic contaminants from recovered paper. The LEF, Voith notes, is easy to operate, requires low-maintenance, and is self-cleaning. The energy requirement is low at 10 to 15 kWh/day. The LEF thus offers the mill energy savings of up to 50% compared with the model it previously used.
Schönfelder Papierfabrik decided in favor of the new InfiltraDiscfilter in the BlueLine product line, along with other products. It guarantees that the pulp suspension is dewatered reliably and in an almost maintenance-free way. The core of the InfiltraDiscfilter is its bag-free BaglessPlus disc. This disc filter has an especially high capacity, since the filter surface is increased due to the corrugated surface. In addition, Schönfelder Papierfabrik chose a new dispersion system from Voith.
Holger Hampel, manager of Schönfelder Papierfabrik, emphasizes the success of this project: "On the basis of the very good quality and performance data achieved from the very beginning, we were able to approve the system without warranty runs. The result simply convinced us."
Schönfelder Papierfabrik produces more than 50,000 metric tpy of graphic paper and specialty paper on a working width of 3,300 mm in a basis weight range of 45 to 120 gsm. The product line includes various paper grades such as offset, office, volume, envelope, and improved newsprint as well as wallpaper base and liner paper.
Back To Top
|
Tembec, Montreal, Que., Canada, this week reported that it supports the Guidelines for Sustainable Paper Products released April 24 by GreenBlue that "provide the common language and framework the paper products industry needs to take practical and profitable steps toward sustainability." The Guidelines for Sustainable Paper Products is a joint effort of GreenBlue, a non-profit organization, and its Forest Products Working Group, made up of 10 companies including Tembec.
Other members of the Forest Products Working Group include Avery Dennison, Avon Products, Bank of America, Catalyst Paper, Domtar, HAVI Global Solutions, RR Donnelley, Sappi Fine Paper North America, and Staples.
The Guidelines provide common definitions of sustainable paper products, and outline what sustainability means for the paper products industry, for its customers, and for the community at large. They envision a paper products industry in which every product is designed to be safe and healthy for individuals and communities throughout its life cycle, is sourced responsibly, is manufactured, transported, and recycled using clean technology and renewable energy, and, after use, is effectively recovered and recycled to provide a valuable resource for the next generation of products.
"Tembec worked with GreenBlue and other industry partners on the Guidelines for Sustainable Paper Products because we believe adopting a common language and shared values about sustainability will help our industry embrace sustainable development," said Chris Black, Tembec EVP and president, Paper and Paper Pulp Group. "This continues Tembec's long history of working with a wide range of stakeholders to ensure responsible stewardship of resources and sustainable operations."
The Guidelines provide the information companies need to evaluate the sustainability of their operations, identify opportunities for profitable improvement, and integrate life cycle thinking and sustainable criteria into business strategies, Tembec explains. The Guidelines will evolve over time.
More information about the guidelines is available online.
Back To Top
|
UPM, Helsinki, Finland, reports that it has completed the sale of assets and part of the land of the UPM Stracel paper mill site to Blue Paper SAS, the joint venture company of VPK Packaging Group NV and Klingele Papierwerke. Blue Paper SAS will convert the mill to produce recycled fiber-based fluting and test liner. Production is expected to start after completing investments in the autumn of 2013. Blue Paper SAS is creating 130 new jobs at the mill that have been offered to former Stracel employees.
"We are very pleased that we have been able to find a good solution to the Stracel mill. Blue Paper offers a new industrial future for the site and a new opportunity for a number of Stracel employees. We want to express our thanks to all the parties involved in this process," said Jyrki Ovaska, president of the UPM Paper Business Group.
The sale of Stracel was part of UPM's plan to adjust its magazine paper and newsprint paper capacity to match the needs of its global customer base originally announced in August 2011. UPM stopped the production of coated magazine paper at the mill this past January 4.
Back To Top
|
West Fraser, Vancouver, B.C., Canada, has announced voting results from its Annual General Meeting held Tuesday, April 30, in Quesnel, B.C. Canada. A total of 37,370,292 Common shares and Class B common shares were voted at the meeting, representing 87% of the votes attached to all outstanding shares.
Shareholders voted in favor of all items of business before the meeting, including the election of all director nominees as follows: Hank Ketcham (97), Clark S. Binkley (99), J. Duncan Gibson (99), Samuel W. Ketcham (90), Harald H. Ludwig (90), Gerald J. Miller (99), Robert L. Phillips (90), Janice G. Rennie (86), and Ted Seraphim (99). Detailed voting results for the meeting are available online.
West Fraser is an integrated wood products company producing lumber, wood chips, LVL, MDF, plywood, pulp, and newsprint. The company has operations in western Canada and the southern U.S.
Back To Top
|
United Steelworkers (USW), Philadelphia, Pa., USA, reports that its members at Wausau Paper's Rhinelander, Wis., and Mosinee, Wis., mills and the Thilmany mill in Kaukauna, Wis., have ratified a new collective bargaining agreement with KPS Capital Partners in anticipation of the private equity firm successfully creating the largest specialty paper company in North America. USW local 2-00015 and local 01778 represent workers at the Rhinelander mill. USW local 2-00221 and local 2-00316 represent workers at the Mosinee mill. USW local 2-00020 represents workers at the Kaukauna mill. This agreement represents "a new beginning" for about 1,400 paper workers at these three mills, USW notes.
"We are proud of the leadership that our local unions have shown in bringing their respective memberships together to ratify this important deal in the specialty paper sector," said USW President Leo W. Gerard. "This particular piece of the industry still has enormous growth potential and has long been in need of a new strategic vision to capitalize on that opportunity."
"The overwhelming vote makes a powerful statement about how our members are committed to ensuring the long-term viability of these plants," said USW International VP Jon Geenen, who heads the union's paper sector.
The new four-year agreement includes wage increases, benefit improvements, and it locks in retirement security.
"The approach KPS took in working through these negotiations to create a world-class paper company should serve as a reminder to hostile, short-sighted venture capitalists—and even our own state government—that a big part of value creation is people sitting down together to solve difficult problems," said USW District 2 (Wisconsin and Michigan) Director Michael Bolton.
The USW is the largest industrial union in North America and has 850,000 members in the U.S., Canada, and the Caribbean. The union represents workers employed in metals, rubber, chemicals, paper, oil refining, atomic energy, and the service sector.
