How Biomass Torrefaction Works: An Introductory Presentation
Torrefaction is a thermal process to convert biomass into a coal-like material, which has better fuel characteristics than the original biomass. Torrefied biomass is more brittle, making grinding easier and less energy intensive. Compared to fresh biomass, storage of the torrefied material can be substantially simplified since biological degradation and water uptake is minimized.
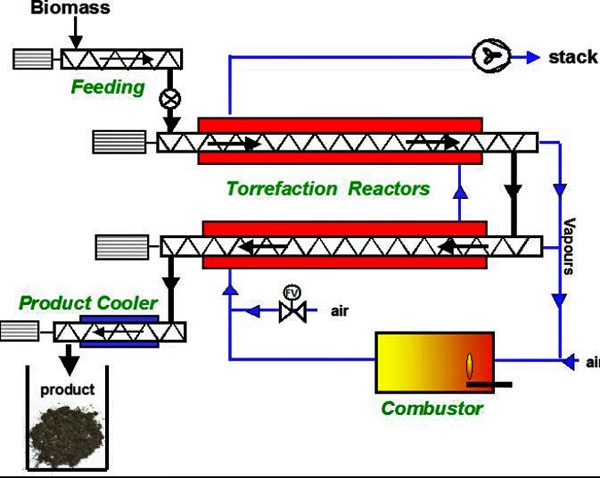
Torrefaction involves the heating of biomass in the absence of oxygen to a temperature of typically 200 to 400°C. The structure of the biomass changes in such a way, that the material becomes brittle, and more hydrophobic. Although the weight loss is about 30%, the energy loss is only 10%. Main product is the solid, torrefied biomass. During the torrefaction process a combustible gas is released, which is utilized to provide heat to the process. In the figure below the energy and mass yields are shown for autothermal operation as a function of the moisture content in the feedstock. With increasing moisture content more gas is required to achieve autothermal operation and as a consequence the degree of torrefaction will increase.
The torrefaction process is shown schematically in the figure above. Four sections can be distinguished in this concept:
- The biomass feeding section;
- The reactor section, where biomass is converted into torrefied material and a combustible gas
- The cooling section; the torrefaction product is highly flammable, necessitating the need for a cooling system.
- The combustor section; the produced gases & vapours are burned with an excess of oxygen in the combustor, and the heat generated is used to heat the process.
In this torrefaction concept, the heat required is generated by combustion of the vapors that are released in the process. For this purpose, the gases are directed to a dedicated combustion chamber, in which the combustion takes place at sufficiently high temperatures. The hot flue gas from the combustion is forced along the wall of the reactor to indirectly heat the biomass. Depending on the feedstock and required product quality excess heat can be generated, f.i. for drying purposes or electricity production. A very wide-range of different biomasses including residues can be converted in the torrefaction process, even very low density materials.
TAPPI
http://www.tappi.org/