Voith Launches New VECO-Drive for Compressors and Pumps
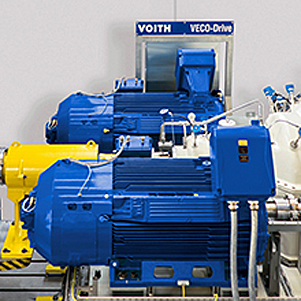
Voith, Germany, this week introduced the first member of a new product family in the field of speed control for compressors and pumps—the VECO-Drive, an electric superimposing gear inspired by the established principle of the Voith Vorecon, with more than 600 installations.
The VECO-Drive combines a mechanical planetary gear with frequency-controlled servo motors. The electrical superimposing gear is the most efficient way to make speed variable. Servo motors are used to drive a planetary gear. Since they only need a small part of rated power, an overall component efficiency of more than 97% is reached. This saves valuable energy and reduces operating expenditures every day.
The VECO-Drive is installed between a constant speed motor and a variable speed compressor or pump. With the new VECO-Drive, Voith combines the reliability of mechanical gears with the outstanding productivity of low voltage VFDs. Since additional power is supplied to the drive train, a smaller main motor can be used. This saves capital expenditures. Moreover, the servo motor can be used as a starter to protect the electric grid from high inrush currents.
For the functional demonstration of the VECO-Drive, a prototype system was built and tested in Crailsheim, Germany, in 2016. Voith engineers designed the system for compressor and pump applications with a maximum output speed of 15,000 rpm, maximum output power of 15 MW, and a speed adjustment range from 50% to 100%. Compared with a typical full-scale medium voltage VFD train with a step-up gearbox, the measured system efficiency of a VECO-Drive is about 2% higher over the whole speed range. Thus, the VECO-Drive system reduces annual energy consumption by more than 2,000 MWh compared with a comparable VFD system. With a typical energy cost of EUR 50/MWh, these energy savings result in cost reductions of more than EUR 100,000/yr.
As a matter of principle, the VECO-Drive is designed as a modular system and thus offers individual specifications for different application types, classes of explosion protection, and speed levels. Advanced functions like the integrated PLC-based output controller, user interfaces, condition monitoring, and simplified maintenance are part of the scope of supply, whereas remote access and remote diagnosis are available on demand.
TAPPI
http://www.tappi.org/