Back To Top
|
Containerboard/Packaging
To satisfy one of the conditions set by the EU Commission for approval of the combination between Billerud and Korsnäs (Sweden), an agreement has been signed with SwedPaper AB concerning divestment of a paper machine (PM 2) at the BillerudKorsnäs Gävle mill in Sweden. Production at PM 2 in 2012 accounted for approximately 2% of BillerudKorsnäs' total combined sales volume.
Under the agreement, PM 2 at the Gävle mill will be sold to SwedPaper. The machine produces kraft and sack paper. The PM 2 operation employs approximately 60 people, who will be offered employment with SwedPaper. Other operations at Gävle will not be affected by the sale and will remain in BillerudKorsnäs' ownership.
The parties have signed long-term commercial agreements, under which BillerudKorsnäs will inter alia supply input items such as pulp, steam, and water to SwedPaper. Pricing for pulp will be in line with the market. Under the conditions of the agreement, BillerudKorsnäs will sell SwedPaper an annual volume of pulp amounting to a maximum of 66 000 metric tons. Sales of pulp to PM 2 will be accounted for in the Packaging Paper Business Area. At BillerudKorsnäs, the operations of PM 2 have been accounted for under Other units.
The disposal will not in any way affect the synergy and cost-cutting program announced earlier for the BillerudKorsnäs Group. The transaction is conditional upon approval of the European Commission and from relevant authorities.
SwedPaper is a newly started company that has been established with the purpose to acquire PM 2. Behind SwedPaper are four private investors—Mikael Colebring, Peter Ekman, Lars-Åke Brännström och, and Lars-Eric Boreström (through their separate companies)—all with extensive experience in entrepreneurship, particularly in the paper industry. SwedPaper has reached an agreement with Ekman & Co. for the distribution of PM 2's products.
Back To Top
|
Boise Inc., Boise, Idaho, USA, reports that it will invest $110-$120 million to convert an idled paper machine at its Deridder, La., mill to produce packaging grades and will close two paper machines at its International Falls, Minn., mill no later than the fourth quarter of this year. Alexander Toeldte, president and CEO, noted that "we experienced unfavorable mix changes in our Packaging segment that partially offset the benefits of the fall 2012 linerboard price increase. In addition, decreasing prices for uncoated freesheet negatively affected our results in Paper.
The investment at Deridder involves the conversion of an idled newsprint machine to produce lightweight linerboard and corrugating medium. As part of the project, the mill also will install an OCC pulping facility. The investment adds approximately 270,000 tons of lightweight containerboard capacity to the company's system and allows it to optimize the product mix on it current linerboard machine, increasing the mill's overall containerboard output by approximately 300,000 tons. Boise is targeting a mid-2014 startup for the completed project, which is expected to create about 50 jobs.
"To improve the cost competitiveness of our Paper business, where we operate against the background of secularly declining demand for our products, we have made the difficult decision to close two paper machines and an off-machine coater at our International Falls mill. These closures will reduce our annual uncoated freesheet capacity by approximately 115,000 tons, or 9%, and will allow us to focus our efforts on key products and machines that drive our profitability, improve our cash flow, and enhance the overall competitiveness of our International Falls mill and our Paper business. This decision will result in the loss of approximately 300 jobs. We understand the impact this decision has on our dedicated employees, as well as the community of International Falls. We appreciate their efforts and support over the years," Toeldte said.
Back To Top
|
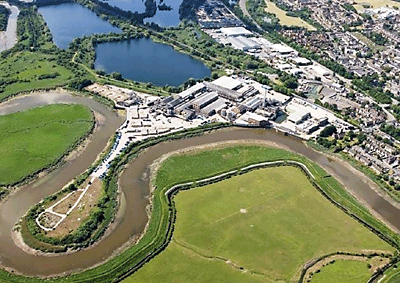 Smurfit Kappa, Ireland, has moved up its earlier announced plans to close two existing containerboard machines at its papermaking facility at Townsend Hook in Kent, U.K. and replace them with a single, more modern machine. The company was originally planning to close the two machines in 2014, with the new machine starting up in early 2015.
The company announced earlier this week, however, that the machines would be closing this July. The machines have a combined capacity of 250,000 metric tpy and are expected to close this July after a consultation process with employees, instead of 2014 as originally planned.
"We are bringing forward the closure to extend the training period for our workforce, advance the startup of the new paper machine, and increase the pace of the expected ramp-up. The facility will be rebuilt (using a machine acquired from the Cadidavid liquidator in 2011) into one 250,000 metric tpy, modern, lightweight machine that will be operational by the fourth quarter of 2014 rather than the first quarter of 2015," the company said.
Back To Top
|
Nonwovens
The Journal of Industrial Textiles has published the results of a study conducted by Texas Tech University and Enercon Industries, Menomonee Falls, Wis., USA, that determined when spunbond polypropylene nonwoven fabrics are pre-treated with atmospheric plasma it increases the breathability of the fabric. Atmospheric plasma treatment increases the number of pores and enlarges the pore size of the fabric, improving the diffusion of vapor between the filaments in the spunbond structure without compromising the barrier properties. These properties are significant within the medical industry when developing disposable medical clothing such as surgical masks, gowns, and drapes.
One of the most demanded properties of barrier fabrics for medical applications is the developments of a low cost non-woven material that is breathable, sterilizable, flexible, and resistant to blood and viral penetration.
Enercon's Plasma3™ is an in-line, dry, and continuous surface treatment process for web application. Its treatment techniques provide a fast, efficient, and eco-friendly breathability effect on nonwoven/textile surfaces.
Dr. Seshadri Ramkumar's group in the Nonwovens & Advanced Materials Laboratory and colleagues in the Departments of Chemistry and Biochemistry and Mechanical Engineering, Texas Tech University collaborated with Enercon to explore environmental friendly ways to enhance the breathability of nonwoven synthetic fabrics.
To view the full article, visit the Journal of Industrial Textiles (Volume 42 No 4) online. Those interested in scheduling an atmospheric plasma lab trial may contact Rory Wolf directly at 1-262-255-6070.
Enercon Industries Corp. is a manufacturer of equipment for the plastics, converting, and packaging industries. The company supplies custom built corona and atmospheric plasma treating systems, as well as induction cap sealing systems.
