Sofidel’s Headbox Energy Recovery System Exceeds Expectations
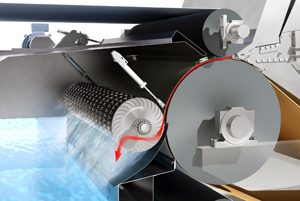
The first installation of Valmet's (Finland) new Advantage ReTurne energy recovery system was recently started up at Sofidel's mill Delicarta Valdottavo in Italy and proved to meet all expectations when it was tested this past week. The Advantage ReTurne system not only recovers energy from the headbox jet power, but also returns it back to the process as electrical energy.
"The first installation of the Advantage ReTurne energy saving system has been a positive experience for us. Its energy saving capabilities turned out to be better than we hoped for and well in line with our target to further reduce our carbon dioxide emissions before the end of 2020," said Simone Capuano, vice chief technical officer, Sofidel.
"We had high expectations of the results from the first installation of the Advantage ReTurne system, which were substantially exceeded. The installation went smoothly and the machine was running at full speed within five days. But most exiting was that the energy recovery proved to be above guaranteed levels," said Jan Erikson, VP sales, Valmet.
The Advantage ReTurne energy recovery system is installed in the forming section. It is unique in the sense that it recovers 50% of the energy from the headbox drainage water and via a generator converts it to electrical power, which supplies the sectional drives. The system does not affect the formation of the paper or the tissue making process. It is easy to handle and has low maintenance needs, and is efficient installed in new or existing tissue machines.
The Sofidel Group is currently the second largest European producer of tissue paper (for sanitary and domestic use) and the sixth largest in the world. It was founded more than 45 years ago (1966) and today boasts 27 subsidiaries in 13 countries –Italy, Spain, Sweden, the U.K., Belgium, France, Croatia, Germany, Poland, Romania, Greece, Turkey, and the U.S. It has about 5,000 employees and a consolidated turnover of EUR 1,699 million (2013) and a capacity of more than 1 million metric tpy.
TAPPI
http://www.tappi.org/