Back To Top
|
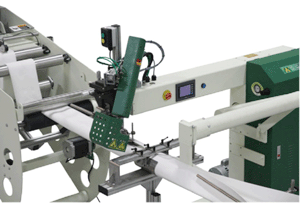 Miller Weldmaster, Navarre, Ohio, USA, showcased its T300 Filter Line at the recent IDEA show in Miami, Fla., and demonstrated how the company can meet the production needs of nonwovens manufacturers. Miller Weldmaster supplies several machines for the nonwoven industry. Each of these machines has features designed for robust product manufacturing, minimized production time, and material set-up with effortless machine operation, the company notes.
The T300 Filter Line unwinds, welds, and cuts filter tubes automatically with precision-controlled parameters. The Filter system can be equipped with an ultrasonic welder, allowing the manufacturing of tubes while simultaneously using an ultrasonic welder to close the ends. Miller Weldmaster also supplies cured-in-place welding and sewing systems to efficiently produce cured-in-place pipelines or rehabilitation tubes.
Miller Weldmaster has supplied rotary hot air, hot wedge, and impulse welding equipment to the industrial fabric and thermoplastics industries for 40 years.
Back To Top
|
New Products
UPM, Helsinbki, Finland, reports that it is the first user of a new uprooting method for the mechanical cleaning of sapling stands. The uprooter is a boom-mounted device fitted to a harvester. It uproots seedlings from the ground.
"Mechanical uprooting means removing coppice with the roots. It will reduce the number of new shoots, meaning that it often will no longer be necessary to make any pre-commercial thinning. At many sites, you may get straight from uprooting to first commercial thinning," explains Jyri Schildt, chief of forest management at UPM Forest.
UPM says that it can carry out mechanical uprooting when the ground is not frozen. The working period from May to October is longer than the manual cleaning period between midsummer and late August. As such, the uprooter lightens the workload during the busy midsummer forestry season, the company adds.
"UPM has developed this method for a long time, along with other active parties. We have carried out mechanical uprooting in company forests for almost a decade now. We have generated excellent results using this form of uprooting. As a result of this development, we are now able to offer this modern and cost-efficient method to private forest owners," says Jari Engström, sales manager at UPM Forest.
Mechanical uprooting has been developed and tested in North Karelia, the home of Pentin Paja, the company that manufactures the uprooters. Next summer, UPM will use three machines equipped with an uprooter in North Savonia, as well as around a dozen machines across the whole of Finland. The number of uprooters is expected to rapidly increase over the next few years.
"Uprooting is highly recommended for seedling stands, both from a silvicultural viewpoint and a financial one. When done at the right time, uprooting is quick and the results are good. If uprooting is performed a couple of years too late, there will be growth losses, the work will be much slower, and the costs will be higher," Schildt says.
Last year, in co-operation with Risutekniikka Ky, UPM introduced a new kind of planting machine, the first to include an automatic seedling feeder. Improving the productivity of mechanical forest management is based on automation, multi-tasking, and multi-tree handling.
"Mechanical forest management offers the benefits of standardized quality and increased profitability. Furthermore, the additional devices allow the forest machines to be used year round. Mechanical forest management is a view of the future. There will be fewer forest workers in the future, and many forest owners do not have the time or the skill to tend their forests themselves," Schildt explains.
Back To Top
|
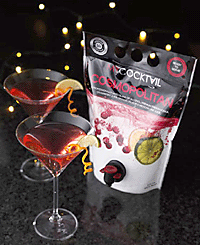 Smurfit Kappa Bag-in-Box, Ireland, will showcase its complete range of new and modern flexible packaging, the Pouch-Up®, at the London International Wine Fair (LIWF) & Distil on May 20 – 22. Available in single and double gusset and in several sizes, the Pouch-Up is designed for customers looking for an innovative packaging solution, and is particularly ideal for cocktails. It offers an attractive and modern design and is ideal for on-the-go consumption, Smurfit Kappa notes, adding that "environmentally aware consumers will also appreciate its low carbon footprint."
At this year's LIWF, the Smurfit Kappa team will offer tastings of the mojito, pinacolada, cosmopolitan, and more, all presented in Pouch-Up packaging, on Tuesday, May 21.
Back To Top
|
Published Pricing
Ahlstrom, Finland, this week announced price increase on its specialty paper materials produced by the Label and Processing business. Ahlstrom noted that the price increase will be made to compensate for the continued high cost of raw materials and energy. It will affect all Label and Processing products worldwide and will be effective for all shipments beginning July 1. The increase will up to 7% and the amount and timing will depend on the markets served, the product, and the agreements in place.
Products manufactured by Ahlstrom's Label and Processing business include graphic, packaging, processing, release, and label papers. The main end-use applications of these products are release liners, self-adhesive labels, metalized wet glue labels, flexible packaging, and repositionable notes. They are also used for the production of posters, abrasive materials, and furniture foils. These specialty papers are manufactured in Brazil, France, Germany, and Italy.
Back To Top
|
Metsä Fibre, Finland, announced this week that it will increase the price of Botnia Nordic Pine NBSK (northern bleached softwood kraft) pulp in Europe, effective immediately. The new price is $870 per metric ton, CIF Metsä Fibre's frequently used European ports of destination. All other terms and conditions remain unchanged.
Metsä Fibre has pulp mills in Joutseno, Kemi, Rauma, and Äänekoski in Finland. The combined annual production capacity of these four mills is 2.4 million metric tons of ECF bleached pulp. Including the pulps of its principal clients, the company's annual sales reach 3.3 million tons. Metsä Fibre also owns the Svir Timber sawmill in Podporozhye, Russia.
Back To Top
|
Energy
California, USA-based Advanced Biofuels Corp., has bought a legacy 7 million gal/yr ethanol plant in Moses Lake, Wash., with plans to retrofit existing systems and install new pretreatment process equipment, converting the facility into a 6 million gal/yr advanced ethanol facility, according to a report this past week by Ethanol Producer Magazine. Rhys Dale, VP and director of development for process providers Bio-Process Innovation Inc., says the company expects to produce 5 million gal/yr of cellulosic ethanol from wheat straw and an additional 1 million gal/yr from waste alcohol.
The Moses Lake project will be the first commercial application of the BPI biomass technology. The company was founded in the early 1980s by a group of Purdue University scientists, with Clark Dale serving as president and CEO, Ethanol Producer Magazine notes. BPI, West Lafayette, Ind., has developed processes for waste sugar streams, waste ethanol, and whey, as well as process technologies for the corn ethanol industry, including high gravity fermentation.
BPI describes its pretreatment process as low temperature steep delignification, which produces a concentrated cellulose/hemicellulose stream at low temperatures, pressures, and chemical loading levels. The soluble lignins are recovered while the cellulose/hemicellulose fraction is reportedly similar to paper pulp. BPI has developed a multi-stage continuous reactor separator that combines hydrolysis, fermentation, and separation of ethanol from biomass feedstocks. Concentrated ethanol beer or bio-solvents are stripped during the fermentation process. The C6 sugars are converted to ethanol while the C5s are separated for conversion to organic acids or biosolvents or used to produce single cell proteins.
BPI is currently developing a 1-tpd pilot facility as the final stages of financing are completed, Ethanol Producer Magazine reported. Financing should be in place within three to four months, and construction at Moses Lake should begin shortly after. The company projects that construction will take a year.
Back To Top
|
People
Mohawk, Cohoes, N.Y., USA, this past week announced three promotions and two new hires. Melissa Stevens was promoted to VP, Sales, Michelle Carpenter was promoted to VP, Environmental and Energy Stewardship, and Beth Reardon was promoted to regional sales manager, Midwest.
Mohawk also announced that it hired Pamela Reedstrom and Katherine Hoffman as digital specialists. Reedstrom and Hoffman will join a team of Mohawk Digital Specialists located throughout North America to oversee market development and grow sales of the company's digital papers and specialty substrate lines. Reedstrom will service the Southern California territory and Hoffman will service customers in New York, New Jersey, Philadelphia, Baltimore, Washington, D.C., and Virginia.
Mohawk is North America's largest privately-owned producer of fine papers and envelopes.
Back To Top
|
TAPPI News
What are cellulose nanomaterials? What potential do they offer our industry? Register for a free webinar to be conducted tomorrow, Friday, May 10, at 11:00 a.m. EST to learn about these new materials and their applications.
Sponsored by TAPPI's International Nanotechnology Division, Sean Ireland, manager of New Technologies and Market Ventures, Verso Paper Corp. and the Nano Division chair, will share how as we move forward in the 21st Century, there is a unique opportunity due to the demand in materials, energy, food, and water driven by world economics and populations. The potential is to open our minds and re-think our uses for trees in producing many of the materials we use today, from composites, batteries, super-capacitors, high-efficiency filters, reinforce polymers, bioplastics, coatings, sensors, flexible display, membranes and many other high-end products.
Sean will explain how this is coming into existence through the most widely available, environmentally friendly polymer on the planet – cellulose. By breaking down cellulose to nanoscale materials, we uncover unique properties, and the nanomaterials can be produced in large quantities for commercialization that will preserve existing jobs, allowing our mature industry to remain competitive and improving the environment.
Learn about the latest advances in renewable nanomaterials at TAPPI's 8th Annual International Conference on Nanotechnology for Renewable Materials to be held June 24-27, 2013, in Stockholm, Sweden. This year's program is the largest to date with more than 80 technical presentations.
Back To Top
|
The popular Paper Machine Operations Course is returning to the TAPPI Training Facility on May 21-23. This course has proven to be one of the best ways to get a good overview of the paper mill operations.
Led by Jim Atkins and a team of instructors, this course will provide participants with an improved understanding of the overall paper machine operation. Fundamental understanding of fiber properties and the way the mechanical components function on the paper machine will give the participant the tools needed to more quickly troubleshoot operational problems and improve paper machine operations and product quality.
Go to the course website to learn more and to reserve your space in this upcoming course.
This course in NOT intended for employees of tissue companies. Those interested in learning about tissue may be more interested in the TAPPI Tissue Runnability Course.
Back To Top
|
Register by May 11 to save for one of 25 seats in the popular TAPPI Introduction to Wet End Chemistry course.
Three industry-known instructors are focusing the three-day curriculum, June 11-13, on innovative wet end chemistry principals and foundations designed to help you reach higher yield, improve confidence in the use of papermaking chemicals, and to better troubleshoot.
View the Workshop Schedule to see the specific topics covered.
This introductory- to intermediate-level course is designed for those in pulp and paper manufacturing facilities with job responsibilities, such as chemical and process engineers, mill superintendents, research and development engineers, technology and chief chemists, R&D vice presidents, process and quality control technicians, and suppliers involved with the wet end processes.
Back To Top
|
The Christian Brothers University TAPPI Student Chapter has completed its first year. Below is a list of activities/involvements of the chapter during this academic year:
- Fall Fried Rice Fund Raising
- TAPPI-CBU Golf Fundraiser
- 2012 Healthcare Packaging Consortium Fall Meeting
- TAPPI Student Conference in North Carolina
- Spring Fried Rice Fundraiser
- 2013 Healthcare Packaging Consortium Spring Meeting.
The chapter held its last meeting for this academic year on Friday, April 26. It elected officers for the 2013-14 academic year. The newly elected officers are:
- President - Mallory Harvey (civil engineering major and packaging minor)
- Vice-Presidentc - Phyo Thoon H. Aung (civil engineering major and packaging minor)
- Secretary - Griselda Matos Martinez (engineering management and packaging minor)
- Treasurer - Patrick Held (engineering management with packaging concentration)
- Past-President - Alvin Siow (chemical engineering and packaging minor)
- Siripong Malasri will continue to serve as the chapter's faculty advisor.
Dr. Malasri said that "on behalf of our student chapter, I would like to thank TAPPI for its support given to the chapter over the past year, including the golf event, TAPPI scholarship, and Student Summit."
The photograph above shows the officers (l-r) who served in the 2012 – 2013 academic year: Dr. Pong Malasri, faculty advisor; Patrick Held, treasurer; Griselda Matos, secretary; Mallory Harvey, president; and Phyo Thoon Aung, vice president).
Back To Top
|
Recyclers and brokers of recovered fiber in Europe, North America, and elsewhere are facing increased hurdles selling into their largest market in China.
In late winter and early spring, shippers of secondary commodities into China have slowly begun to learn about "Operation Green Fence," an effort by Chinese environmental and customs officials to more vigorously inspect (and more willingly reject) what they consider to be sub-par container loads.
Paper Recycling Conference Asia, May 30-31 at the Hongta Hotel in Shanghai, represents an ideal opportunity for packers, merchants, and brokers to get on-the-scene insight into this emerging issue.
In each of the past years, North America alone has sent from 570,000 to 695,000 containers filled with scrap materials to China—with recovered fiber being the largest commodity by volume. Europe has sent a similarly large number of shipments to China. But carrying on with business as usual has not been an option for many in the recovered paper sector since Operation Green Fence was implemented in February 2013.
Numerous representatives from Chinese paper companies, government ministries, and trade associations are on the roster at Paper Recycling Conference Asia. Delegates will be able to find out from them—and have the opportunity to ask—details about the "Green Fence," what it is trying to keep out and how long it will last.
The event is being organized and co-hosted by the Recycling Today Media Group, Smithers Pira, and China TAPI. A full list of conference topics can be found on the webpage.
Register and reserve a hotel room to attend Paper Recycling Conference Asia.
Back To Top
|
The TAPPI Best Practices on the Corrugator Course, June 25-27 at the TAPPI Training Center in Peachtree Corners, Ga., USA.
Last year's course sold out, so here's your chance to attend. If you work with a corrugator, this is your opportunity to learn how to:
- Increase productivity and improve quality
- Reduce excess waste
- Adopt the "Centerline Process" to achieve a product that is consistent on every shift
- Maintain quality while reaching maximum corrugator speeds
- Get the maximum yield of boxes from the paperboard consumed
- Troubleshoot the most common operational problems
- Recognize critical properties of paperboard, starch, adhesive, and how to control warp.
What to Bring with You: Your questions and issues related to corrugator operations and samples of your defects.
What You'll Take Home: New ideas and operational methods to improve production.
Want to know more? Here's the Proposed Course Schedule.
Put June 25-27 on your calendar and register now to lock in your participation before seats fill.
Just one last note...
If you register by May 27, you can save up to $200 for this course. We look forward to seeing you here at the TAPPI Training Center.
Back To Top
|
TAPPI's 2013 Introduction to Wet End Chemistry Course provides in-depth training on paper machine wet end chemistry that will bring both mill technicians and suppliers up to speed on this key area of papermaking. The three-day course, to be held June 11-13 in Peachtree Corners (Metro Atlanta), Ga., USA,, is the only course of its kind in the world.
"This course is ideal for engineers and other technical people who need a better understanding of wet end chemistry," notes Scott Springmier, Manager, Pulp and Paper for TAPPI. "The course not only covers the key technologies, chemical additives and terminology but it also delves into the use of papermaking additives to change paper properties, improve runnability and reduce costs."
The course is designed for anyone that is involved with wet end operations as well as anyone training staff working in this area. New engineers with a strong technical background but lacking papermaking process knowledge would also benefit. Instructors focus this 3-day interactive training on innovative wet end chemistry principals and the use of additives to change or create new paper products. Through case studies, break-out sessions and networking with others in the course, attendees will learn how to implement new technology to improve efficiency and product quality, reduce machine downtime and off-specification production, select and use of papermaking chemicals, and troubleshoot problems.
Topics covered include: basic water chemistry, fibers and fines, starch, dry and wet strength agents, alum chemistry, rosin sizing, synthetic sizes, dyes, fillers, retention systems and deposit and pitch control. The impact of recent regulatory developments and how changes in fiber quality are impacting wet end operations are also reviewed.
The three course instructors are respected experts in wet end chemistry. Martin A. Hubbe, Ph.D., is Professor, Department of Forest Biomaterials, North Carolina State University. He began his career with American Cyanamid before joining International Paper Company as a research associate and later principal scientist. Larry Anker, Ph.D., is Sizing and Wet Strength Applications Group Leader for Ashland Hercules Water Technologies. He earned a B.S. in Chemistry, Mathematics and Physics from Washington and Lee University and Ph.D. in Chemistry at Penn State University. Przem Pruszynski, Ph.D., is Global Technical Specialist for Nalco. He holds an M.S. in Analytical Chemistry and Ph.D. in Physical Organic Chemistry from University of Poznan, Poland, where he taught for 12 years. He's authored nearly 100 papers, holds several patents and has taught numerous technical courses.
Back To Top
|
Alabama Southern will host a one-day-only Operator Training Conference & Workshop. This complimentary event, funded by the National Science Foundation (NSF) in conjunction with NPT2, will help HR professional and mill leaders add value to their existing operator training programs and provide practical advice on how to create a more competitive and better trained workforce.
Date: Friday, July 18
Location: Alabama Southern, Thomasville, Ala.
Time: 8:00 a.m.- 3:00 p.m CST
Discover new tools, learn best practices, and better equip your operator workforce. For more details or to register for the event, please contact Martha Wynn by email or by phone at 334.637.3194.
Back To Top
|
Nominations for the major TAPPI 2014 awards are due by August 1. The awards that may be presented in the upcoming year are:
Gunnar Nicholson Gold Medal Award - The Association's highest technical honor may be presented annually to recognize an individual or individuals for preeminent scientific and engineering achievements of proven commercial benefit to the world's pulp, paper, board, and forest products industries and the other industries that TAPPI serves.
Herman L. Joachim Distinguished Service Award - The Association's highest award for service may be presented annually to recognize leadership and service that have significantly and demonstrably contributed to the advancement of the Association.
Paul W. Magnabosco Outstanding Local Section Member Award - The highest honor for Local Sections may be presented annually to recognize an individual for outstanding leadership and exceptional service to one or more Local Sections, which have resulted in significant and demonstrable benefits to the Local Section members.
TAPPI Fellow - TAPPI Fellows are individuals who have been members of TAPPI for not less than 10 years prior to the nomination, and who have contributed meritorious service to the Association and/or the paper and related industries. Retiring members of the TAPPI Board of Directors become Fellows automatically at the end of their term.
The TAPPI Awards and Honors page has links to these awards that will show the qualifications required and links to the nomination forms that must be completed. You may submit all nomination forms by email to standards@tappi.org, or you may fax them to the attention of the awards department at +1-770-446-6947, or send them by mail to TAPPI, Awards Department, 15 Technology Parkway South, Peachtree Corners, GA 30092, USA.
Back To Top
|
The launch of this successful conference series, produced by the Recycling Today and Smithers Pira, in co-operation with China TAPI, into Asia provides a unique opportunity for companies in North America, Europe, and the rest of the world to meet buyers in the Asian market.
The full program for Paper Recycling Conference Asia launching on May 30-31 has been announced. Highlights include the opening keynote address - The role of recyclables in China's Economic Resurgence, presented by Professor Wang, Ministry of Environmental Protection, China; An Overview of Macro-Economic Trends Impacting Asia's Recovered Paper Industry from Sally Sun, Deloitte China, and an exclusive One-on-One Interview with Ross Li, Lee & Man.
Save 20% on a ticket to attend by using the code CD20TAP!
Attendees will hear from other key speakers on the agenda, including; Randy Kim, Ekman Recycling; Henri Vermeulen, Smurfit Kappa Group; Niu Qingmin, Jiangsu Paper Association; Yoshimitsu Tanaka, Kaneko, and more, on recovered paper supply, infrastructure, and quality issues and challenges.
"We're excited about launching a Paper Recycling Conference in Asia, particularly as Asian demand continues to represent the major growth area for recovered paper. Since this inaugural event replicates the design of our existing events' list to attract merchants, brokers, suppliers of recovered fiber, and mills from around the globe, it's sure to represent a unique and powerful opportunity for the world's suppliers and consumers of recovered paper to meet," Jim Keefe, EVP and group publisher, Recycling Today, said.
More information about the inaugural Paper Recycling Conference is available online.
Back To Top
|
The TAPPI Centennial Celebration will be a multi-year long series of outreach events and educational offerings showcasing the proud history and promising future of the global pulp, paper, packaging, and related industries. This once-in-a-lifetime event will expand public awareness, foster further connection, and provide outstanding opportunities for collaboration, growth, and investment in our future for all of those involved. Goals for the TAPPI Centennial Celebration are:
- To honor TAPPI's 100 years of connection, education, and advancement as a foundation for the sustainable success of our members, our industries, and the world we share
- To recognize the achievements of those who built our industry and to inspire those who seek to build its future
- To celebrate the contributions and innovations of the global pulp, paper, and packaging industries to human culture, commerce, health, and social advancement
- To sustain the industry and support its growth, vitality, and future through the TAPPI Foundation.
We invite you to be a part of this momentous event. The sooner you join us the more opportunities there are for recognition of your company, its products, and key innovations. Keep in mind that an early commitment allows you to spread your investment over multiple years' budgets.
For more information on sponsorship and volunteer opportunities please contact dbell@tappi.org.
The sponsorship prospectus can be downloaded online.
Back To Top
|
In 2015, TAPPI will celebrate its one hundredth year. The TAPPI Centennial Celebration will be a multi-year series of outreach events and educational offerings showcasing the proud history and promising future of the global pulp, paper, packaging, and related industries. This once-in-a-lifetime event will expand public awareness, foster further connection, and provide outstanding opportunities for collaboration, growth, and investment in our future for all of those involved.
BUCKMAN has become the first company to support the Centennial Celebration at the $100,000 level. Kathy Buckman Gibson, chairman of the board, noted that "Buckman is delighted to celebrate TAPPI's 100th anniversary by being a Centurion Sponsor. Like so many others, we have benefitted from the many ways TAPPI has been an advocate for knowledge-sharing, innovation, and growth in the paper industry. We appreciate the opportunity to take a leadership position in encouraging others within the industry to support the Centennial, share our industry's story of sustainability, and forge the future of innovation."
Goals for the TAPPI Centennial Celebration are:
- To honor TAPPI's 100 years of connection, education, and advancement as a foundation for the sustainable success of our members, our industries, and the world we share
- To recognize the achievements of those who built our industry, and to inspire those who seek to build its future
- To celebrate the contributions and innovations of the global pulp, paper, and packaging industries to human culture, commerce, health, and social advancement
- To sustain the industry and support its growth, vitality and future through the TAPPI Foundation.
Lela Simpson Gerald, director of Global Marketing Communications, added that "the value we get from TAPPI has continued to grow over the course of our decades of working together. Leading the sponsorship campaign for TAPPI's 100th anniversary is our way of thanking them for all they've done in the past and to proactively help the world understand the role paper products will play in the future."
We invite you to be a part of this momentous event. The sooner you join us, the more opportunities there are for recognition of your company, its products, and key innovations. Keep in mind, an early commitment allows you to spread your investment over multiple years' budgets. For more information on the Centennial Celebration and sponsorship opportunities please visit our website or contact David Bell at dbell@tappi.org; 770-209-7209.
Back To Top
|
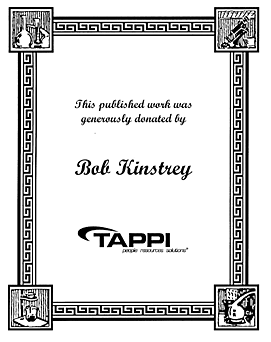
Do you have a history book gathering dust on your shelf? TAPPI's 100th year is coming soon and we are looking for donations to the TAPPI Library. Specifically, we are interested in histories of companies and mills in the paper and packaging industry (both producers and suppliers). Each donated book will have a bookplate in the front cover recognizing the donor. For more information please contact David Bell.
Please send books to:
c\o David Bell
TAPPI
15 Technology Parkway, South
Suite 115
Peachtree Corners, Georgia 30092
Back To Top
|
Patrice Mangin, Professor at the University of Québec à Trois-Rivières, Department of Chemical Engineering's Chemical Research Centre on Lignocellulosic Materials (CRML), has been named winner of the 2013 TAPPI Research & Development Technical Award and the William H. Aiken Prize. The award recognizes outstanding accomplishments or contributions that have advanced the technology of the paper and related industries in the field of research and development.
"Dr. Mangin has had an outstanding career as general manager of international research and development institutes at CTP in France and CIPP in Canada," notes Dr. Dominique Lachenal, professor at Grenoble INP-Pagora, who nominated Dr. Mangin. "Despite his heavy responsibilities, Dr. Mangin continuously made extremely valuable contribution to science and technology through the supervision of graduate students, the presentation of conferences, and the writing of scientific papers."
Mangin, a TAPPI member since 1980, received his Ph.D. from the Institute National Polytechnique of Grenoble (INPG) in 1988. He is chairman ex-officio of PAPTAC, and a member of the AGENDA 2020 CTO Committee. Patrice coordinates the wood valuation and job creation program of his regional (Mauricie) forest products industries. In his 40-year career, he built the Integrated Pulp and Paper Centre of which he was general director until 2012. He was CEO of the French Centre Technique du Papier, scientific director of the Swedish Print Research program, held industry chairs both at UQTR and KTH (Stockholm), and worked 17 years at PAPRICAN.
Patrice participated in many research and development strategic planning sessions in Canada (Canadian Forest Innovation Council, Conseil de l'Industrie Forestière du Québec, and Senate Commissions), in the U.S. (Agenda 2020) and Europe (CEPI). As CEPI Research Group chairman, he coordinated the European forest products industry proposals to the 6th EU Research Framework Program. Author of more than 300 articles, he published in 2011 UNO year of the forest, the book "Once Upon a Forest" to celebrate forest as humanity's best hope for the future.
He is a TAPPI Fellow (2010) and received TAGA highest Award (M.H. Bruno) in 2009. The award is given for outstanding accomplishments or contributions that have advanced the technology of the paper and related industries in the field of research and development. The prize is funded by an endowment from the estate of William H. Aiken, TAPPI president in 1967-1968, and VP of technology for the former Union Camp Corp.
Back To Top
|
The only conference that focuses exclusively on renewable and sustainable nanomaterials, showcasing the latest applications and discoveries using cellulose, chitosan-derived, and other nanomaterials....
In its eighth year, TAPPI's 2013 International Conference on Nanotechnology for Renewable Materials to be held June 24-27 in Stockholm, Sweden, features the largest program to date, with more than 80 technical presentations.
KTH Royal Institute of Technology Campus - Stockholm, Sweden
Register online and also reserve your hotel room at the Elite Hotel Arcadia, the preferred conference hotel.
Your conference registration also includes a tour of either Innventia AB or the Wallenberg Wood Science Center beginning at 16:00 on Monday, June 24. Space is limited on both tours. Both will end by 18:30 so that you can attend the welcome reception. More details will be available soon, but allow for an early arrival time so you don't miss out.
This conference is your opportunity to learn about composite foams made with modified nanofibrillated cellulose from pulp mill waste streams, eco-friendly membranes, and high-strength, thin, and flexible films made from cellulose nanomaterials. Presentations also address material characterization, self-assembly behavior, rheology and processing of nanomaterials, novel medical applications, characterization techniques, and health and safety issues. A Standards Workshop is also scheduled to help advance the development of standards for cellulose nanomaterials.
With the two pre-conference tours, five keynote presentations, a poster session plus Student Poster Competition, it will be a packed three days in Stockholm. Register today, and see what solutions are available to support tomorrow's bioeconomy.
The 8th Annual International Conference on Nanotechnology for Renewable Materials is hosted by TAPPI's International Nanotechnology Division, which strives to collectively advance the responsible and sustainable production and use of renewable nanomaterials.
Learn more about the Nanotechnology Division.
Back To Top
|
The Pulp and Paper Safety Association (PPSA) will host its 70th Annual Safety and Health Conference - "The Human Element of Safety," June 9-12, in Williamsburg, Va., USA.
At the conference, presenters will address how human behavior will proactively help prevent, detect, and control events before they occur. Professionals from across the country know the importance of safety and attendees will hear from 18 speakers who will show the impact of addressing the human impact on safety. The conference will feature updates from OSHA, member company case studies, and PPSA's popular legal update.
Among the confirmed speakers are representatives from MeadWestvaco, Weyerhaeuser Co., Domtar, Safe Start, International Paper, REM Safety Consulting, Michael Best & Friedrich Law Firm, Training Logic, Change Management Consulting, and BushCo.
PPSA is a non-profit, non-political, international organization, devoted to the countinuous improvement of safety throughout all aspects of the paper industry. From forest products to paper mills, to converting plants, to recycle collections centers, our membership is grouped by category to ensure a fair and appropriate basis for comparison.
Registration is currently open for this event. More information is available online.
Back To Top
|
The Pulp and Paper Manufacturers Association (PPMA) has launched its first-ever Best Place to Work Award. The award is open to all companies in the forest products industry and will look not only at corporate life but also look at how employees feel about their work environments.
In conjunction with Majority Opinion Research Group, PPMA has started taking nominations for this award and will continue to accept nominations through July 1.
"This award is an exciting opportunity for PPMA to honor great companies. As an association that serves HR professionals, we know the value of the making your company a great place to work," said PPMA President Joe Thibaudeau, employee relations manager - Procter & Gamble - Green Bay, Wis., USA.
The award will be presented to the winner at the annual PPMA conference on October 23-25, 2013, in Milwaukee, Wis., USA. The winner will have the chance to speak with conference attendees about what makes his or her company the "Best Place to Work."
PPMA is a nonprofit association built around a community comprised of executives, managers, and human resource professionals from the pulp and paper industry. For its members, PPMA serves as a primary source of information on labor settlements and current human resource issues, governmenta,l and related operational issues.
To nominate your company for the Best Place to Work Award, use the online form.
Back To Top
|
The existence of cellulose nanocrystals and cellulose nanofibrils has been known for several decades, yet recent advances in science, particularly in the field of nanotechnology, have revealed that these materials contain unique physical properties, particularly high strength properties. Researchers have been studying how these materials can improve paper properties and will present their latest finding this June 24-27 in Stockholm, Sweden, at TAPPI's 8th Annual International Conference on Nanotechnology for Renewable Materials at the KTH Royal Institute of Stockholm.
The program for this year's event has been released, and one session will focus on using cellulose nanofibers for improving retention and increasing strength in paper. Researchers from Aalto University in Finland will report on improved flocculation of both precipitated calcium carbonate (PCC) and kaolin with the addition of certain cellulose nanomaterials. Researchers from Papiertechnische Stiftung (PTS) in Heidenau, Germany, will report on the importance of adding fillers, celluloses, and compounding agents in the right order to achieve the best results. Researchers from VTT in Finland will report on ways to increase the strength of paper by using filler particles coated with nanoscale calcium silicate hydrate (CS) structures.
New reports at the conference will present some exciting advances for both within the pulp and paper industry and beyond. The technical program features cellulose nanomaterials in a variety of applications, including:
- Unique and Thin-Film Composites
- Filler and Coating Applications for Different Paper Grades
- Improved Barrier Properties for Packaging Applications
- Cellulose Nanomaterials as Films and Carriers in Medical Applications
- Nanopaper and Iridescent Colored Cellulose Films.
With more than 80 technical presentations, five keynote presentations, and 50 poster presentations, this year's conference is packed with the latest applications of renewable nanomaterials.
Watch for additional updates from TAPPI on how nanotechnology, and cellulose nanomaterials in particular, can be a transformative technology for the pulp and paper industry.
The 8th Annual International Conference on Nanotechnolgy for Renewable Materials is hosted by TAPPI's International Nanotechnology Division, which strives to collectively advance the responsible and sustainable production and use of renewable nanomaterials. More information is available online.
Back To Top
|
The Bleaching of Pulp, Fifth Edition
By Alan W. Rudie and Peter Hart
Previous editions of The Bleaching of Pulp have provided comprehensive information on the technology used to bleach wood pulps. The 5th edition will continue this tradition as the premiere industry text on bleaching technologies but will be more focused on the modern industrial processes with less emphasis on fundamental science. New or more comprehensive sections are included on elemental chlorine free bleaching, enzymes, acid treatments for hexeneuronic acids, control of mineral scale, and multi-stage modeling as used to optimize bleaching among multiple stages.
Item Number: 0101R331 • List Price: $232 • Member Price: $155
Handbook for Pulp and Paper Technologists
(The Smook Book) Third Edition
By: Gary A. Smook
This best-selling text provides an introduction to the entire technology of pulp and paper manufacture. The book features 27 chapters covering all aspects of pulping and papermaking. Hundreds of illustrations, charts, and tables help the reader grasp the concepts being presented. The third edition features additional material on secondary fiber recovery and utilization, mechanical pulping, kraft pulping and bleaching, and papermaking. 2002. 425 pages, hard cover.
Item Number: 0202SMOOK • List Price : $75 • Member Price: $56
Troubleshooting the Papermaking Process
By: By Jerome M. Gess and Paul H. Wilson
This book takes the reader through the process of making paper, pointing out where interruptions can occur and where elements that are added to the system can cause problems in that part or subsequent parts of the papermaking process. The aim of this book is to give papermakers and those involved in the papermaking process the information required to allow them to understand how to track down and solve problems at their source rather than where the problems surface.
Item Number: 0101R298 •List Price: $161• Member Price: $106
Paper Machine Quality Control Systems - Vol. 1: Measurement Systems and Product Variability
By: Quality Control Systems Education Common Interest Group of the Process Control Division
This book describes in detail the measurement technology used in Quality Controls Systems (QCS). Individual chapters are devoted to the five most prevalent QCS measurements (basis weight, moisture, caliper, ash, and color) in the paper industry. Each of these chapters covers the physical principles involved in each measurement, sensor designs, various methods of implementation, and influence factors. A somewhat lighter coverage is given to 10 other QCS measurements that do not have such a broad installation base. Common issues that impact all sensors are explained, including how sensor performance is measured and reported, the impact of scanning process, filtering, scanner designs and construction, and sensor calibration and correlation. Statistical methods are covered in depth from discrete one-dimensional variability to multi-dimensional variability. Guidance is provided for using these statistical methods to locate the sources of variability in the paper process.
Item Number: 0101R328•List Price: $205• Member Price: $135
The Corrugated Containers Manufacturing Process
By: Jody A. Brittain, Stephen R. Perkins, and Philip G. Schnell
This comprehensive textbook describes the entire process of manufacturing corrugated containers. In addition to detailed explanations, the book also features practical troubleshooting tips, and a discussion of common problems and solutions within each major section. Seven detailed chapters cover the following topics:
- Paper and the Papermaking Process
- Steam
- Corrugating Adhesives
- Singleface Operations
- Doublebacker Process
- Combined Board
- Converting.
This textbook is designed to provide in-depth explanations and information for professionals working in all areas of the corrugated containers industry.
Item Number: 0101R281•List Price: $185•Member Price: $37
Back To Top
|
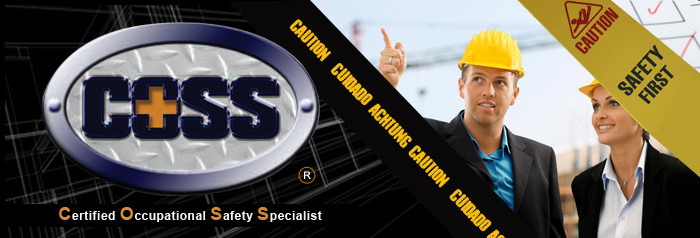
Are you ready to go further, faster in your safety career? The Certified Occupational Safety Specialist (COSS) class can take you there.
The COSS Class is Unique
Not only will you learn how to read and understand the OSHA 1910 and 1926 CFRs and help your company avoid OSHA citations that cost millions of dollars, but more importantly, by learning how to work safely on a job site, you can teach your company how to lower fatalities and near misses. Almost 47% of COSS graduates responding to our survey indicate that, since taking COSS, their company's injury rate and/or OSHA recordables have decreased by as much as 25% and others attest to as much as a 100% decrease!
Request a Course Outline & Syllabus for more information.
The class also addresses the psychology of safety, the true cost of an accident, hazard recognition, how to start up a health and safety program, behavior based safety, system safety, and much more!
What Will You Receive?
Upon successfully completing the class, you will obtain your national Certified Occupational Safety Specialist (COSS) designation, your OSHA 10-hr. card of completion in construction, and your OSHA 10-hr. card of completion in general industry.
National Program Recognitions
COSS is currently one of only 37 programs in the world recongnized and accredited by the American Petroleum Institute (API). In addition, the certifying body for construction education for colleges, universties and technical/trade schools, American Council for Construction Education (ACCE), has also recongnized our program. COSS is the only non-degree program to receive this national endorsement. Lastly, COSS has been established as a mandatory course for students in the Construction Management Program at Louisiana State University.
Program Content
The program consists of 40 hr. of hands on, face-to-face learning, which is delivered by an Authorized OSHA outreach trainer in both construction and general industry. Case studies and workshops are used extensively to bring learning objectives into focus. Guest speaker from areas such as OSHA and other governmental agencies are used to enhance the learning experience. Student presentations, daily quizzes, practical reviews, and a comprehensive final exam will allow you to demonstrate your competency.
Prerequisites
The only prerequisite for the COSS class is you must have a high school diploma or equivalent. In each class, we tend to have a mix of non-experienced, first time safety persons, as well as safety professionals who have been in the safety field for 20+ years. But, we have learned that regardless of the numbers of years of experience you have in safety, everyone leaves the COSS class with a wealth of knowledge!
Visit the COSS website for FAQs, testimonials and a list of clients that have taken COSS.
Register now.
If you would like more information on the COSS program, contact Beth Gordon at 877-610-2677.
Back To Top
|
|
|
TAPPI Over the Wire | 15 Technology Pkwy. S. | Norcross, GA 30092 USA | Voice: 770.446.1400 | Fax: 770.446.6947
|
 |